-
Whatsapp: +86 13526572721
-
Email: info@zydiamondtools.com
-
Address: AUX Industrial Park, Zhengzhou City, Henan Province, China
-
Whatsapp: +86 13526572721
-
Email: info@zydiamondtools.com
-
Address: AUX Industrial Park, Zhengzhou City, Henan Province, China
Resin Bond Diamond/CBN Grinding Wheels: Mastering Selection and Application for Superior Results
- Grinding Wheels Knowledge
- -2022-10-18
- - byKevin Ray
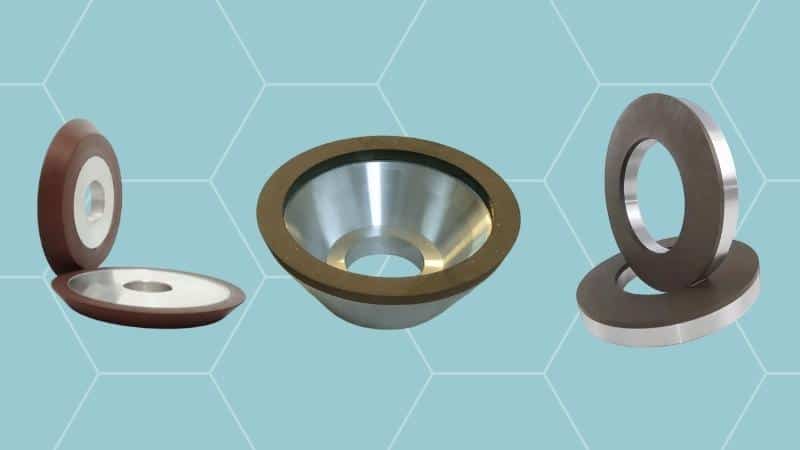
Looking to truly understand how to choose the best resin bond diamond or CBN grinding wheels for your needs and then use them to achieve outstanding results?
Mastering resin bond diamond/CBN grinding wheels involves understanding why resin bonds are advantageous for specific materials, knowing the critical factors for selecting the right wheel—including abrasive type, specifications, and geometry—and applying best practices for wheel preparation, operation, and troubleshooting to maximize performance, lifespan, and overall cost-effectiveness, all while prioritizing operational safety.
Table of Contents
ToggleWhy Choose Resin Bond for Your Diamond/CBN Grinding Wheels?
So, you might be wondering, with several types of abrasive wheel bonds available, why specifically choose a resin bond for your diamond or CBN grinding wheels?
Resin bond diamond and CBN grinding wheels are primarily chosen for their excellent balance of efficient cutting action, superior surface finish capabilities, and their ability to grind heat-sensitive materials with reduced thermal damage. Their inherent elasticity allows for smoother grinding, making them versatile for a wide range of precision applications on hard and brittle materials.
Let’s explore this further.
The Science Behind Resin Bonds: Key Properties and Benefits
At its core, a resin bond acts like a sophisticated glue, holding superabrasive particles like diamond or CBN firmly in place. These bonds are typically made from phenolics1 or polyimide resins, which are types of strong plastics. Imagine the resin as a matrix that wears away gradually during grinding. This controlled wear is actually a good thing! It continuously exposes fresh, sharp abrasive particles to the workpiece. This “self-sharpening” characteristic is a key advantage.
Key Properties of Resin Bonds:
- Good Elasticity: Unlike very rigid bonds, resin bonds have a degree of flexibility or “give.” Think of it like having slight shock absorbers. This property helps in achieving finer surface finishes and reduces the risk of chipping, especially on brittle materials.
- Self-Sharpening Action: As mentioned, the resin wears away at a controlled rate. This prevents the wheel from becoming dull (a condition called “glazing”) and ensures consistent cutting performance.
- Lower Grinding Temperatures (in some cases): Compared to metal bonds, resin bonds can sometimes generate less heat during grinding. This is crucial when working with materials that are sensitive to temperature changes, helping to prevent warping or metallurgical damage to the workpiece.
- Versatility in Formulation: Resin bonds can be formulated with various fillers and additives. This allows manufacturers to fine-tune the bond’s characteristics – like its hardness, toughness, and wear rate – to suit specific applications and materials.
Core Benefits for You:
- Excellent Surface Finish: The elasticity and self-sharpening nature contribute to smoother, higher-quality surface finishes on the ground parts. This can reduce or even eliminate the need for subsequent finishing operations.
- Reduced Workpiece Damage: The gentler grinding action and lower heat generation minimize issues like micro-cracks, burns, or changes in material hardness.
- Good Material Removal Rates (for suitable applications): While not always matching the aggressive stock removal of some metal bonds, resin bonds offer a very effective balance of cutting speed and finish for many precision tasks.
- Versatility: They can be used for a wide range of operations, from sharpening cutting tools to precisely shaping components.
How Do Resin Bonds Compare to Other Bond Types (Vitrified, Metal, Electroplated)?
Choosing the right bond type is like picking the right tires for a car – different tracks and conditions demand different solutions. Resin bond is a fantastic all-rounder in many scenarios, but how does it stack up against other common bond types?
