-
Whatsapp: +86 13526572721
-
Email: info@zydiamondtools.com
-
Address: AUX Industrial Park, Zhengzhou City, Henan Province, China
-
Whatsapp: +86 13526572721
-
Email: info@zydiamondtools.com
-
Address: AUX Industrial Park, Zhengzhou City, Henan Province, China
CBN Chipbreaker Inserts: How to Select and Apply Them for Optimal Hard Material Machining?
- Knowledge, PCD & CBN Tools Knowledge
- -2025-03-20
- - byKevin Ray
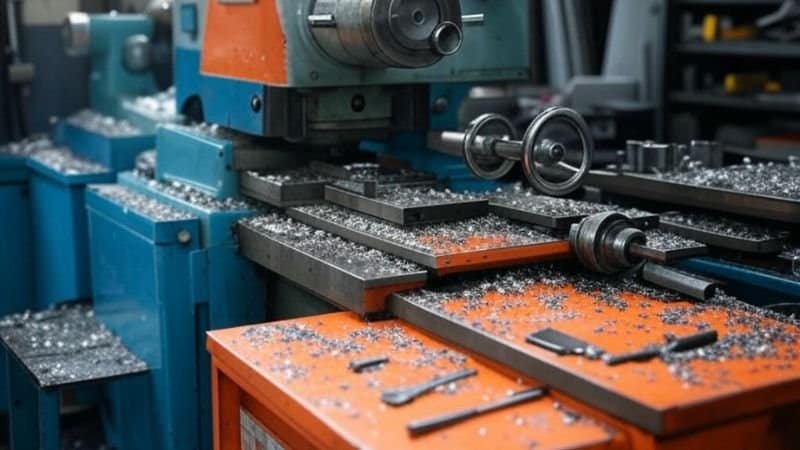
So, you need to machine hard materials efficiently – how do you actually choose the right CBN chipbreaker insert and use it correctly for the best results?
Selecting and effectively applying CBN chipbreaker inserts involves understanding the machining challenges they solve (like poor chip control and tool wear), how different designs and edge preparations impact performance, matching the correct CBN grade and chipbreaker to your material and cut type, and adhering to best practices for cutting parameters, setup rigidity, and troubleshooting.
Table of Contents
ToggleWhat Machining Challenges Do CBN Chipbreaker Inserts Address?
So, what specific problems in hard machining do these CBN chipbreaker inserts actually solve?
CBN chipbreaker inserts are specifically engineered cutting tools designed to tackle critical issues in machining hard materials (typically above HRC 45). Primarily, they provide effective chip control to prevent dangerous tangles, significantly extend tool life by resisting wear from abrasive materials, and ultimately improve the surface finish and dimensional accuracy of the final workpiece.
Let’s explore these key benefits in more detail.
Overcoming Poor Chip Control in Hard Turning and Boring
Machining very hard metals often creates long, stringy, and hot chips. If these chips aren’t managed properly, they can cause significant problems. Think about trying to untangle a fishing line that’s wrapped around everything – it’s messy and can cause damage!
Why Uncontrolled Chips Are Problematic
Uncontrolled chips present several major issues:
- Safety Hazards: Long, hot, sharp chips flying around or wrapping onto the tool or workpiece pose a serious risk to machine operators.
- Workpiece Damage: Chips can tangle around the workpiece, scratching or damaging the freshly machined surface. This is especially critical during finishing passes where surface quality is paramount. Imagine a stray piece of sandpaper scratching a newly polished table – the damage is often unacceptable.
- Tool Damage: Chips packing tightly around the cutting edge can lead to sudden tool breakage or chipping, stopping production unexpectedly.
- Machine Downtime: Operators frequently need to stop the machine to manually clear tangled chips, leading to significant losses in productivity. For instance, in automated production lines like those making automotive transmission gears, frequent manual intervention due to chip tangles can drastically reduce overall equipment effectiveness (OEE)1.
How Chipbreakers Provide a Solution
Chipbreaker inserts feature carefully designed grooves or obstacles molded or ground into the top surface of the insert, near the cutting edge. What do these features do?
- Forcing Chip Breakage: As the metal chip flows across the insert face, it hits the chipbreaker geometry. This forces the chip to curl more tightly upon itself until it becomes brittle and breaks into shorter, more manageable segments. It’s similar to how scoring glass with a cutter creates a weak point, making it easy to snap cleanly.
