-
Whatsapp: +86 13526572721
-
Email: info@zydiamondtools.com
-
Address: AUX Industrial Park, Zhengzhou City, Henan Province, China
-
Whatsapp: +86 13526572721
-
Email: info@zydiamondtools.com
-
Address: AUX Industrial Park, Zhengzhou City, Henan Province, China
Is PCD Tooling the Key to Faster, Cheaper, Better Aluminum Machining?
- PCD & CBN Tools Knowledge
- -2023-07-11
- - byKevin Ray
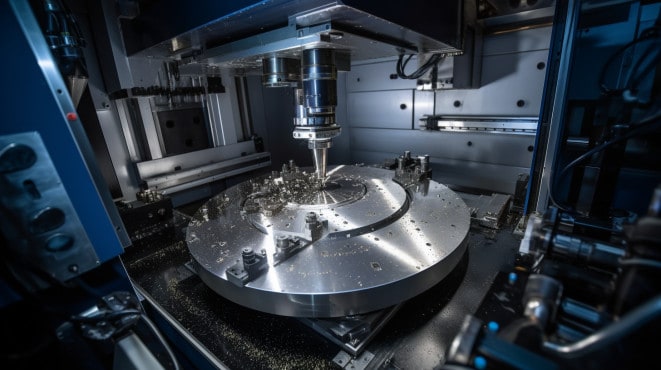
So, what’s the verdict – is PCD tooling really the ultimate solution for machining aluminum?
Yes, in many demanding applications, PCD (Polycrystalline Diamond) tooling provides a powerful combination of significantly faster machining speeds, lower overall cost per part despite higher initial investment, and superior surface finish and tool life compared to traditional carbide tools when machining aluminum, especially in high-volume or abrasive alloy scenarios.
Table of Contents
ToggleHow Does PCD Achieve Significantly Higher Machining Speeds?
So, how exactly does PCD tooling manage to cut aluminum so much faster than other materials like carbide?
Simply put, PCD (Polycrystalline Diamond)1 achieves significantly higher machining speeds primarily due to its exceptional hardness, which resists wear even under intense conditions, and its excellent thermal conductivity, which rapidly draws heat away from the cutting edge, preventing degradation at high temperatures.
Extreme Hardness and Wear Resistance Explained
Imagine trying to cut something tough with a dull knife versus a razor-sharp one. Which one works faster and better? The sharp one, right? PCD works on a similar principle, but at an extreme level.
PCD is made by fusing tiny, synthetic diamond particles together under immense heat and pressure. Diamond is the hardest natural material known. This incredible hardness2 gives PCD cutting edges several key advantages for high-speed machining:
- Maintaining Sharpness: Because PCD is so hard, its cutting edge doesn’t dull quickly, even when cutting through aluminum at high speeds. A sharp edge cuts more efficiently, requires less force, and allows for faster movement. Carbide tools, while hard, wear down much faster, especially when machining abrasive aluminum alloys, forcing operators to slow down to preserve tool life.
- Resisting Abrasion: Some aluminum alloys, particularly those with high silicon content (common in automotive castings), are quite abrasive. Think of it like cutting fine sandpaper – it wears things down quickly. PCD’s hardness allows it to withstand this abrasive wear far better than carbide, maintaining its cutting ability for longer periods at higher speeds. This means fewer tool changes and more consistent cutting performance.
Therefore, the sheer hardness of PCD directly translates to its ability to handle the physical demands of high-speed aluminum machining without rapidly breaking down.
Thermal Conductivity Advantages for High RPMs
Cutting metal generates a lot of heat, especially at high speeds (RPMs – Revolutions Per Minute). If this heat isn’t managed, it can soften the cutting tool’s edge, causing it to wear out faster or even fail completely. This is where PCD shines again due to its excellent thermal conductivity3.
Think of thermal conductivity like a heat highway. Materials with high thermal conductivity let heat travel through them very quickly. Diamond is one of the best thermal conductors available.
- PCD as a Heatsink: When a PCD tool cuts aluminum at high speed, the intense heat generated at the very tip is quickly pulled away from the cutting edge and dissipated into the body of the tool and the machine spindle. This prevents the critical cutting edge from overheating.
- Carbide’s Limitation: Carbide, while decent, doesn’t conduct heat nearly as well as PCD. At very high speeds, heat can build up right at the cutting edge of a carbide tool, potentially softening it and drastically reducing its effectiveness and lifespan. This thermal limitation is a major reason why carbide tools often can’t match PCD’s top speeds in aluminum.
