-
Whatsapp: +86 13526572721
-
Email: info@zydiamondtools.com
-
Address: AUX Industrial Park, Zhengzhou City, Henan Province, China
-
Whatsapp: +86 13526572721
-
Email: info@zydiamondtools.com
-
Address: AUX Industrial Park, Zhengzhou City, Henan Province, China
What Are Diamond Grinding Wheels and Why Should You Care?
- Grinding Wheels Knowledge, Knowledge
- -2025-04-03
- - byKevin Ray
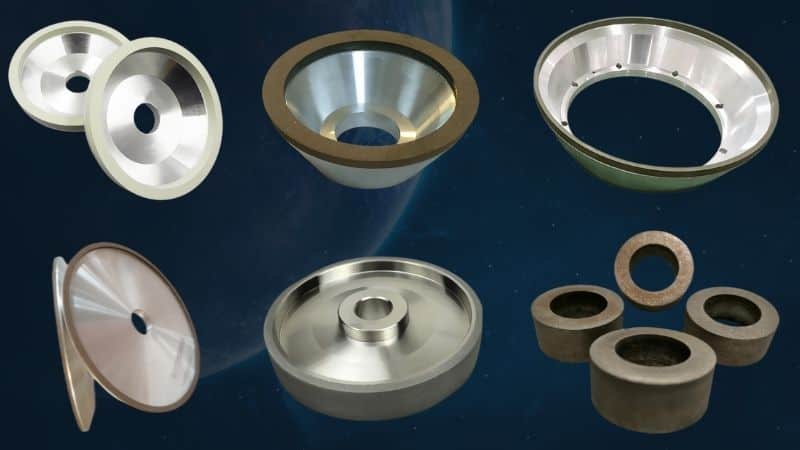
What exactly are diamond grinding wheels and why are they important?
Diamond grinding wheels are specialized abrasive tools that use diamond particles bonded together to precisely shape, cut, or finish extremely hard or brittle materials like carbide, ceramics, glass, and stone. Their importance lies in their unique ability to efficiently process these challenging materials, enabling crucial manufacturing processes in industries requiring high precision and durability, from aerospace components to medical implants and construction tasks.
Table of Contents
ToggleHow Do Diamond Wheels Actually Grind Materials?
So, how exactly does a diamond grinding wheel cut through tough materials?
Diamond grinding wheels work by using superhard diamond particles, held in place by a bonding material, to precisely shear off tiny chips from the workpiece through friction and abrasion as the wheel rotates at high speed. Essentially, the diamond crystals provide the cutting edges, while the bond controls how these diamonds are exposed and supported during the grinding process.
The Role of Diamond Abrasives
Think of a diamond grinding wheel as a very advanced piece of sandpaper, designed for extremely hard materials. The “grit” on this wheel isn’t sand, however; it’s tiny particles of diamond. Diamond is known as the hardest natural material on Earth. This incredible hardness is what allows the wheel to effectively cut or grind other very hard substances like carbide, ceramics, or hardened steel.
Microscopic Cutting Action
Each individual diamond particle on the wheel acts like a miniature cutting tool. As the wheel spins rapidly against the workpiece, these sharp diamond edges physically scrape and shear away tiny fragments, or chips, of the material. This process is known as abrasion. It’s not melting the material, but rather mechanically removing it bit by bit at a microscopic level. The size of these diamond particles, known as the grit size, influences how quickly material is removed and the smoothness of the final surface. Finer grits have smaller diamond particles for smoother finishes, while coarser grits use larger particles for faster material removal.
Synthetic vs. Natural Diamonds
While natural diamonds can be used, most modern grinding wheels utilize synthetic diamonds. Manufacturers can create synthetic diamonds with very consistent properties, like size, shape, and strength. This consistency is crucial for producing reliable and predictable grinding wheels for demanding industrial applications, such as shaping carbide cutting tools or finishing aerospace components.