- Consistent Chip Evacuation: These smaller chip segments are much easier to flush away from the cutting zone by coolant or gravity. This prevents chip packing and tangling, especially in confined spaces like internal boring operations.
By effectively controlling and breaking chips, these inserts ensure smoother, safer, and more continuous machining operations, directly leading to increased productivity and reduced scrap rates.
Extending Tool Life When Machining Abrasive or High-Hardness Materials (HRC 45+)
Cutting hardened steel, tool steel, or abrasive cast irons is like trying to cut sandpaper with regular scissors – the scissors wear out incredibly fast. These materials fight back against the cutting tool.
The Challenge of Abrasive Wear
Materials harder than approximately 45 HRC contain very hard microscopic particles (like carbides in steel or abrasive inclusions in cast iron). During cutting, these particles act like tiny grinding stones, scraping away at the cutting edge and causing it to dull quickly. This is known as abrasive wear2. Furthermore, the high temperatures generated during hard machining can accelerate other wear mechanisms. Rapid tool wear means:
- Frequent tool changes, increasing downtime and cost.
- Inconsistent part quality as the tool dulls.
- Higher risk of sudden tool failure.
CBN Material and Chipbreaker Synergy for Longevity
Cubic Boron Nitride (CBN)3 itself is the second hardest material known, making it inherently resistant to abrasive wear. This is the primary reason it’s chosen for hard machining. However, chipbreakers add another layer of protection:
- Reduced Friction and Heat: Well-designed chipbreakers can influence how the chip flows across the insert face, potentially reducing the contact area and friction. Efficiently breaking and directing chips away also helps dissipate heat more effectively from the cutting edge, slowing down temperature-related wear.
- Preventing Catastrophic Failure: By preventing chips from packing around the edge, chipbreakers reduce the mechanical stress concentration that can lead to micro-chipping or complete edge fracture, especially under demanding conditions.
While the CBN material provides the base wear resistance, the chipbreaker optimizes the cutting process to protect the cutting edge. Real-world applications, such as turning hardened bearing races (e.g., AISI 52100 steel at 60 HRC), have shown that switching from a standard CBN insert to one with an optimized chipbreaker can sometimes increase the number of parts produced per cutting edge by 20-50% or more.
It’s important to remember that actual tool life gains are highly dependent on the specific material, machine conditions, chosen cutting parameters, and the exact CBN grade and chipbreaker geometry. Always consult supplier recommendations for your specific application.
Improving Surface Finish and Dimensional Accuracy on Difficult-to-Machine Parts
Achieving a mirror-like finish and holding tight tolerances (meaning the part dimensions are extremely precise) can be tough when machining hard materials. Several factors can work against you.
Sources of Surface Imperfections and Inaccuracy
Why is precision sometimes difficult in hard machining?
- Chip Interference: As mentioned, uncontrolled chips can scratch or mar the finished surface as they drag across it.
- Vibration: Hard materials often require higher cutting forces, which can induce vibration in the machine, toolholder, or workpiece. Vibration acts like a tiny hammer on the cutting edge, leaving chatter marks (a wavy pattern) on the surface and making it difficult to hold exact dimensions.
- Built-Up Edge (BUE): Although less common with CBN at high speeds, under certain conditions, tiny fragments of workpiece material can weld themselves to the cutting edge, then break off, taking part of the tool edge with them and leaving a rough surface.
- Tool Wear: As the tool wears, its precise geometry changes, leading to deviations in part size and a rougher finish.
How Chipbreakers Contribute to Precision
Proper chip control, facilitated by chipbreakers, directly contributes to better quality parts:
- Clear Cutting Zone: By breaking chips effectively and guiding them away, chipbreakers minimize the chance of chips interfering with the cutting zone or scratching the newly generated surface. This is crucial for achieving low surface roughness values (often measured as Ra). For example, manufacturers of hydraulic spools or fuel injector components often require Ra values below 0.4 µm, which is achievable with optimized CBN chipbreaker inserts.
- More Stable Cutting: Some chipbreaker designs can help stabilize the cutting process by promoting smoother chip flow or even slightly reducing cutting forces compared to flat-top inserts under certain conditions. Lower, more consistent forces mean less tendency for vibration, leading to better dimensional accuracy (e.g., holding tolerances within ±0.01 mm or tighter, corresponding to IT tolerance grades like IT6 or IT7).