Bond Type | Primary Characteristic | Best For | Resin Bond Advantage Over This Type For Certain Apps |
---|---|---|---|
Resin Bond | Elastic, self-sharpening, good finish, versatile | Precision grinding, heat-sensitive materials, tool sharpening | N/A (This is our focus bond) |
Vitrified (Ceramic) Bond | Hard, rigid, porous, good stock removal, holds form well | High productivity grinding, grinding steels, good for CNC machines | Resin bonds are more elastic, offering better surface finish and less chipping on very brittle materials. They can also be more forgiving if grinding parameters aren’t perfectly optimized. |
Metal Bond | Extremely tough, highest wear resistance, excellent form holding | High-volume production, cutting off, grinding very abrasive non-metallics (e.g., concrete, stone with diamond) | Resin bonds generally produce less heat and achieve finer finishes. They are also preferred for many tool steels where CBN is used, as metal bonds2 can sometimes be too harsh or cause thermal stress. |
Electroplated Bond | Single layer of abrasive, aggressive cut, complex forms | Profile grinding, grinding composites, some specialized short-run jobs | Resin bonds have multiple layers of abrasive, offering significantly longer wheel life and more consistent performance over that life. Electroplated wheels are often used until the single abrasive layer is gone. |
In essence, while a vitrified bond might be chosen for its aggressive material removal and rigidity in high-production steel grinding, a resin bond would be preferred if the steel is heat-sensitive or if a superior surface finish is paramount.
Similarly, though a metal bond offers unmatched durability for cutting very hard, abrasive materials, its aggressive nature and higher grinding forces might be unsuitable for delicate precision components where a resin bond would provide a gentler, more controlled action.
And while electroplated wheels are great for holding intricate shapes and initial aggressive cutting, resin bond wheels will typically offer a much longer operational lifespan and a more consistent cutting action over time because new abrasive layers are continually exposed.
Identifying Ideal Applications Where Resin Bond Wheels Truly Excel
So, where do resin bond diamond and CBN wheels really shine? Their unique blend of properties makes them indispensable in several key industrial applications.
Resin Bond Diamond Wheels are often the top choice for:
- Grinding Tungsten Carbide3: This is a major application. Think of sharpening carbide cutting tools (end mills, drills, reamers, saw blades), grinding carbide dies, punches, and wear parts. The resin bond provides an excellent finish and minimizes chipping on the brittle carbide. For example, in the manufacturing of precision carbide drill bits for circuit boards, resin bond diamond wheels are used to create the sharp cutting edges and flutes with high accuracy.
- Grinding Hard Ceramics: Materials like alumina, zirconia, and technical ceramics used in electronics, aerospace, and medical devices can be effectively ground with resin bond diamond wheels, especially when surface finish and integrity are critical.
- Grinding Glass and Quartz: For optical lenses, laboratory glassware, or other precision glass components, resin bond diamond wheels offer controlled material removal and fine finishes.
- Grinding Cermets (Ceramic-Metal composites): These materials combine the hardness of ceramics with the toughness of metals. Resin bond diamond wheels provide a good balance for machining them.
- Other Brittle Non-Metallic Materials: Including silicon, ferrite, and some advanced composites.
Resin Bond CBN (Cubic Boron Nitride) Wheels excel when grinding:
- Hardened Ferrous Metals (Steels): This is the primary domain for CBN.
- High-Speed Steels (HSS): Sharpening HSS cutting tools like broaches, hobs, and milling cutters. For instance, a gear manufacturing company would use resin bond CBN wheels to maintain the precise profiles of HSS hobs used for cutting gear teeth, ensuring gear accuracy and tool longevity.
- Tool Steels & Die Steels: (D2, A2, M2, etc.) Grinding dies, molds, and other hardened tool steel components. The lower grinding temperature of resin bond helps maintain the steel’s hardness and prevents distortion.
- Alloy Steels (Hardened): Grinding various hardened alloy steel parts used in automotive (e.g., crankshafts, camshafts where finish is key), bearings, and machinery.
- Superalloys (some applications): While metal bonds are also used for superalloys (like Inconel®, Hastelloy®), resin bond CBN wheels can be preferred for applications requiring finer finishes or when grinding heat-sensitive aerospace components, as they can offer a gentler action. The choice between resin and metal bond for superalloys can be complex and often depends on the specific alloy, stock removal requirements, and finish; consulting with an application engineer is advisable.
- Case-Hardened Steels: Grinding components that have a very hard surface layer.
The common theme for resin bond’s excellence is its ability to deliver precision and a fine surface finish, especially on hard, brittle, or heat-sensitive materials, without compromising too much on material removal efficiency for those specific applications. They are the workhorses for many tool room operations and precision manufacturing processes.
What Critical Factors Should Guide Your Resin Bond Diamond/CBN Wheel Selection?
So, you understand the benefits of resin bond wheels, but when you’re faced with so many options, how do you choose the exact right one for your particular grinding job?
Selecting the correct resin bond diamond or CBN grinding wheel involves first choosing the right abrasive type4 (diamond for non-metallic and non-ferrous materials, CBN for steels and ferrous alloys). Next, you must specify the appropriate grit size, abrasive concentration, and bond hardness based on the material being ground and the desired surface finish. Finally, matching the wheel’s shape and size to your grinding machine and the specific task is crucial for success, especially when aiming for high-precision results.
