-
Whatsapp: +86 13526572721
-
Email: info@zydiamondtools.com
-
Address: AUX Industrial Park, Zhengzhou City, Henan Province, China
-
Whatsapp: +86 13526572721
-
Email: info@zydiamondtools.com
-
Address: AUX Industrial Park, Zhengzhou City, Henan Province, China
Choosing Between CBN and Diamond Grinding Wheels: Which One is Right for Your Needs?
- Grinding Wheels Knowledge, Knowledge
- -2025-04-02
- - byKevin Ray
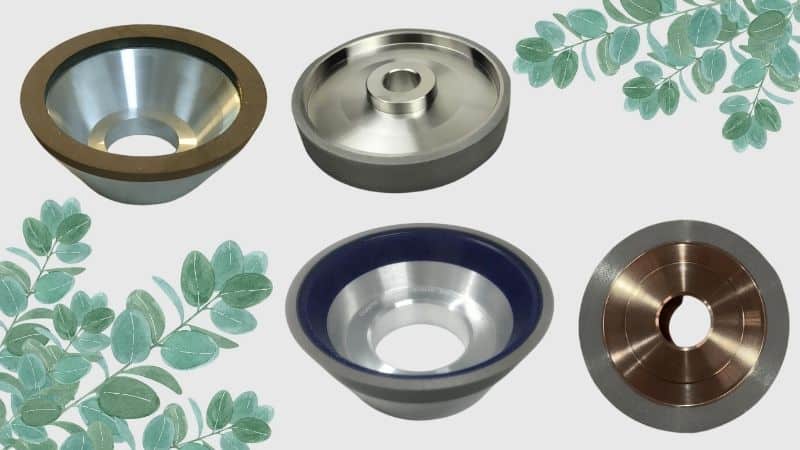
When faced with choosing between CBN and Diamond grinding wheels, how do you know which one is truly right for your specific needs?
Choosing the right superabrasive wheel, whether CBN (Cubic Boron Nitride) or Diamond, hinges primarily on the material you intend to grind. CBN excels with ferrous metals like steel, while Diamond is unmatched for non-ferrous metals and hard/brittle materials like carbide or ceramics. Factors like performance requirements, your grinding setup, and overall cost-effectiveness further refine the selection process.
Table of Contents
ToggleWhat Material Will You Be Grinding?
So, when you’re trying to pick the right grinding wheel, what’s the absolute first thing you need to figure out?
The most crucial factor in choosing between CBN (Cubic Boron Nitride) and Diamond grinding wheels is the type of material you need to grind. Essentially, CBN wheels are the go-to choice for ferrous metals, which include common materials like steel and cast iron. In contrast, Diamond wheels are best suited for grinding non-ferrous metals and very hard or brittle materials such as tungsten carbide, ceramics, and glass.
Identifying Ferrous Metals (Steels, Cast Iron): The Case for CBN
First things first, what are ferrous metals? Put simply, ferrous metals contain iron. Think of materials like:
- Hardened Steels: This includes tool steels (like High-Speed Steel or HSS used for drill bits), alloy steels, and stainless steels.
- Cast Iron: Often used for heavy machine bases or engine blocks.
Now, why is CBN the right choice for these iron-containing materials? It comes down to chemistry under heat. Grinding creates a lot of heat right where the wheel touches the metal. Diamond, although very hard, reacts chemically with iron at these high temperatures. This reaction actually causes the diamond abrasive to break down quickly, wearing out the wheel much faster than expected.
However, CBN is different. It’s also extremely hard (second only to diamond), but crucially, it does not react chemically with iron even when things get hot during grinding. This means a CBN wheel stays stable, keeps its cutting edge, and lasts much longer when grinding steels or cast iron compared to a diamond wheel. Using CBN ensures efficient grinding and prevents premature wheel failure when working with ferrous metals.