- Consistent Performance: By helping to manage wear (as discussed previously), chipbreakers contribute to the tool maintaining its effective cutting geometry for longer, leading to more consistent part dimensions and surface finish over a batch of components.
In essence, the chip control provided isn’t just about safety and avoiding tangles; it’s a fundamental factor in enabling stable, predictable cutting, which is the key to achieving high precision and excellent surface quality in demanding hard machining applications.
How Do Different Chipbreaker Designs Impact Performance?
Okay, but how do the actual shapes and features of these chipbreakers change how the insert performs?
The specific geometry and manufacturing method of a CBN insert’s chipbreaker significantly influence its cutting performance. Different designs are optimized for various operations (like finishing or roughing) by altering chip curl, cutting forces, and edge strength, while edge preparation adds crucial reinforcement, and manufacturing techniques like laser etching allow for more complex, specialized geometries compared to traditional molding.
Let’s dive into how these design aspects make a real difference in your machining results.
Comparing Finishing, Medium, and Roughing Chipbreaker Geometries
Not all chipbreakers are created equal. Just like you use different tools for different jobs in a workshop, chipbreakers are designed for specific types of cuts. They generally fall into three main categories: Finishing (F), Medium (M), and Roughing (R).
Think of it like tire treads on a vehicle: smooth tires work best for high-speed racing on a smooth track (finishing), while deep, aggressive treads are needed for traction in rough off-road conditions (roughing). Medium treads offer a balance for everyday driving.
Chipbreakers for Finishing Touches (F-Geometry)
- Goal: To produce the best possible surface finish and tight dimensional accuracy.
- Application: Used for light depths of cut (DoC) and lower feed rates.
- Design: Typically features a wider, shallower groove or a more open geometry. This design gently encourages the thin chip produced during finishing to curl and break without applying excessive force that could mar the surface or induce vibration.
- Outcome: Aims for small, comma-shaped (“C” or “6” shaped) chips and minimizes cutting forces to ensure precision. Ideal for final passes on components like hydraulic valve spools or precision bearing seats.
Handling Heavy Cuts with Roughing Geometries (R-Geometry)
- Goal: To reliably break the thick, heavy chips generated during high material removal operations.
- Application: Used for large depths of cut and higher feed rates.
- Design: Often incorporates a narrower, deeper groove or a more pronounced obstruction placed closer to the cutting edge. This forces the thick chip to curl very tightly and break forcefully against the feature.
- Outcome: Manages thick, segmented chips effectively, preventing them from becoming long and hazardous ribbons. Cutting forces are generally higher, and the focus is on material removal rate and process security rather than ultimate surface finish. Used for initial passes to remove bulk material quickly.
The Versatile Medium Chipbreaker (M-Geometry)
- Goal: To provide a good balance of chip control across a wider range of cutting conditions.
- Application: Suitable for moderate depths of cut and feed rates, bridging the gap between finishing and roughing.
- Design: Features are intermediate between F and R types. Offers reliable chip breaking without being as aggressive as a rougher or as gentle as a finisher.
- Outcome: Provides acceptable chip control and surface finish for many general-purpose hard turning or semi-finishing operations. Often a good starting point if the application involves varying depths of cut.
Here’s a simplified comparison:
Chipbreaker Type | Typical Depth of Cut (DoC) | Typical Feed Rate | Primary Goal | Expected Chip Form |
---|---|---|---|---|
Finishing (F) | Light (e.g., < 0.5 mm) | Low (e.g., < 0.1 mm/rev) | Best Surface Finish | Small, C-shaped |
Medium (M) | Moderate (e.g., 0.5-1.5 mm) | Moderate | Versatility | Controlled Segments |
Roughing (R) | Heavy (e.g., > 1.5 mm) | High | Max Material Removal | Thick, Broken Segments |
(Note: These DoC and feed ranges are illustrative examples; always refer to manufacturer guidelines for specific insert capabilities.)
Understanding the Role of Edge Preparation (Honing/T-Land) with Chipbreakers
While the chipbreaker shapes the chip, the very edge of the insert needs special attention, especially with superhard CBN. This is where edge preparation4 comes in.