Let’s break down each of these critical factors.
Diamond or CBN: Making the Right Abrasive Choice for Your Material
The very first decision, and it’s a big one, is choosing between diamond and Cubic Boron Nitride (CBN) as your abrasive material. These are superhard materials, but they interact differently with various workpiece materials.
- Diamond Abrasives: Best for Non-Ferrous and Non-Metallic Materials
Think of diamond as the champion for grinding really hard things that don’t contain iron or steel. Why not steel? At the high temperatures generated during grinding, diamond (which is made of carbon) can have a chemical reaction with iron in steel. This makes the diamond wear out much faster.
Choose diamond for:- Tungsten Carbide: This is a very common use – things like cutting tools, dies, and wear parts.
- Hard Ceramics: Alumina, zirconia, porcelain, and other technical ceramics.
- Glass and Quartz: For optical components or specialty glass products.
- Non-Ferrous Metals: Such as hard bronzes or some aluminum alloys (though conventional abrasives are often used for softer aluminums).
- Composite Materials: Like carbon fiber reinforced plastics (CFRPs).
- Natural Stone and Concrete: Though often with metal bond wheels for very aggressive cutting.
- CBN (Cubic Boron Nitride) Abrasives: The Expert for Steels and Ferrous Alloys
CBN is the second hardest material known, right after diamond. Its superpower is that it doesn’t react chemically with iron, even at high grinding temperatures. This makes it perfect for grinding hardened steels and other iron-based (ferrous) materials.
Choose CBN for:- Hardened Steels: Any steel with a hardness typically above 45 HRC (Rockwell C scale).
- Tool Steels: High-Speed Steel (HSS), D2, A2, M2, etc. Used for making cutting tools, punches, and dies. For example, regrinding HSS drill bits or milling cutters.
- Die Steels: Used in stamping and forming operations.
- Bearing Steels: Like 52100 steel.
- Case-Hardened Steels: Steels that have a very hard surface layer.
- Superalloys: Nickel-based or cobalt-based alloys like Inconel®, Waspaloy®, and Stellite®, which are notoriously difficult to grind. CBN maintains its hardness at the high temperatures generated when grinding these tough materials.
- Hard Cast Irons: Some types of cast iron that are very hard and wear-resistant.
- Hardened Steels: Any steel with a hardness typically above 45 HRC (Rockwell C scale).
Quick Comparison: Diamond vs. CBN in Resin Bond Wheels
Feature | Diamond Abrasive | CBN Abrasive |
---|---|---|
Best For | Non-ferrous metals, non-metallic hard materials | Ferrous metals (steels, cast irons) > 45 HRC, superalloys |
Why? | Highest hardness | High hardness, chemically stable with iron at high temperatures |
Avoid With | Steels (due to chemical reaction at high temp) | Softer, non-ferrous materials (less cost-effective) |
Common Uses | Tungsten carbide, ceramics, glass | Hardened tool steels, HSS, superalloys, bearing steels |
Choosing the wrong abrasive type is a common mistake that can lead to very poor wheel life and bad grinding results. So, always start by identifying your workpiece material!
Decoding Key Wheel Specifications: Grit Size, Concentration, Hardness, and Bond Modifications
Once you’ve chosen between diamond and CBN, you need to specify several other important characteristics of the wheel. These specifications determine how the wheel will cut, the finish it will produce, and how long it will last. For a deeper dive into selection for various processes, see this guide on how to select the right diamond grinding wheel5.
- Grit Size (Particle Size)
This refers to the size of the individual diamond or CBN abrasive grains in the wheel. It’s like sandpaper – coarser grits have bigger particles, and finer grits have smaller ones.- Coarse Grits (e.g., 60/80, 80/100, D/B181, D/B151):
- Remove material faster (higher stock removal).
- Produce a rougher surface finish.
- Good for initial grinding operations or when finish isn’t critical.
- Medium Grits (e.g., 100/120, 120/140, D/B126, D/B107):
- Offer a balance between stock removal and surface finish.
- Common for general-purpose grinding.
- Fine Grits (e.g., 200/230, 320/400, D/B76, D/B46, and even finer micron sizes):
- Remove material slower.
- Produce a very smooth, fine surface finish.
- Used for precision finishing operations.
*The specific grit size ranges and their designations can vary slightly between standards (like ANSI, FEPA, or JIS) and manufacturers. For instance, a D126 in one system is roughly a 120/140 US mesh. It’s always best to consult your supplier’s catalog or technical support to understand their specific grit sizing and to get recommendations for your material and desired Ra (surface roughness).
- Coarse Grits (e.g., 60/80, 80/100, D/B181, D/B151):
- Concentration
Concentration tells you how much diamond or CBN abrasive is packed into the resin bond material by volume. A common reference is C100 (or N100 for CBN), which means the bond contains 72 carats of abrasive per cubic inch, or 4.4 carats per cubic centimeter.- Lower Concentrations (e.g., C50, C75):
- Fewer abrasive particles.
- Often used for dry grinding, deep cuts, or when a very free-cutting action is needed to avoid loading (where the wheel gets clogged with material).