Identifying Non-Ferrous & Hard/Brittle Materials (Carbide, Ceramics, Glass): The Case for Diamond
On the other side, we have materials that don’t contain iron, or are extremely hard and brittle. These include:
- Non-Ferrous Metals: Such as aluminum or copper alloys (though grinding these is less common with superabrasives compared to harder materials).
- Cemented Carbides: Especially Tungsten Carbide, commonly used for cutting tools and wear parts due to its extreme hardness.
- Ceramics: Like alumina or zirconia, used in various industrial and technical applications.
- Glass: Including optical glass or industrial glass components.
- Composites: Certain types of fiber-reinforced materials.
For these types of materials, diamond is the champion. Why? Because diamond is the hardest known substance. This exceptional hardness allows it to effectively cut and shape these very tough or brittle materials where other abrasives would quickly dull or fail.
Importantly, since these materials generally lack iron, the chemical reaction problem that plagues diamond when grinding steel doesn’t happen here. Diamond can use its superior hardness to efficiently grind materials like tungsten carbide or ceramics without breaking down chemically. This results in precise shaping, good surface finishes, and reasonable wheel life for these challenging applications.
Why Material Type is the Most Critical Factor
So, why do we emphasize the material type above all else? It’s because the interaction between the grinding wheel abrasive and the workpiece material is the fundamental difference determining success or failure.
Think about it:
- Chemical Compatibility: As we saw, diamond reacts poorly with hot iron, while CBN does not. This chemical compatibility (or lack thereof) is a non-negotiable starting point. Using the wrong wheel type based on material can lead to disastrously short wheel life. For instance, trying to grind hardened steel with a diamond wheel optimized for carbide can result in the diamond layer being consumed far quicker than anticipated, wasting significant money.
- Efficiency and Effectiveness: Choosing the right wheel ensures the abrasive can actually do its job. Diamond’s supreme hardness is needed for materials like carbide. While CBN might scratch carbide, it won’t grind it nearly as effectively or efficiently as diamond, leading to long cycle times and potentially poor results.
- Preventing Waste: Selecting the correct wheel from the start, based primarily on the material, prevents wasting expensive grinding wheels, saves valuable time, and helps ensure the quality of the finished part.
Ultimately, considering the material first sets the foundation for your choice. Why worry about the subtle differences in potential grinding speed or surface finish if the wheel you choose fundamentally isn’t suited for the material you need to shape? Getting the material match right is the essential first step towards successful grinding with CBN or diamond wheels.
How Do CBN and Diamond Wheels Perform Differently?
Okay, you know which wheel type generally matches your material. But beyond that, how do CBN and diamond wheels actually compare when it comes to getting the job done?
Diamond and CBN wheels show distinct performance differences. Diamond is the hardest material known, offering excellent wear resistance, particularly on non-ferrous and hard/brittle materials. CBN, while slightly less hard on paper, possesses superior thermal stability, making it ideal for handling the intense heat generated when grinding ferrous metals like steel. These core differences also influence potential surface finish quality, grinding speed, and overall efficiency depending on the specific grinding task.
Comparing Hardness and Wear Resistance
Hardness simply means how well a material resists scratching or denting. Wear resistance is how long it lasts before wearing down during use. These two properties are closely related.
- Diamond: As the undisputed champion, diamond is the hardest natural material on Earth. On scientific scales like the Knoop hardness test, it scores extremely high (often cited around 7000-10000 HK), topping the Mohs hardness scale1 at 10. This incredible hardness translates directly to excellent wear resistance when grinding the right materials – namely, very hard substances like tungsten carbide, ceramics, or glass. It holds its sharp cutting edges longer against these demanding materials.
- CBN (Cubic Boron Nitride): CBN is the second hardest material known, significantly harder than conventional abrasives. Its Knoop hardness typically falls in the range of 4500-5000 HK. While technically softer than diamond, it’s still exceptionally hard. Critically, its superior chemical stability when grinding steel means it doesn’t degrade like diamond does in that application. Therefore, CBN offers outstanding wear resistance and long life when used correctly on ferrous metals.
