-
Whatsapp: +86 13526572721
-
Email: info@zydiamondtools.com
-
Address: AUX Industrial Park, Zhengzhou City, Henan Province, China
-
Whatsapp: +86 13526572721
-
Email: info@zydiamondtools.com
-
Address: AUX Industrial Park, Zhengzhou City, Henan Province, China
How Do You Select the Right Diamond Grinding Wheel for Your Specific Process?
- Grinding Wheels Knowledge
- -2023-01-06
- - byKevin Ray
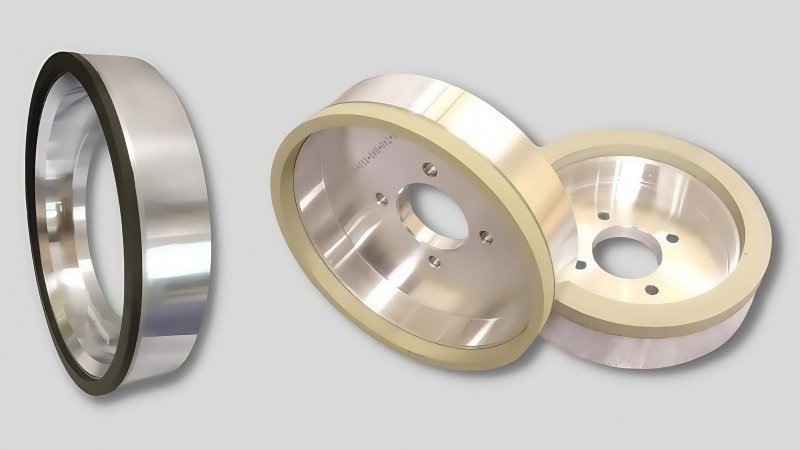
So, how do you actually select the right diamond grinding wheel for your specific process?
Selecting the right diamond grinding wheel involves carefully considering several critical factors: the material being ground, the appropriate bond type (resin, metal, vitrified, electroplated), the required diamond grit size for speed versus finish, the diamond concentration affecting life and cutting action, the correct wheel shape and size for the operation and machine, and whether to grind wet or dry.
Table of Contents
ToggleWhat Material Are You Grinding?
So, what is the very first thing you need to think about when picking a diamond grinding wheel?
The type of material you plan to grind is the single most important factor guiding your diamond grinding wheel selection. Because different materials behave differently, the material directly influences the best choice for the wheel’s bond type, diamond grit size, and concentration, ensuring efficient grinding and preventing damage to both the wheel and your workpiece.
Understanding the material you’re working with is truly step one. It sets the stage for all other choices you’ll make about the grinding wheel. Let’s look at some common material groups.
Matching Wheel Specs to Common Materials (Concrete, Stone)
Concrete and natural stone (like granite or marble) are quite common materials needing grinding, perhaps for smoothing floors or shaping countertops. These materials share some key traits:
- Abrasive Nature: They contain hard particles (like sand and aggregate in concrete, or crystals in stone) that wear down grinding wheels quickly. Think of it like sandpaper rubbing against sandpaper – it causes a lot of wear.
- Bulk Removal Needs: Often, the goal is to remove a good amount of material quickly, rather than achieving a mirror finish initially.
Consequently, when grinding concrete or stone, you generally need wheels built for toughness. This usually means:
- Durable Bonds: Wheels often use metal bonds. These bonds are tough and hold onto the diamond particles securely, even when grinding rough, abrasive surfaces. This helps the wheel last longer. (We’ll explore bond types more later!)
- Specific Segment Design: For floor grinding, cup wheels often have specially shaped segments designed to handle large surface areas and clear away dust effectively.
- Grit Size Consideration: While it depends on the finish needed, initial grinding on these materials frequently uses coarser diamond grits to remove material faster.
A Quick Note: Keep in mind that concrete mix designs vary, and different types of stone have unique hardness levels (granite is much harder than marble, for instance). Therefore, it’s always a good idea to check the wheel manufacturer’s recommendations for the specific type of concrete or stone you’re grinding.
Considerations for Hard & Brittle Materials (Carbide, Ceramics, Glass)
Now, let’s consider materials like tungsten carbide1 (used in cutting tools), engineered ceramics (found in electronics or wear parts), and glass. These materials are quite different from concrete:
- Extreme Hardness: They are often significantly harder than stone or metal.
