-
Whatsapp: +86 13526572721
-
Email: info@zydiamondtools.com
-
Address: AUX Industrial Park, Zhengzhou City, Henan Province, China
-
Whatsapp: +86 13526572721
-
Email: info@zydiamondtools.com
-
Address: AUX Industrial Park, Zhengzhou City, Henan Province, China
Hard Turning Explained: What Is It and How Does It Compare to Grinding?
- Grinding Wheels Knowledge, Industry Knowledge, PCD & CBN Tools Knowledge
- -2022-12-27
- - byKevin Ray
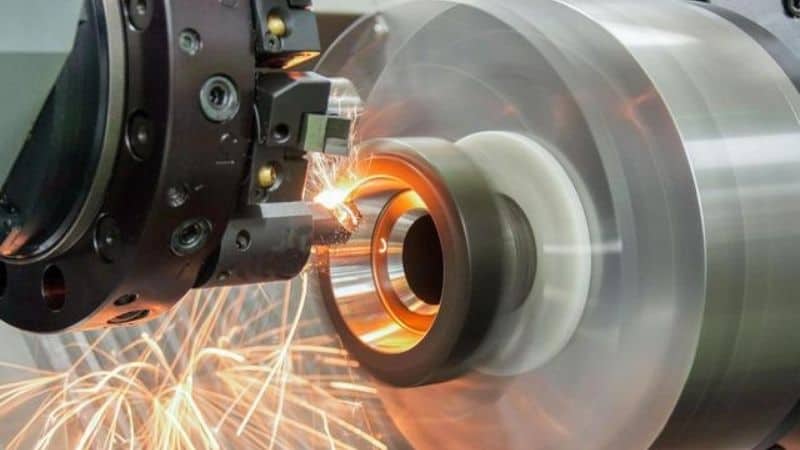
Thinking about finishing hardened parts, what exactly is hard turning, and how does it really stack up against traditional grinding?
Hard turning is a specialized machining process used to cut already hardened materials (typically 45-68 HRC) on a lathe, employing superhard cutting tools like CBN or ceramics. It aims to achieve final dimensions and surface finishes after heat treatment, often serving as a direct alternative to grinding operations.
Compared to grinding, hard turning often offers significant advantages in speed, flexibility for complex shapes, and cost-effectiveness by potentially reducing process steps and eliminating coolant. However, it requires highly rigid machines, careful process control to manage tool wear and surface integrity, and may not achieve the absolute finest finishes possible with precision grinding. The best choice depends heavily on specific application requirements.
Table of Contents
ToggleHow Does the Hard Turning Process Actually Work?
So, how exactly does hard turning manage to cut materials that are already incredibly hard?
Hard turning is a precision machining process that uses specialized cutting tools, typically made from Cubic Boron Nitride (CBN) or ceramics, to cut materials with high hardness levels (usually above 45 HRC) on a lathe or turning center. Unlike traditional turning performed before heat treatment, hard turning machines the part after it has been hardened.
This process relies heavily on extremely rigid and precise machine tools capable of handling the high forces involved and maintaining tight tolerances. It works by shearing off small amounts of the hardened material with the superhard cutting edge, often generating fine, brittle chips instead of the continuous ribbons seen in softer material turning.
The Basic Machining Principle vs. Traditional Turning
Think about shaping wood. Traditional turning is like carving relatively soft pine before you treat it. You can use standard steel tools, and the wood cuts easily. Now, imagine that wood has been petrified, becoming rock-hard. That’s similar to the materials used in hard turning.
Hard turning tackles materials after they’ve undergone heat treatment processes like hardening or case hardening, making them very strong and wear-resistant. The fundamental principle is still removing material using a cutting tool on a rotating workpiece (a lathe operation). However, because the material is already hard (often 45 to 70 Rockwell C (HRC), sometimes even higher), the approach must change significantly:
- Cutting Action: Instead of peeling off long, flowing chips like in soft turning, hard turning often involves shearing or fracturing tiny segments of the material due to its brittleness and hardness. This demands very different tool geometry and process parameters.
- Force & Heat: Cutting hardened steel generates considerably higher cutting forces and much more heat concentrated at the tool tip compared to turning softer metals.
- Goal: Often, hard turning aims to replace slower grinding operations, achieving similar precision and surface finish directly on a lathe, potentially in a single setup if soft turning was also done on the same machine.
Critical Role of Superhard Cutting Tools (CBN & Ceramics)
You can’t cut hardened steel effectively with the same tools you’d use for mild steel or aluminum. It would be like trying to cut granite with a butter knife – the tool would dull or break almost instantly. This is where superhard cutting tools become essential, with Cubic Boron Nitride (CBN) being a primary choice.