It’s worth remembering that exact hardness values can vary slightly based on the specific quality and type of abrasive crystal used. You might want to confirm specific performance expectations related to wear with your wheel supplier.
Understanding Heat Tolerance and Thermal Stability
Grinding generates significant heat right at the point of contact. How well the wheel handles this heat is crucial.
- CBN’s Strength: Thermal Stability: This is where CBN truly shines, especially when grinding steel. CBN maintains its hardness and structural integrity at very high temperatures (remaining stable well above 1200°C or ~2200°F). Crucially, it doesn’t chemically react with iron even under this intense heat. This thermal stability2 allows CBN wheels to be used aggressively on steels without rapid breakdown.
- Diamond’s Limitation (with Steel): While diamond itself has a high melting point, its practical heat tolerance is limited when grinding ferrous metals. At temperatures typically starting around 700-800°C (~1300-1500°F), the carbon in the diamond begins to react with the iron in steel, causing the diamond to degrade and lose its effectiveness quickly. However, when grinding materials that do not contain iron, such as non-ferrous metals, carbides, or ceramics, this reaction isn’t an issue, and diamond performs well.
The Role of Thermal Conductivity
Both diamond and CBN are excellent thermal conductors. This means they are very good at transferring heat away from the grinding zone and into the body of the wheel or coolant.
- Benefit: This helps prevent the workpiece from overheating, which could cause burns, warping, or undesirable changes in the material’s properties (like softening hardened steel).
- Comparison: Diamond generally has higher thermal conductivity3 than CBN. This is particularly advantageous when grinding heat-sensitive materials where minimizing thermal damage to the part is absolutely critical.
Assessing Impact on Surface Finish Quality
Surface finish refers to the smoothness and texture of the ground surface. It’s often measured in units like Ra (Roughness average)4.
- Diamond’s Potential: Diamond wheels, particularly those with finer abrasive grits and specific bond systems, are often capable of producing exceptionally smooth, almost mirror-like finishes. They excel at creating sharp edges and fine details, especially on very hard materials like ceramics or tungsten carbide inserts used in cutting tools.
- CBN’s Capability: CBN wheels can also achieve very good, high-quality surface finishes on hardened steels and other ferrous alloys. Modern CBN wheels with optimized grit sizes and bonds deliver excellent results for many precision applications.
- Key Influences: It’s vital to understand that the final surface finish depends heavily on more than just the abrasive type. Factors include:
- Grit Size: Finer grits generally produce smoother finishes (for both CBN and diamond).
- Bond Type: The material holding the abrasive grains affects how the wheel cuts.
- Machine Condition: A rigid, precise machine is essential for fine finishes.
- Grinding Parameters: Speed, feed rate, and depth of cut all play a significant role.
Because achievable surface finish depends greatly on the specific wheel formulation and application parameters, it’s advisable to discuss your exact finish requirements (e.g., target Ra value) with the grinding wheel manufacturer or supplier. They can recommend the best wheel specification for your needs.
Evaluating Grinding Speed and Efficiency Potential
Efficiency in grinding often means removing material quickly and effectively. This is often quantified as the Material Removal Rate (MRR).
- Superabrasive Advantage: Both CBN and diamond are considered “superabrasives” because they allow for significantly higher grinding speeds and material removal rates (MRR) compared to conventional abrasives like aluminum oxide or silicon carbide. This means you can often grind parts faster.
- Diamond’s Edge (on appropriate materials): Due to its extreme hardness, diamond can be very efficient at removing material when grinding things like tungsten carbide or ceramics. It allows for aggressive cutting under the right conditions.
- CBN’s Power (on ferrous metals): CBN’s thermal stability allows it to withstand the high temperatures generated during high-speed grinding of hardened steels without breaking down. This enables high MRR and efficient production cycles in applications like grinding engine components or tool steels.