- Brittleness: They can chip or crack easily if subjected to too much force or vibration—a property known as brittleness. Imagine tapping glass incorrectly – it shatters rather than bending.
- Heat Sensitivity: Some ceramics and carbide tools can be damaged by excessive heat generated during grinding.
Because of these properties, choosing a wheel requires a different approach:
- Preventing Chipping: Using finer diamond grits is often essential. Finer grits take smaller “bites” out of the material, reducing the risk of chipping and producing a smoother finish right away.
- Bond Selection is Critical:
- Resin bonds are frequently used because they offer a softer grinding action and generate less heat, protecting sensitive materials.
- Vitrified bonds might be chosen for high-precision grinding on some ceramics due to their rigidity and ability to hold form.
- Sharp Diamonds Needed: The wheel needs very sharp, high-quality diamonds to cut these hard materials cleanly without just rubbing and creating heat.
For example, sharpening a carbide router bit requires a wheel (often resin bond with a fine grit) that can precisely remove material without overheating or chipping the delicate cutting edge. Similarly, shaping a ceramic component for a medical device demands extreme precision and minimal subsurface damage.
Guidelines for Metals and Composites
This group includes materials like non-ferrous metals (aluminum, copper – though diamond isn’t always the first choice here) and advanced composites.
Grinding Non-Ferrous Metals and Metal Matrix Composites (MMCs)
While Cubic Boron Nitride (CBN) wheels are generally preferred for grinding ferrous metals (like steel and cast iron) due to a chemical reaction between diamond and iron at high temperatures, diamond wheels are used for:
- Non-Ferrous Metals: Aluminum or copper alloys in some specific applications. A key challenge here can be “loading,” where the soft metal clogs the wheel. Wheel design must account for this.
- Metal Matrix Composites (MMCs): These combine metals with reinforcing materials (like ceramics). Diamond wheels are often needed to effectively grind the hard reinforcement.
The choice here involves selecting bonds and grits that cut freely and resist loading up with metal particles.
Tackling Composite Materials (CFRP, GFRP)
Composites like Carbon Fiber Reinforced Polymer (CFRP) and Glass Fiber Reinforced Polymer (GFRP) are becoming very common in aerospace, automotive, and sporting goods. They pose unique grinding challenges:
- Abrasive Fibers: The carbon or glass fibers are very abrasive.
- Softer Matrix: These fibers are held in a much softer polymer (plastic) matrix.
- Risk of Damage: Poor grinding can cause delamination (layers separating), fiber pull-out, or excessive heat buildup melting the matrix.
Therefore, wheels for composites often feature:
- Sharp Diamonds: Essential for cleanly shearing the fibers rather than pushing them aside. Electroplated bonds, which expose a single layer of very sharp diamond, are common for aggressive cutting or shaping (like routing).
- Specialized Geometries: Wheels might have specific shapes or edge preparations to minimize chipping or fraying of the composite material.
- Finer Grits for Finishing: Similar to brittle materials, finer grits help achieve a clean edge finish.
Successfully grinding a CFRP aircraft component, for example, requires a wheel that cuts cleanly through the abrasive fibers without damaging the surrounding resin matrix, ensuring the part’s structural integrity.
Which Diamond Bond Type Suits Your Task?
Now that you understand how the material you’re grinding is the starting point, what holds the diamonds in the wheel, and why does it matter so much?
The bond is the material matrix that holds the diamond abrasive particles within the grinding wheel; choosing the correct bond type is critical because it determines the wheel’s wear rate, heat generation, cutting action, and overall suitability for specific materials and grinding operations. Essentially, the bond controls how effectively the diamonds are presented to the material being ground.
Think of the bond as the specific “glue” holding the super-hard diamond crystals. Different types of “glue” have vastly different properties, making them suitable for different jobs. Let’s explore the main types:
Resin Bonds: For Heat-Sensitive Materials & Fine Finishes
Imagine a strong, slightly flexible adhesive – that gives you an idea of a resin bond. These bonds are made from synthetic resins, often mixed with fillers.
- Key Characteristics:
- Softer Grinding Action: Resin bonds wear away relatively easily compared to other types. This sounds bad, but it’s actually beneficial as it constantly exposes fresh, sharp diamond particles.
- Lower Heat Generation: Because they wear away and offer less friction, resin bonds generate less heat during grinding.