The main materials used are:
- Cubic Boron Nitride (CBN): This is the second hardest known material after diamond, possessing unique material properties1. CBN excels because it maintains its hardness even at the very high temperatures generated during hard turning. It’s particularly effective on hardened ferrous (iron-based) materials like steel alloys. Different CBN grades exist, often with varying CBN content and binder materials (like ceramic or metal), tailored for specific hardness ranges or whether continuous or interrupted cuts are needed.
- Ceramics: Certain advanced ceramics (like Silicon Nitride or whisker-reinforced ceramics) are also used, especially for specific applications like machining cast irons or in certain high-speed scenarios. They offer excellent wear resistance and high-temperature stability but can sometimes be more brittle than CBN.
Why are they critical?
- Hardness: They are significantly harder than the hardened workpiece material, allowing them to penetrate and cut effectively.
- Thermal Stability: They resist softening and degradation at extreme cutting temperatures, maintaining a sharp cutting edge for longer.
- Wear Resistance: They withstand the abrasive nature of hardened materials, leading to acceptable tool life.
It’s important to note that the optimal grade, coating, and geometry (shape) of a CBN or ceramic insert depend heavily on the specific workpiece material, its hardness, the type of cut (continuous vs. interrupted), and the desired surface finish. Always consult tool supplier recommendations for your specific application, as these details can vary significantly.
Machine Tool Requirements: Rigidity and Precision
Imagine trying to draw a perfectly straight line while standing on a trampoline. Any small bounce will ruin the line’s accuracy. Hard turning presents a similar challenge – the high forces involved demand an extremely stable platform.
Success in hard turning heavily depends on the machine tool itself. Key requirements include:
- High Static and Dynamic Rigidity: The entire machine structure – bed, slides, turret, spindle, tailstock – must be incredibly stiff, a concept detailed under general machine tool requirements. This prevents vibrations and deflections under the high cutting forces. Even tiny vibrations can lead to poor surface finish, inaccurate dimensions, and rapid tool wear or even tool breakage. Think of machine tool builders designing specific “hard turning” lathes with enhanced damping and stiffness features.
- Spindle Accuracy and Power: The spindle must run true (minimal runout) and provide sufficient power and torque, especially at the specific speeds required for hard turning, which might differ from conventional turning. Precise speed control is crucial.
- Axis Drive Precision: High-resolution encoders and precise, backlash-free axis drives are needed to accurately control the tool’s path and maintain tight dimensional tolerances, often in the micron range (μm).
- Thermal Stability: Machines designed for hard turning often incorporate cooling systems and design features to manage heat generated by the spindle and drives, preventing thermal expansion that could affect accuracy over long production runs.
Without this foundation of rigidity and precision, achieving the tolerances and surface finishes possible with hard turning (often comparable to grinding) becomes impossible, regardless of how good the cutting tool is. It’s a system where the machine, tool, and process parameters must all work together perfectly.
What Are the Key Advantages of Choosing Hard Turning?
Given how demanding hard turning is, why would manufacturers choose it over traditional methods like grinding?
The primary advantages of hard turning often center on increased efficiency and reduced manufacturing costs. By machining parts after they are hardened, hard turning can eliminate entire process steps, drastically cut down cycle times, and potentially combine roughing, finishing, and hard machining in a single machine setup.
Furthermore, this process offers significant flexibility for complex part geometries compared to conventional grinding. It can achieve high levels of accuracy and surface finish suitable for many demanding applications, often with lower initial investment in machinery and the environmental benefit of eliminating coolant.
Potential for Reduced Cycle Times and Operations
One of the most compelling reasons manufacturers adopt hard turning is its potential to dramatically speed up production. How does it achieve this?
- Eliminating Process Steps: Traditionally, making a precise hardened part might involve: soft turning -> heat treatment -> grinding. Hard turning can often consolidate this to: soft turning -> heat treatment -> hard turning. Removing the separate grinding operation saves time, handling, and potential delays.
- Single Setup Machining: Modern CNC turning centers capable of hard turning can often perform both soft turning (before heat treat) and hard turning (after heat treat) on the same machine. This “done-in-one” approach minimizes setup time, reduces work-in-progress (WIP) inventory, and simplifies logistics. Imagine finishing a complex automotive transmission shaft completely on one machine versus moving it between a lathe and a grinder.
- Higher Material Removal Rates (Compared to Grinding): While not always the case, in certain applications, especially rough hard turning, the material removal rates can be higher than grinding, further shortening cycle times.
Industry case studies often report significant time savings. For instance, in the production of certain automotive components like gear wheels or shafts, manufacturers have documented cycle time reductions ranging from 30% to over 70% by replacing grinding processes with hard turning, leading to substantial productivity gains.
