-
Whatsapp: +86 13526572721
-
Email: info@zydiamondtools.com
-
Address: AUX Industrial Park, Zhengzhou City, Henan Province, China
-
Whatsapp: +86 13526572721
-
Email: info@zydiamondtools.com
-
Address: AUX Industrial Park, Zhengzhou City, Henan Province, China
What Are the Most Common Superhard Tool Materials and Where Are They Used?
- Industry Knowledge, PCD & CBN Tools Knowledge
- -2023-01-03
- - byKevin Ray
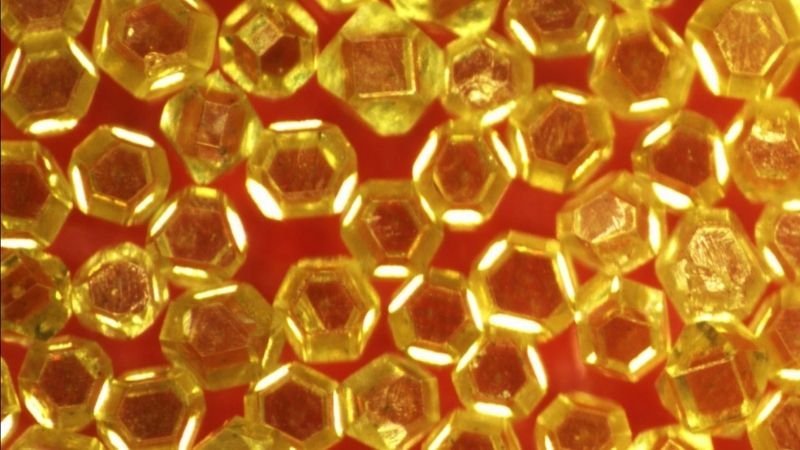
When tackling tough materials, what are the most common superhard tool options available, and what jobs are they best suited for?
The most common superhard tool materials are diamond (in various forms like PCD, CVD, MCD) and Cubic Boron Nitride (CBN/PCBN). Diamond excels in machining non-ferrous metals, composites, ceramics, and achieving ultra-precision finishes, while CBN is the primary choice for hard ferrous materials like hardened steel and cast iron due to its chemical stability at high temperatures. Advanced ceramics also serve as important near-superhard alternatives in specific high-heat applications.
Table of Contents
ToggleHow Do We Define Superhard and What Are Their Key Properties?
So, what exactly makes a material “superhard,” and what properties define this special group of materials used in advanced tooling?
Superhard materials are generally defined by their exceptionally high hardness, typically measured above 40 Gigapascals (GPa) on the Vickers scale. Their key properties include outstanding wear resistance derived from this hardness, high thermal conductivity (though this varies significantly), specific chemical stability characteristics influencing their application, and relatively lower toughness compared to many conventional tool materials.
Let’s break down these defining characteristics.
Defining Superhardness: Hardness Scales Explained (Vickers, Mohs)
When we talk about hardness, what do we really mean? Hardness is simply a material’s resistance to scratching or indentation (being dented). Think about trying to scratch a windowpane – your fingernail won’t work, but a specialized glass cutter, often tipped with a hard material, will.
Two common scales help us measure this:
- Mohs Scale1: This is a simpler, relative scale from 1 (Talc, very soft) to 10 (Diamond, the hardest natural material). It tells you which materials can scratch others. While easy to understand, it doesn’t show the magnitude of difference, especially at the top end; the jump from 9 (Corundum) to 10 (Diamond) is much larger than lower steps.
- Vickers Hardness Test2 (Hv): This is a more precise, quantitative test used in industry. It measures the indentation left by a diamond pyramid pressed into the material under a specific force. The result is given in Gigapascals (GPa). This scale clearly shows how much harder one material is than another. The benchmark for “superhard” is often set at 40 GPa.
For context:
- Hardened Steel: Might be around 8-9 GPa.
- Tungsten Carbide (Common tool material): Often 15-25 GPa.
- Cubic Boron Nitride (CBN): Typically 45-65 GPa.
- Diamond: Can range from 70 GPa up to over 150 GPa for certain types.
(Note: These are typical ranges; specific grades from different manufacturers can vary.)