- Good Surface Finish: They are excellent for achieving smooth, fine surface finishes.
- Primary Uses:
- Grinding hard but heat-sensitive and brittle materials like tungsten carbide, ceramics, and glass (connecting back to our material discussion).
- Applications requiring a high-quality surface finish.
- Common in tool and cutter grinding (like sharpening drill bits or end mills) and precision grinding operations.
- Example: When resharpening carbide cutting tools, a resin bond wheel is often chosen because it can remove material precisely without generating excessive heat that could damage the tool’s temper or cause micro-cracking.
However, this easier wear means resin bonds typically don’t last as long as harder bonds when grinding very rough or abrasive materials.
Metal Bonds: For Durability in Abrasive Materials
Picture the diamonds securely locked within a tough metal framework – that’s a metal bond. These bonds use powdered metals (like bronze, steel, or tungsten alloys) joined together through a process called sintering2 to hold the diamonds. You can learn more about why metal bonds are chosen3 for specific applications.
- Key Characteristics:
- Extreme Durability & Wear Resistance: Metal bonds are very hard and hold diamonds extremely securely. They wear down very slowly.
- High Heat Resistance: They can withstand high temperatures generated during heavy grinding.
- Long Lifespan: Their toughness translates to a long service life, especially under demanding conditions.
- Primary Uses:
- Grinding highly abrasive materials such as concrete, natural stone (granite), asphalt, and some abrasive composites.
- Applications involving heavy stock removal where longevity is crucial.
- Widely used in the construction and stone industries for cutting, grinding, and polishing.
- Example: Grinding down high spots on a concrete floor uses metal-bond diamond segments because they can withstand the constant abrasion from the sand and aggregate, lasting through large surface areas.
While incredibly durable, metal bonds can sometimes generate more heat and may not produce the finest finishes without follow-up steps using different wheels. Their rigid nature demands sturdy grinding equipment.
Vitrified Bonds: For Precision & High-Efficiency Grinding
Think of vitrified bonds like diamonds embedded in a very hard, strong, but porous ceramic or glassy structure. They are formed by fusing glassy materials at high temperatures, also often involving sintering.
- Key Characteristics:
- High Rigidity & Form Holding: Vitrified bonds are very stiff and hold their shape extremely well, making them ideal for precision profile grinding.
- Porosity: They naturally have pores or spaces within the bond. This helps with coolant delivery (in wet grinding) and clearing away grinding debris (swarf).
- Aggressive Cutting: They offer a free-cutting action, allowing for high material removal rates.
- Dressable: They can be easily trued and dressed to maintain precise geometry and cutting performance. Information on how to dress diamond wheels4 can be useful here.
- Primary Uses:
- Precision grinding of hard materials like advanced ceramics, some types of carbide, and hardened steels (though CBN is often preferred for steels).
- High-production environments where speed, accuracy, and maintaining tight tolerances are essential (e.g., automotive or aerospace component manufacturing).
- Example: Manufacturing precision ceramic ball bearings requires grinding to extremely tight dimensional and geometric tolerances. Vitrified bond diamond wheels provide the necessary rigidity, cool cutting action (with porosity), and high material removal rates for this demanding application.
Vitrified bonds are less impact-resistant than metal bonds and typically require very stable, high-precision grinding machines.
Electroplated Bonds: For Aggressive Stock Removal & Profile Grinding
This type is different – imagine a single layer of diamond particles attached directly to the wheel’s core using a layer of electroplated nickel.
- Key Characteristics:
- Maximum Diamond Exposure: With only a single layer, a large portion of each diamond particle is exposed, leading to a very aggressive cut.
- Excellent Form Holding (Initially): Because the diamonds are plated onto a pre-formed core, they hold complex shapes very accurately at first.
- Fast Stock Removal: They offer the highest initial material removal rates among bond types.
- Non-Dressable: Once the single diamond layer wears down, the wheel is depleted and cannot be re-sharpened or dressed.
- Primary Uses:
- Grinding complex profiles or contours.
- Rapid cutting or shaping of materials like composites (FRP), plastics, or graphite.
- Applications where initial cutting speed is more critical than overall tool life, or for short production runs.
- Example: Trimming or shaping Fiber Reinforced Polymer (FRP) components in boat building or automotive applications often uses electroplated diamond routers or specialized wheels for their ability to quickly follow contours and cut through the abrasive fibers aggressively.
