-
Whatsapp: +86 13526572721
-
Email: info@zydiamondtools.com
-
Address: AUX Industrial Park, Zhengzhou City, Henan Province, China
-
Whatsapp: +86 13526572721
-
Email: info@zydiamondtools.com
-
Address: AUX Industrial Park, Zhengzhou City, Henan Province, China
Unlocking the Indexable Advantage: Maximizing Economics and Flexibility with PCD/CBN Inserts
- PCD & CBN Tools Knowledge
- -2023-07-07
- - byKevin Ray
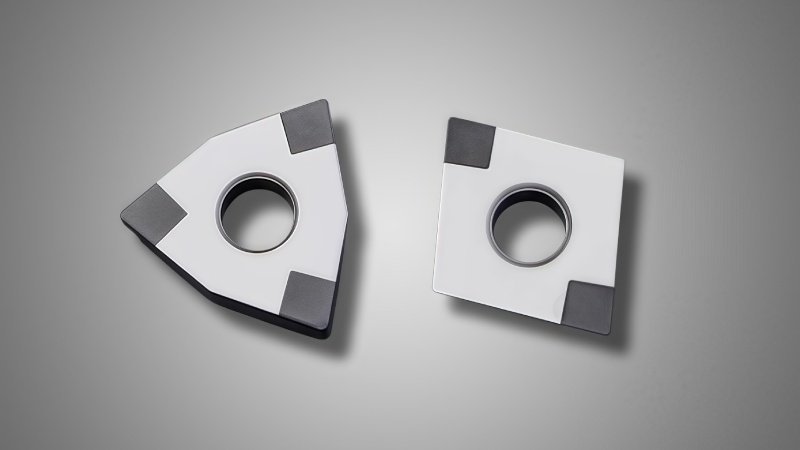
What makes using indexable inserts with advanced materials like PCD and CBN such a smart strategy for improving machining economics and flexibility?
Leveraging the indexable format with PCD/CBN inserts unlocks significant advantages by spreading high material costs over multiple cutting edges, drastically cutting non-productive time via rapid indexing, and enabling process flexibility through standardized tooling and diverse geometries. Successful implementation requires careful handling, appropriate insert selection, stable machining conditions, and optimized parameters, ultimately delivering maximum ROI in high-volume, high-variety, or automated applications.
Table of Contents
ToggleHow Does the Indexable Format Maximize the Cost-Effectiveness of PCD/CBN?
So, how exactly does using indexable inserts, the ones with replaceable cutting tips, make inherently expensive materials like PCD (Polycrystalline Diamond)1 and CBN (Cubic Boron Nitride)2 friendlier to your budget compared to solid or permanently attached (brazed3) tools?
The indexable format maximizes the cost-effectiveness of PCD/CBN primarily by distributing the high initial material cost over multiple cutting edges per insert. Additionally, it drastically reduces costly machine downtime through rapid edge rotation or replacement. Furthermore, it enables tooling standardization, which lowers inventory costs, often resulting in a lower total cost per machined part compared to non-indexable options, especially in demanding or high-volume production.
Leveraging Multiple Edges: Optimizing Cost-Per-Edge for Premium Materials
PCD and CBN are superhard materials, making them fantastic for cutting tough or abrasive substances, but they also come with a higher price tag than traditional carbide4. Now, imagine buying a tool where the entire cutting head is made of this expensive material, or where a single tip is permanently brazed on. If that one edge wears out or chips, the entire tool might need costly regrinding (if possible) or complete replacement. This is where indexable inserts offer a clever solution.
Think of an indexable insert like a small, precisely shaped piece of PCD or CBN held in a reusable steel tool body. The key advantage? This small insert often has more than one usable cutting edge. Depending on its shape (square, triangle, round, etc.) and how it’s used, you might get two, three, four, or even more cutting edges from a single insert.
Calculating the True Edge Cost
Instead of looking at the insert’s purchase price alone, the smarter metric is the cost-per-edge. You calculate this simply:
Cost-Per-Edge = Total Insert Price / Number of Usable Cutting Edges
For example, let’s consider an illustrative scenario:
- A high-quality indexable CBN insert for hard turning might cost $150. If it’s a square insert used in a way that allows four distinct corners (edges) to be used before discarding, the cost-per-edge is $150 / 4 = $37.50.
- In contrast, a custom brazed CBN tool for the same operation might cost $100. However, it effectively has only one edge. When it wears, the entire $100 tool needs attention (re-tipping or replacement), making its initial cost-per-edge $100.