- It’s All About the Match: There isn’t one simple answer to “which is faster?” The true efficiency depends entirely on matching the wheel correctly to the material, using appropriate machine settings (speed, feed, depth of cut), and the specific operation. Using the wrong wheel type will always lead to inefficiency – either through extremely slow cutting (like CBN on carbide) or rapid wheel wear (like diamond on steel). Proper application is key to unlocking the speed and efficiency potential of both CBN and diamond wheels.
Does Your Grinding Setup Influence the Choice?
We’ve covered materials and how the wheels perform, but does your actual grinding machine or the way you grind affect whether you should choose CBN or diamond?
Yes, your specific grinding setup definitely plays a role in selecting the best wheel. Important factors like the operating speed of your grinder – whether it’s high-speed or low-speed – and if you’re grinding wet (using coolant) or dry significantly influence how CBN or diamond wheels perform, how long they last, and the final quality of your workpiece.
High-Speed vs. Low-Speed Grinding Considerations
Grinding machines operate at different speeds, often measured in Surface Feet Per Minute (SFPM) or Meters per Second (m/s), which tells you how fast the wheel’s surface moves past the workpiece.
High-Speed Grinding (Production Machines)
- Characteristics: These are typical industrial grinders running at high rotational speeds (RPM), resulting in high surface speeds. Think of production CNC grinders used for making engine parts or cutting tools.
- Heat Generation: High speeds naturally generate more friction and heat at the grinding point.
- Wheel Choice Impact:
- For Steel (Ferrous): The intense heat reinforces why CBN is essential. Its excellent thermal stability allows it to handle high-speed steel grinding without breaking down chemically. Diamond’s tendency to react with hot iron is much more problematic at these speeds.
- For Carbide/Ceramics (Non-Ferrous): Diamond wheels often excel at high speeds for these materials, leveraging their hardness for efficient material removal.
Low-Speed Grinding (Bench Grinders, Sharpening Systems)
- Characteristics: This includes common bench grinders or specialized low-speed wet sharpeners (like Tormek systems) operating at much lower RPMs and surface speeds.
- Heat Generation: Less heat is typically generated compared to high-speed grinding.
- Wheel Choice Impact:
- For Steel (Ferrous): While less heat is generated, CBN remains the safest and usually recommended choice due to its inherent chemical stability with iron. Some users might experiment with diamond on very low-speed wet systems because the reaction may be less severe, but CBN avoids the risk altogether.
- For Carbide/Ceramics (Non-Ferrous): Diamond is still the primary choice due to its hardness, even at lower speeds.
- Other Factors: At low speeds, factors like the specific grit sizes available or wheel construction designed for that type of machine might also influence the choice.
Important Speed Note: Always check your grinding machine’s specifications and the grinding wheel manufacturer’s recommended operating speed range (often marked on the wheel or in its documentation). Using a wheel at speeds significantly higher or lower than recommended can be dangerous and lead to poor performance or wheel damage. Confirm these details with your supplier if unsure.
Wet vs. Dry Grinding Factors
Another key setup difference is whether you use a coolant fluid during grinding.
Wet Grinding (Using Coolant)
- Benefits:
- Temperature Control: Coolant effectively removes heat from the grinding zone, significantly reducing the risk of burning the workpiece or damaging the wheel from overheating.
- Cleaning Action: It flushes away grinding debris (called swarf), preventing the wheel surface from getting clogged (“loading”) and ensuring clean cutting.
- Improved Finish & Life: Often leads to better surface finishes and can help extend the grinding wheel’s lifespan.
- Wheel Compatibility: Most CBN and Diamond wheels with robust bond systems (like vitrified, metal, or resin bonds used in production) are designed primarily for wet grinding. This is the standard practice for precision or high-volume work.