Consequently, PCD’s ability to manage heat effectively is crucial for maintaining edge integrity and performance when running machines at the very high RPMs needed for optimal productivity in aluminum. However, it’s also important to consider that extremely high speeds can impact the aluminum workpiece itself, requiring careful control to maintain desired quality and avoid issues related to the material’s behavior under intense heat.
Practical Speed and Feed Ranges vs. Carbide
So, what does this difference in hardness and heat management mean in practice? It means PCD can often run dramatically faster than carbide when machining aluminum. A deeper look into the differences between PCD and carbide tools4 highlights these performance gaps.
While exact parameters depend heavily on the specific aluminum alloy, the machine’s capability (rigidity, spindle power), the depth of cut, and the tool supplier’s recommendations, here’s a general comparison:
Feature | Typical Carbide Range (Aluminum) | Typical PCD Range (Aluminum) | Key Advantage of PCD |
---|---|---|---|
Cutting Speed | 300 – 1000 m/min (approx.) | 1000 – 6000+ m/min (approx.) | 3x to 10x (or more) higher cutting speed |
Feed Rate | Often lower to manage wear | Can often be significantly higher | Faster material removal per revolution |
Data represents typical ranges; actual performance varies.
Important Note: These speed and feed ranges are general guidelines. The optimal parameters for your specific application can vary significantly based on the factors mentioned earlier (machine, material, tool design). Always consult your tooling supplier for their specific recommendations for the PCD tool and aluminum alloy you are using.
Industry data and case studies, particularly from high-volume sectors like automotive manufacturing (e.g., machining engine blocks or transmission cases), consistently show significant cycle time reductions when switching from carbide to PCD tooling, often achieving the higher end of these speed ranges. Tools like specific PCD end mills for aluminum5 are designed to maximize these benefits. This increased speed directly translates to higher throughput and productivity, driven by PCD’s unique combination of hardness and thermal stability.
Does the High Initial Cost of PCD Truly Pay Off?
Okay, it’s clear PCD tooling costs more to buy initially than standard carbide tools, but does that bigger price tag actually make financial sense when machining aluminum?
Yes, absolutely. Despite the higher upfront purchase price, PCD tooling frequently delivers substantial long-term cost savings for aluminum machining, especially in high-volume production settings. This financial benefit stems directly from significantly longer tool life (reducing replacement frequency and costs), minimized machine downtime due to fewer tool changes, and faster cycle times that increase overall productivity and lower the cost per part.
Calculating Total Cost of Ownership (TCO) for Aluminum Parts
When you’re deciding if PCD is worth the investment, looking only at the initial price tag doesn’t tell the whole story. You need to consider the Total Cost of Ownership (TCO)6, which gives you a much clearer picture of the true cost over the tool’s entire working life. Think of it like buying a car – the purchase price is just one part; fuel efficiency, maintenance, and how long it lasts also determine the real cost.
For cutting tools, TCO includes several key factors beyond the initial purchase:
Initial Tool Cost vs. Lifetime Value
While a PCD insert or end mill might cost several times more than its carbide equivalent, it often lasts dramatically longer – sometimes 50 to 100 times longer, or even more, in the right aluminum application. This means you buy far fewer PCD tools over time compared to carbide tools for the same amount of work. You are trading a higher initial cost for significantly reduced replacement costs down the line.
Factoring in Machine Time and Productivity
This is often the biggest saving. As we saw earlier, PCD allows much faster cutting speeds and feeds. This means:
- Shorter Cycle Times: Each part is finished faster.
- Higher Throughput: You can produce more parts in the same amount of time using the same machine and operator.
When you factor in the cost of running the machine (electricity, operator wages, overhead), producing parts faster directly lowers the cost attributed to each individual part.
Considering Associated Operational Costs
Other costs add up too:
- Downtime Costs: Less frequent tool changes mean the machine spends more time cutting and less time idle (we’ll explore this next).
- Tool Setting Costs: Time spent setting up new tools is reduced.
- Quality Costs: Sometimes, the better, more consistent finish from PCD (discussed later) can reduce or eliminate the need for secondary finishing steps, saving time and money.
- Inventory Costs: Holding fewer replacement tools in stock might be a minor saving.