This multi-edge approach significantly lowers the effective cost each time you present a fresh cutting surface to the workpiece, making the high initial investment in PCD/CBN materials much more economical over the insert’s life. Remember, the exact number of usable edges can depend on the specific insert geometry and the depth of cut used in your application; it’s always good practice to confirm this based on the manufacturer’s recommendations and your process.
Slashing Non-Cutting Time: The Economic Gains from Rapid Edge Indexing
Every minute your machine isn’t cutting material is a minute that costs money. Non-cutting time includes tasks like changing worn tools, making adjustments, and setting up new tools. Indexable inserts dramatically reduce this wasted time.
When a cutting edge on an indexable PCD/CBN insert becomes dull:
- The operator simply loosens a clamp screw.
- Rotates (indexes) the insert to expose a fresh, unused edge.
- Tightens the clamp screw.
This entire process can often be completed in just one or two minutes, right at the machine, without removing the main tool body from its holder.
Contrast this with non-indexable tools:
- A brazed tool requires removing the entire toolholder, potentially sending the tool out for re-tipping or regrinding (which takes time and adds cost), and then carefully resetting the new or repaired tool’s position in the machine. This can easily take 15-30 minutes or significantly longer, involving skilled labor and interrupting production flow.
- A solid PCD/CBN tool needs removal for specialized, often expensive, regrinding services, again involving significant downtime and logistical effort.
In high-volume industries like automotive component manufacturing or aerospace production, where cycle times are measured in seconds and machine hour rates are high, these time savings translate directly into substantial cost reductions and increased output. Reducing tool change time from 20 minutes to 2 minutes on a critical machine can significantly boost overall equipment effectiveness (OEE).
Streamlining Tool Logistics: Standardization Benefits via Holders and Inserts
Another often-overlooked economic advantage of indexable systems is standardization. Most indexable PCD/CBN inserts are designed to fit into industry-standard toolholders (following international standards like ISO or other recognized systems).
What does this mean for your shop’s costs?
- Reduced Holder Inventory: You can use the same basic toolholders (for turning, milling, etc.) for various jobs, simply by changing the insert’s grade (PCD or CBN type), geometry, or coating. You don’t need a completely unique, dedicated tool body for every slight variation in application or material.
- Simplified Purchasing & Stocking: Managing inventory becomes easier. Instead of stocking numerous unique brazed tools, you primarily stock reusable holders and a variety of standardized inserts. This reduces the capital tied up in inventory and simplifies procurement.
- Easier Tool Management: Tracking tool life and usage is often simpler with replaceable inserts compared to managing the regrinding cycles and variable life of unique solid or brazed tools. This aids in predictable tooling cost allocation.
This standardization streamlines the entire tooling workflow, from purchasing and inventory to setup and operation, contributing to overall cost efficiency.
Comparative Cost Analysis: Indexable vs. Brazed/Solid PCD/CBN Solutions
So, how do these factors stack up when deciding between indexable and non-indexable PCD/CBN? We need to look beyond the initial purchase price and consider the Total Cost of Ownership (TCO)5 or, more relevantly for machining, the Total Cost Per Part.
While a direct comparison depends heavily on the specific application, material being cut, production volume, and labor/machine rates, we can generalize the key economic differences using a simple comparison:
Feature | Indexable PCD/CBN | Brazed / Solid PCD/CBN |
---|---|---|
Initial Cost | Higher per insert, Lower per holder | Lower per tool (brazed), High (solid) |
Edges per Unit | Multiple | Usually One (brazed), Regrindable (solid) |
Cost Per Edge | Generally Lower | Generally Higher |
Changeover Time | Very Fast (Minutes) | Slower (Minutes to Hours) |
Downtime Impact | Minimal | Significant |
Inventory Needs | Standard Holders, Various Inserts | Many Unique Tools / Regrind Logistics |
Setup Simplicity | High (Standard Pockets) | Moderate to Complex (Resetting) |
Overall TCO | Often Lower in High Volume / Demanding Apps | Can be Lower in Low Volume / Specific Profiles |
When does the indexable advantage typically win on cost?
- High-volume production: Where reduced cycle time and minimal downtime per part have a massive impact.
- Demanding applications: Where tool life is relatively short even for PCD/CBN, making frequent edge changes necessary.