Achieving High Accuracy and Surface Finish
Can hard turning really match the precision of grinding? For many applications, the answer is a resounding yes.
While grinding might still hold the edge for the absolute finest surface finishes (sub-micron Ra values), hard turning routinely achieves excellent results suitable for a vast range of components:
- Dimensional Tolerances: With the rigid machines and precise controls discussed earlier, hard turning can hold dimensional tolerances well within the IT6 or IT5 range2 (International Tolerance grades), which is sufficient for many bearing seats, gear journals, and hydraulic components.
- Surface Finish: Surface finishes typically ranging from Ra 0.8 down to 0.2 µm (micrometers) are achievable, depending on the material, tooling, and cutting conditions. This often meets or exceeds the requirements for parts previously finished by grinding.
- Consistency: Once the process is optimized, hard turning offers highly repeatable accuracy from part to part.
This capability allows manufacturers to achieve final part specifications directly on the lathe, contributing significantly to the reduction in process steps and lead times mentioned above.
Flexibility in Handling Complex Geometries
Turning processes, by their nature, offer great flexibility in creating various shapes. Hard turning retains this advantage when working with hardened materials.
- Profiling and Contouring: Unlike grinding, where complex wheel shapes might need frequent dressing (reshaping), a single-point hard turning tool can easily follow complex contours, create radii, chamfers, grooves, and tapers on hardened surfaces. Think about machining the intricate curved raceways on a large bearing ring – this is often more straightforward with hard turning than form grinding.
- Internal and External Features: Hard turning can be applied to both outer diameters (OD) and inner diameters (ID), allowing for the finishing of bores and external profiles on the same machine, often in the same setup.
- Non-Circular Turning: Advanced turning centers can even perform non-circular hard turning for components like cams or specific shaft profiles, offering design possibilities that might be difficult or impossible with conventional grinding methods.
This geometric flexibility simplifies the production of complex hardened parts and can even enable new design approaches previously limited by manufacturing constraints.
Cost-Effectiveness and Environmental Considerations (Dry Machining)
Beyond cycle time, hard turning offers compelling economic and environmental benefits:
- Lower Machine Investment (Potentially): While high-precision lathes capable of hard turning are significant investments, they are often less expensive than dedicated, high-precision grinding machines. Furthermore, a single turning center might replace both a standard lathe and a grinder, reducing the total capital equipment cost.
- Reduced Tooling Inventory: Consolidating operations can sometimes lead to a simpler overall tooling inventory compared to managing separate tools for soft turning and grinding.
- Dry Machining Capability: This is a major advantage. Hard turning often works best without coolant. The intense heat generated is mostly carried away in the chips.
- Environmental: Eliminates the purchase, maintenance, filtering, and disposal costs associated with cutting fluids. This also avoids potential health hazards from coolant mist and creates a cleaner working environment. Disposal of used coolant is subject to increasingly strict environmental regulations, making its elimination a significant plus.
- Cost Savings: Coolant management can represent a surprisingly large portion (some estimates suggest 10-15% or more) of total machining costs. Eliminating it directly impacts the bottom line.
- Clean Chips: Dry chips are easier to handle, store, and recycle, often fetching higher scrap value compared to coolant-contaminated swarf.
Therefore, when evaluating the total cost of ownership and environmental impact, hard turning frequently presents a very attractive alternative to traditional grinding processes. Think of it like avoiding the mess and cost of oil-based paints by using high-quality water-based alternatives.
Are There Significant Drawbacks or Limitations to Consider?
It sounds promising, but surely hard turning isn’t perfect – what are the potential challenges or downsides?
Yes, despite its advantages, hard turning presents distinct challenges. Key limitations include managing the less predictable wear of expensive superhard cutting tools and the critical need to control surface integrity, avoiding potential issues like detrimental white layers or unfavorable residual stresses.
Furthermore, while hard turning achieves excellent precision for many applications, it generally cannot match the absolute finest surface finishes or the tightest form tolerances attainable through specialized precision grinding processes. Careful evaluation is needed to ensure it meets the specific requirements of the component.
Tool Wear Predictability and Management
While CBN and ceramic tools are incredibly hard, they operate under extreme stress when cutting hardened materials. This leads to challenges in managing tool wear:
- Less Predictable Wear: Unlike turning softer materials where tool wear is often gradual and predictable, wear in hard turning can sometimes be more erratic. Sudden micro-chipping or fracture of the cutting edge can occur, especially if encountering material inconsistencies or vibrations. Think of it like driving a high-performance race car tire – it performs amazingly but wears out much faster and less predictably than a standard road tire.