- Can be more economical for some applications.
- Higher Concentrations (e.g., C100, C125, C150):
- More abrasive particles doing the work.
- Generally provide longer wheel life and can handle harder-to-grind materials or larger contact areas.
- Often preferred for wet grinding and achieving fine finishes.
Higher concentration usually means a higher wheel price, but it can also lead to better overall performance and longer life, potentially reducing total costs. The optimal concentration can depend significantly on the application, material, and grinding parameters, so discussing this with your supplier is very beneficial.
- Lower Concentrations (e.g., C50, C75):
- Hardness (of the Bond)
This doesn’t refer to the hardness of the diamond or CBN (which are already superhard!), but rather to how strongly the resin bond holds onto those abrasive
particles.- Softer Bonds (e.g., grades like J, K, L):
- Release dull abrasive grains more easily, exposing fresh, sharp ones. This is good for self-sharpening.
- Used for grinding very hard materials, large contact areas, or when there’s a risk of the wheel loading or glazing.
- Harder Bonds (e.g., grades like P, Q, R, S):
- Hold onto abrasive grains longer.
- Used for grinding softer materials, maintaining intricate wheel profiles (form holding), or when grinding small contact areas.
- Provide longer wheel life in the right applications.
Choosing the wrong bond hardness can lead to either rapid wheel wear (if too soft) or the wheel becoming dull and not cutting effectively (if too hard, called “glazing”). Bond grade systems also vary, so always refer to your supplier’s specific grading and recommendations.
- Softer Bonds (e.g., grades like J, K, L):
- Bond Modifications
Resin bonds are not just simple plastics; they are often complex formulations. Manufacturers can add different types of fillers and additives to the resin to change its properties:- Metallic Fillers (e.g., copper, aluminum powder): Can improve heat dissipation (helping the wheel run cooler) and increase the bond’s strength and wear resistance.
- Solid Lubricants (e.g., graphite): Can make the bond more “free-cutting” by reducing friction.
- Other Fillers (e.g., ceramic particles): Can enhance wear resistance or alter the bond’s erodibility.
These modifications create different “flavors” of resin bonds, each tailored for certain performance characteristics – for example, some might be designed for high material removal, others for exceptional surface finish, or for dry grinding. These formulations are often proprietary to the wheel manufacturer. This is where a good supplier can really help by recommending a bond modification specifically suited to your unique challenge.
How to Match Wheel Geometry (Shape & Size) to Your Specific Grinding Task
The “geometry” of a grinding wheel refers to its shape and its dimensions (like diameter, thickness, and arbor hole size). Getting this right is essential for the wheel to fit your machine, reach the area you need to grind, and perform the operation effectively.
Common Resin Bond Wheel Shapes:
Manufacturers produce a wide variety of standard wheel shapes, often designated by codes (like ANSI or ISO types). Here are a few common ones and what they’re good for:
- Type 1A1 (Straight Wheels):
- These are the most common type – simple, flat discs, like these 3A1 Resin Bond Diamond Grinding Wheels6. (Note: 1A1 and 3A1 are similar straight wheel types, with 3A1 often having a relief on one side).
- Uses: Surface grinding (grinding flat surfaces), cylindrical grinding (grinding round parts between centers or in a chuck), bench grinding, and general tool sharpening. For instance, sharpening the flat face of a lathe tool.
- Type 11V9 or 12V9 (Flaring Cup Wheels):
- These are cup-shaped with the grinding face on the rim, often tapered. The 11V9 is more dramatically tapered (flaring) than the 12V9.
- Uses: Tool and cutter grinding, especially for sharpening milling cutters, reamers, and taps. They offer good visibility of the workpiece. Example: Sharpening the primary relief on an end mill.
- Type 6A2 or 12A2 (Dish Wheels):
- These are also cup-shaped but typically have a thinner rim or grinding section. The 6A2 is a straight cup, while the 12A2 is a dish shape (tapered sides).
- Uses: Grinding cutters, reamers, deep slots, and profiles where a thinner wheel edge is needed for access. Example: Grinding the flutes of a carbide drill.
- Type 14A1 (Saucer Wheels):
- These are very thin, like a saucer, with the grinding face usually on the periphery.
- Uses: Sharpening certain types of milling cutters, saws, or tools with narrow slots.
Key Dimensions to Consider:
- Diameter (D): The overall size of the wheel. It affects the surface speed of the wheel and must be compatible with your grinding machine’s RPM range and guarding.
- Thickness (T or W): The width of the grinding face. A thicker wheel provides more stability and a larger contact area, while a thinner wheel can access narrower features.
- Hole Size (H) or Arbor Hole: The diameter of the central hole that fits onto the grinding machine’s spindle. This must match your machine precisely.
- Rim Width (W or X for cup wheels): The width of the abrasive section on cup or dish wheels.
- Depth of Abrasive (X for some types): How deep the diamond or CBN layer is.
When choosing a shape and size, think about:
- Your Grinding Machine: What sizes and types of wheels can it safely accommodate?
- The Workpiece: What is its shape? What surfaces need to be ground? Is there clear access, or do you need a special shape to reach into corners or slots?