Understanding the Bonding Matrix
The diamond particles can’t do their job alone; they need to be held securely. That’s the primary role of the bonding matrix or simply, the bond. Imagine it as the specialized “glue” that holds the diamond grit onto the wheel and gives the wheel its overall shape and structure. But the bond does more than just hold the diamonds.
Holding the Abrasives Firmly
The bond must securely anchor the diamond particles while they are doing the intense work of cutting. If the bond is too weak, the diamonds can be pulled out prematurely, leading to rapid wheel wear and inefficient grinding. This is especially important when grinding under high pressure or working on particularly tough materials.
Controlled Wear for Fresh Cutting Edges
Here’s a critical aspect: the bond itself is designed to wear away gradually during grinding. Why? Because as the diamond particles cut, they eventually become dull or slightly fractured. For the wheel to continue cutting effectively, these worn diamonds need to fall away, exposing fresh, sharp diamond particles embedded deeper within the bond.
This controlled erosion of the bond is vital.
- If the bond wears away too quickly, the wheel life will be very short, increasing costs.
- If the bond wears away too slowly, the dull diamonds remain on the surface. The wheel can become “glazed” or “loaded,” meaning it loses its cutting ability, generates excess heat, and can potentially damage the workpiece.
The type of bonding material used (such as in Resin bond diamond wheels1) significantly influences this wear rate and how the wheel performs. Different bond formulations are engineered for specific materials and grinding conditions. Therefore, the precise wear characteristics and suitability can vary, making it important to consult supplier specifications for the intended application to ensure optimal performance.
Why is Diamond the Superior Abrasive for Certain Tasks?
What makes diamond stand out as the best choice for grinding specific materials?
Diamond’s superiority for certain grinding tasks stems primarily from its exceptional hardness, allowing it to cut the toughest materials. This is combined with its outstanding ability to conduct heat away from the grinding zone and its remarkable resistance to wear, ultimately leading to longer tool life and greater precision.
Unmatched Hardness for Tough Materials
Hardness simply means how well a material resists scratching or indentation. On this front, diamond is in a class of its own – it is the hardest known substance found in nature. Think about trying to scratch a diamond; it’s incredibly difficult.
Comparing Diamond Hardness
This extreme hardness is key to its grinding ability. To effectively grind a material, the abrasive must be significantly harder than the material being ground. Diamond excels here, especially compared to other common industrial abrasives like silicon carbide (SiC) or aluminum oxide (Al₂O₃).
Abrasive Material | Relative Hardness (Approx. Knoop Scale) | Typical Uses |
---|---|---|
Diamond | ~7000 – 8000+ | Carbide, ceramics, glass, stone, hardened steel |
Silicon Carbide | ~2500 – 2600 | Non-ferrous metals, cast iron, softer materials |
Aluminum Oxide | ~2000 – 2100 | Steels, ferrous alloys |
Note: Hardness values can vary slightly based on measurement method (like the [Knoop Scale]) and specific material grade.
What does this difference mean in practice? Diamond wheels can efficiently grind extremely hard and wear-resistant materials like:
- Tungsten Carbide: Commonly used for cutting tools and wear parts. Conventional abrasives struggle to shape or sharpen carbide effectively.
- Advanced Ceramics: Materials like alumina, zirconia, or silicon nitride used in aerospace, medical, and electronic applications.
- Hardened Tool Steels: Steels treated for maximum hardness.
- Glass and Stone: While other abrasives can work, diamond provides faster cutting and better edge quality.
Without diamond’s hardness, effectively processing these critical materials would be much more difficult, slower, and less precise.
Excellent Thermal Conductivity (Heat Management)
Grinding generates a lot of heat right at the point where the wheel touches the workpiece. This intense localized heat can be a major problem. It can cause thermal damage like cracks, burns, or warping in the material being ground. Excessive heat can also damage the grinding wheel itself, particularly the bond holding the diamonds.
This is where another remarkable property of diamond comes into play: thermal conductivity2. Diamond is the best conductor of heat among all known materials – even better than metals like copper or silver!