- Higher Tool Cost: CBN and ceramic inserts are significantly more expensive than conventional carbide tools. Unpredictable or premature tool failure, therefore, carries a higher cost penalty, impacting the overall process economics.
- Sensitivity to Conditions: Tool life is extremely sensitive to cutting parameters (speed, feed, depth of cut), tool geometry, edge preparation (honing or chamfering), material hardness variations, and machine stability. Finding the optimal balance for reliable tool life requires careful process development and control.
- Need for Monitoring: Due to the higher cost and potential for sudden failure, effective tool wear monitoring systems or carefully planned, often conservative, tool change intervals are crucial for maintaining consistent part quality and avoiding catastrophic tool failure that could damage the workpiece.
Managing tool life effectively is perhaps one of the most critical aspects of implementing a successful and economical hard turning operation.
Surface Integrity Considerations
What happens to the surface of the material during hard turning is critically important for the final part’s performance, especially its fatigue life and wear resistance. Understanding surface integrity3 is key. While hard turning can produce excellent surfaces, potential issues need careful management:
- Understanding Surface Integrity: This refers not just to the roughness but also the metallurgical condition of the surface and immediate subsurface – its microstructure, hardness, and residual stresses.
- Potential for White Layers: Under certain conditions, the intense heat and pressure at the cutting edge can create a very thin, extremely hard, and often brittle layer known as a “white layer” (named for its appearance after etching). While sometimes harmless or even beneficial, undesirable white layers can act as initiation points for cracks, potentially reducing the fatigue life of components subjected to high cyclical loads, such as bearings or gears.
- Residual Stresses: Hard turning typically imparts compressive residual stresses into the workpiece surface. This is often highly beneficial, as compressive stress helps to resist crack initiation and propagation, thereby improving fatigue life compared to the potentially tensile stresses sometimes induced by grinding. However, the magnitude and depth of this compressive stress must be controlled. The challenge lies in ensuring the stress state is consistently favorable and doesn’t involve unwanted tensile components or excessive stress gradients.
- Microstructural Alterations: The heat involved can cause other subtle changes in the material’s microstructure near the surface, which may need evaluation depending on the application’s criticality.
Achieving desirable surface integrity consistently relies heavily on optimizing the cutting parameters, using the correct tool edge preparation (e.g., honed or chamfered edges are often preferred over sharp edges), and ensuring machine stability. Careful analysis and testing are often required, especially for fatigue-critical components. Think of it like cooking with high heat – done correctly, it sears perfectly; done wrong, it burns the outside while leaving the inside raw, creating undesirable layers.
Limitations Compared to Precision Grinding Finishes
While hard turning offers impressive accuracy and finish capabilities, as discussed in the advantages, it’s important to recognize its limits compared to grinding, particularly specialized grinding processes:
- Ultimate Surface Finish: For applications demanding the absolute lowest possible surface roughness (e.g., Ra values significantly below 0.1 µm), precision grinding, lapping, or honing processes still generally hold the advantage. Hard turning can get close, but grinding excels at achieving ultra-smooth, often mirror-like finishes.
- Form Accuracy (Roundness, Cylindricity): Similarly, for components requiring the utmost perfection in form – extremely precise roundness on a shaft or flatness on a face – specialized grinding techniques often provide tighter control than hard turning.
- Specific Surface Textures: Grinding can create specific surface patterns or textures (e.g., cross-hatching in cylinder bores for oil retention) that might be difficult or impossible to replicate precisely with single-point hard turning.
Therefore, the choice isn’t always about completely replacing grinding. Hard turning is an excellent, efficient alternative for a vast range of applications, but for those requiring the absolute pinnacle of surface finish or form accuracy, precision grinding remains the benchmark process.
When Does Hard Turning Make More Sense Than Grinding?
With both pros and cons, how do you actually decide whether hard turning or grinding is the better choice for a specific job?
The decision hinges on a careful analysis of the part’s specific requirements versus the capabilities and costs of each process. Hard turning often becomes the preferred method when the required tolerances and surface finish are within its achievable range (even if not the absolute finest possible), when the part geometry benefits from turning’s flexibility, and when significant reductions in cycle time and overall production cost can be realized by eliminating separate grinding operations.
Conversely, grinding typically remains necessary when the component demands ultra-high precision in terms of surface finish (sub-Ra 0.1 µm) or form accuracy that exceeds hard turning’s capabilities, or when dealing with very simple geometries where grinding setups are highly efficient. Evaluating the trade-offs between speed, flexibility, cost, and ultimate precision is key.
Analyzing Required Tolerances and Surface Finish Needs
The first critical checkpoint is the engineering drawing. What level of precision does the final part actually require?