What is Edge Preparation (Hone and T-Land)?
Edge preparation refers to modifying the sharp cutting edge to increase its strength. The two common types are:
- Honing: Creating a very small radius along the cutting edge (imagine slightly rounding a knife edge).
- T-Land (Negative Land): Grinding a small, flat surface at a negative angle right behind the cutting edge (like adding a tiny bevel).
Why Edge Strength Matters for CBN Inserts
CBN is extremely hard, but it’s also more brittle than traditional carbide tools. This means it can chip or fracture more easily under stress. Factors that increase stress on the cutting edge include:
- Machining very hard materials.
- Interrupted cuts (where the tool repeatedly enters and exits the material, like turning a keyed shaft).
- The forces involved in curling and breaking chips against the chipbreaker geometry.
Edge preparation acts like reinforcement, making the edge less prone to chipping. Think of reinforcing the corner of a building structure to handle stress – the T-land provides similar support to the cutting edge.
Balancing Strength and Sharpness
There’s a trade-off:
- More Edge Prep (larger hone or T-land): Increases edge strength significantly, making the tool more reliable in tough conditions or interrupted cuts. However, it also makes the edge slightly less sharp, which can slightly increase cutting forces and generate more heat.
- Less Edge Prep: Maintains maximum sharpness for potentially lower cutting forces and the best possible surface finish in stable, continuous finishing cuts, but the edge is more vulnerable to chipping.
The amount and type of edge preparation (e.g., T-land width typically ranges from 0.05 mm to 0.2 mm, with angles from -15° to -30°) are critical design choices. The exact size and angle of the edge preparation significantly affect performance and reliability, and these specifications can vary widely between manufacturers and specific insert designations. Always verify these details with the supplier for your chosen insert to ensure it matches your application’s demands (e.g., continuous finishing vs. heavy interrupted roughing).
Assessing Laser-Etched vs. Molded Chipbreaker Technologies
How are these intricate chipbreaker shapes actually made on such a hard material? There are two primary manufacturing methods, and they impact the possible designs.
Molded Chipbreakers: The Standard Approach
- Process: The chipbreaker geometry is essentially pressed or molded into the CBN material before it undergoes the final high-pressure, high-temperature sintering process5 that makes it superhard.
- Characteristics: This method is well-established and cost-effective for producing common, relatively simple chipbreaker geometries (like basic grooves or bumps).
- Limitations: The molding process can limit the complexity, sharpness, and precision of the features that can be created.
Laser Technology: Enabling Advanced Geometries
- Process: After the CBN insert blank is fully sintered and hard, a high-precision laser is used to ablate or etch the chipbreaker geometry onto the insert’s surface.
- Characteristics: Lasers allow for the creation of much more complex, intricate, and precise 3D chipbreaker shapes. Features can be sharper, and designs can be tailored very specifically for certain applications or materials. Imagine the difference between a simple shape pressed into clay versus intricate patterns engraved with a fine tool.
- Benefits: Advanced laser-etched chipbreakers can offer superior chip control over a wider operating window, potentially lower cutting forces due to optimized flow paths, and enable solutions for very challenging applications (like finishing with very low feed rates or machining gummy materials) where molded geometries might struggle. Industry case studies have shown laser-designed chipbreakers providing consistent performance in small-diameter boring of hardened transmission components, where chip evacuation is extremely critical and space is limited.
While molded chipbreakers are effective for many standard applications, laser technology opens the door to higher performance and more specialized solutions through advanced geometric designs. The choice often depends on the specific performance requirements and the complexity of the machining task.
How Do You Choose the Right CBN Grade and Chipbreaker Combination?
With all these options, how do you actually pick the best mix of CBN material and chipbreaker for your specific job?
Choosing the optimal CBN grade and chipbreaker combination requires matching the insert’s properties to the specific demands of your application. Key factors include the workpiece material’s hardness and toughness (which dictates the required CBN content), the type of cut (continuous or interrupted, influencing chipbreaker and edge prep choice), and the unique characteristics of the material being machined (like cast iron versus superalloys).
Making the right choice is crucial for performance. Let’s break down these selection factors.