The major trade-off for electroplated wheels is their relatively short lifespan compared to bonded wheels containing multiple layers of diamond.
Remember: Bond formulations can be complex, with variations even within these main categories. Specific performance characteristics can differ between manufacturers, so consulting supplier specifications for your intended application is always recommended.
How Does Grit Size Affect Your Results?
Alright, we know the material matters and the bond holding the diamonds is key, but what about the diamonds themselves – specifically, how big are they?
Grit size refers to the size of the individual diamond particles embedded in the wheel’s bond; it directly controls the trade-off between how fast you remove material and how smooth the resulting surface finish will be. In simple terms, larger diamond grits (coarse) cut faster but leave a rougher surface, while smaller grits (fine) cut slower but produce a much smoother finish.
Think of it just like sandpaper. Rough sandpaper (low grit number) removes wood quickly but leaves deep scratches. Fine sandpaper (high grit number) removes wood slowly but leaves a very smooth surface. Diamond grinding wheels work on the same principle. Grit sizes are typically designated by numbers – lower numbers mean coarser grits, higher numbers mean finer grits according to various abrasive grit standards.
Coarse Grits: Prioritizing Material Removal Speed
Coarse grits use larger diamond particles. Imagine using chunky, sharp rocks instead of fine sand for sanding.
- Typical Grit Range: Usually includes lower numbers like 20/30, 30/40, 50/60, or 60/80. Be aware that different grit standards (like FEPA or ANSI) exist, so these numbers can vary slightly. Always check the manufacturer’s specific designation and recommendations.
- Characteristics:
- Fast Material Removal: Each large diamond particle takes a significant “bite” out of the material, leading to rapid stock removal.
- Rough Surface Finish: This aggressive action leaves behind a visibly rough surface with noticeable scratch patterns.
- Higher Grinding Force: Can sometimes require more machine power and generate more heat compared to finer grits.
- Best For:
- Initial grinding stages where removing a lot of material quickly is the main goal (bulk stock removal).
- Leveling very uneven surfaces.
- Applications where the final surface finish is not critical or will be refined in later steps.
- Example: When preparing an old concrete floor that has many imperfections, the process almost always starts with coarse metal-bond diamond segments (perhaps 30/40 grit) to aggressively grind down high spots and expose a fresh, level surface quickly.
Medium Grits: Balancing Speed and Finish
Medium grits represent the middle ground, using diamond particles that are neither exceptionally large nor extremely small.
- Typical Grit Range: Includes intermediate numbers such as 70/80, 100/120, or 120/140. Again, refer to the specific standard and manufacturer data.
- Characteristics:
- Balanced Performance: Offers a reasonable compromise between the speed of coarse grits and the finish of fine grits.
- Scratch Removal: Effectively removes the deeper scratches left behind by coarser grits.
- General Purpose: Suitable for a wide range of tasks that don’t require extreme speed or an ultra-fine finish.
- Best For:
- Intermediate grinding steps, bridging the gap between rough grinding and final polishing.
- General shaping or grinding where moderate speed and a decent finish are acceptable.
- Some less demanding tool sharpening or surface preparation tasks.
- Example: After the initial coarse grind on a concrete or stone surface, a switch to medium grits (like 100/120) helps to smooth out the texture, remove the coarse scratch pattern, and prepare the surface for subsequent finer polishing stages.
Fine Grits: Achieving Smooth Surface Finishes
Fine grits utilize very small, densely packed diamond particles, much like using polishing powder or the finest grades of sandpaper.
- Typical Grit Range: Includes higher numbers, such as 200/220, 400, 800, 1500, 3000, and sometimes even higher for specialized polishing. The exact numbering and availability depend heavily on the wheel type and supplier.
- Characteristics:
- Slow Material Removal: Each tiny particle takes only a very small “bite,” resulting in a much slower grinding process.
- Smooth, Fine Finish: Produces a very smooth surface with minimal or no visible scratches. Higher grits lead to more reflective, polished finishes.
- Reduced Chipping: The gentle cutting action is ideal for grinding brittle materials like glass, ceramics, or carbide, as it significantly reduces the risk of chipping or edge damage.
- Best For:
- Final finishing and polishing steps to achieve a desired level of smoothness or gloss.
- Applications requiring high precision and excellent surface quality.
- Grinding brittle or delicate materials where minimizing damage is critical.