- The Grinding Operation: Are you grinding a flat surface, a cylindrical one, a cutting edge, or a complex profile?
For example, you wouldn’t use a large diameter straight wheel (1A1) to sharpen the intricate flutes of a small end mill; a smaller flaring cup (11V9) or dish wheel (6A2) would be much more appropriate.
Special Considerations for Achieving High-Precision Grinding Tolerances
When your goal is to achieve extremely tight dimensional tolerances (the allowable variation in a part’s size) and super-fine surface finishes, a few extra considerations come into play during wheel selection and preparation. This is common in industries like aerospace, medical device manufacturing, and precision mold making.
- Emphasis on Fine Grit Sizes and Specialized Bonds:
For ultra-precision, you’ll almost certainly be using very fine grit sizes (often in the micron range, e.g., M40, M20, M10, which correspond to very high mesh numbers). Moreover, wheel manufacturers often develop highly specialized resin bond formulations specifically for high-precision tasks. These bonds might be designed for extremely low grinding forces, exceptional surface finish, or minimal heat generation. This is an area where close consultation with your wheel supplier to select a premium, application-specific wheel is highly recommended. - Wheel Balance is Non-Negotiable:
An out-of-balance wheel will cause vibrations, leading to chatter marks, poor surface finish, and inability to hold tight tolerances. For precision work, wheels often need to be dynamically balanced on the grinding machine spindle or on a separate balancing machine. - Truing and Dressing Perfection:
While the next section will cover how to true and dress, for selection in precision contexts, understand that the wheel must be capable of being trued to a very high degree of concentricity (running perfectly true with the spindle) and dressed to expose a consistent layer of sharp abrasive grains. The bond must respond well to the chosen dressing method. - Machine Stability and Rigidity:
No grinding wheel, no matter how good, can produce precision parts on a machine that is worn, lacks rigidity, or has spindle runout. The entire grinding system (machine, wheel, workpiece, coolant) must be optimized. - Consistent Coolant Application:
For thermal stability and to effectively flush away grinding swarf (which can scratch precision surfaces), the coolant type, concentration, and delivery method must be perfectly controlled. The wheel selection might also be influenced by coolant compatibility. - Minimizing Deflection:
In precision grinding, even tiny amounts of deflection (bending) of the wheel, workpiece, or machine components can lead to errors. Selecting a wheel with appropriate stiffness (which can be related to its thickness, diameter, and bond type) for the grinding forces involved is important.
Achieving high-precision tolerances is about controlling all variables. Selecting a resin bond wheel with the right fine grit, a suitable specialized bond, and ensuring it can be perfectly prepared on a capable machine are foundational steps. For example, grinding fuel injector pintles for diesel engines to micron-level tolerances requires highly specialized fine-grit CBN resin bond wheels, exceptional machine tools, and meticulous process control.
How Can You Maximize Grinding Performance and Extend Wheel Lifespan?
You’ve invested in a quality resin bond diamond or CBN wheel – so, how do you ensure you’re unlocking its full potential for top-notch grinding results and a long operational life?
Maximizing grinding performance and extending the lifespan of your resin bond diamond or CBN wheel hinges on meticulous wheel preparation, including proper mounting, truing, and dressing. Furthermore, operating with optimal speeds, feeds, and effective coolant strategies, along with promptly troubleshooting any grinding issues, is crucial. Adhering to key safety measures and understanding how these practices contribute to overall cost-effectiveness are also vital for achieving success.
Let’s break down these essential aspects.
Essential Best Practices for Wheel Preparation: Mounting, Truing, and Dressing
Before you even start grinding, preparing your wheel correctly is like a chef sharpening their knives – it’s fundamental for a great outcome. This involves three key steps: mounting, truing, and dressing.
1. Mounting the Wheel Securely and Accurately
Mounting is about fitting the wheel onto the grinding machine’s spindle.
- Cleanliness is Key: Always ensure the machine spindle, mounting flanges (the circular plates that hold the wheel), and the wheel’s arbor hole are perfectly clean and free from any burrs, dirt, or old residues.
- Use Blotters: Blotters are compressible paper or cardboard washers that go between the wheel and the flanges. They help distribute clamping pressure evenly and compensate for any minor surface irregularities. Always use new, undamaged blotters of the correct size.
- Proper Tightening: When tightening flange screws, do it in a star or crisscross pattern, gradually and evenly. This prevents distorting the wheel or flanges, which could lead to vibration or wheel breakage. Don’t overtighten!
- Check for Runout: After mounting, use a dial indicator to check for radial runout (wobble up and down) and axial runout (wobble side to side) on the wheel’s grinding face. Excessive runout means the wheel isn’t spinning perfectly true, which will affect your grinding quality. If runout is significant, re-check your mounting procedure.
2. Truing the Wheel for Geometric Perfection
Truing makes the grinding wheel perfectly round and concentric with the spindle. It also ensures the wheel face is flat, or has the correct profile if you’re doing form grinding. Think of it as making the wheel geometrically perfect for the job.
- Why Truing is Vital: An untrue wheel will cause vibrations, poor surface finish, and inaccurate parts.