- Is “Good Enough” Truly Good Enough? As we’ve seen, hard turning can produce excellent results (tolerances in IT6/IT7 range, finishes down to Ra 0.2 µm or sometimes better). If the part specification falls comfortably within this range, hard turning is a strong contender. Why use a potentially slower, more expensive process (grinding) if hard turning meets the functional requirements?
- Identifying the Non-Negotiables: However, if the drawing specifies extremely tight tolerances (e.g., IT4/IT5), requires a near-mirror surface finish (Ra < 0.1 µm), or demands exceptional roundness or cylindricity for ultra-precision applications (like high-end bearing races or metrology components), then precision grinding is likely unavoidable. Hard turning, while capable, typically has limitations at these extreme levels discussed previously.
- Surface Integrity Requirements: Beyond just roughness, consider the surface integrity needs. Does the application benefit significantly from the compressive residual stresses typically induced by well-controlled hard turning? Or does it have extreme sensitivity to potential white layers, perhaps favoring the often lower-impact material removal of fine grinding?
Think of it this way: If you need a reliable family car that performs well (meets standard tolerances/finish), hard turning is often the efficient choice. If you need a Formula 1 race car built to the absolute limits of performance (ultra-high precision), you might need the specialized approach of grinding.
Evaluating Part Complexity and Material Type
Next, consider the shape of the part and the material it’s made from.
- Geometric Complexity: Does the hardened part feature complex profiles, contours, grooves, undercuts, or tapers? Hard turning’s single-point tool offers significant flexibility here, often machining these features more easily and quickly than shaping or dressing a grinding wheel. For simpler shapes like plain cylinders or flat surfaces, grinding can be very efficient. However, as complexity increases, the setup and processing advantages often shift towards hard turning.
- Material Suitability: Is the workpiece made from a material well-suited for hard turning? This typically includes hardened steels (through-hardened, case-hardened, induction-hardened), tool steels, bearing steels, and some hard cast irons, usually within a hardness range of approximately 45 to 68 HRC. While grinding works on these too, hard turning often excels in this range. Remember to check tool supplier recommendations, as specific CBN/ceramic grades are optimized for different hardness levels and material compositions. Think of the ideal materials like very hard wood or ceramic tiles – too soft, and conventional turning is better; significantly harder or more abrasive, and other processes might be needed.
- “Difficult-to-Grind” Materials: Some materials might be prone to grinding issues like thermal damage (grinding burn) or surface cracking. In certain cases, hard turning might offer a more controllable process, provided suitable tooling exists.
If the part has intricate features or is made of a standard hardenable steel alloy, hard turning’s flexibility often makes it a more sensible choice than trying to form-grind complex shapes.
Comparing Process Efficiency and Overall Costs
Finally, it comes down to the numbers and the overall manufacturing strategy. Which process delivers the required quality at the lowest total cost and highest efficiency? Understanding the difference between cutting and grinding4 fundamentally helps here.
- Cycle Time Impact: As highlighted before, hard turning’s ability to potentially eliminate grinding steps and allow single-setup machining can lead to major cycle time reductions. How valuable is this speed increase for your production volumes and lead time requirements? Calculate the time saved per part and multiply by the production volume.
- Machine & Investment Costs: Compare the cost of acquiring and operating a capable hard turning center versus a suitable grinding machine (and potentially a separate lathe for soft turning). Consider floor space and utility requirements as well.
- Operational Costs: Weigh the benefits of dry machining in hard turning (no coolant costs) against the higher cost and potentially less predictable life of CBN/ceramic tools compared to grinding wheels and dressing tools. Factor in labor costs for setups and operation.
- Total Cost Per Part: The ultimate comparison involves calculating the Total Cost of Ownership (TCO)5 per part for each feasible process chain. This includes machine time, labor, tooling (inserts vs. wheels/dressing), consumables (coolant or lack thereof), setup time, and handling costs. Often, hard turning proves more cost-effective when the cycle time savings and elimination of coolant outweigh the higher tooling costs, especially for medium to high production volumes or complex parts.
- Flexibility Value: Don’t underestimate the value of flexibility. A turning center capable of hard turning can often be quickly repurposed for other turning jobs (soft or hard), potentially offering better machine utilization than a dedicated grinder.
By systematically analyzing the part’s requirements (tolerance, finish), its features (complexity, material), and the total economic picture (efficiency, cost), you can make an informed decision on whether hard turning is the more sensible and profitable approach compared to grinding for your specific application.
What Materials and Applications Are Ideal for Hard Turning?
Now that we understand the process and its trade-offs, where does hard turning typically shine in the real world?