- Operations requiring high precision and consistency: Where rapid, repeatable edge indexing maintains accuracy better than tool resetting.
Conversely, for very specialized, low-volume jobs or profiles where a brazed tool’s specific form is essential and tool changes are infrequent, the lower initial cost of a brazed tool might sometimes be justified. However, for maximizing the cost-effectiveness of premium PCD/CBN materials across a broader range of common applications, the indexable format often provides the superior economic strategy. For a detailed TCO analysis specific to your parts and processes, consulting with tooling suppliers who may offer specialized calculators or case studies is often beneficial.
How Does Indexability Maximize the Application Flexibility of PCD/CBN?
Beyond the cost savings we’ve discussed, how does using replaceable indexable inserts actually make working with specialized PCD and CBN materials more versatile and adaptable for a wider range of machining tasks?
Indexability maximizes the application flexibility of PCD/CBN by enabling rapid switching between different materials or operations using standardized holders. Furthermore, it provides access to a wide variety of readily available insert geometries and chipbreakers. It also ensures consistent quality through precise edge positioning and enhances overall equipment versatility by allowing multiple tasks with interchangeable tooling.
Enabling Production Agility: Fast Adaptation Across Materials and Operations
Imagine needing to machine different types of parts or materials throughout the day. Production agility means being able to switch between these jobs quickly and efficiently. Indexable tooling is a major enabler of this agility when working with PCD and CBN.
Instead of needing entirely separate, dedicated tools (like uniquely shaped brazed tools) for each specific task or material, indexable systems use reusable tool bodies (holders). The “intelligence” or specialization comes from the small, replaceable insert.
Consider a typical scenario:
- A job shop might machine aluminum castings (requiring PCD inserts for good tool life and finish) in the morning.
- In the afternoon, they might need to switch to hard turning heat-treated steel shafts (requiring CBN inserts).
With an indexable system on their CNC lathe, the operator might only need to swap the insert within the same standard turning toolholder. They’d switch from a PCD insert grade and geometry to a suitable CBN insert. This fast adaptation saves significant setup time compared to changing out entire tool assemblies, measuring new tool offsets, and potentially re-programming. This rapid changeover capability allows manufacturers to respond quickly to changing production demands and handle a wider variety of jobs with the same machine setup.
Expanding Design Freedom: Utilizing Diverse Standard Insert Geometries
When engineers design parts or machinists plan a process, having choices in cutting tool geometry is crucial for optimizing performance. Indexable inserts offer a vast library of options, readily available “off-the-shelf.”
These options, often following international standards like ISO, include:
- Different Shapes: Squares (strong corners for roughing), triangles (versatile), rhomboids (good for profiling/finishing), rounds (strong edge, good for profiling or high feeds), and more.
- Various Sizes: To match the scale of the operation and the toolholder.
- Corner Radii: Affects surface finish and edge strength. Smaller radii for fine details, larger radii for strength or high-feed finishing (like wiper inserts).
- Chipbreaker Designs: Molded or ground features on the insert face that help control the metal chips produced during cutting, improving safety and surface quality.
This huge variety means you can easily select an optimal standard insert geometry made from PCD or CBN for nearly any task. Need a strong edge for roughing hardened steel? There’s likely a standard CBN insert shape for that. Need a sharp, pointed insert for finishing an intricate aluminum groove? A standard PCD option probably exists.
This contrasts sharply with brazed or solid tools, where achieving a specific geometry often requires custom design and manufacturing, adding time and cost. The availability of diverse standard geometries provides engineers and programmers much greater design freedom when planning how to machine parts using superhard materials. It’s worth noting that while many geometries are standardized, advanced chipbreaker designs or specialized shapes might be unique to specific tooling manufacturers, so always consult their catalogs for the full range of available options.
Ensuring Consistent Quality: The Role of Precise Edge Positioning
Flexibility isn’t just about variety; it’s also about reliability and predictability. When you machine parts, especially those with tight tolerances (like aerospace or medical components), you need the cutting tool to be exactly where the machine expects it to be, every single time. Indexable systems are designed for this.
Here’s how it works:
- High-quality toolholders have precisely machined pockets or seats.
- The indexable inserts themselves are manufactured to very tight dimensional tolerances.
- When an insert is clamped into the pocket, its cutting edge(s) are located very accurately and repeatably relative to the toolholder body.
Therefore, when an edge wears and you index the insert to a fresh one, that new edge sits in almost the exact same position as the previous one (often within a few microns6). This precise edge positioning means:
- Consistent Part Quality: Tolerances are maintained from part to part, even after indexing.