- Coolant Choice: Generally, standard grinding coolants suitable for superabrasives work well. While very rare with modern wheels, it’s worth noting that some older or specialized CBN types theoretically could be sensitive to highly alkaline coolants over long exposure. It’s always wise to use coolants recommended by the wheel or machine manufacturer and confirm compatibility if using non-standard fluids.
Dry Grinding (No Coolant)
- Challenges:
- Heat Buildup: Without coolant, heat accumulates quickly, increasing the risk of thermal damage to the part (like softening or warping) and potentially shortening wheel life, especially with heavy grinding.
- Wheel Loading: Swarf isn’t flushed away and can clog the wheel’s surface, reducing cutting efficiency.
- Wheel Choice & Use:
- Dry grinding is possible but often requires wheels specifically designed for it, perhaps with more porous bond structures or specialized abrasive coatings (like electroplated wheels for certain tasks).
- CBN is often used for dry grinding steel on bench grinders for tool sharpening, largely thanks to its heat tolerance. However, lighter pressure and intermittent grinding might be needed.
- Diamond can be used dry for some light applications on non-ferrous materials, but heat buildup is a major concern, especially with finer grits or heavier stock removal.
- General Preference: For most precision grinding or when removing significant amounts of material, wet grinding is strongly preferred for both CBN and Diamond wheels whenever the machine setup allows. It generally leads to better results, longer wheel life, and greater process stability.
What is the Difference in Cost and Overall Value?
So, apart from how they work, what about the price tag? How do CBN and diamond wheels actually compare when you consider the cost and the value you get?
Generally, CBN wheels often have a higher initial purchase price compared to many standard diamond wheels, but it’s crucial to know that prices vary widely. However, the real story isn’t just the upfront cost; it’s about the total value over time. Both CBN and diamond wheels last significantly longer and need much less maintenance (like dressing) than traditional grinding wheels. This leads to a lower cost for each part you grind, less machine downtime, and better long-term savings when you use the right wheel for the right job.
Initial Wheel Price Comparison
Let’s talk about the price you pay when you first buy the wheel.
- General Trend: Often, you’ll find that CBN wheels tend to cost more initially than many diamond wheels of a similar size and type. The process to create the synthetic CBN abrasive material can sometimes be more complex or costly.
- But Wait – It Varies A Lot! This is really important: you cannot assume CBN is always more expensive. The price of both CBN and diamond wheels can change dramatically based on many factors:
- Wheel Size and Shape: Bigger or more complex wheels naturally cost more.
- Abrasive Concentration: Wheels with a higher concentration (more diamond or CBN grit packed in) are typically pricier.
- Bond Type: The material holding the abrasive (like Resin, Vitrified, Metal, or Electroplated) affects the cost. Vitrified and metal bonds are often more expensive but can last longer.
- Quality and Manufacturer: Different brands and quality levels come with different price points.
- Customization: Wheels made specially for a unique job will cost more than standard off-the-shelf wheels.
- The Bottom Line on Price: Comparing prices directly can be tricky. Can you fairly compare a small, simple diamond wheel for a hobbyist bench grinder to a large, complex CBN wheel designed for a high-production automotive factory? Probably not. The only reliable way to know the initial cost is to get specific quotes from grinding wheel suppliers based on the exact wheel specifications your application requires.
Lifespan, Maintenance, and Long-Term Economics
Okay, so the initial price is just one part of the puzzle. To understand the true value, we need to look at the bigger picture over the life of the wheel.
Astonishingly Long Lifespan
- Compared to Old-School Wheels: Here’s where CBN and diamond really shine. Compared to conventional abrasive wheels (like the brownish aluminum oxide ones you might see), both CBN and diamond wheels can last hundreds or even thousands of times longer when used correctly.
- CBN vs. Diamond Lifespan: When you match the wheel to the material properly (CBN for steel, diamond for carbide/ceramics), both offer excellent, long service life. Of course, using the wrong one drastically cuts this short – trying to grind steel with a diamond wheel will wear it out incredibly fast, making it poor value despite its hardness.