Essential Property 1: Unmatched Hardness & Wear Resistance
This is the star property. Because superhard materials like diamond and CBN are significantly harder than almost any workpiece material (metals, composites, ceramics), they can cut and shape them effectively.
This extreme hardness directly translates to exceptional wear resistance. Wear happens when a tool’s edge gets ground down or abraded during use. A harder tool resists this abrasion much better. Imagine trying to sand down a rock versus sanding down a piece of wood – the rock resists wear far more.
This means tools made from superhard materials generally:
- Last much longer than conventional tools when machining difficult materials.
- Maintain their sharp cutting edge for longer, leading to better accuracy and surface finish on the workpiece.
- Allow for faster cutting speeds, increasing productivity.
Essential Property 2: Managing Heat – Thermal Conductivity & Stability
Cutting generates a lot of heat right at the tool’s tip. Managing this heat is crucial for tool life and performance. Two thermal properties matter here:
- Thermal Conductivity3: This measures how quickly heat can travel away from the cutting edge through the tool material. High thermal conductivity is usually good, as it prevents the tip from overheating. Diamond, especially certain types, has extraordinarily high thermal conductivity – much better than copper! CBN also has good thermal conductivity.
- Thermal Stability (Hot Hardness): This describes how well a material keeps its hardness when it gets very hot. Some materials soften significantly at high temperatures. Superhard materials generally maintain high hardness even at elevated cutting temperatures. CBN, for instance, is known for its exceptional thermal stability, making it suitable for high-heat applications.
A key point here is that thermal properties can vary significantly based on the specific type and grade of superhard material (e.g., different types of diamond, varying CBN content). Always check the specific data provided by the tool supplier.
Essential Property 3: Chemical Inertness and Reactivity Issues
How does the tool material react chemically with the material being cut, especially at high temperatures?
- Chemical Inertness: Ideally, a tool material shouldn’t react with the workpiece. Reactions can cause the tool to degrade quickly (diffusion wear) or cause material from the workpiece to weld onto the tool tip (built-up edge).
- Reactivity: This is where a major distinction arises, particularly relevant later when comparing diamond and CBN. Diamond, being carbon, can react chemically with iron-based (ferrous) materials like steel and cast iron at the high temperatures generated during cutting. This limits its effectiveness in high-speed steel machining. CBN, however, is much more chemically stable when cutting ferrous materials, making it the preferred choice for those applications.
Understanding this chemical behavior is vital for selecting the right superhard material for a specific job.
The Toughness Compromise: Strength vs. Brittleness
While incredibly hard, superhard materials generally have lower toughness4 compared to materials like High-Speed Steel (HSS) or many grades of Tungsten Carbide.
What is toughness? It’s a material’s ability to resist fracturing or chipping when subjected to sudden impacts, vibrations, or stress concentrations. Think of it like this: a ceramic plate is very hard (resists scratching) but not very tough (it shatters easily if dropped).
This lower toughness means:
- Superhard tools can be more prone to chipping or breaking if used improperly (e.g., heavy interrupted cuts, machine tool instability, incorrect geometry).
- Machine setups need to be rigid and stable.
- Tool geometries (edge preparations) are often designed to add strength, sometimes slightly sacrificing sharpness for durability.
It’s a trade-off: you gain extreme hardness and wear resistance but must manage the lower toughness through careful application and tool design. This is a fundamental concept in selecting and using superhard tooling effectively.
Why is Diamond (Natural, PCD, CVD, MCD) a Primary Choice?
Given other options available, why does diamond remain such a go-to choice for many demanding tooling applications?
Diamond, in its various forms (Natural, PCD, CVD, MCD), is a primary tooling choice due to its unmatched hardness leading to exceptional wear resistance, generally high thermal conductivity, and the ability to produce extremely sharp cutting edges. These properties make it ideal for efficiently machining abrasive non-ferrous materials and composites, as well as achieving ultra-precise finishes, despite its key limitation when working with ferrous metals at high temperatures.
Let’s explore the different types of diamond used in tooling and why they are so effective.