- Reliable Surface Finish: The cutting action remains consistent.
- Reduced Adjustments: Operators spend less time making minor offset adjustments in the machine control after an index compared to potentially resetting the position of an entire replaced brazed tool.
This consistency is a key aspect of flexibility, as it allows manufacturers to confidently run production processes with minimal interruption and predictable results, even when using multiple edges of an insert.
Maximizing Equipment Versatility with Interchangeable PCD/CBN Tooling
Ultimately, the flexibility offered by indexable PCD/CBN inserts enhances the versatility of the machine tools themselves. A single CNC machine becomes capable of tackling a much broader spectrum of applications efficiently.
Think about a modern CNC machining center or a multi-tasking lathe. By equipping it with a range of standard indexable toolholders, that machine can be quickly configured for various jobs:
- It could perform high-speed milling of aluminum engine blocks using indexable PCD face mills.
- Minutes later, after a tool change involving only swapping inserts (or pre-loaded holders), it could be hard turning steel bearing races using CBN inserts.
- It might then use a different indexable tool with PCD inserts for boring precise holes in a composite component.
This ability to use the same machine and largely the same toolholders for diverse tasks with easily interchangeable PCD/CBN tooling significantly improves the machine’s utilization rate and overall return on investment. It allows manufacturers to consolidate operations, reduce the need for specialized single-purpose machines, and adapt their production capabilities more easily to new market opportunities or product designs. This interchangeability is fundamental to making advanced materials like PCD and CBN practical and flexible for everyday manufacturing challenges.
What Are the Keys to Successfully Leveraging Indexable PCD/CBN Inserts?
So, you understand the potential cost savings and flexibility, but what does it actually take to make these advanced indexable PCD and CBN inserts work reliably and effectively in your day-to-day machining operations?
Successfully leveraging indexable PCD/CBN inserts requires meticulous handling and clamping procedures due to the materials’ inherent brittleness. Success also depends critically on maintaining excellent toolholder integrity and ensuring high machine stability. Furthermore, strategic selection of the correct insert grade, geometry, and edge preparation for the specific application is vital, alongside careful optimization and control of cutting parameters like speed, feed, and depth of cut.
Best Practices: Handling, Clamping, and Care for Indexable Inserts
PCD and CBN are extremely hard, which is why they cut tough materials so well. However, they are also more brittle than traditional carbide, almost like ceramic or glass in some ways. This means careful handling is essential to avoid costly damage before the insert even touches metal. Remember, these inserts represent a significant investment.
Follow these best practices:
- Gentle Handling: Always treat inserts with care. Avoid dropping them or banging them against hard surfaces. Keep them in their original protective packaging until ready for use. Consider using gloves to prevent skin oils from contaminating seating surfaces.
- Immaculate Cleaning: Before mounting an insert, ensure the toolholder pocket and the insert seat itself are perfectly clean. Even tiny chips, dirt, or old residue can prevent the insert from seating correctly. This leads to inaccurate cutting, vibration, and dramatically increases the risk of the insert cracking or failing prematurely. Use compressed air carefully (wear safety glasses!) or appropriate cleaning solutions.
- Correct Clamping Procedures: This is absolutely critical. Use a calibrated torque wrench to tighten the clamping screw or wedge to the exact torque value specified by the toolholder manufacturer.
- Over-tightening is a common mistake and can easily crack the brittle PCD or CBN insert.
- Under-tightening allows the insert to move or vibrate during the cut, leading to poor tool life, bad surface finish, and potential catastrophic failure of both the insert and holder.
- Regularly inspect the clamping screws and mechanisms for wear or damage. Replace them if necessary.
- Careful Indexing: When rotating the insert to expose a new edge, handle it carefully. Avoid touching the sharp cutting edges. Ensure the insert is seated correctly in its new orientation before re-tightening the clamp.
Critical Success Factors: Toolholder Integrity and Machine Stability
Think of the indexable insert as the precision cutting element. For it to perform optimally, the components supporting it – the toolholder and the machine tool – must provide a solid and stable foundation.
- Toolholder Integrity: The condition of the toolholder is paramount.
- Pocket Condition: Inspect the insert pocket regularly for signs of wear, damage, or deformation (sometimes called “pocket wear”). A worn or damaged pocket will not support the insert properly, leading to poor performance and insert breakage. It’s like trying to mount a precision component onto a damaged base.