- Common Truing Methods for Resin Bond Wheels:
- Brake-Controlled Truing Device: This is a common method where a driven silicon carbide7 or aluminum oxide wheel (the “truing wheel”) is brought into contact with the rotating resin bond wheel. The brake on the truing device controls its speed, allowing it to abrade the resin bond wheel effectively.
- Dressing Sticks (for light form correction): Sometimes, coarse grit abrasive sticks can be used for minor shape corrections, though this is more related to dressing.
- Powered Rotary Dressers: For some CBN resin bond wheels, especially in high-production environments, driven diamond rotary dressers are used for precise and efficient truing.
- The truing process carefully shaves off a small amount of the bond and abrasive to achieve the desired shape and concentricity.
3. Dressing (or “Opening”) the Wheel for Optimal Cutting
After truing, the surface of the resin bond wheel might be a bit too smooth, with the abrasive particles not exposed enough to cut efficiently. This is called a “closed” wheel. Dressing, as detailed in this diamond wheel dressing guide8, roughens the surface slightly by removing a small amount of the bond material from between the abrasive grains. This exposes the sharp cutting edges of the diamond or CBN and creates space for grinding chips (swarf).
- Why Dressing Matters: A well-dressed wheel cuts more freely, generates less heat, and produces a better surface finish.
- Common Dressing Method for Resin Bond Wheels:
- Abrasive Sticks: Soft-grade aluminum oxide or silicon carbide dressing sticks are commonly used. The stick is gently pressed against the rotating, trued wheel. The stick wears away, taking some of the resin bond with it and exposing the superabrasive particles.
- Truing vs. Dressing: Remember, truing is about the wheel’s shape and concentricity. Dressing is about the wheel’s cutting condition. You always true first, then dress.
*A note on preparation: The best tools and techniques for truing and dressing can depend on the specific resin bond formulation and the abrasive type (diamond or CBN). Always consult your wheel supplier or the manufacturer’s guidelines for their recommended procedures and truing/dressing tools for the specific wheel you are using.
What Are the Optimal Operating Parameters: Speeds, Feeds, and Coolant Strategies?
Once your wheel is perfectly prepared, using the right operating parameters is like choosing the right gear and speed for your car – it ensures smooth, efficient, and safe operation.
- Wheel Speed (Surface Speed)
This is how fast the grinding surface of the wheel is moving past the workpiece, usually measured in meters per second (m/s) or surface feet per minute (SFPM).- General Ranges: For resin bond diamond wheels, typical speeds might be 15-35 m/s (approx. 3000-7000 SFPM). For resin bond CBN wheels, speeds are often higher, perhaps 25-60 m/s (approx. 5000-12000 SFPM).
- Impact of Speed:
- Too slow: Can lead to increased wheel wear, poor surface finish, and a less efficient cutting action.
- Too fast: Can cause overheating of the workpiece (burning), excessive wheel wear if the bond can’t handle it, and most importantly, can be a serious safety hazard if the wheel’s maximum rated speed is exceeded.
- Crucial Note: Optimal surface speeds are highly dependent on the specific wheel bond, abrasive type, material being ground, the rigidity of the grinding machine, and the coolant used. Always adhere to the maximum operating speed marked on the wheel and consult the manufacturer’s recommendations for the ideal speed range for your application.
- Workpiece Speed and Feed Rates
These parameters control how quickly material is presented to the grinding wheel.- Workpiece Speed: In operations like cylindrical grinding, this is how fast the workpiece is rotating.
- Table Speed / Traverse Rate: In surface grinding, this is how fast the machine table (carrying the workpiece) moves back and forth.
- Infeed / Depth of Cut: This is how much material the wheel removes in a single pass or how deeply it’s plunged into the workpiece.
- General Approach for Resin Bonds: Resin bond wheels often perform best with moderate depths of cut and feed rates. Trying to remove too much material too quickly can overload the wheel, leading to excessive heat, poor finish, and rapid wear.
- It’s a balancing act: faster feeds and deeper cuts increase the material removal rate (MRR), but can negatively impact surface finish and wheel life. Slower, lighter passes generally improve finish and precision. Again, starting with conservative parameters and gradually optimizing based on results and supplier advice is a good strategy.
- Coolant Strategies: More Than Just Keeping Things Cool
Coolant (or grinding fluid) plays multiple vital roles in grinding, especially with superabrasives:- Cooling: It carries away the heat generated in the grinding zone, preventing thermal damage to the workpiece (like burning or changes in hardness) and protecting the integrity of the resin bond.
- Lubrication: It reduces friction between the abrasive grains, the workpiece, and the grinding chips. This can lead to a better surface finish and reduced grinding forces.
- Swarf Removal (Cleaning): It flushes away the tiny chips of material (swarf) being removed, preventing them from clogging (loading) the wheel or scratching the workpiece surface.
- Common Coolant Types: Water-soluble coolants (synthetics, semi-synthetics) are very common with resin bond wheels. They offer good cooling and cleaning properties.
- Application is Key:
- Generous Flow: You need enough coolant to flood the grinding zone effectively.
- Correct Nozzle Placement: Aim the coolant jets precisely where the wheel meets the workpiece.
- Filtration: Good coolant filtration is essential to remove swarf and keep the coolant clean, which helps maintain workpiece quality and extends coolant life.