Understanding Diamond Tool Variants: Natural Crystal, Polycrystalline (PCD), CVD, and Monocrystalline (MCD)
Not all diamond tools are the same. The term “diamond tooling” covers several distinct forms, each with its best uses:
Diamond Type | Structure | Key Feature / Primary Use |
---|---|---|
Natural Diamond | Single crystal, mined from the earth | Historically significant, high cost, variable quality. Used less now in industry. |
Polycrystalline (PCD) | Synthetic diamond grains sintered5 with a binder (e.g., Cobalt) | Most common type for general machining; balances wear resistance, toughness, and cost. |
CVD Diamond | Diamond film grown chemically (Chemical Vapor Deposition6) | Often binderless, high purity/thermal stability. Used as coatings or solid tools. |
Monocrystalline (MCD)7 | Single perfect crystal (natural or lab-grown) | Enables the sharpest possible edge (nanometer level) for ultra-precision, mirror finishes. |
- Natural Diamond: While historically important, natural diamonds are expensive and can have inconsistencies. They are less common in modern industrial cutting tools compared to synthetic options.
- Polycrystalline Diamond (PCD): This is the workhorse. Imagine tiny diamond grits fused together under high pressure and temperature with a metal binder (like cobalt) onto a tungsten carbide base. This creates a tough, wear-resistant layer. PCD comes in different grades, mainly varying by diamond grain size. Larger grains offer higher abrasion resistance but a less fine edge, while smaller grains provide sharper edges but may wear slightly faster in highly abrasive materials. Because performance depends heavily on the grade, it’s crucial to consult with your supplier to choose the right PCD specification for your specific application.
- CVD Diamond: Instead of sintering powder, this diamond is “grown” atom by atom onto a surface using chemical reactions in a vacuum chamber. It can create thick, often pure diamond layers without the metallic binder found in PCD. This purity can lead to even higher thermal conductivity and stability. It’s used both for coating other tool materials and for making solid diamond tools.
- Monocrystalline Diamond (MCD): This is a single, flawless diamond crystal (either a select natural stone or, increasingly, a lab-grown one). Because it’s a perfect crystal structure, it can be sharpened to an incredibly fine edge – think sharpness measured in nanometers! This makes MCD the ultimate choice for creating extremely smooth, mirror-like surfaces.
Core Advantages Shared by Diamond Tools
Despite the variations, most diamond tools share these powerful benefits:
- Extreme Hardness and Wear Resistance: As the hardest known material, diamond offers unparalleled resistance to abrasion. When machining highly abrasive materials like high-silicon aluminum or carbon fiber composites, diamond tools can outlast carbide tools by factors of 10x, 50x, or even more, leading to significant cost savings through longer tool life and less downtime.
- High Thermal Conductivity: Diamond excels at pulling heat away from the cutting edge. This helps prevent the edge from overheating, preserving its hardness and sharpness, especially during high-speed machining operations.
- Low Coefficient of Friction: Diamond surfaces are very slippery against many materials. This reduces the force needed to make a cut, generates less heat, and helps prevent workpiece material from sticking to the tool edge (known as built-up edge or BUE).
- Potential for Extremely Sharp Edges: While MCD offers the ultimate sharpness, even fine-grained PCD and smooth CVD diamond can achieve cutting edges sharper than most other tool materials. This contributes to cleaner cuts, better surface finishes, and lower cutting forces.
Key Application Areas: General Machining (PCD/CVD) vs. Ultra-Precision & Mirror Finishes (MCD)
Where do these advantages translate into real-world use?
General Machining Applications (Primarily PCD and CVD):
- Non-Ferrous Metals: This is a major area. High-silicon aluminum alloys used in automotive engines (pistons, blocks), copper alloys used in electronics, brass, magnesium, and titanium alloys are all machined efficiently with diamond tools, often at very high speeds.
- Abrasive Non-Metallic Materials: Diamond is essential here. Examples include:
- Composites: Carbon Fiber Reinforced Polymers (CFRP) and Glass Fiber Reinforced Polymers (GFRP) used in aerospace, automotive, and sporting goods are notoriously abrasive. Diamond tools (especially PCD) provide the needed wear resistance for trimming, routing, and drilling.