Matching CBN Content (Low vs. High) to Material Hardness and Toughness Requirements
CBN inserts aren’t made of 100% pure Cubic Boron Nitride. Instead, they contain tiny CBN crystals held together by a binder material, often a ceramic or metallic compound. The percentage of CBN content significantly affects how the insert behaves.
What ‘CBN Content’ Means
Think of it like making concrete: CBN crystals are like the hard gravel, and the binder is like the cement holding it together. Changing the amount of gravel affects the concrete’s properties.
- Low CBN Content (e.g., ~40-60% CBN): Less “gravel,” more binder. This results in an insert that is extremely hard and highly resistant to abrasive wear (like sandpaper rubbing against it). However, it’s generally more brittle, meaning it’s more susceptible to chipping or breaking under impact.
- High CBN Content (e.g., ~85-95% CBN): More “gravel,” less binder. This makes the insert tougher and more resistant to fracturing or chipping upon impact. However, it might be slightly less resistant to gradual abrasive wear compared to low-content grades.
Low CBN: Prioritizing Wear Resistance
When should you choose a low CBN content grade?
- Application: Primarily for continuous finishing cuts in very hard materials (typically > 55 HRC), such as hardened tool steels or bearing steels.
- Reasoning: In these situations, the main enemy is abrasive wear slowly dulling the edge. The extreme hardness of low CBN grades provides the best defense against this, leading to longer tool life and consistent surface finish.
High CBN: Prioritizing Toughness
When is a high CBN content grade the better option?
- Application: Generally preferred for machining cast irons, handling interrupted cuts, or machining materials where edge chipping (rather than slow wear) is the primary mode of tool failure.
- Reasoning: The increased toughness helps the cutting edge withstand the impacts and stresses encountered in interrupted cuts or when machining materials with hard inclusions or irregularities (like some cast irons).
It’s important to note that specific CBN percentages and the resulting balance between hardness and toughness vary across different manufacturers’ grade offerings. Always check the supplier’s technical data for the properties of the specific grade you are considering.
Selecting Chipbreakers for Continuous vs. Lightly Interrupted vs. Heavily Interrupted Cuts
The nature of the cut itself plays a huge role in choosing the right chipbreaker and the necessary edge preparation (discussed in the previous section).
Understanding Cut Types
- Continuous Cut: The cutting edge stays constantly engaged with the workpiece. Think of turning a smooth, solid shaft – no breaks in the cut.
- Interrupted Cut: The cutting edge repeatedly enters and exits the material during a single rotation or pass. Examples include:
- Turning a shaft with a keyway or spline.
- Facing a part with bolt holes.
- Machining cast parts with rough or uneven surfaces.
- Light Interruption: Small interruptions, relatively smooth entry/exit.
- Heavy Interruption: Large gaps, harsh impacts upon re-entry (e.g., facing across large holes).
Matching Chipbreakers to Continuous Cuts
- Conditions: Smooth engagement, lower mechanical shock. Emphasis is often on surface finish and precision.
- Typical Choice: Finishing (F) or sometimes Medium (M) chipbreakers are often suitable. Because the cut is stable, minimal edge preparation (light hone) might be sufficient to maximize sharpness and achieve the best possible finish.
Addressing Interrupted Cuts
- Conditions: High mechanical shock and stress concentration on the cutting edge each time it impacts the material. Edge chipping is a major risk. Robust chip control is needed to prevent chips from interfering during re-entry.
- Typical Choice:
- Light Interruption: May use F or M chipbreakers, BUT require a more significant edge preparation (like a T-land) to strengthen the edge against chipping. A higher toughness CBN grade (often higher content) might also be beneficial.
- Heavy Interruption: Typically demands M or Roughing (R) chipbreakers combined with the strongest available edge preparation (larger T-land) and often necessitates a high-toughness (high CBN content) grade to survive the repeated impacts. Process security becomes paramount.
For example, a common scenario in automotive manufacturing involves machining case-hardened gears with splines (an interrupted cut). While a standard finishing insert might work on a smooth shaft, it could easily chip on the gear. Successfully machining the gear often requires switching to an insert with a stronger T-land edge preparation, possibly a medium chipbreaker, and a tougher CBN grade.
Key Considerations for Specific Materials (Hardened Steels, Cast Irons, Superalloys, Sintered Metals)
Different materials behave differently during machining. Here are some general guidelines for common material groups:
Hardened Steels6 (> 45 HRC)
- Challenge: High hardness leads primarily to abrasive wear. Requires high cutting temperatures.