Hard turning is most commonly applied to ferrous materials, primarily hardened steels and hard cast irons, that fall within a specific hardness range, generally between 45 and 68 HRC. It finds extensive use in industries where precision, efficiency, and cost-effectiveness are critical for hardened components.
Key sectors leveraging hard turning include the automotive industry (for powertrain and driveline parts), bearing manufacturing, gear production, hydraulics and pneumatics, and mold and die making. It’s chosen for its ability to finish hardened parts quickly and accurately, often replacing traditional grinding operations.
Suitable Material Types and Hardness Ranges (e.g., 45-70 HRC)
Hard turning isn’t suitable for all materials, but it excels within a specific window, primarily involving iron-based alloys that have been heat-treated to high hardness levels.
Common material families successfully machined by hard turning include:
- Case-Hardened Steels: These have a hard outer surface layer and a softer core. Examples include carburized, carbonitrided, or nitrided steels commonly used for gears and shafts. Hard turning effectively removes the hardened case to achieve final dimensions.
- Through-Hardened Steels: These materials have a relatively uniform hardness throughout their cross-section. Bearing steels (like 52100/100Cr6), tool steels (H13, D2), spring steels, and various alloy steels fall into this category after hardening and tempering.
- Induction or Flame Hardened Steels: Steels where only specific surface areas are rapidly heated and quenched to create localized hardness, often used for shafts or ways. Hard turning can precisely machine these hardened zones.
- Hard Cast Irons: Certain types of cast iron with sufficient hardness and suitable microstructure can also be effectively hard turned.
The typical hardness range for efficient hard turning lies between approximately 45 and 68 Rockwell C (HRC). Below this range, conventional turning with carbide tools is usually more economical. Above this range, tool life can decrease significantly, and other processes might become more viable, although turning up to 70 HRC is sometimes possible with specialized tooling and techniques.
Important Note: The suitability of hard turning and the selection of optimal cutting tools and parameters are highly dependent on the specific material grade, its microstructure, and the exact hardness. It’s always recommended to consult with cutting tool suppliers for detailed application recommendations based on your specific material.
Common Industry Applications (Automotive, Bearings, Gears, Molds)
Hard turning has become a cornerstone technology in several major manufacturing sectors due to its ability to combine speed, precision, and cost-effectiveness:
- Automotive Industry: This is arguably the largest user of hard turning. High production volumes demand efficient processes. Hard turning is used extensively for finishing transmission components (shafts, gears), engine parts (crankshaft journals – less common now but historically significant, valve seats), driveline components (CV joints, axle shafts), and fuel system parts. The goal is often to replace grinding to reduce cycle times and costs.
- Bearing Industry: Precision is paramount for bearings. Hard turning is widely used to finish the raceways, faces, and bores of inner and outer bearing rings made from hardened bearing steels, often achieving the required accuracy and surface finish without grinding.
- Gear Manufacturing: After gears are heat-treated for strength and wear resistance, hard turning is frequently used to finish non-gear tooth surfaces like faces, bores, and journals to tight tolerances, ensuring proper alignment and fit.
- Hydraulics and Pneumatics: Components like valve spools, pistons, rods, and cylinder bores require good surface finishes and tight tolerances on hardened materials for sealing and wear resistance. Hard turning provides an efficient way to achieve these specifications.
- Mold and Die Industry: Hard turning is used to machine hardened tool steels for mold cavities, cores, slides, and other components used in injection molding, die casting, and stamping, where hardness and dimensional accuracy are crucial.
Examples of Typical Hard-Turned Components
To make this more concrete, here are some specific examples of parts frequently finished using hard turning across various industries:
- Automotive:
- Transmission input/output shafts (bearing journals, seal surfaces)
- Gear wheel faces and bores
- Constant Velocity (CV) joint bells, cages, and inner races
- Differential pinions and side gears
- Select crankshaft and camshaft features (historically)
- Fuel injection pump components
- Bearings:
- Inner and outer bearing rings (raceways, shoulders, bores, ODs)
- Gears:
- Gear blanks (bores, faces, journals) prior to final gear cutting/grinding
- Finished gear features (non-tooth surfaces)
- Hydraulics/Pneumatics:
- Valve spools (grooves, diameters)
- Hydraulic cylinder rods and pistons
- Molds & Dies:
- Mold cores and cavities with rotational symmetry
- Ejector pins and guide bushings
- Die components for stamping or casting
These examples illustrate the versatility of hard turning in producing precise functional surfaces on a wide variety of hardened components critical to modern machinery and vehicles.
What Are the Essentials for Implementing Hard Turning Successfully?
Alright, you’ve decided hard turning is the way to go. What absolutely needs to be in place to make it work reliably and effectively?