- Graphite: Used for electrodes in EDM processes.
- Ceramics: Especially in their “green” or partially sintered states.
- Wood Products: Highly abrasive materials like particleboard, MDF, and hardwood flooring.
- Stone and Concrete: Cutting, grinding, and drilling applications often rely on diamond segments embedded in tools.
Ultra-Precision & Mirror Finish Applications (Primarily MCD):
- Optics: Machining molds for plastic lenses, creating reflective surfaces on metals for telescopes or laser systems.
- Electronics: Finishing critical components requiring extreme smoothness.
- Medical Devices: Creating implants or surgical tools with exceptionally smooth surfaces.
- Research & Development: Any application demanding surface finishes measured in nanometers (billionths of a meter).
Important Limitations: Reactivity with Ferrous Metals
Despite its strengths, diamond has one major limitation: it reacts chemically with iron at high temperatures.
Above approximately 700°C (1300°F), the carbon atoms in diamond can dissolve into iron-based materials like steel and cast iron. This causes rapid chemical wear, quickly dulling the diamond tool. Therefore, diamond tools are generally unsuitable for high-speed machining of ferrous materials. While some very specific low-speed finishing operations might be possible, diamond is not the recommended choice for productive steel or iron cutting. This is the primary reason why CBN was developed, as we’ll discuss later. Additionally, remember the inherent lower toughness (brittleness) requires stable machines and careful handling to avoid chipping the cutting edge.
When is Cubic Boron Nitride (CBN / PCBN) the Go-To Material?
Since diamond, despite its hardness, struggles with steel and iron at high speeds, when does its close relative, Cubic Boron Nitride or CBN, become the essential choice for tough machining tasks?
Cubic Boron Nitride (CBN) and its polycrystalline form (PCBN) are the go-to superhard materials primarily when machining hard ferrous metals (like hardened steels and cast irons) and certain challenging superalloys. This selection hinges on CBN’s unique combination of high hardness (second only to diamond), excellent thermal stability (hot hardness), and its crucial chemical inertness towards iron, even at the high temperatures generated during cutting.
Let’s delve into what makes CBN uniquely suited for these specific, demanding applications.
Introducing CBN and PCBN: Synthesized for Specific Needs
Cubic Boron Nitride (CBN) is a synthetic material created under conditions similar to synthetic diamond manufacturing. It doesn’t exist naturally. Structurally, it’s very similar to diamond, but instead of carbon atoms, it uses alternating boron and nitrogen atoms. This structure gives it hardness approaching that of diamond.
Just like diamond has PCD, CBN is most commonly used in tooling in its polycrystalline form: PCBN (Polycrystalline Cubic Boron Nitride).
- PCBN is made by sintering fine CBN grains together under high pressure and temperature.
- These grains are typically bonded using a binder, which can be ceramic (like TiN, TiC, Al2O3) or sometimes metallic.
- This sintered PCBN “tip” or “nib” is usually brazed onto a tougher tungsten carbide substrate to form a cutting tool insert.
Different grades of PCBN are engineered for specific tasks. They vary in:
- CBN Content: High CBN content (e.g., >85%) is often used for cast iron, while lower CBN content (e.g., 40-65%) with specific ceramic binders is typically preferred for hard turning.
- Grain Size: Affects the balance between edge toughness and wear resistance.
- Binder Type: Influences toughness, chemical stability, and wear characteristics.
Choosing the correct PCBN grade is vital for optimal performance. Factors like the workpiece material, whether the cut is continuous or interrupted, and required surface finish all play a role. Always refer to manufacturer recommendations or consult with your tooling supplier.
Core Advantages of Using CBN Tools
CBN tools offer a distinct set of properties tailored for their niche:
- Very High Hardness & Wear Resistance: While diamond is harder, CBN (typically 45-65 GPa Vickers) is still vastly harder than conventional materials like ceramics or tungsten carbide. This provides excellent resistance to abrasive wear when cutting hard ferrous materials or gritty cast irons.
- Exceptional Thermal Stability (Hot Hardness): This is where CBN truly shines, especially compared to diamond in certain environments. CBN maintains its hardness remarkably well at very high temperatures encountered during high-speed cutting of hard materials – often remaining effective above 1000°C (1832°F). Diamond’s practical temperature limit is lower, particularly when oxygen or ferrous materials are present.