It’s crucial to understand the typical cost structure in machining. Often, the direct cost of the cutting tool represents only a small percentage (perhaps 5-15%) of the total cost to produce a part. The majority comes from machine time, labor, overhead, and energy. This perspective highlights why improvements driven by advanced tooling like PCD – such as reduced cycle times and minimized downtime – can have such a significant positive impact on overall manufacturing costs, even if the tool itself costs more initially.
Calculating TCO involves looking at all these elements. While the exact calculation depends on your specific operational costs, the principle remains: PCD’s longevity and speed often drastically reduce the operational costs per part, outweighing the higher initial tool price in many aluminum applications.
The Economic Impact of Reduced Downtime and Tool Changes
Every time a machine stops production to change a worn-out cutting tool, it costs money. This downtime is a significant hidden cost in manufacturing. Why?
- Lost Production: The machine isn’t making parts.
- Operator Time: An operator is busy changing the tool instead of overseeing production.
- Potential Scrap: Sometimes tool changes can lead to minor inconsistencies on the first part run after the change.
This is where PCD’s incredible tool life offers a massive economic advantage. Let’s consider a simplified example:
Imagine machining 100,000 aluminum components.
- Using Carbide: If a carbide insert lasts for, say, 500 parts, you would need 200 tool changes (100,000 / 500). If each tool change takes 5 minutes of machine downtime, that’s 1,000 minutes (over 16 hours!) of lost production time just for tool changes.
- Using PCD: If a PCD insert performing the same operation lasts 50 times longer (a realistic possibility in some aluminum jobs), it might last for 25,000 parts (500 * 50). You would only need 4 tool changes (100,000 / 25,000). At 5 minutes per change, that’s only 20 minutes of downtime.
In this illustrative scenario, switching to PCD saved 980 minutes (more than 16 hours) of machine downtime purely from reduced tool changes. The actual savings depend heavily on the tool life difference achieved in your specific application, which can vary. It’s valuable to track your current tool life and changeover times to accurately estimate this potential saving. For high-volume producers, minimizing downtime is a critical factor in profitability, making PCD very attractive.
Real-World ROI: When PCD Saves You Money
So, when does the investment in PCD tooling show a clear Return on Investment (ROI)7? While every situation is unique, PCD typically delivers the fastest and most significant ROI under these conditions:
- High-Volume Production: The more parts you make, the more you benefit from PCD’s longevity and speed. The savings per part multiply across large production runs, quickly offsetting the initial tool cost. Automotive component manufacturing is a prime example.
- Machining Abrasive Aluminum Alloys: When cutting high-silicon aluminum, carbide wears out extremely quickly. PCD’s resistance to this wear means the tool life difference is maximized, leading to huge savings in replacements and downtime.
- Stable, Long-Running Jobs: Processes that run consistently over long periods allow the full lifespan advantage of PCD to be realized.
- When Cycle Time is Critical: If reducing the time it takes to make each part is a major goal (e.g., to meet demand or free up machine capacity), PCD’s speed advantage directly contributes to ROI.
Consider this illustrative comparison for machining a complex aluminum housing:
Factor | Carbide Scenario | PCD Scenario | Comments |
---|---|---|---|
Initial Tool Cost/Set | $150 | $750 | PCD is 5x more expensive upfront |
Tool Life (Parts/Set) | 1,000 | 60,000 | PCD lasts 60x longer in this example |
Cycle Time/Part | 3 minutes | 2 minutes | PCD is 33% faster |
Tool Changes (per 60k) | 60 | 1 | Significantly less downtime with PCD |
Est. Cost Per Part | Significantly Higher | Significantly Lower | Factoring tool cost, machine time, downtime |
Numbers are illustrative examples only.
In scenarios like this, even though the PCD tooling cost five times more initially, the drastically lower cost per part (due to longevity, speed, and reduced downtime) means the initial investment is paid back quickly, and significant savings accumulate over the production run.
Therefore, while not the answer for every single aluminum job (especially very short runs or non-abrasive alloys where carbide performs adequately), in many demanding, high-volume situations, the higher initial cost of PCD tooling is not just paid off – it becomes a key driver of profitability.
What Makes PCD Deliver Superior Finish and Tool Life on Aluminum?
We know PCD can be faster and often cheaper in the long run, but how does it actually improve the quality of the aluminum parts themselves and last so much longer?
Fundamentally, PCD tooling achieves a better surface finish on aluminum because its extremely sharp, low-friction diamond edge strongly resists material buildup, leading to cleaner cuts. This same exceptional hardness and resistance to wear are precisely why PCD tools maintain their cutting ability and last dramatically longer than alternatives like carbide.