Why Heat Management Matters in Grinding
Because diamond transfers heat so efficiently, it acts like a heat sink at the cutting point. It rapidly draws the intense grinding heat away from the immediate contact zone. This heat is then dissipated into the body of the wheel or removed by any coolant being used (wet grinding).
The benefits are significant:
- Reduced Thermal Damage: Minimizes the risk of burning or cracking heat-sensitive materials like certain ceramics or composites.
- Maintained Material Integrity: Helps preserve the desired properties of the workpiece near the ground surface.
- Potential for Higher Productivity: In some cases, better heat management allows for faster grinding speeds or higher material removal rates without causing damage.
- Improved Precision: Less heat distortion contributes to maintaining tighter dimensional tolerances, crucial for precision components like medical implants or optical lenses.
Longevity and Wear Resistance
Logically, because diamond is so incredibly hard, it also resists wearing down. This wear resistance is a major advantage, leading directly to longer wheel life.
Reduced Tooling Costs and Downtime
Diamond grinding wheels typically last much longer than wheels made with conventional abrasives when used on suitable materials. For example, in a production line grinding hundreds of carbide inserts per shift, a diamond wheel might last for days or weeks, whereas a conventional wheel might need replacing multiple times per day. This longevity translates to:
- Lower overall spending on grinding wheels.
- Reduced machine downtime needed for wheel changes.
- More consistent production output.
Maintaining Precision Over Time
Equally important is how well the wheel maintains its shape. Because diamond wears so slowly and evenly, the grinding wheel holds its precise profile for much longer. This ability to maintain form is critical in applications demanding high accuracy:
- Form Grinding: Creating specific shapes or profiles on a part.
- Precision Finishing: Achieving exact dimensions and smooth surfaces on components like bearings or engine parts.
Furthermore, diamond wheels generally require less frequent “dressing.” Dressing is the process of removing dull abrasive grains and restoring the wheel’s proper cutting shape. Less dressing means more time spent actually grinding parts and less material wasted from the wheel itself.
What Are the Main Types and Shapes of Diamond Grinding Wheels?
What different kinds of diamond grinding wheels are available?
Diamond grinding wheels primarily vary by their bond type—which holds the diamond abrasive (resin, metal, vitrified, electroplated)—and their physical shape or profile (like straight wheels, cup wheels, or dish wheels). Crucially, each combination is designed for specific materials and grinding operations.
Classification by Bond Type
The bond is the material that holds the diamond abrasive particles together in the wheel. Think of it as the supporting structure. The type of bond significantly impacts how the wheel cuts, how long it lasts, and what materials it works best on. Choosing the right bond is critical for effective grinding.
Here’s a quick comparison of the main bond types:
Bond Type | Key Characteristics | Typical Applications | Grinding |
---|---|---|---|
Resin | Softer, cooler cutting, good finish, faster wear rate | Carbide grinding (fluting, sharpening), ceramics, glass | Wet/Dry |
Metal | Very durable, long life, holds form well, tougher cut | Glass, ceramics, stone, concrete, cutting abrasive materials | Wet |
Vitrified | Hard, rigid, porous, holds form well, good removal rate | Precision grinding of carbide, ceramics, PCD/PCBN tools | Wet |
Electroplated | Aggressive cut, high diamond exposure, single layer life | Composites, plastics, soft ceramics, form grinding, fast cutting | Wet/Dry |
Let’s look at each bond type more closely:
Resin Bond Wheels
Resin bond wheels use polymers (like phenolic resin) to hold the diamond particles. They are generally considered a “softer” bond compared to metal or vitrified types. This allows them to provide a smoother cutting action and generate less heat, which is beneficial for heat-sensitive materials or achieving fine surface finishes. While they may wear faster, this controlled wear consistently exposes fresh, sharp diamond particles. They are versatile and commonly used for grinding tungsten carbide tools, sharpening applications, and working with ceramics.