- Chemical Stability with Iron: This is the key differentiator from diamond for many applications. CBN is largely chemically inert when machining steel and cast iron, even at high temperatures. It doesn’t readily react or dissolve, preventing the rapid chemical wear that plagues diamond in these situations.
- Good Thermal Conductivity: While generally lower than diamond, it’s still good enough to help conduct heat away from the cutting zone.
Key Application Areas: Excelling in Hardened Steels, Cast Irons, and Superalloys
CBN/PCBN finds its primary use where other materials struggle, specifically with:
- Hard Turning / Hard Machining8: This involves machining steel components after they have been hardened (typically above 45 HRC, often 58-65 HRC). PCBN tools can often replace slower grinding operations for finishing parts like:
- Bearing races and components
- Gears and transmission shafts
- Axles and driveshafts
- Dies and molds
This offers benefits like faster cycle times, potentially improved surface integrity (compressive residual stress), and the ability to machine complex shapes in a single setup.
- Cast Iron Machining: Excels at high-speed cutting of various cast irons, including:
- Grey Cast Iron (e.g., automotive brake discs, engine blocks)
- Ductile Iron
- Compacted Graphite Iron (CGI)
PCBN provides long tool life despite the abrasive nature of these materials. High CBN content grades are often preferred here.
- Superalloy9 Machining: Used for finishing cuts on difficult-to-machine nickel-based (e.g., Inconel) and cobalt-based superalloys commonly found in aerospace (jet engine parts) and power generation turbines. These materials generate intense heat and pressure during cutting.
- Sintered Ferrous Materials / Powder Metallurgy (PM): Effectively machines hard and often abrasive PM parts used in automotive and other industries.
The Chemical Stability Advantage for Ferrous Machining
Let’s underscore this critical point: Why choose CBN for steel or iron when diamond is technically harder? It comes down entirely to chemistry at high temperatures.
As mentioned, diamond (carbon) reacts with iron above roughly 700°C, leading to rapid tool failure through diffusion wear. Cutting hard steel or cast iron at productive speeds easily generates temperatures exceeding this limit.
CBN, made of boron and nitrogen, does not have this chemical affinity for iron. It remains stable, resisting chemical breakdown even when the cutting edge gets extremely hot during ferrous metal machining. This chemical inertness is the fundamental reason CBN tools can successfully machine hardened steels and cast irons at high speeds, offering productivity and tool life far beyond what diamond or even advanced ceramics can achieve in these specific, challenging applications. It effectively overcomes diamond’s main limitation for a huge segment of industrial materials.
How Do Diamond and CBN Tools Directly Compare?
Now that we’ve looked at both diamond and CBN individually, how do these two leading superhard materials stack up directly compare10 when it comes to choosing the right tool?
Diamond and CBN tools primarily differ in their optimal application ranges due to chemical stability: diamond excels with non-ferrous materials and composites but reacts with hot iron, while CBN is chemically stable with ferrous metals like steel and cast iron at high temperatures. Diamond is generally harder and has higher thermal conductivity, whereas CBN often boasts superior thermal stability (hot hardness) and the crucial chemical inertness needed for machining iron-based materials.
Understanding these key differences is crucial for making the right choice for performance and efficiency.
Head-to-Head: Hardness vs. Thermal & Chemical Stability
Let’s compare their core properties side-by-side:
Property | Diamond (Typical Range) | CBN (Typical Range) | Key Takeaway |
---|---|---|---|
Hardness (Vickers) | ~70 – 150+ GPa | ~45 – 65 GPa | Diamond is significantly harder. |
Thermal Conductivity | Very High (~1000 – 2200+ W/m·K) | Good to Very Good (~100 – 1300 W/m·K) | Diamond generally removes heat more effectively. |
Thermal Stability | Lower limit with Fe/O₂ (~700°C / 1300°F) | Excellent (stable >1000°C / 1832°F) | CBN maintains hardness better at extreme cutting temperatures, especially with iron. |
Chemical Stability | Reacts with Ferrous Metals at high temp. | Inert with Ferrous Metals at high temp. | The critical difference for application selection. |
Toughness | Generally Low | Generally Low (but varies by grade) | Both require stable machining; specific grades offer toughness variations. |
(Note: Specific values for hardness, thermal conductivity, and toughness can vary significantly based on the type (PCD, MCD, PCBN grade) and manufacturer. Always check supplier specifications.)