- Typical Approach: Low CBN content grades are often preferred for their superior wear resistance, especially in finishing. Chip control is critical; F or M chipbreakers are common. Edge preparation choice depends heavily on whether the cut is continuous or interrupted. Coated CBN grades can further enhance performance.
Cast Irons (Gray, Nodular, Chilled)
- Challenge: Can be abrasive due to graphite, silicon carbide, or sand inclusions. Chilled iron has a very hard surface layer. Can often be machined at high speeds.
- Typical Approach: High CBN content grades are frequently used due to their toughness, which helps resist abrasion from inclusions and handles potential interruptions or surface irregularities. M or R chipbreakers are often used for roughing. Edge preparation is important for durability.
Superalloys (e.g., Inconel…)
- Challenge: Maintain high strength at high temperatures, tend to work-harden rapidly, chemically reactive with tool materials (causing crater wear). Very demanding to machine.
- Typical Approach: Requires specialized CBN grades, often with specific coatings (like TiAlN or others) designed to resist high temperatures and chemical wear. Both low or medium CBN content grades might be used depending on the specific alloy and operation. Chip control and effective heat management (coolant application) are absolutely critical. Chipbreaker selection needs careful consideration based on the specific cut.
Sintered Metals (Powder Metallurgy – PM)
- Challenge: Properties vary widely based on composition and density. Can be highly abrasive. Porosity can act like micro-interruptions during cutting.
- Typical Approach: Often requires high CBN content grades for toughness to handle the abrasive nature and potential micro-interruptions caused by porosity. Chipbreaker selection (F, M, or R) depends heavily on the material’s density, the required surface finish, and the depth of cut.
Here’s a potential starting point guide (always verify with specific application details):
Material Group | Typical CBN Choice | Common Chipbreaker Type(s) | Key Considerations |
---|---|---|---|
Hardened Steel | Low Content | F, M | Wear resistance, cut continuity |
Cast Iron | High Content | M, R | Toughness, abrasion resistance |
Superalloys | Specialized/Coated | Application-Specific | Heat resistance, chemical stability, chip control |
Sintered Metals | High Content | Application-Specific | Toughness, abrasion, porosity |
Disclaimer: These are general recommendations. The optimal grade and chipbreaker combination for a specific alloy (e.g., Inconel 718 vs. Waspaloy) or a particular cast iron specification can differ significantly. Always consult cutting tool manufacturer’s detailed recommendations and grade charts for your exact workpiece material and application.
What Are Best Practices for Applying CBN Chipbreaker Inserts Effectively?
Now that you’ve chosen the right insert, how do you actually use it effectively to get the best results?
Applying CBN chipbreaker inserts effectively involves using appropriate cutting parameters (speed, feed, depth of cut) tailored to the material and grade, ensuring a rigid and stable machining setup including proper toolholding, and knowing how to troubleshoot common issues like premature wear or vibration to optimize performance.
Getting these application details right is key to unlocking the full potential of your CBN tooling. Let’s explore these best practices.
Recommended Cutting Parameters (Speed, Feed, Depth of Cut)
Using the right cutting speed, feed rate, and depth of cut is fundamental for success with any cutting tool, but especially important for CBN due to its unique properties.
The Importance of Cutting Speed with CBN
CBN tools generally perform best at relatively high cutting speeds, particularly when machining hardened steels. Why? The high speed generates localized heat right at the cutting zone. This intense heat actually helps to slightly soften the microscopic layer of the hard workpiece material just ahead of the cutting edge, making it easier to shear. Think of it like heating glass slightly before trying to cut it – it makes the process smoother. However, too much speed can lead to excessive heat and rapid tool wear.
Balancing Feed Rate and Depth of Cut
- Feed Rate (mm/rev or inch/rev): This affects chip thickness, surface finish, and tool life. Higher feeds generally increase productivity but can put more stress on the cutting edge and may result in a rougher finish. Lower feeds improve finish but reduce material removal rate.
- Depth of Cut (DoC – mm or inch): This is the amount of material removed in one pass. It should align with the capability of the selected chipbreaker (Finishing, Medium, Roughing, as discussed earlier) and the strength of the cutting edge preparation. Trying to take too large a DoC with a finishing insert, for example, will likely lead to tool failure.