Effective coolant use is particularly important for resin bond wheels because the resin can be sensitive to excessive heat.
Effectively Troubleshooting Common Grinding Issues and Implementing Solutions
Even with the best preparation and parameters, you might sometimes encounter grinding problems. Knowing how to identify and fix them can save a lot of time and material. Here are some common issues:
Issue | Likely Causes | Possible Solutions |
---|---|---|
Wheel Glazing | Wheel surface is smooth, shiny, and not cutting. | Dress the wheel to expose fresh abrasive. Use a softer grade wheel or coarser grit if the problem persists. Check if speed is too high/feed too low. |
Wheel Loading | Grinding swarf is packed into the wheel face, preventing cutting. Often seen with softer or gummy materials. | Dress the wheel. Ensure good coolant flow and filtration. Consider a wheel with a more open structure, coarser grit, or specific bond modifications. |
Chatter Marks/Vibration | Wavy or patterned marks on the workpiece surface. | Balance the wheel. Re-true and dress. Check machine for loose components (spindle bearings, gibs). Secure workpiece firmly. Adjust speeds/feeds. |
Burning of Workpiece | Discoloration (blue, brown) or other signs of thermal damage on the workpiece. | Reduce wheel speed, depth of cut, or feed rate. Improve coolant supply (flow, direction). Dress the wheel (if glazed/loaded). Use a softer grade/coarser grit wheel. |
Poor Surface Finish | Surface is rougher than desired. | Use a finer grit wheel. Optimize dressing technique (lighter dressing). Check for machine vibration. Ensure coolant is clean and effective. Reduce feed rate. |
Rapid Wheel Wear | Wheel is wearing down too quickly. | Ensure the wheel is not too soft for the material/operation. Reduce depth of cut or feed rate. Improve coolant. Verify correct abrasive type is being used. |
Wheel Breakage | Serious safety hazard. | STOP IMMEDIATELY. Investigate cause: over-speeding, damaged wheel, incorrect mounting, excessive impact, machine fault. Do not reuse. |
When troubleshooting, it’s usually best to change only one thing at a time so you can pinpoint the exact cause of the problem.
Key Safety Measures to Observe When Operating Superabrasive Wheels
Safety should always be your number one priority when working with any grinding wheel, including resin bond diamond and CBN wheels. These wheels operate at high speeds, and accidents can be severe. Adherence to standards like ANSI B7.1 is fundamental.
- Always Wear Personal Protective Equipment (PPE):
- Eye Protection: Safety glasses with side shields are a minimum. A full-face shield provides even better protection from flying particles.
- Hand Protection: Wear suitable gloves when handling wheels to protect from sharp edges, but be cautious about gloves getting caught in moving machinery during operation.
- Respiratory Protection: If dry grinding or if significant dust is generated (even with coolant), use an appropriate dust mask or respirator.
- Protective Clothing: Close-fitting clothing, and consider aprons if needed.
- Inspect the Wheel Before Mounting: Carefully check for any cracks, chips, or other visible damage. While the “ring test” (tapping a wheel to hear its sound) is common for vitrified wheels, it’s generally not effective for resin bond wheels. A thorough visual inspection is key. If damaged, do not use it.
- Ensure Machine Guarding is in Place: All safety guards provided by the machine manufacturer must be in place, properly adjusted, and in good condition. They are there to contain fragments in the unlikely event of a wheel breakage.
- Never Exceed Maximum Operating Speed: The maximum safe operating speed (in RPM) is marked on the wheel or its packaging. Ensure your machine’s spindle speed does not exceed this limit.
- Mount Wheels Correctly: Follow the proper mounting procedures discussed earlier.
- Secure the Workpiece: Make sure the part you are grinding is held firmly in a fixture, vise, or chuck.
- Stand Aside During Start-Up: After mounting a new wheel and before starting to grind, let the wheel run at operating speed for at least one minute with no one standing directly in line with it. This is a precaution in case there’s an unseen defect.
- Apply Gradual Pressure: Don’t jam or force the workpiece into the wheel. Apply steady, even pressure.
- Be Aware of Your Surroundings: Know where sparks and swarf are being directed. Ensure no flammable materials are nearby.
- Maintain Your Machine: Regularly inspect and maintain the grinding machine, including spindle bearings, belts, and guarding.
Grinding can be done safely if you respect the machine and the wheel and always follow established safety protocols.
Understanding the Impact of Proper Use on Overall Cost-Effectiveness and ROI
Using your resin bond diamond or CBN wheels correctly isn’t just about getting good parts; it’s also about saving money in the long run. The “Return on Investment” (ROI) for your grinding wheels is significantly impacted by how well you use them.
- Extended Wheel Life = Lower Wheel Costs:
Proper preparation (truing/dressing), optimal operating parameters, and effective troubleshooting directly lead to longer wheel life. If you can make a wheel last 20-50% longer through good practices, you’re buying fewer wheels over time, which directly reduces your consumable costs.- Example: A company grinding carbide tools found that by implementing a strict wheel dressing schedule and optimizing coolant flow, they extended the life of their resin bond diamond wheels by 30%, saving thousands of dollars annually on wheel replacements.