What does this table tell us?
- Diamond wins on pure hardness and heat removal. Its incredible hardness provides maximum abrasion resistance, and its high thermal conductivity pulls heat away quickly.
- CBN wins on high-temperature performance, especially with steel/iron. Its ability to retain hardness when very hot (thermal stability) and its lack of chemical reaction with iron (chemical stability) are its defining advantages in specific areas.
Application Showdown: Choosing Between Ferrous and Non-Ferrous Machining
These property differences lead to distinct application fields:
- Choose DIAMOND (PCD, CVD, MCD) for:
- Non-Ferrous Metals: Aluminum alloys (especially high-silicon), copper, brass, magnesium, titanium alloys.
- Abrasive Non-Metals: Carbon/glass fiber composites (CFRP/GFRP), graphite, ceramics (green/sintered), plastics, fiberglass.
- Wood Products: MDF, particleboard, hard woods, laminate flooring.
- Stone & Concrete: Cutting, grinding, drilling.
- Ultra-Precision Needs: Mirror finishes on suitable materials (typically non-ferrous metals or plastics) using MCD.
- Why? Diamond’s superior hardness handles the abrasion, its sharp edge capability provides finish, and it doesn’t react chemically with these materials.
- Choose CBN (PCBN) for:
- Hardened Ferrous Metals: Steels heat-treated above ~45 HRC (hard turning/milling).
- Cast Irons: Grey iron, ductile iron, CGI, chilled iron.
- Superalloys: Nickel-based (Inconel) and Cobalt-based alloys (often finishing operations).
- Sintered Ferrous Metals: Hard powder metallurgy components.
- Why? CBN’s chemical stability prevents reactions with iron at high cutting temperatures, and its excellent hot hardness allows it to maintain a cutting edge under intense heat and pressure.
The core rule is simple: If the material is iron-based (steel, cast iron) and you’re machining it productively (generating significant heat), CBN is almost always the correct superhard choice. For most other abrasive or high-precision applications, diamond is the leader.
A Note on Relative Cost and Performance Value
Both diamond and CBN tools represent a significant investment compared to conventional carbide or HSS tools. Determining which is “more expensive” is complex:
- Costs vary greatly depending on the specific type (e.g., PCD vs. MCD), the grade (CBN content, grain size), the size of the diamond/CBN tip, the complexity of the tool body, and the manufacturer.
- A simple PCD insert might be less costly than a certain complex, high-CBN content PCBN insert, but a large MCD tool will likely be more expensive than both.
Instead of focusing purely on initial price, consider the performance value or cost-per-part11:
- The higher upfront cost is often quickly recovered through:
- Dramatically longer tool life: Reducing the number of tool changes and tool purchases.
- Faster cycle times: Higher cutting speeds and feeds increase machine throughput.
- Improved part quality: Better surface finishes and dimensional accuracy reduce scrap or rework.
- Process consolidation: For example, hard turning with PCBN can eliminate separate grinding operations.
When used in the correct application, the productivity gains from superhard tools typically provide excellent value and lower the overall cost of manufacturing the component. As costs are highly variable, obtaining quotes for specific tools tailored to your application is essential.
Quick Selection Guide: Matching the Material to the Job
Here’s a simplified thought process for choosing between diamond and CBN:
- Identify Your Workpiece Material:
- Ferrous (Steel > 45 HRC, Cast Iron)? → CBN / PCBN is likely required.
- Non-Ferrous (Al, Cu, Composites, Ceramics, Wood, Plastic, Graphite)? → Diamond (PCD / CVD) is likely the best choice.
- Superalloy (Inconel, etc.)? → Often CBN / PCBN for finishing, but check specific recommendations (ceramics might also be options).
- Need an optical / mirror finish? → MCD (on suitable non-ferrous/plastic materials).