Metal Bond Wheels
In these wheels, diamond particles are mixed with metal powders (like bronze, cobalt, or steel alloys) and sintered3 (fused together with heat and pressure). This creates an extremely strong, durable, and wear-resistant bond. Metal bond wheels excel in applications involving highly abrasive materials such as glass, quartz, stone, and concrete cutting or grinding. They hold their shape very well under heavy pressure (good form holding) and offer the longest lifespan. However, they can generate more heat and may have a slower cutting rate than other types, often requiring wet grinding (using coolant).
Vitrified Bond Wheels
Vitrified bonds are essentially a specialized glass or ceramic material that bonds the diamond particles after being fired at very high temperatures. This results in a wheel structure that is hard, rigid, and porous. The porosity helps with coolant delivery and chip removal. Vitrified wheels are known for their excellent form holding, aggressive material removal capabilities, and relative ease of dressing (resharpening the wheel). They are often the preferred choice for high-precision grinding operations on tungsten carbide, advanced ceramics, and superhard materials like PCD (Polycrystalline Diamond) and PCBN (Polycrystalline Cubic Boron Nitride) cutting tools.
Electroplated Wheels
Electroplated wheels feature a single layer of diamond particles attached to a metal core using nickel plating. Because the diamonds are highly exposed, these wheels offer a very aggressive, fast cutting action. They are particularly good at grinding complex shapes (form grinding) because the plating process can precisely follow the shape of the core. However, since there’s only one layer of diamond, they have a limited lifespan compared to bonded wheels and cannot be dressed. They are often used for grinding composites, fiberglass, plastics, and sometimes in specialized metalworking or ceramic applications where rapid stock removal or intricate shape generation is the priority.
Important Note: The specific formulations and resulting performance characteristics of resin, metal, and vitrified bonds can vary significantly between manufacturers. It’s always recommended to consult the supplier’s technical data and recommendations to choose the best bond formulation for your specific material and grinding operation. Don’t just guess based on the general type.
Common Wheel Shapes (Profiles)
Beyond the bond type, the physical shape of the grinding wheel is crucial. The shape determines how the wheel interacts with the workpiece and dictates the type of grinding operation possible. While countless custom shapes exist, several common profiles are widely used:
Straight Wheels (Peripheral Grinding)
This is the most common wheel shape – a simple, flat cylinder (often designated as Type 1 in industry standards). Grinding occurs on the wheel’s periphery, or outer edge. Straight wheels are highly versatile and used for surface grinding (creating flat surfaces), cylindrical grinding (grinding round parts), and general tool sharpening tasks.
Cup Wheels (Face Grinding)
As the name suggests, these wheels are shaped like a cup or bowl. Grinding is done using the rim or face of the wheel. There are two main variations: straight cup wheels (Type 6) and flaring cup wheels (Type 11), where the rim flares outwards. Cup wheels (Type 6 or 11) for face grinding provide a large contact area, making them suitable for quickly grinding large flat surfaces (including concrete floor preparation with large-diameter versions) and for sharpening certain types of cutting tools where face grinding is required.
Dish Wheels (Tool Sharpening)
Dish wheels (often Type 12) resemble cup wheels but are typically thinner and have a profile designed to provide better clearance. Their shape allows them to reach into tighter areas, making them ideal for sharpening tools like milling cutters, saws, or other complex cutting tools where grinding needs to happen on specific surfaces or angles without hitting other parts of the tool.
Other Specialized Shapes
Manufacturers can produce diamond wheels in a vast array of other shapes tailored to specific industrial needs. Examples include wheels with angled faces, tapered edges, specific radius profiles, or complex contours. These are often used in form grinding – where the wheel’s profile is precisely transferred onto the workpiece, such as grinding the intricate ‘fir tree’ root shape on gas turbine blades. The availability and exact dimensions of standard and specialized shapes should always be confirmed with the grinding wheel supplier.
Which Materials and Jobs Require Diamond Grinding Wheels?
When are diamond grinding wheels actually necessary?