Minimal Maintenance Needs
- No More Constant Dressing: Traditional grinding wheels wear down relatively quickly and lose their shape or get clogged. They need frequent “dressing” (cleaning the surface and restoring the shape) and “truing” (making sure the wheel runs perfectly round).
- Superabrasive Advantage: CBN and diamond wheels, because they are so hard and wear so slowly, hold their shape remarkably well. They generally do not require the frequent dressing and truing needed for conventional wheels.
- Saving Time and Money: This translates directly into savings:
- Less Downtime: The grinding machine spends more time actually grinding parts, not being stopped for wheel maintenance.
- Reduced Labor: Operators don’t need to constantly monitor and dress the wheel.
- No Dressing Tool Costs: You save money on the tools used for dressing conventional wheels.
The Real Value: Lower Cost-Per-Part
- Thinking Beyond the Price Tag: Smart businesses often look at the cost-per-part5 to judge value. This means figuring out how much it costs to grind each individual piece, often considered as part of the Total Cost of Ownership (TCO).
- Calculating Value (Simplified Idea): You’d roughly consider: (Initial Wheel Cost + Cost of Machine Time Used + Cost of Any Downtime) ÷ (Total Number of Good Parts Ground with One Wheel).
- Why CBN/Diamond Win: Even though a CBN or diamond wheel might cost significantly more upfront, its incredibly long life and drastically reduced maintenance downtime mean it can grind vastly more parts. For example, maybe a $40 conventional wheel grinds 150 parts effectively before needing significant attention, while a $600 CBN wheel grinds 75,000 similar steel parts reliably. When you do the math, the cost associated with each part ground using the CBN wheel is much, much lower.
- Overall Economics: Focusing only on the initial wheel price can be misleading. The true economic advantage of using the correct CBN or diamond wheel comes from dramatically increased productivity, reduced labor, less scrap, consistent part quality, and ultimately, a lower total cost to produce each finished part.
Making the Choice: Key Factors Summarized
After exploring all these details, let’s quickly summarize the key points to help you make your final choice.
Making the final decision between CBN and diamond grinding wheels boils down to carefully matching the wheel’s strengths to your specific job requirements. Remember, the most critical factor is always the material you’ll be grinding (with ferrous metals pointing towards CBN, and non-ferrous or hard/brittle materials favoring diamond). Following that, weigh the performance needs, your grinding machine’s capabilities (like speed and coolant use), and the overall long-term value to select the most effective and economical wheel.
Quick Decision Checklist: CBN or Diamond?
Here’s a quick cheat sheet summarizing the main points to guide your initial direction:
- Choose CBN (Cubic Boron Nitride) if:
- Your primary task involves grinding Ferrous Metals (this includes most steels like tool steel, stainless steel, hardened steel, and also cast iron).
- You need excellent Thermal Stability, especially for high-speed grinding operations on steel where heat buildup is significant.
- Avoiding a chemical reaction between the abrasive and iron workpiece at high temperatures is essential for wheel life.
- Choose Diamond if:
- You are mainly grinding Non-Ferrous Metals (like aluminum alloys, though less common for diamond), Cemented Carbides (like tungsten carbide), Ceramics, Glass, composites, or other very hard and/or brittle non-metallic materials.
- You need the absolute highest level of Hardness to effectively cut the extremely hard material.
- Achieving the potentially finest Surface Finish or sharpest edges on these specific hard materials is a top priority.
This checklist covers the fundamental starting point based on material, which is the most important distinction.
Final Questions to Ensure the Right Fit
Before you place that order, take a moment to ask yourself these final questions to confirm you’ve considered all the angles for your specific situation:
- Material Certainty: Am I absolutely positive about the exact type of material I need to grind? Is it definitely ferrous, or is it non-ferrous, carbide, ceramic, or something else? (Getting this wrong is the most common mistake!)