- Consider the Operation:
- Is it a heavy, interrupted cut? You might need a tougher grade of PCD or PCBN.
- Is surface finish paramount? Finer grain PCD, smooth CVD, or MCD might be needed.
- Consult Your Tooling Supplier: This is always the best final step. Provide details about your material, machine, operation, and goals (tool life, finish, speed). They can recommend the most suitable specific grade and geometry (e.g., PCD grain size, PCBN content/binder) from their offerings, like those available from ZYDiamondTools, to ensure optimal results.
Other Significant Hard Materials in Tooling
While diamond and CBN are the primary focus when discussing superhard tools, it’s worth looking at other significant hard materials used in demanding applications.
While diamond and CBN dominate the true superhard tooling landscape (typically defined as >40 GPa Vickers hardness), advanced ceramics serve as significant near-superhard alternatives. These ceramics are valued for their excellent hot hardness and chemical stability in specific high-speed applications, particularly with cast iron or superalloys. Additionally, research continues into emerging potentially superhard materials like boron carbide or carbon nitrides, although these are not yet common in mainstream cutting tools.
Let’s briefly touch upon these other important material classes.
Brief Overview: Advanced Ceramics as Near-Superhard Alternatives
Ceramic cutting tools aren’t technically “superhard” by the strict 40 GPa definition – most fall in the 15-30 GPa Vickers range, similar to or slightly above tungsten carbide. However, their exceptional performance at high temperatures places them in a similar category of advanced materials used for challenging applications.
What makes ceramics useful in tooling?
- Excellent Hot Hardness: Ceramics retain their hardness exceptionally well at very high cutting temperatures, often even better than CBN in some respects. This allows for very high cutting speeds, especially when machining cast irons or heat-resistant superalloys.
- High Chemical Stability: They generally don’t react chemically with workpiece materials, resisting diffusion wear and built-up edge formation.
- Availability & Cost: Often less expensive than PCD or PCBN alternatives.
However, they also have limitations:
- Lower Toughness: Ceramics are typically more brittle (less tough) than even PCD and PCBN, making them sensitive to vibrations, interruptions in the cut, and improper handling. They require rigid machines and stable cutting conditions.
- Lower Thermal Conductivity: Compared to diamond or CBN, ceramics don’t conduct heat away as quickly, which can concentrate heat at the cutting edge.
Common Types of Tooling Ceramics:
- Alumina-Based (Al₂O₃):
- White Ceramics: Pure alumina, good wear resistance, used mainly for finishing cast iron.
- Black Ceramics (Mixed): Alumina mixed with other materials like Titanium Carbide (TiC) to improve toughness and thermal conductivity. Widely used for machining cast irons and some hardened steels.
- Silicon Nitride (Si₃N₄): Generally tougher than alumina ceramics with better thermal shock resistance. Excellent for high-speed rough machining of gray cast iron.
- SiAlONs: A family of materials based on Silicon (Si), Aluminum (Al), Oxygen (O), and Nitrogen (N). They offer a good balance of hardness, toughness, and high-temperature strength, often used for machining heat-resistant superalloys (HRSA).
- Whisker-Reinforced Ceramics: A ceramic base (like alumina) reinforced with extremely strong, tiny single crystals (“whiskers”) of Silicon Carbide (SiC). This significantly increases toughness and thermal shock resistance, making them suitable for demanding superalloy machining.
As with PCBN, the specific grade and composition of a ceramic tool drastically affect its performance. Close consultation with tooling suppliers is essential to select the right ceramic for a given application.
Mention of Other Emerging Superhard Candidates
While diamond, CBN, and advanced ceramics cover the vast majority of today’s high-performance tooling for difficult materials, researchers are always exploring new possibilities. Some materials studied for their potential superhardness include:
- Boron Carbide (B₄C): This material is extremely hard (around 30-38 GPa) and lightweight. However, it’s also quite brittle and difficult to consolidate into dense forms suitable for sharp cutting edges. Its primary uses currently are in wear-resistant parts, abrasive nozzles, and armor, rather than mainstream cutting tools.