Diamond grinding wheels are essential for working with very hard or brittle materials that conventional abrasives cannot effectively cut, such as tungsten carbide, advanced ceramics, glass, and stone. They are also vital in industries requiring high precision and excellent surface finishes, like aerospace, medical device manufacturing, and automotive component production, as well as for demanding concrete and masonry grinding tasks.
Grinding Hard & Brittle Materials (Carbide, Ceramics, Glass, Stone)
The primary reason diamond wheels are chosen is their ability to tackle materials that are simply too hard or too brittle for standard abrasives like aluminum oxide or silicon carbide. If you tried using a conventional wheel on these, it would wear down incredibly fast or potentially shatter the workpiece.
Shaping Tungsten Carbide Tools
Tungsten carbide is extremely hard and wear-resistant, making it ideal for cutting tools (drill bits, end mills, saw blades, inserts) and wear parts. However, this same hardness makes it very difficult to shape or sharpen. Diamond grinding wheels are the standard choice here, capable of precisely grinding carbide to create sharp cutting edges and complex tool geometries.
Processing Advanced Ceramics
Technical ceramics like alumina, zirconia, silicon nitride, and others are used where properties like heat resistance, electrical insulation, or wear resistance are critical. Diamond wheels are needed to:
- Machine ceramic components after firing when they are extremely hard.
- Achieve the very smooth surfaces and tight dimensional tolerances required for parts like electronic substrates, seals, bearings, or medical implants.
- Grind these brittle materials carefully to avoid chipping or cracking.
Working with Glass
From precision optical lenses and prisms requiring near-perfect surfaces to shaping the edges of architectural or automotive glass, diamond wheels are indispensable. They provide a clean, chip-free cut and can achieve the high degree of polish needed for optical applications. Metal bond wheels are often used for rough shaping and cutting, while resin bonds might be used for finer finishing.
Cutting and Finishing Stone
In the stone industry, diamond tools are crucial for cutting and finishing natural stone (like granite and marble) and engineered quartz surfaces for countertops, tiles, and monuments. Diamond saws, core drills, and grinding wheels (often metal bond cup wheels) have the durability needed to cut through these abrasive materials efficiently and shape edges smoothly.
Precision Work in Key Industries (Aerospace, Medical, Automotive)
Beyond just hard materials, diamond wheels are vital where extreme precision and flawless surface finishes are non-negotiable.
Aerospace Component Finishing
The aerospace industry demands parts with incredibly tight tolerances and perfect surface integrity for safety and performance. While other superabrasives like CBN are used for steels, diamond wheels are critical for:
- Grinding ceramic coatings applied to metal parts for heat or wear resistance.
- Finishing components made from composite materials.
- Achieving specific profiles and smooth finishes on various engine and structural parts where diamond is the suitable abrasive.
Medical Device Manufacturing
Precision is paramount in medical manufacturing. Diamond grinding wheels are used to:
- Shape and finish artificial joints (hip and knee implants) often made from ceramics or metals with hard coatings. The required smoothness minimizes friction and wear inside the body.
- Manufacture high-precision surgical instruments.
- Create dental implants, crowns, and grinding burs requiring intricate shapes and biocompatibility finishes.
Automotive Component Production
In the high-volume automotive world, consistency and precision are key. Diamond wheels play a role in grinding:
- Components with hard ceramic coatings for wear or heat resistance.
- Certain engine parts, fuel injection system components, and transmission parts made from hard materials requiring precise dimensions and finishes to ensure efficiency and longevity.
Concrete and Masonry Applications
Moving away from high-tech manufacturing, diamond grinding wheels are also workhorses in the construction and renovation industry. Their durability makes them ideal for the highly abrasive nature of concrete and stone. Common uses include:
Floor Preparation and Surface Grinding
Large diameter diamond cup wheels, often used with angle grinders or specialized floor grinding machines, are employed to:
- Level uneven concrete floors or high spots.
- Remove old coatings like epoxy, paint, or mastic.
- Smooth rough concrete or masonry surfaces before polishing or applying new finishes.
- Prepare surfaces for optimal adhesion of new coatings or overlays.