- Example: Achieving that mirror-like polish on a granite countertop involves using a sequence of progressively finer resin-bond diamond pads, often starting around 200 or 400 grit and moving up to 1500, 3000, or even higher “buff” pads. Likewise, grinding the precise edge on a delicate ceramic component might use an 800 grit or finer wheel to ensure smoothness and prevent chipping.
Choosing the right grit size involves understanding your goal: do you need to remove material fast, or do you need a perfect finish? Often, achieving both requires starting coarse and working your way up through progressively finer grits.
What Role Does Diamond Concentration Play?
So, you know the diamond size, but how much diamond is actually packed into the wheel, and why is that important?
Diamond concentration indicates the volume percentage of diamond abrasive within the bond matrix; it significantly impacts the wheel’s cutting speed, its usable lifespan, and the grinding pressure required. Generally, higher concentrations provide longer life but cut slower, while lower concentrations cut faster but wear out more quickly.
Think about making chocolate chip cookies. Grit size is like using mini chips versus big chunks. Concentration, however, is about how many chips you pack into each cookie. A low concentration wheel has fewer “chips” (diamonds), while a high concentration wheel is packed full.
Understanding Concentration Values (Low vs. High)
Concentration is usually indicated by a number. A common scale uses values like 25, 50, 75, and 100, where 100 is considered a standard reference point (representing 25% diamond by volume in the abrasive layer). Higher concentrations, like 125, are also sometimes used.
- Low Concentration (e.g., 25, 50): Contains a relatively smaller amount of diamond abrasive per unit volume of the bond.
- High Concentration (e.g., 75, 100, 125): Contains a larger amount of diamond abrasive packed into the same volume of bond.
Important Note: While these numbers provide a standard scale, the exact percentage of diamond and the overall performance also depend on the specific bond formulation used by the manufacturer. Therefore, it’s wise to consult the supplier’s data for detailed specifications.
Impact on Cutting Speed and Wheel Lifespan
The concentration level creates a fundamental trade-off between how fast the wheel cuts and how long it lasts:
- Low Concentration Wheels:
- Cutting Speed: Tend to cut faster and more freely. Why? With fewer diamonds, there’s higher pressure on each individual cutting point, allowing for deeper penetration into the material. There’s also more space between diamonds for chips (swarf) to be cleared away easily.
- Lifespan: Tend to wear out faster. Why? The workload is shared among fewer diamond particles, causing each one to wear down more quickly. The surrounding bond material also erodes faster relative to the amount of diamond doing the work.
- High Concentration Wheels:
- Cutting Speed: Tend to cut slower and may require higher grinding pressure. Why? The grinding force is distributed over many more diamond points, leading to shallower penetration for each one. Less space between diamonds can also hinder chip clearance slightly.
- Lifespan: Tend to last significantly longer. Why? The workload is spread across a much larger number of diamonds, reducing the wear rate of individual particles. The bond itself lasts longer relative to the diamond content.
It’s worth noting this relationship isn’t always perfectly linear – doubling the concentration won’t necessarily double the lifespan or exactly halve the cutting speed, as other factors are always at play.
Matching Concentration to Bond Type and Application
So how do you choose the right concentration? It depends heavily on the bond type you’re using and what you need to achieve:
- Interaction with Bond Type:
- Softer Bonds (like Resin): Often perform better with lower to medium concentrations (e.g., 50-75). Since the bond wears away easily to expose new diamonds (which is good for resin!), packing it too densely with diamonds (high concentration) might actually hinder this process or lead to the wheel surface “glazing” over. Lower concentrations allow for a cooler, freer cut, often desired for fine finishes.
- Harder Bonds (like Metal or Vitrified): Frequently utilize higher concentrations (e.g., 75-100 or more). Because these bonds are very durable and resist wear, a higher diamond concentration is needed to ensure a long lifespan. The bond is strong enough to hold onto the diamonds even under heavy load.
- Matching to Application:
- Heavy Stock Removal (e.g., Rough concrete grinding): A high concentration (perhaps 75 or 100) in a durable metal bond is often preferred for maximum wheel life during this demanding task.
- Precision Finishing (e.g., Carbide tool polishing): A lower concentration (perhaps 50 or 75) in a softer resin bond might be chosen to provide a cooler cutting action, prevent heat damage, and achieve a superior surface finish.