- Clamping Mechanism Health: Ensure the screw threads and clamp components are in good condition and function smoothly.
- Overall Condition: Check the holder shank for damage and ensure it fits correctly in the machine spindle or turret.
- Machine Stability: PCD and CBN inserts perform best on rigid, well-maintained machine tools.
- Vibration Control: Vibration is the enemy of these brittle materials. It leads to micro-chipping of the cutting edge, poor surface finish, and drastically reduced tool life. Ensure your machine tool structure, slides, and fixtures are robust. This is generally more critical than when using tougher carbide tools.
- Spindle and Bearings: A spindle with worn bearings or excessive runout will induce vibrations and lead to poor results.
- Secure Workholding: The workpiece itself must be clamped rigidly to prevent it from vibrating during the cut.
Addressing these foundational elements is crucial; otherwise, you won’t achieve the full potential life and performance from your premium inserts.
Strategic Insert Selection: Matching Grade, Geometry, and Edge Prep
Using the right indexable PCD/CBN insert for the job is just as important as how you handle it. There’s no single “best” insert; selection must be strategic.
- PCD Grades: Primarily for non-ferrous metals (aluminum alloys, copper, brass), composites, plastics, and wood. Different PCD grades exist with varying diamond grain sizes and binder content, optimized for factors like wear resistance vs. toughness, or for specific materials like high-silicon aluminum.
- CBN Grades: Primarily for hard ferrous materials (hardened steels, cast irons, powdered metals, some superalloys). (It’s worth noting that while CBN refers to the base material, the cutting inserts are typically made from Polycrystalline Cubic Boron Nitride (PCBN), a tough composite material engineered for these demanding applications.) CBN grades vary significantly in CBN content, grain size, and binder type (ceramic or metallic), making them suitable for different hardness levels, continuous vs. interrupted cuts, or specific alloys.
- Reminder: Choosing the optimal grade is critical. Always consult tooling supplier catalogs and technical experts to match the grade precisely to the workpiece material and hardness.
- Geometry Selection: As discussed under Flexibility, the insert’s shape, clearance angles, and size impact its strength and how it interacts with the workpiece. A robust square insert might be chosen for rough turning, while a sharper rhomboid insert might be selected for finishing.
- Edge Preparation: The cutting edge itself often receives special preparation to enhance performance. This isn’t just a sharp edge; it might be:
- Honed: A slight rounding of the edge to increase strength.
- Chamfered (T-land): A small flat surface ground onto the edge for maximum strength, often used in heavy cuts or interrupted cuts.
- The type and size of edge preparation significantly impact tool life, especially in demanding operations. A sharper edge might be used for finishing non-ferrous materials with PCD, while a heavier chamfer might be necessary for interrupted hard turning with CBN.
- Reminder: Edge preparation options and recommendations vary significantly between manufacturers and applications. Verify the suggested preparation for your specific cutting conditions.
Process Optimization: Tailoring Parameters for Indexable Performance
Finally, successfully leveraging these inserts requires optimizing the cutting process itself. You generally cannot just use the same speeds and feeds as you would for carbide.
- Cutting Parameters (Speed, Feed, Depth of Cut – DOC):
- Speeds: PCD can often run at extremely high cutting speeds in aluminum alloys. CBN speeds vary widely based on the material being cut (e.g., speeds for cast iron are often much higher than for hardened steel), the CBN grade, and whether coolant is applied.
- Feeds & DOC: Often, particularly for finishing, feeds and depths of cut with PCD/CBN are lighter or finer compared to carbide capabilities. This helps manage cutting forces and protect the more brittle edge. However, specific grades and geometries are designed for heavier roughing cuts where appropriate.
- Reminder: Start with the tooling manufacturer’s recommended parameters for your specific insert grade and workpiece material. These are crucial starting points. Then, carefully adjust based on observing chip formation, listening to the cut, measuring surface finish, and monitoring tool wear. Finding the optimal parameters for your specific machine and setup is key.
- Coolant Application: The strategy here is critical.
- CBN: Often requires high-pressure flood coolant, especially in hard turning, to manage heat, prevent thermal shock, and aid chip evacuation. However, some CBN grades are designed for dry cutting. Inconsistent coolant application is highly detrimental and can cause immediate thermal cracking.
- PCD: Frequently run dry in aluminum, especially milling. Coolant or Minimum Quantity Lubrication (MQL) might be used to manage chips or improve finish in certain operations.