In all these diverse applications, from microscopic ceramic components to large concrete floors, the unique properties of diamond make it the necessary abrasive choice. Success, however, relies on selecting the correct type of diamond wheel (bond, grit, shape) for the specific material and task at hand.
How Do You Select the Right Diamond Wheel for Your Needs?
How can you figure out which diamond grinding wheel is the right one for your job?
Selecting the correct diamond grinding wheel involves several key steps. You must match the wheel to the specific material being ground, choose the appropriate bond type for the application, determine the right grit size and diamond concentration for the desired finish and removal rate, decide between wet or dry grinding, and finally, identify the necessary wheel shape for the operation.
Choosing the wrong wheel can lead to poor results, short wheel life, damage to the workpiece, or even unsafe operating conditions. Let’s break down each selection factor:
Matching the Wheel to the Material
This is the starting point. As we’ve discussed, diamond wheels are primarily for hard, brittle, or highly abrasive materials.
- Confirm the Material: Know exactly what you are grinding. Is it tungsten carbide, a specific type of ceramic (like alumina or zirconia), glass, granite, concrete, or something else? Different grades within these categories can sometimes influence the best wheel choice.
- Rule Out Alternatives: If you are grinding softer steels or non-ferrous metals like aluminum, other abrasives like CBN (Cubic Boron Nitride) or conventional aluminum oxide might be more suitable and cost-effective. Diamond is generally not the best choice for ferrous materials due to potential chemical reactions at high grinding temperatures.
Choosing the Correct Bond Type
Once you know the material, you need to select a bond that works well with it and suits your grinding goals. Recall the main types:
- Resin bonds offer cooler cutting and good finishes, often preferred for carbide tool grinding and heat-sensitive ceramics.
- Metal bonds provide maximum durability and longevity, ideal for highly abrasive materials like glass, stone, and concrete where long life is crucial.
- Vitrified bonds give a balance of hardness, porosity, and good material removal, excellent for precision work on carbides and technical ceramics.
- Electroplated bonds deliver aggressive cutting with high diamond exposure, suitable for composites, plastics, and generating complex shapes.
Crucially, bond formulations are complex. Manufacturers offer various “hardness” levels and specific formulations within each bond type (resin, metal, vitrified). These subtle differences significantly impact performance. Always consult the manufacturer’s recommendations or technical support to select the specific bond code best suited for your material and application. Don’t just guess based on the general type.
Selecting Appropriate Grit Size and Concentration
These two factors control how the wheel cuts and the resulting surface finish.
Understanding Grit Size (Mesh Size)
Grit size refers to the physical size of the diamond particles. It’s usually indicated by a number (mesh size).
- Lower Numbers (e.g., 40, 60, 80): Coarser grit (larger diamond particles). Provides faster material removal but leaves a rougher surface finish. Use for initial shaping or heavy stock removal.
- Medium Numbers (e.g., 100, 120, 150): General-purpose grinding. Offers a balance between removal rate and finish.
- Higher Numbers (e.g., 200, 400, 600+): Finer grit (smaller diamond particles). Provides slower material removal but achieves a much smoother, finer surface finish. Use for finishing passes, achieving tight tolerances, or polishing.
Understanding Diamond Concentration
Concentration indicates the amount of diamond abrasive within the working layer of the bond. It’s often expressed as a number (e.g., C75, C100, C125), where C100 is typically considered a standard concentration.
- Higher Concentration (e.g., C125): More diamond particles. Generally offers longer wheel life and can handle higher grinding pressures. However, it increases wheel cost and might generate more heat.
- Lower Concentration (e.g., C75): Fewer diamond particles. May cut cooler and cost less, but the wheel might wear faster. Often suitable for applications where minimal heat generation is critical.
The ideal grit size and concentration depend heavily on the material, the desired finish, the required removal rate, and the bond type being used. Again, check supplier charts and recommendations, as standards can vary. They often provide starting points based on common applications.
Considering Wet vs. Dry Grinding
The presence or absence of coolant drastically affects the grinding process.