- Form Holding (e.g., Grinding profiles with Vitrified): Concentration choice here carefully balances the need for the wheel to hold its shape (higher concentration helps) against the need for efficient cutting.
Ultimately, the ideal concentration is a balance. It’s tied closely to the material being ground, the bond used, the grit size selected, the grinding machine’s capabilities (power, rigidity), and the specific goals of the operation (speed vs. finish vs. life). Don’t hesitate to review manufacturer charts or consult their technical support for recommendations tailored to your specific process.
Understanding Wheel Shape and Size
Beyond the wheel’s internal makeup (‘ingredients’), its physical form—shape and size—also plays a crucial role. Why do these physical aspects matter so much?
Yes, the shape and size of a diamond grinding wheel are absolutely critical; the shape dictates how the wheel interacts with the workpiece and is chosen based on the specific grinding operation (like surface grinding vs. edge grinding), while the size must precisely match the specifications of your grinding machine for safe and effective operation.
Choosing the wrong shape means you might not be able to grind the area you need to, while choosing the wrong size can be inefficient at best, and extremely dangerous at worst. Let’s break down these physical aspects.
Common Shapes and Their Primary Uses (Cup, Straight, Profile, etc.)
Diamond grinding wheels come in various shapes, each designed for different ways of contacting the material:
- Straight Wheels (Type 1): These are the basic flat discs, like a thick hockey puck. They primarily grind using their outer edge (periphery).
- Use: Common in surface grinding machines, cylindrical grinding (grinding round parts), and some tool sharpening.
- Cup Wheels (Type 6 – Straight Cup, Type 11 – Flaring Cup): Shaped like a cup or bowl, these grind using the flat rim or face of the wheel. Flaring cups angle outwards, sometimes offering better visibility.
- Use: Very common for grinding large flat surfaces (especially concrete floors with angle grinders or floor machines), creating bevels, or edge grinding.
- Dish Wheels (Type 12): Resemble a shallow dish with a thin grinding rim.
- Use: Designed for grinding in tight spaces, slots, or creating clearance angles in tool and cutter grinding.
- Profile or Form Wheels: These wheels have their grinding edge specifically shaped to create a desired profile on the workpiece (e.g., a rounded “bullnose” edge, a decorative “ogee” edge, or a specific groove).
- Use: Creating decorative edges on stone countertops, grinding specific forms onto tools, matching existing profiles.
Other specialized types exist, like small mounted points for detail work or thin cut-off wheels for slicing, but the shapes above cover most common grinding operations.
Selecting Shape Based on Your Grinding Operation
The task you need to perform directly dictates the best wheel shape:
- Grinding Flat Surfaces: You’ll likely use the face of a Cup Wheel (common on angle grinders/floor machines) or the periphery of a Straight Wheel (common on bench grinders or dedicated surface grinders5).
- Grinding Edges or Chamfers: Cup Wheels used on their face are often ideal. Specially angled straight wheels can also be used.
- Grinding Inside Slots or Grooves: Thin Straight Wheels or specialized Dish Wheels are needed to fit within the confined space.
- Creating Specific Shapes: You must use a Profile Wheel that exactly matches the contour you need to produce.
- Sharpening Tools: This often involves multiple shapes depending on the tool – perhaps a Straight Wheel for the cylindrical part of a drill bit and a Dish or Cup Wheel for the cutting edges and flutes.
Think about how the wheel needs to touch the workpiece – on its edge, its face, or a special contour? That will guide your shape selection.
Ensuring Size Compatibility with Your Machine (Diameter, Arbor Hole)
This part is absolutely critical for safety and proper function. You must match the wheel size to your grinder:
- Overall Diameter: The wheel’s diameter must be suitable for your machine. Using a wheel that’s too large might mean it won’t fit inside the machine’s safety guard (which should always be used!) or could over-stress the motor. Using one that’s too small might be inefficient.
- Arbor Hole Size: This is the central hole that fits onto the grinder’s spindle (the rotating shaft). The arbor hole on the wheel MUST exactly match the diameter of your machine’s spindle. A hole that’s too small simply won’t fit. A hole that’s too large will cause the wheel to be off-center, leading to dangerous vibrations and potential wheel failure. Arbor sizes are standardized (e.g., 7/8″, 20mm, 5/8″-11 threaded), but always double-check both the wheel marking and your machine’s specification.
- Wheel Thickness (for Straight Wheels): Ensure the thickness is appropriate for your machine and the task.