Overcoming Built-Up Edge (BUE) Challenges
One of the biggest headaches when machining aluminum, especially softer grades, is something called Built-Up Edge (BUE). What is BUE?
Imagine tiny bits of the aluminum actually welding themselves onto the very tip of the cutting tool as it cuts. This clump of material forms the “built-up edge.” This is bad news because:
- It changes the tool’s shape, leading to inaccurate cuts.
- It creates a rougher surface finish on the part.
- Bits of the BUE can break off and get stuck on the finished surface.
- It increases cutting forces, which can cause vibration or even break the tool.
PCD tooling is naturally very good at preventing BUE for a few key reasons:
- Low Friction: Diamond has a very slippery surface. Think of how difficult it is for sticky material to cling to a very smooth, non-stick surface compared to a rougher one – PCD’s low friction works similarly against BUE.
- Maintained Sharpness: As we discussed, PCD stays sharp. A truly sharp edge cuts cleanly through the aluminum. A dulling edge (more common with carbide over time) tends to plow or push material, increasing the pressure and heat that encourage BUE formation.
- Thermal Conductivity: PCD’s ability to pull heat away (as mentioned in the speed section) also helps. Lower temperatures at the cutting point make it less likely for the aluminum to reach a state where it readily welds to the tool.
By minimizing BUE, PCD achieves a cleaner, more consistent cutting action, which is the foundation for a better surface finish and more reliable machining process.
Achieving High-Quality Surface Finishes (Ra Values)
The result of PCD’s sharp edge and resistance to BUE is often a significantly smoother surface finish on the machined aluminum part. Surface finish is commonly measured using Ra (Roughness average)8, where a lower Ra number means a smoother surface.
- PCD Capability: With the right cutting conditions and tool geometry, PCD tooling can often achieve excellent surface finishes on aluminum, frequently reaching Ra values below 0.8 micrometers (µm), and sometimes significantly lower, approaching mirror-like finishes in certain finishing operations.
- Comparison to Carbide: While carbide can produce good finishes initially, its tendency to wear and form BUE means the finish quality often degrades over the tool’s life. PCD maintains its ability to produce a high-quality finish for a much longer period.
- Impact: Achieving a fine finish directly from the machining operation can sometimes reduce or even eliminate the need for costly and time-consuming secondary operations like polishing or grinding. This is particularly valuable for components where appearance or surface integrity is critical, such as decorative automotive trim or precision aerospace parts.
Important Consideration: Achieving the best possible surface finish depends on many factors beyond just the tool material. Machine tool condition and rigidity, proper tool holding, vibration control, coolant application (if used), precise cutting parameters (speed, feed, depth of cut), and the specific edge preparation on the PCD tool all play crucial roles. The achievable Ra range can vary, so it’s wise to discuss specific finish requirements with your tooling supplier to select the optimal PCD geometry and cutting parameters.
Understanding the Exceptional Longevity Factor of PCD
We’ve mentioned PCD’s long life multiple times, but how long are we talking about? The “longevity factor” comes directly from PCD’s core properties:
- Extreme Hardness & Wear Resistance: This is the fundamental reason. Because diamond is so hard and resists abrasion so well (as explained under the speed section), the PCD cutting edge simply doesn’t wear down anywhere near as quickly as carbide when cutting aluminum, especially abrasive alloys.
- The Multiplier Effect: Compared to uncoated carbide tools in aluminum applications, it’s common for PCD tools to last 50 to 100 times longer, and in some optimal cases involving high-silicon aluminum or specific finishing operations, reports suggest multipliers can be even higher. This means a single PCD tool can potentially do the work of dozens or even hundreds of carbide inserts.
Crucial Caveat: This tool life multiplier is highly variable. It depends greatly on:
- The specific grade of aluminum being machined (especially silicon content).
- The cutting speed, feed rate, and depth of cut.
- The rigidity and condition of the machine tool.
- The specific design and quality of both the PCD tool and the carbide tool it’s being compared against.
Therefore, while the potential for vastly extended tool life is real, claiming a specific universal multiplier (like “100x”) isn’t accurate without context. It’s essential to evaluate PCD’s performance in your specific application to determine the actual life improvement you can expect.
Beyond just lasting longer (which impacts cost, as discussed previously), this exceptional longevity also contributes to process stability and consistency. Knowing that a tool will maintain its cutting performance accurately for tens of thousands of parts, rather than just hundreds, simplifies process control and improves part-to-part consistency.