Critical Note: Starting Points vs. Optimization
Tool manufacturers provide recommended starting parameters for their inserts based on the workpiece material and type of operation. Typical starting ranges might look something like this (these are highly generalized examples):
- Hardened Steel (55-62 HRC), Continuous Turning:
- Speed (Vc): 120 – 180 m/min (approx. 400 – 600 sfm)
- Feed (f): 0.05 – 0.15 mm/rev (approx. 0.002 – 0.006 ipr)
- Depth of Cut (ap): 0.1 – 0.5 mm (approx. 0.004 – 0.020 inch) – Use lower end for Finishing (F) chipbreakers.
- Cast Iron (Gray/Nodular), Roughing:
- Speed (Vc): Can be much higher, sometimes 300 m/min+ (approx. 1000 sfm+)
- Feed (f): 0.15 – 0.30 mm/rev (approx. 0.006 – 0.012 ipr)
- Depth of Cut (ap): 1.0 – 3.0 mm+ (approx. 0.040 – 0.120 inch+) – Use appropriate Roughing (R) or Medium (M) chipbreakers.
Crucially, these parameters are highly dependent on the specific CBN grade, workpiece material composition and hardness, chipbreaker geometry, edge preparation, machine capability, coolant application, and overall setup rigidity. The values provided by manufacturers are only starting points.
Think of it like tuning a performance car: the factory provides base settings, but achieving peak performance requires careful adjustment based on track conditions and driver feedback. Similarly, you must always consult the cutting tool manufacturer’s specific recommendations for the exact insert you are using, and be prepared to optimize speeds, feeds, and depth of cut based on observing the actual cutting performance, chip formation, surface finish, and tool wear patterns.
Toolholding and Machine Stability Requirements
Even the best CBN insert will perform poorly or fail quickly if the machining setup isn’t rigid and stable. CBN’s hardness also means it’s more brittle than carbide, making it less forgiving of vibration.
Why Rigidity is Non-Negotiable
Imagine trying to write intricate details with a pencil lead held in a flimsy, wobbly holder – the results would be terrible. It’s the same in machining:
- Vibration: Any looseness or flex in the system (machine, toolholder, workpiece) can lead to vibration (chatter) during cutting. Vibration hammers the delicate cutting edge, causing it to chip prematurely, produces poor surface finish, and can even damage machine components like spindle bearings.
- Deflection: Lack of stiffness can cause the tool or workpiece to push away slightly under cutting forces, leading to dimensional inaccuracies.
Choosing the Right Toolholder
The toolholder is the critical link between the machine spindle and the cutting insert. For demanding CBN applications:
- Use High-Quality, High-Rigidity Holders: Options like hydraulic expansion chucks, shrink-fit holders, or robust power-milling chucks provide superior clamping force and concentricity compared to standard collet chucks or side-lock holders, minimizing vibration.
- Minimize Overhang: The distance the tool sticks out from the holder (overhang) acts like a lever, amplifying any tendency to vibrate. Keep overhang as short as absolutely possible for the operation. For boring operations, use solid carbide or heavy metal damped boring bars for deep holes to maximize stiffness.
Machine Tool and Workpiece Clamping Considerations
- Machine Condition: The machine tool itself must be rigid and well-maintained. Worn spindle bearings or loose guideways will undermine any effort to achieve stable cutting. Hard machining generally requires robust, heavy-duty machines.
- Workpiece Clamping: The part being machined must be held securely without any possibility of movement or vibration. Use appropriate chucks, fixtures, or vises, ensuring adequate clamping force and support.
Investing in a rigid setup is essential for protecting your CBN inserts, achieving desired part quality, and ensuring process reliability.