- Wet Grinding (Recommended): Using a coolant (water or specialized grinding fluid) is highly recommended for most diamond grinding operations, especially with metal and vitrified bonds or when precision is required. Coolant keeps the wheel and workpiece cool, flushes away grinding debris (swarf), extends wheel life, and typically allows for better surface finishes and higher productivity.
- Dry Grinding: Sometimes necessary due to the machine setup (like handheld angle grinders) or specific job constraints. If grinding dry, you generally need to use lighter pressure and potentially slower speeds. Wheels specifically designed for dry use (often certain resin or electroplated types) are preferable. Be aware that dry grinding generates significant dust, requiring appropriate respiratory protection and dust extraction systems.
Identifying the Required Wheel Shape
Finally, the wheel’s physical shape must match the grinding operation and fit the machine correctly.
- Match Shape to Task: Select the profile needed for the job – a straight wheel (Type 1) for peripheral grinding, a cup wheel (Type 6 or 11) for face grinding, a dish wheel (Type 12) for tool sharpening clearance, or a specialized profile wheel for form grinding.
- Check Machine Compatibility: Ensure the wheel’s arbor hole4 diameter matches your machine’s spindle. Also, verify the wheel’s overall diameter and thickness are compatible and that the machine’s maximum operating speed (RPM) is suitable and safe for the chosen wheel diameter. These specifications are critical for safe operation.
Choosing the right diamond wheel involves considering all these factors together. Often, consulting the wheel manufacturer’s technical documentation or speaking with their application engineers is the best way to ensure you select the most effective and efficient wheel for your specific needs.
Conclusion
In summary, diamond grinding wheels are indispensable tools in modern manufacturing, construction, and technology. Their effectiveness comes from the unique properties of diamond – its incredible hardness, excellent heat conductivity, and wear resistance. Understanding how they work, the different types of bonds and shapes available, and the specific materials and applications they excel in is crucial. Ultimately, making the right selection based on material, bond type, grit, concentration, grinding conditions, and wheel shape is key to achieving optimal results, ensuring efficiency, precision, and safety in your grinding operations.
References
- Resin bond diamond wheels1 – ZYDiamondTools comprehensive guide to mastering the selection and application of resin bond diamond/CBN grinding wheels.
- thermal conductivity2 – HyperPhysics page providing a table and explanation of thermal conductivity values for various materials.
- sintered3 – ScienceDirect topic page explaining the sintering process in engineering and materials science.
- arbor hole4 – Glossary definition explaining the arbor hole is the central hole in the wheel fitting the machine spindle.
ZY Superhard Tools Co., Ltd.
Do you have any needs for PCD tools or diamond grinding wheels? We can customize products to meet your specific requirements. If you have any ideas or requests, feel free to reach out—we’ll respond within 24 hours!
Do you have any needs for PCD & CBN tools or diamond grinding wheels? We can customize products to meet your specific requirements. If you have any ideas or requests, feel free to reach out—we’ll respond within 24 hours!
Do you have any needs for PCD & CBN tools or diamond grinding wheels? We can customize products to meet your specific requirements. If you have any ideas or requests, feel free to reach out—we’ll respond within 24 hours!
Post Categories
Product Categories
About Company
Related Posts
Why Are CBN Inserts the Key to Successful Hardened Steel Machining?
Learn why hardened steel is tough to machine & how CBN inserts succeed. Our guide covers selection, key parameters, setup
What Are PDC Cutters and Why Are They a Game-Changer in Modern Drilling?
Learn what PDC cutters are, how they’re made, their top uses in oil & gas, and how they differ from
2, 4, or 6 Flutes? How to Choose the Right End Mill for Your Material and Operation
Unlock better machining results. Our guide explains how to choose the right end mill flute count for any material (aluminum,
The Importance of Tool Dynamic Balance: A Complete Guide
Discover the importance of tool dynamic balance. Our complete guide explains its key benefits, how it impacts machine performance, and
Subscribe
Simply enter your email below and click “Subscribe” to stay connected with everything new and exciting.