When is PCD the Undeniable Choice Over Carbide for Aluminum?
We’ve explored the speed, cost, and quality benefits of PCD. But are there specific aluminum machining jobs where using PCD isn’t just an option, but clearly the best, or even necessary, choice compared to carbide?
Absolutely. PCD tooling emerges as the practically essential choice in several key scenarios: when machining highly abrasive high-silicon aluminum alloys that rapidly destroy carbide tools, within demanding high-volume automotive and aerospace applications requiring speed, longevity, and reliability, and whenever maintaining the utmost precision and dimensional consistency over long production runs is critical.
Excelling with Abrasive High-Silicon Aluminum Alloys
Not all aluminum is created equal when it comes to machining. Many aluminum alloys used in casting, particularly for automotive parts (like grades A356, A380, or similar), contain a significant amount of silicon. This makes them high-silicon aluminum alloys9. Why does this matter?
- The Abrasive Challenge: Silicon particles within the aluminum are extremely hard and abrasive – think of them like tiny, hard rocks embedded in the softer aluminum matrix. When a cutting tool hits these particles, it’s like cutting through sandpaper.
- Carbide’s Struggle: Standard carbide tools, even coated ones, wear down incredibly quickly when machining these high-silicon alloys. The sharp cutting edge is rapidly eroded by the abrasive silicon, leading to very short tool life, poor surface finish, and frequent machine stoppages for tool changes. Trying to machine these alloys efficiently with carbide in high volumes is often a frustrating and costly battle.
- PCD’s Solution: This is where PCD truly dominates. Because PCD is made from diamond particles, its extreme hardness allows it to cut through these abrasive silicon particles with significantly less wear. It maintains its sharp edge far, far longer than carbide in these conditions. The application of PCD in piston processing10, often involving such alloys, showcases this advantage.
Therefore, for high-volume machining of components like aluminum engine blocks, cylinder heads, pistons, or transmission parts made from high-silicon alloys, PCD tooling often transitions from being a “good idea” to being the only economically viable solution for achieving acceptable tool life and productivity.
Critical Applications in Automotive and Aerospace Industries
The automotive and aerospace industries rely heavily on aluminum for its lightweight properties, but they also have incredibly demanding manufacturing requirements. PCD tooling is frequently the preferred choice for meeting these challenges:
Automotive High-Volume Needs
The automotive industry produces millions of vehicles, requiring components to be manufactured quickly, reliably, and cost-effectively.
- Speed & Efficiency: PCD’s ability to run at very high cutting speeds is crucial for meeting the high production volumes needed for parts like engine components, transmission cases, suspension parts, and wheels. Faster cycle times mean higher output from expensive machine tools.
- Process Stability: Automated production lines rely on predictable processes. PCD’s exceptionally long tool life minimizes unexpected tool changes and downtime, leading to smoother, more reliable production flow compared to carbide, which would require constant monitoring and frequent replacement in high-volume scenarios.
Aerospace Precision and Material Challenges
Aerospace components often involve complex geometries, tight tolerances, and critical safety requirements. While volumes might be lower than automotive, the value and specifications per part are extremely high.
- Precision Machining: PCD’s ability to maintain a sharp edge and resist wear ensures consistent dimensional accuracy and excellent surface finishes, which are critical for parts like structural components (wing ribs, spars), landing gear elements, and engine mounts where surface integrity affects fatigue life.
- Machining Advanced Materials: Besides aluminum alloys, aerospace often uses other non-ferrous materials like composites (CFRP) where PCD also excels due to its wear resistance.
In both industries, the combination of speed, longevity, precision, and reliability offered by PCD makes it an indispensable tool for efficiently machining critical aluminum components.
Scenarios Demanding Maximum Precision and Consistency
Beyond specific industries or alloys, any aluminum machining application where holding tight tolerances and ensuring part-to-part consistency over long runs is paramount becomes a strong candidate for PCD tooling.
- The Wear Problem: As a carbide tool wears, its cutting edge geometry changes slightly. This wear inevitably causes the dimensions of the machined part to drift over time. To stay within specification, operators must frequently stop the machine to measure parts and make tool offsets (adjustments) or change the tool altogether.
- PCD’s Stability Advantage: Because PCD wears extremely slowly and predictably, it can hold tight dimensional tolerances for a vastly longer period. A PCD tool might machine thousands, or tens of thousands, of parts while staying within the required tolerance band, where a carbide tool might only manage hundreds before needing adjustment or replacement.