- Maximum Safe Operating Speed (RPM): Every grinding wheel has a maximum RPM rating marked on it, adhering to safety standards like ANSI B7.1. This RPM rating MUST be greater than or equal to the maximum operating speed of your grinder. Never mount a wheel on a grinder that spins faster than the wheel’s maximum rated speed. Doing so risks catastrophic wheel breakage, which can cause severe injury. Always verify both the wheel’s RPM rating and your grinder’s speed.
Trying to force fit the wrong size wheel or exceeding the RPM limit is extremely hazardous. For instance, mounting a large 7-inch cup wheel meant for a low-RPM floor grinder onto a small, high-RPM angle grinder6 is a recipe for disaster due to mismatches in diameter, arbor type, and especially speed rating. Always prioritize safety and compatibility.
Should You Grind Wet or Dry?
You’ve got the right wheel composition and shape, but does it matter if you use water while grinding?
Yes, the choice between wet grinding (using a liquid coolant, usually water) and dry grinding significantly impacts heat generation, dust control, wheel lifespan, and surface finish. While wet grinding is generally preferred for its numerous benefits, dry grinding is sometimes necessary or more practical, often requiring wheels specifically designed to handle the increased heat and lack of lubrication.
Making the right choice here affects not only the quality of your work but also your safety and the longevity of your diamond wheel. Let’s look at the pros and cons.
Advantages of Wet Grinding (Cooling, Dust Suppression, Longevity)
Using water or a coolant during grinding offers several major advantages, making it the preferred method in many professional applications:
- Superior Cooling: Grinding generates a lot of friction and heat. Water acts like constantly pouring coolant onto a hot engine part – it effectively absorbs and carries away heat from both the workpiece and the grinding wheel. This is critical for:
- Preventing heat damage to sensitive materials (like carbide, ceramics, or tempered parts).
- Protecting the wheel’s bond (especially resin bonds) from overheating and degrading prematurely.
- Excellent Dust Suppression: This is a huge health and safety benefit. Grinding materials like concrete, stone, or ceramics creates fine dust (including potentially harmful silica dust7). Water captures this dust at the source, turning it into a manageable slurry instead of letting it become airborne where it can be inhaled. Think of trying to sweep dry sand versus wet sand – the water keeps it down. Proper slurry management is also important for environmental reasons.
- Increased Wheel Lifespan: By reducing heat and providing lubrication, wet grinding minimizes the stress on the bond and the diamond particles. This leads to slower wear and tear, meaning your expensive diamond wheel lasts considerably longer, especially for resin and vitrified bonds.
- Potentially Improved Surface Finish: The coolant helps flush away grinding debris (swarf) from the cutting zone. This prevents loose particles from scratching the surface or clogging the wheel, often leading to a cleaner cut and a smoother finish.
- Example: High-precision grinding in manufacturing, such as shaping medical implants or sharpening industrial cutting tools, is almost always done wet to maintain strict tolerances and prevent thermal damage. Likewise, professional concrete polishing relies heavily on wet grinding for superior dust control and achieving high-gloss finishes.
When Dry Grinding is Appropriate or Necessary
Despite the benefits of wet grinding, there are situations where grinding dry is the chosen or only option:
- Machine Limitations: Many common handheld power tools, like standard angle grinders or bench grinders, are not designed for use with water. Introducing liquid could damage the motor, bearings, or electrical components. Always check your tool’s manual.
- Convenience and Setup: For quick, small jobs or work in areas where water access is difficult or messy cleanup is undesirable, dry grinding can be more convenient. It eliminates the need for water hoses, pumps, slurry collection, and disposal.
- Material Interaction (Less Common): In rare cases, a specific material might react poorly with water or coolant additives, although this is unusual for typical diamond grinding applications.
- Specific Wheel Design: Some wheels, particularly certain aggressive metal-bond segments for concrete removal, are engineered to withstand the heat of dry grinding, although their performance is often still enhanced by water.
- Critical Safety Note: If you must grind dry, effective dust control and personal protective equipment (PPE)8 are non-negotiable. This means using:
- A grinder equipped with a proper vacuum shroud connected to a dust extractor (HEPA filter recommended for silica).
- Appropriate respiratory protection (e.g., an N95 mask or a respirator rated for the specific dust hazard).
- Eye protection (safety glasses or face shield).