- Improved Workpiece Quality = Less Scrap and Rework:
When wheels are used correctly, you get parts that meet dimensional specifications and surface finish requirements the first time. This means:- Less material wasted due to scrapped parts.
- Less time and labor spent on reworking parts that are out of spec.
- Fewer customer rejections.
- Increased Productivity = More Parts Per Shift:
While you shouldn’t be overly aggressive, optimized parameters mean you can often achieve good material removal rates without sacrificing wheel life or quality. A well-maintained, free-cutting wheel grinds more efficiently. This translates to:- Shorter cycle times per part.
- More output from your grinding machines and operators.
- Reduced Machine Downtime = More Uptime:
When grinding operations run smoothly, there’s less unexpected downtime for troubleshooting, emergency wheel changes, or machine repairs caused by improper use. - Thinking About Total Cost of Ownership (TCO)9:
The initial purchase price of a grinding wheel is only one part of its true cost. The TCO includes the wheel price, but also factors in how long it lasts, the quality of parts it produces, its impact on productivity, and any associated labor or rework costs.- A slightly more expensive, high-quality resin bond wheel that is used properly can often have a lower TCO than a cheaper wheel that wears out quickly or produces inconsistent results.
- For instance, investing time in operator training on proper wheel dressing might seem like an expense, but if it leads to a 10% reduction in wheel consumption and a 5% decrease in scrapped parts, the ROI on that training can be very high.
By focusing on proper use, you’re not just grinding parts; you’re optimizing an entire system for cost-effectiveness and a better return on your investment in superabrasive tooling.
Conclusion
Mastering the selection and application of resin bond diamond and CBN grinding wheels is a journey that combines understanding the fundamental science of these advanced tools with practical, hands-on knowledge. By recognizing the unique advantages of resin bonds, diligently applying critical selection criteria for your specific material and task, and committing to best practices in wheel preparation, operation, and maintenance, you can significantly enhance your grinding outcomes.
Ultimately, the goal is not just to grind a part, but to do so efficiently, accurately, safely, and cost-effectively. The insights provided aim to empower you to achieve precisely that, transforming your grinding operations and maximizing the return on your investment in these sophisticated superabrasive products. Remember that ongoing learning and close consultation with your wheel supplier are key components of continuous improvement in the ever-evolving field of precision grinding.
Ready to achieve superior grinding results? Explore our extensive range of Resin Bond Diamond and CBN Grinding Wheels. If you don’t see the exact specifications you need, remember we specialize in custom-designing wheels to meet your unique application requirements. Contact us today to discuss your project and let us help you find the perfect grinding solution!
References
- phenolics1 – ScienceDirect article providing an overview of phenolics, including their use in resins.
- metal bonds2 – ZYDiamondTools blog post detailing reasons and applications for metal bond diamond/CBN grinding wheels.
- Tungsten Carbide3 – Britannica article providing an overview of tungsten carbide, its properties, and uses.
- choosing the right abrasive type4 – ZYDiamondTools blog post guiding the selection between CBN and diamond grinding wheels.
- how to select the right diamond grinding wheel5 – ZYDiamondTools blog post on selecting diamond grinding wheels for specific processes.
- 3A1 Resin Bond Diamond Grinding Wheels6 – ZYDiamondTools product page for 3A1 type resin bond diamond grinding wheels.
- silicon carbide7 – Wikipedia article detailing Silicon Carbide, a common abrasive material.
- diamond wheel dressing guide8 – ZYDiamondTools practical how-to guide on mastering diamond wheel dressing.
- Total Cost of Ownership (TCO)9 – ZYDiamondTools guide explaining Total Cost of Ownership for superhard tooling and abrasives.
ZY Superhard Tools Co., Ltd.
Do you have any needs for PCD tools or diamond grinding wheels? We can customize products to meet your specific requirements. If you have any ideas or requests, feel free to reach out—we’ll respond within 24 hours!
Do you have any needs for PCD & CBN tools or diamond grinding wheels? We can customize products to meet your specific requirements. If you have any ideas or requests, feel free to reach out—we’ll respond within 24 hours!
Do you have any needs for PCD & CBN tools or diamond grinding wheels? We can customize products to meet your specific requirements. If you have any ideas or requests, feel free to reach out—we’ll respond within 24 hours!
Post Categories
Product Categories
About Company
Related Posts
Rough Boring vs. Finish Boring: How to Choose the Right Process for Optimal Results?
Explore the key differences between rough boring for speed and finish boring for precision. Our guide compares technical specs, tooling,
What Is Honing and How Does It Achieve a Perfect Surface Finish?
Learn what honing is and how it creates perfect surfaces. This guide covers the process, tools, stone selection, and how
PCD Drilling Tools: Understanding Their Value and How to Select the Perfect One for Your Application
Unlock top performance with PCD drilling tools. This in-depth guide covers selection, benefits, and use cases to help you improve
Mastering PCD Countersinking for aerospace Composites: Advanced Techniques for Optimal Performance and Hole Quality
Master PCD countersink drilling for aerospace composite. Your guide to optimal PCD tool selection, design insights, and process control for
Subscribe
Simply enter your email below and click “Subscribe” to stay connected with everything new and exciting.