- Tool Path Strategy: Pay attention to how the tool enters and exits the cut, especially in interrupted cuts (e.g., milling across slots, turning parts with keyways). Abrupt impacts can chip the edge. Programming smoother entries (e.g., rolling into the cut) can significantly improve tool life.
Realizing Maximum ROI with Indexable PCD/CBN
Determining when indexable PCD/CBN offers the best Return on Investment (ROI)7 involves identifying key applications and making strategic assessments based on the economic and flexibility benefits previously discussed.
The indexable advantage for PCD/CBN typically translates to maximum Return on Investment (ROI) in high-volume production runs where reduced cycle times significantly lower cost per part. It’s also highly beneficial in environments with high product variety requiring frequent, fast changeovers, and in automated systems where minimizing human intervention for tool changes is crucial. Ultimately, a careful assessment comparing indexable versus non-indexable options based on specific application demands reveals the optimal path.
Identifying High-Payoff Applications: Volume, Variety, and Automation
While indexable PCD/CBN tooling offers broad advantages, certain applications see these benefits amplified, leading to a much faster and higher ROI. Think about where the core strengths – reduced downtime, multiple edges per insert, and standardization – provide the biggest leverage:
- High-Volume Production: This is a classic high-payoff scenario. Consider automotive powertrain components or standard bearings produced by the thousands or millions.
- Why it pays off: Even small reductions in cycle time per part (achieved through faster indexing or potentially higher cutting speeds enabled by optimal insert choice) multiply into massive savings over the entire production run. The consistent tool life per edge also aids in process predictability, crucial for large volumes. The lower cost-per-edge becomes highly significant.
- High-Variety Manufacturing (Job Shops): Shops handling frequent job changes with different materials or part geometries greatly benefit.
- Why it pays off: The ability to quickly switch inserts (e.g., from PCD for aluminum to CBN for steel) in standard holders drastically cuts down non-productive setup time. This increases machine availability for billable work, directly boosting profitability.
- Automated Environments: Robotic cells, lights-out machining, or minimally attended operations rely on predictable and efficient tooling.
- Why it pays off: Indexable inserts allow for automated tool changes using standard systems. Their predictable life per edge enables planned tool replacements or indexing within the automation logic, minimizing the need for human intervention compared to managing unique brazed or solid tools.
- Demanding Materials or Operations: When machining highly abrasive materials (like some Metal Matrix Composites – MMCs8) or performing aggressive interrupted cuts where even PCD/CBN tool life per edge is limited.
- Why it pays off: Frequent tool changes are unavoidable. The speed advantage of indexing (minutes vs. much longer for replacing other tool types) becomes essential to maintain reasonable productivity and keep costs under control.
If your application falls into one or more of these categories, the strategic value and ROI potential of indexable PCD/CBN are likely very high.
Making the Right Choice: Indexable vs. Non-Indexable PCD/CBN Assessment
Choosing between indexable and non-indexable (brazed or solid) PCD/CBN tooling isn’t always clear-cut. It requires a strategic assessment based on your specific operational realities. Here’s a simplified comparison to guide the decision:
Favor Indexable PCD/CBN When:
- Production volumes are medium to high.
- Tool changes are relatively frequent (due to wear or job changes).
- Minimizing machine downtime is a critical cost factor.
- Operational flexibility and rapid setups are needed.
- Standard insert geometries can effectively machine the required features.
- Process automation is implemented or planned.
- Streamlined tool inventory and management are beneficial.
Consider Brazed or Solid PCD/CBN When:
- Production volumes are very low (e.g., prototyping, one-off repairs).
- Initial tool cost is the absolute primary constraint, and long-term TCO is less critical.
- The required tool geometry is highly complex and cannot be achieved with standard indexable inserts.
- Tool changes are extremely infrequent for the specific operation.
- Maximum possible tool rigidity is perceived as necessary for a unique, challenging cut (though modern indexable systems offer excellent rigidity).
This decision directly impacts your manufacturing costs and flexibility. It’s not just a technical choice; it’s an economic and strategic one.
A Framework for Evaluating the Indexable Advantage in Your Operations
To make an informed decision grounded in data, rather than just feel, use a structured approach. Ask these key questions about your specific application where you’re considering PCD/CBN:
- What is the typical production volume (parts per setup, per month, per year)?
- (Higher volume generally favors indexable).