Successful hard turning implementation relies on a tightly integrated system approach. This requires four essential pillars: selecting a machine tool with exceptional rigidity and precision, choosing the precisely correct cutting tool material and geometry for the specific task, meticulously optimizing the cutting parameters (speed, feed, depth of cut), and ensuring rock-solid workpiece clamping and overall process stability.
Getting any one of these elements wrong can compromise the entire process, potentially leading to poor part quality, inconsistent results, rapid tool wear, or even damage to the machine or workpiece. Careful planning and attention to detail in each area are crucial for realizing the full benefits of hard turning.
Selecting the Right High-Performance Machine Tool
We’ve mentioned that hard turning demands rigidity and precision, but what does that mean when choosing equipment? You can’t just use any lathe off the shop floor.
- Focus on Stiffness: Look for machines explicitly designed or rated for hard turning. Key indicators include:
- Massive, well-damped base structures: Often using materials like polymer concrete or cast iron with optimized ribbing to absorb vibration. Think of this as the essential foundation for a skyscraper – without a solid base, the structure won’t be stable or reach its potential height (precision).
- Robust guideways: Wide, preloaded linear roller guides or heavy-duty box ways provide stiffness under load.
- Rigid turret and tool clamping: Ensure minimal deflection where the tool meets the part.
- Thermally Stable Design: Features like spindle cooling, ballscrew cooling, and insulated castings help maintain accuracy during long runs by minimizing heat-induced expansion.
- Precision Components:
- High-accuracy spindle: Check specifications for low runout (axial and radial) and good balance, crucial for achieving fine finishes and tolerances.
- Precise axis drives: High-resolution encoders and responsive servo motors ensure the tool follows the programmed path accurately. Think of the machine’s precision like high-fidelity audio equipment – any distortion or noise (vibration/inaccuracy) introduced by the player (machine) degrades the output quality (part quality), regardless of the speakers (tool).
Investing in a machine platform truly capable of handling the stresses of hard turning is non-negotiable.
Choosing Appropriate Cutting Tool Materials and Geometries
Having the right machine is only half the battle; selecting the optimal cutting tool is equally critical. This goes beyond just picking CBN or ceramic.
- Matching Tool Material to Workpiece: Different grades of CBN (e.g., high CBN content for continuous cuts, lower CBN content with ceramic binders for interrupted cuts) and various ceramic types (e.g., SiAlONs, whisker-reinforced) excel in different applications. Consulting tool manufacturers is essential to match the tool grade to your specific workpiece material, its exact hardness, and whether the cut is smooth or interrupted.
- Insert Geometry: The shape of the cutting insert matters. Round inserts often provide the strongest cutting edge, while other shapes (like rhombic or triangular) offer more versatility for profiling. Wiper geometries feature a special flat on the cutting edge to improve surface finish at higher feed rates.
- Edge Preparation: This is vital in hard turning, influencing factors like tool life and surface integrity. Understanding edge radiusing6 is crucial. A razor-sharp edge, ideal for soft materials, would chip instantly on hardened steel. Common edge preparations include:
- Hone: A very small radius applied to the edge to increase strength.
- Chamfer (K-land): A small flat angle ground onto the edge, providing significant strengthening.
The size and angle of the hone or chamfer significantly impact tool life and surface integrity. Again, supplier recommendations based on the application are key.
- Coatings: Modern coatings (e.g., TiAlN, AlCrN based) applied to CBN or ceramic inserts can further enhance performance by reducing friction, improving wear resistance, and preventing material adhesion.
Choosing the right combination is like selecting the perfect knife for the job – a bread knife (with its specific edge geometry) for bread, a paring knife (different shape, perhaps sharper edge prep) for detailed work. The wrong tool makes the job harder and gives poor results.
Optimizing Cutting Parameters (Speed, Feed, Depth of Cut)
You can have the best machine and the perfect tool, but using the wrong settings will lead to poor results. Optimizing cutting parameters is a balancing act.
- Cutting Speed (Vc): This is how fast the workpiece surface moves past the tool. In hard turning, speeds are generally high (often 100-200 m/min or 300-650 sfm, but highly variable).
- Too low: Can cause rubbing, poor chip formation, and built-up edge.
- Too high: Increases heat, accelerates tool wear, may negatively impact surface integrity.
- Feed Rate (f): This is how fast the tool advances along or into the workpiece per revolution.
- Too low: Inefficient, can cause rubbing and accelerate certain types of tool wear.
- Too high: Increases cutting forces, risk of tool chipping/fracture, poorer surface finish (unless using wiper inserts). Typical finishing feeds are often low (e.g., 0.05-0.15 mm/rev or 0.002-0.006 ipr).
- Depth of Cut (ap): How much material the tool removes in one pass.