Troubleshooting Common Issues (e.g., Premature Wear, Vibration, Poor Chip Breaking)
Even with careful selection and setup, you might encounter issues. Here’s a basic guide to troubleshooting common problems:
Problem | Potential Causes | Possible Solutions |
---|---|---|
Premature Flank/Crater Wear | – Cutting speed too high or too low. – Wrong CBN grade (insufficient wear resistance). – Ineffective coolant. – Setup instability. | – Adjust speed (consult wear guides/supplier). – Verify correct grade for material. – Improve coolant flow/pressure/direction. – Check/improve setup rigidity. |
Edge Chipping / Fracture | – Feed rate or Depth of Cut too high. – Wrong CBN grade (insufficient toughness). – Edge prep too sharp (insufficient T-land/hone). – Heavy interruptions. – Instability/vibration. | – Reduce feed/DoC. – Select tougher grade (higher CBN%). – Select insert with stronger edge prep. – Ensure correct grade/prep for interrupted cuts. – Improve rigidity. |
Vibration / Chatter | – Setup not rigid (toolholder, workpiece, machine). – Tool overhang too long. – Incorrect cutting parameters (speed/feed). – Dull/worn tool edge. | – Improve rigidity (holder, clamping, shorter overhang). – Adjust speed or feed (often +/- 10-20% can help). – Check tool for wear/damage; replace if needed. |
Poor Chip Breaking | – Feed rate or Depth of Cut too low for the chipbreaker. – Wrong chipbreaker selected (e.g., F for roughing). – Incorrect coolant application (not breaking/flushing chips). | – Increase feed/DoC (within limits). – Verify correct chipbreaker (F/M/R) for the operation. – Optimize coolant pressure/nozzle position to target chip/edge interface. |
Troubleshooting Approach: When facing an issue, try to diagnose the likely cause based on observations (wear type, chip form, sound). Change only one variable at a time (e.g., adjust only speed, then evaluate) to understand its effect. Systematically working through potential causes is the most effective way to optimize the process.
Conclusion
Successfully leveraging CBN chipbreaker inserts goes beyond simply choosing a tool; it requires a holistic approach. By understanding the specific machining challenges they address, appreciating how different designs and edge preparations influence cutting action, carefully selecting the right grade and geometry combination for your material and cut type, and diligently applying best practices regarding parameters and setup rigidity, you can significantly enhance your hard machining operations. Paying attention to these details is key to achieving optimal tool life, superior part quality, and efficient, reliable production.
Ready to find the specific PCBN insert solution for your hard machining needs? Download our PCBN Insert Product Catalog PDF to explore detailed specifications, available grades, and chipbreaker geometries designed for optimal performance.
References
- overall equipment effectiveness (OEE)1 – OEE.com homepage, a resource dedicated to understanding and implementing OEE.
- abrasive wear2 – ScienceDirect topic page defining and discussing abrasive wear in engineering contexts.
- Cubic Boron Nitride (CBN)3 – ZYDiamondTools comprehensive guide to CBN cutting tools.
- edge preparation4 – ZYDiamondTools blog post explaining edge radiusing (a form of edge preparation) for PCBN inserts.
- sintering process5 – Encyclopedia Britannica article defining the sintering process in technology.
- Hardened Steels6 – ZYDiamondTools blog post explaining hard turning, often applied to hardened steels.
ZY Superhard Tools Co., Ltd.
Do you have any needs for PCD tools or diamond grinding wheels? We can customize products to meet your specific requirements. If you have any ideas or requests, feel free to reach out—we’ll respond within 24 hours!
Do you have any needs for PCD & CBN tools or diamond grinding wheels? We can customize products to meet your specific requirements. If you have any ideas or requests, feel free to reach out—we’ll respond within 24 hours!
Do you have any needs for PCD & CBN tools or diamond grinding wheels? We can customize products to meet your specific requirements. If you have any ideas or requests, feel free to reach out—we’ll respond within 24 hours!
Post Categories
Product Categories
About Company
Related Posts
Which Turning Insert Shape Should You Choose?
Master turning insert selection. Our guide covers choosing the right shape for your job, decoding ISO codes, and selecting the
How Do You Solve Vibration, Chip Control, and Surface Finish Issues in PCD Grooving?
Solve common PCD grooving problems. This guide details how to fix vibration, improve chip evacuation, and achieve a flawless sidewall
Why Is Your Tooling Wearing Out Prematurely? A Machinist’s Guide to Key Causes & Proven Solutions
Facing premature tool wear? Learn the key causes like heat, vibration, & wrong parameters. Discover proven solutions from setup to
How Do You Select the Optimal PCD Tools for Scroll Compressor Machining?
Learn how to select the right PCD tools for scroll compressor machining. This guide covers the benefits over carbide, key
Subscribe
Simply enter your email below and click “Subscribe” to stay connected with everything new and exciting.