- Carbon Nitrides (e.g., β-C₃N₄): Theoretical calculations suggest some forms of carbon nitride could potentially be harder than diamond. However, actually synthesizing these materials in stable, usable forms has proven extremely difficult. They remain largely in the realm of laboratory research.
- Other Complex Borides, Carbides, Nitrides: Ongoing research explores various compounds involving boron, carbon, nitrogen, and sometimes metals (like Tungsten Boride, Osmium Diboride) aiming to achieve novel combinations of hardness, toughness, and stability.
For now, these emerging materials haven’t reached widespread commercial use in cutting tools the way diamond and CBN have. The challenges often lie in synthesizing high-quality material affordably and achieving sufficient toughness for reliable tooling applications. Diamond and CBN remain the established leaders when true superhard performance is required.
Conclusion
Choosing the right advanced cutting tool material boils down to understanding the specific demands of your application. Diamond and CBN stand out as the premier superhard materials, each with a distinct area of expertise defined largely by chemical compatibility. Diamond, in its versatile forms like PCD and MCD, reigns supreme for non-ferrous metals, composites, and ultra-precision work. CBN, particularly as PCBN, is the essential solution for productively machining hard steels, cast irons, and superalloys. While advanced ceramics offer valuable high-temperature capabilities as near-superhard options, the ultimate selection always depends on matching the material’s properties – hardness, stability, toughness, and reactivity – to the workpiece and machining conditions. For optimal results and value, always consult with experienced tooling providers, like ZYDiamondTools, to leverage their expertise in selecting the perfect superhard solution for your needs.
References
- Mohs Scale1 – Wikipedia page explaining the relative scale of mineral hardness.
- Vickers Hardness Test2 – Wikipedia page detailing the quantitative indentation hardness test.
- Thermal Conductivity3 – Wikipedia page defining and explaining thermal conductivity in physics.
- Toughness4 – Wikipedia page explaining the concept of toughness in materials science.
- sintered5 – Wikipedia page describing the process of sintering used to form solid materials from powders.
- Chemical Vapor Deposition6 – Wikipedia page explaining the CVD process used to produce thin films and coatings.
- Monocrystalline (MCD)7 – ZYDiamondTools blog post explaining MCD tools and their use for precision finishes.
- Hard Turning / Hard Machining8 – ZYDiamondTools blog post explaining the process of hard turning.
- Superalloy9 – Wikipedia page providing an overview of high-performance superalloys.
- directly compare10 – ZYDiamondTools blog post specifically comparing PCD and CBN cutting tools.
- performance value or cost-per-part11 – ZYDiamondTools blog post explaining Total Cost of Ownership (TCO) for superhard tooling.
ZY Superhard Tools Co., Ltd.
Do you have any needs for PCD tools or diamond grinding wheels? We can customize products to meet your specific requirements. If you have any ideas or requests, feel free to reach out—we’ll respond within 24 hours!
Do you have any needs for PCD & CBN tools or diamond grinding wheels? We can customize products to meet your specific requirements. If you have any ideas or requests, feel free to reach out—we’ll respond within 24 hours!
Do you have any needs for PCD & CBN tools or diamond grinding wheels? We can customize products to meet your specific requirements. If you have any ideas or requests, feel free to reach out—we’ll respond within 24 hours!
Post Categories
Product Categories
About Company
Related Posts
Which Turning Insert Shape Should You Choose?
Master turning insert selection. Our guide covers choosing the right shape for your job, decoding ISO codes, and selecting the
How Do You Solve Vibration, Chip Control, and Surface Finish Issues in PCD Grooving?
Solve common PCD grooving problems. This guide details how to fix vibration, improve chip evacuation, and achieve a flawless sidewall
Why Is Your Tooling Wearing Out Prematurely? A Machinist’s Guide to Key Causes & Proven Solutions
Facing premature tool wear? Learn the key causes like heat, vibration, & wrong parameters. Discover proven solutions from setup to
How Do You Select the Optimal PCD Tools for Scroll Compressor Machining?
Learn how to select the right PCD tools for scroll compressor machining. This guide covers the benefits over carbide, key
Subscribe
Simply enter your email below and click “Subscribe” to stay connected with everything new and exciting.