- Finishing passes usually involve very small depths (e.g., 0.05-0.25 mm or 0.002-0.010 inches) to minimize forces, control heat, and achieve final tolerance/finish.
- Roughing passes (if applicable) can be deeper but require robust tooling and careful force management.
Finding the optimum requires a methodical approach, often starting with supplier recommendations and then fine-tuning through testing while monitoring tool wear, surface finish, dimensional accuracy, and chip formation. Never assume standard parameters will work; always verify ranges with your tool supplier for your specific machine and material combination.
Ensuring Secure Workholding and Process Stability
The final essential piece is ensuring the entire cutting system is stable, starting with how the workpiece is held using effective workholding.
- Rigid Workholding: The chuck, collet, or fixture must grip the hardened part securely without causing distortion. High gripping forces are often needed to counteract the cutting forces. Consider:
- Chuck/Collet Quality: Use high-precision, high-rigidity chucks or collets maintained in good condition.
- Jaw/Collet Design: Ensure sufficient contact area and appropriate serrations or gripping surfaces for hardened parts.
- Part Geometry: Ensure the part itself is rigid enough to withstand clamping and cutting forces without excessive deflection. Thin-walled parts require special consideration.
- Tailstock Support: For shaft-like parts, using a rigid tailstock with adequate center pressure is almost always mandatory to prevent deflection and vibration.
- Toolholder and Turret Stability: Ensure toolholders are robust, properly seated, and securely clamped in the turret. The connection between the insert and the toolholder is also critical.
- Minimizing Vibration: Vibration is the enemy. It ruins surface finish, causes inconsistent dimensions, and drastically shortens tool life. Stability comes from the combination of a rigid machine, strong tooling, secure workholding, and optimized cutting parameters that avoid exciting natural frequencies of the system.
Think of the entire setup – from the machine base up to the tool tip and the workpiece – as a structural system, like a three-legged stool. If any leg (machine rigidity, tool stability, workholding security) is weak or wobbly, the whole thing is unstable and cannot perform its function reliably.
Conclusion
In summary, hard turning presents a powerful and efficient alternative to grinding for finishing hardened components across a wide range of industries. By understanding its fundamental principles, leveraging its key advantages like speed and flexibility, and carefully managing its challenges related to tooling and process control, manufacturers can make informed decisions about when and how to implement it successfully. Achieving success requires a holistic approach, focusing on the crucial interplay between the machine tool, cutting tool, cutting parameters, and workholding stability to unlock the full potential of this demanding yet rewarding machining process.
References
- Material properties1 – AZoM article detailing the properties of Cubic Boron Nitride.
- IT6 or IT5 range2 – Engineers Edge page explaining ISO Tolerance Grades (IT Grades).
- Surface integrity3 – ScienceDirect topic page providing an overview of surface integrity in engineering.
- Difference between cutting and grinding4 – ZYDiamondTools blog post comparing cutting and grinding processes.
- Total Cost of Ownership (TCO)5 – ZYDiamondTools guide explaining the TCO concept and application for superhard tooling & abrasives.
- Edge radiusing6 – ZYDiamondTools blog post explaining the importance of edge preparation for PCBN inserts.
ZY Superhard Tools Co., Ltd.
Do you have any needs for PCD tools or diamond grinding wheels? We can customize products to meet your specific requirements. If you have any ideas or requests, feel free to reach out—we’ll respond within 24 hours!
Do you have any needs for PCD & CBN tools or diamond grinding wheels? We can customize products to meet your specific requirements. If you have any ideas or requests, feel free to reach out—we’ll respond within 24 hours!
Do you have any needs for PCD & CBN tools or diamond grinding wheels? We can customize products to meet your specific requirements. If you have any ideas or requests, feel free to reach out—we’ll respond within 24 hours!
Post Categories
Product Categories
About Company
Related Posts
What is a Wire Drawing Die and How Does it Actually Work?
Discover what a wire drawing die is and how it works. This guide covers die materials like PCD and carbide,
Why Is My Solid CBN Insert Chipping or Wearing Out Fast on Cast Iron Rolls?
Diagnose and fix the two main failures of solid CBN inserts: chipping and rapid wear. Learn why it happens on
How Do You Machine a Ball Screw for a Perfect Fit? A Step-by-Step Guide
Learn how to machine a ball screw with our step-by-step guide. Covers proper clamping, hard turning with CBN tools, and
Honing vs. Internal Grinding: Which Precision Finishing Process Is Right for Your Application?
Learn the key differences between honing and internal grinding. This guide covers mechanics, surface finish, and accuracy to help you
Subscribe
Simply enter your email below and click “Subscribe” to stay connected with everything new and exciting.