- Where it Matters Most: This stability is crucial for components with:
- Tight Fits: Parts that need to assemble precisely with others.
- Sealing Surfaces: Surfaces that require exceptional flatness and smoothness to prevent leaks (e.g., valve bodies, hydraulic components).
- Complex Geometries: Where dimensional accuracy across multiple features is critical.
So, whenever the cost or risk associated with parts going out of tolerance is high, or when minimizing in-process adjustments is key to efficiency, PCD’s ability to deliver consistent precision over extended periods makes it the superior and often necessary choice over carbide for aluminum machining.
Conclusion
In summary, while the initial investment for PCD tooling is higher than for traditional carbide, its unique properties offer compelling advantages for aluminum machining. The combination of extreme hardness and excellent thermal conductivity enables significantly faster cutting speeds, boosting productivity.
Furthermore, this resilience translates into dramatically longer tool life, which, when factored into the Total Cost of Ownership, often leads to lower overall costs per part, especially in high-volume production, by minimizing tool replacement costs and costly machine downtime. PCD also excels at delivering superior surface finishes and maintaining consistent dimensional accuracy over long runs, partly due to its resistance to Built-Up Edge.
Ultimately, PCD tooling proves to be not just beneficial but often the undeniable choice for challenging applications like machining abrasive high-silicon alloys, meeting the demanding requirements of the automotive and aerospace industries, and ensuring maximum precision and consistency where required. Evaluating your specific application’s volume, material properties, and quality needs against the potential ROI is key to determining if PCD tooling is the right investment to unlock faster, cheaper, and better aluminum machining results. Of course, achieving these benefits requires applying PCD tooling correctly in stable machining conditions suited to its specific material properties.
- Polycrystalline Diamond (PCD)1 – ZYDiamondTools comprehensive guide detailing Polycrystalline Diamond (PCD) cutting tools.
- Hardness2 – Wikipedia article explaining the concept of hardness in materials science, including various measurement scales.
- Thermal conductivity3 – Wikipedia article defining thermal conductivity and its significance in physics and engineering.
- Differences between PCD and carbide tools4 – ZYDiamondTools blog post detailing the comparison between PCD and Carbide cutting tools.
- PCD end mills for aluminum5 – ZYDiamondTools guide specifically covering PCD end mills for aluminum applications.
- Total Cost of Ownership (TCO)6 – ZYDiamondTools guide explaining the TCO concept and application for superhard tooling & abrasives.
- Return on Investment (ROI)7 – Investopedia article explaining the financial metric of Return on Investment and how it’s calculated.
- Ra (Roughness average)8 – Wikipedia section detailing various surface roughness parameters, including Ra.
- high-silicon aluminum alloys9 – ZYDiamondTools in-depth guide exploring the specific challenges of tool wear when machining high-silicon aluminum.
- Application of PCD in piston processing10 – ZYDiamondTools blog post detailing the use of PCD tools specifically for manufacturing automotive pistons.
ZY Superhard Tools Co., Ltd.
Do you have any needs for PCD tools or diamond grinding wheels? We can customize products to meet your specific requirements. If you have any ideas or requests, feel free to reach out—we’ll respond within 24 hours!
Do you have any needs for PCD & CBN tools or diamond grinding wheels? We can customize products to meet your specific requirements. If you have any ideas or requests, feel free to reach out—we’ll respond within 24 hours!
Do you have any needs for PCD & CBN tools or diamond grinding wheels? We can customize products to meet your specific requirements. If you have any ideas or requests, feel free to reach out—we’ll respond within 24 hours!
Post Categories
Product Categories
About Company
Related Posts
Which Turning Insert Shape Should You Choose?
Master turning insert selection. Our guide covers choosing the right shape for your job, decoding ISO codes, and selecting the
How Do You Solve Vibration, Chip Control, and Surface Finish Issues in PCD Grooving?
Solve common PCD grooving problems. This guide details how to fix vibration, improve chip evacuation, and achieve a flawless sidewall
Why Is Your Tooling Wearing Out Prematurely? A Machinist’s Guide to Key Causes & Proven Solutions
Facing premature tool wear? Learn the key causes like heat, vibration, & wrong parameters. Discover proven solutions from setup to
How Do You Select the Optimal PCD Tools for Scroll Compressor Machining?
Learn how to select the right PCD tools for scroll compressor machining. This guide covers the benefits over carbide, key
Subscribe
Simply enter your email below and click “Subscribe” to stay connected with everything new and exciting.