- How critical is cycle time? What is the machine hour rate?
- (Higher rates make downtime savings from indexing more valuable).
- What is the expected tool life per cutting edge in this specific cut?
- (Shorter life per edge means more frequent indexing, amplifying the time-saving benefit).
- How often do setups or material types change on this machine?
- (More frequent changes favor the flexibility of indexable systems).
- What is the cost difference between an indexable insert (considering cost-per-edge) and a comparable non-indexable tool?
- (Calculate this based on supplier quotes and expected edges).
- What is the estimated time difference for a tool change (indexing vs. replacing/resetting)?
- (Factor in labor time and machine downtime).
- Can standard indexable geometries meet the part requirements effectively?
- (If not, custom non-indexable might be necessary).
- What are the inventory implications (number of unique tools vs. holders/inserts)?
- (Consider storage space and management costs).
- Is process automation a current or future goal for this operation?
- (Automation strongly favors indexable tooling).
By gathering realistic answers to these questions, you can start to build a simple cost model (estimating cost-per-part or TCO) for both the indexable and non-indexable scenarios based on these factors. This data-driven approach allows you to quantify the potential ROI and confidently determine when unlocking the indexable advantage is the most profitable strategy for your PCD/CBN applications. Consulting with experienced tooling application engineers can also provide valuable insights during this evaluation process.
Conclusion
In summary, the indexable format provides a powerful strategic advantage when utilizing advanced PCD and CBN cutting tool materials. By effectively distributing costs over multiple edges, slashing non-productive time, enabling standardization, and offering significant application flexibility, indexable inserts can dramatically improve machining economics. However, unlocking this full potential isn’t automatic. It demands careful attention to best practices in handling and implementation, stable machining conditions, strategic tool selection, and optimized cutting parameters. By thoroughly evaluating your specific production needs against the benefits and requirements outlined here, you can confidently determine where the indexable advantage will deliver the greatest value and make informed decisions to boost your manufacturing efficiency and profitability.
References
- PCD (Polycrystalline Diamond)1 – ZYDiamondTools blog post providing a comprehensive overview of Polycrystalline Diamond (PCD) tools.
- CBN (Cubic Boron Nitride)2 – ZYDiamondTools blog post offering a complete guide to Cubic Boron Nitride (CBN) cutting tools.
- brazed3 – Wikipedia page explaining the metal-joining process of brazing.
- traditional carbide4 – ZYDiamondTools blog post comparing PCD and traditional Carbide cutting tools.
- Total Cost of Ownership (TCO)5 – ZYDiamondTools guide explaining the TCO concept and application for superhard tooling & abrasives.
- microns6 – Wikipedia page explaining the micrometre (micron) as a unit of length.
- Return on Investment (ROI)7 – Investopedia article defining and explaining the financial metric Return on Investment.
- Metal Matrix Composites – MMCs8 – Wikipedia page explaining Metal Matrix Composites.
ZY Superhard Tools Co., Ltd.
Do you have any needs for PCD tools or diamond grinding wheels? We can customize products to meet your specific requirements. If you have any ideas or requests, feel free to reach out—we’ll respond within 24 hours!
Do you have any needs for PCD & CBN tools or diamond grinding wheels? We can customize products to meet your specific requirements. If you have any ideas or requests, feel free to reach out—we’ll respond within 24 hours!
Do you have any needs for PCD & CBN tools or diamond grinding wheels? We can customize products to meet your specific requirements. If you have any ideas or requests, feel free to reach out—we’ll respond within 24 hours!
Post Categories
Product Categories
About Company
Related Posts
Which Turning Insert Shape Should You Choose?
Master turning insert selection. Our guide covers choosing the right shape for your job, decoding ISO codes, and selecting the
How Do You Solve Vibration, Chip Control, and Surface Finish Issues in PCD Grooving?
Solve common PCD grooving problems. This guide details how to fix vibration, improve chip evacuation, and achieve a flawless sidewall
Why Is Your Tooling Wearing Out Prematurely? A Machinist’s Guide to Key Causes & Proven Solutions
Facing premature tool wear? Learn the key causes like heat, vibration, & wrong parameters. Discover proven solutions from setup to
How Do You Select the Optimal PCD Tools for Scroll Compressor Machining?
Learn how to select the right PCD tools for scroll compressor machining. This guide covers the benefits over carbide, key
Subscribe
Simply enter your email below and click “Subscribe” to stay connected with everything new and exciting.