- Working in a well-ventilated area.
- Example: A contractor might quickly smooth a small, chipped concrete corner using an angle grinder dry for speed and convenience, but should absolutely use a vacuum shroud and wear a respirator and eye protection while doing so.
Choosing Wheels Designed for Wet vs. Dry Conditions
Critically, not all diamond wheels can handle both conditions. You need to use a wheel appropriate for your chosen method:
- Check Manufacturer Recommendations: This is the most important step. The wheel manufacturer will specify if a wheel is designed for wet use only, dry use only, or wet/dry use.
- Wet Use Only Wheels: Many wheels, especially those with certain resin or specialized vitrified bonds optimized for cooling, can be quickly damaged or destroyed by the excessive heat of dry grinding. Using them dry is unsafe and ineffective.
- Dry Use Wheels: Wheels specifically designed for dry grinding typically feature heat-resistant bonds and sometimes design elements like cooling holes or specially spaced segments to help manage heat.
- Wet/Dry Wheels: Many durable wheels (often metal bond for construction/stone) are designated for both. However, even with these, performance (cutting speed, finish) and especially lifespan will almost always be significantly better when used wet.
- Example: Attempting to dry polish a stone countertop with resin pads clearly marked “Wet Use Only” will likely result in smeared resin, glazed diamonds, and a ruined pad very quickly. Using a metal cup wheel marked “Wet/Dry” for concrete dry will work, but expect it to wear faster and potentially create more heat than if you used it with water.
Always match the wheel to the grinding condition recommended by the manufacturer to ensure safety, achieve good results, and maximize the life of your investment.
Conclusion
Choosing the right diamond grinding wheel isn’t about just one factor, but about understanding how material, bond, grit, concentration, shape, size, and grinding conditions all work together. By carefully considering each element discussed, you can select a wheel that performs efficiently, provides the desired finish, lasts longer, and ensures safe operation. Always refer to manufacturer specifications and recommendations when making your final selection to achieve the best results for your specific process.
- Tungsten Carbide1 – Wikipedia article explaining the properties and uses of Tungsten Carbide.
- Sintering2 – ScienceDirect topic page explaining the sintering process used in creating metal and vitrified bonds.
- Why Metal Bonds Are Chosen3 – ZYDiamondTools blog post discussing the reasons for selecting metal bond diamond/CBN grinding wheels.
- How to Dress Diamond Wheels4 – ZYDiamondTools guide on the process of dressing diamond grinding wheels.
- Surface Grinders5 – Wikipedia page defining and describing the surface grinding process and machinery.
- Angle Grinder6 – Wikipedia article explaining what an angle grinder is and its common uses.
- Silica Dust7 – OSHA page detailing the hazards associated with occupational exposure to respirable crystalline silica.
- Personal protective equipment (PPE)8 – OSHA resource page covering regulations and information regarding PPE in the workplace.
ZY Superhard Tools Co., Ltd.
Do you have any needs for PCD tools or diamond grinding wheels? We can customize products to meet your specific requirements. If you have any ideas or requests, feel free to reach out—we’ll respond within 24 hours!
Do you have any needs for PCD & CBN tools or diamond grinding wheels? We can customize products to meet your specific requirements. If you have any ideas or requests, feel free to reach out—we’ll respond within 24 hours!
Do you have any needs for PCD & CBN tools or diamond grinding wheels? We can customize products to meet your specific requirements. If you have any ideas or requests, feel free to reach out—we’ll respond within 24 hours!
Post Categories
Product Categories
About Company
Related Posts
What is a Wire Drawing Die and How Does it Actually Work?
Discover what a wire drawing die is and how it works. This guide covers die materials like PCD and carbide,
Why Is My Solid CBN Insert Chipping or Wearing Out Fast on Cast Iron Rolls?
Diagnose and fix the two main failures of solid CBN inserts: chipping and rapid wear. Learn why it happens on
How Do You Machine a Ball Screw for a Perfect Fit? A Step-by-Step Guide
Learn how to machine a ball screw with our step-by-step guide. Covers proper clamping, hard turning with CBN tools, and
Honing vs. Internal Grinding: Which Precision Finishing Process Is Right for Your Application?
Learn the key differences between honing and internal grinding. This guide covers mechanics, surface finish, and accuracy to help you
Subscribe
Simply enter your email below and click “Subscribe” to stay connected with everything new and exciting.