- Key Performance Goal: For this particular job, what is my main performance priority? Is it achieving the smoothest possible surface finish? Removing material as fast as possible? Getting the longest possible wheel life? How do the performance characteristics we discussed for CBN and diamond align with this specific goal on my material?
- Setup Suitability: Does my grinding machine operate at high speed or low speed? Does this favor CBN’s heat handling (for steel) or diamond’s hardness (for carbide)? Will I be grinding wet or dry? Is the wheel I’m considering designed for that method?
- True Value Check: Am I looking beyond the initial sticker price? Have I thought about the long-term savings from extended wheel life and minimal maintenance (dressing/truing)? Does the potential lower cost-per-part justify the upfront investment in a superabrasive wheel?
- Expert Consultation: Have I talked about my specific application – the material, the machine, my desired outcome, and budget – with a knowledgeable grinding wheel supplier or manufacturer? Getting their expert recommendation can prevent costly errors and ensure you get a wheel truly optimized for your needs.
By running through this checklist and considering these final questions, you’ll be in a much stronger position to choose the grinding wheel – CBN or diamond – that is truly right for your needs.
Conclusion
Selecting the correct grinding wheel, whether it’s CBN or Diamond, is a critical step towards achieving efficient, high-quality, and cost-effective grinding results. By systematically evaluating the material you need to grind, the specific performance characteristics required, the capabilities of your grinding setup, and the overall long-term value proposition, you can navigate the choices effectively. Remember that the fundamental difference lies in material compatibility – CBN for ferrous metals and Diamond for non-ferrous/hard-brittle materials. Building upon that core principle and considering the other factors discussed will lead you to the optimal solution. When complex situations arise or doubts remain, consulting with experienced grinding wheel suppliers or application engineers is always a valuable step to ensure you make the most informed decision for your operations.
References
- Mohs hardness scale1 – U.S. National Park Service explanation of the Mohs Hardness Scale.
- thermal stability2 – ScienceDirect topic page defining thermal stability in materials science.
- thermal conductivity3 – Britannica explanation of thermal conductivity.
- Ra (Roughness average)4 – Machining Doctor resource explaining surface finish measurements including Ra.
- cost-per-part5 – ZYDiamondTools guide explaining the TCO concept and application for superhard tooling & abrasives.
ZY Superhard Tools Co., Ltd.
Do you have any needs for PCD tools or diamond grinding wheels? We can customize products to meet your specific requirements. If you have any ideas or requests, feel free to reach out—we’ll respond within 24 hours!
Do you have any needs for PCD & CBN tools or diamond grinding wheels? We can customize products to meet your specific requirements. If you have any ideas or requests, feel free to reach out—we’ll respond within 24 hours!
Do you have any needs for PCD & CBN tools or diamond grinding wheels? We can customize products to meet your specific requirements. If you have any ideas or requests, feel free to reach out—we’ll respond within 24 hours!
Post Categories
Product Categories
About Company
Related Posts
Which Turning Insert Shape Should You Choose?
Master turning insert selection. Our guide covers choosing the right shape for your job, decoding ISO codes, and selecting the
How Do You Solve Vibration, Chip Control, and Surface Finish Issues in PCD Grooving?
Solve common PCD grooving problems. This guide details how to fix vibration, improve chip evacuation, and achieve a flawless sidewall
Why Is Your Tooling Wearing Out Prematurely? A Machinist’s Guide to Key Causes & Proven Solutions
Facing premature tool wear? Learn the key causes like heat, vibration, & wrong parameters. Discover proven solutions from setup to
How Do You Select the Optimal PCD Tools for Scroll Compressor Machining?
Learn how to select the right PCD tools for scroll compressor machining. This guide covers the benefits over carbide, key
Subscribe
Simply enter your email below and click “Subscribe” to stay connected with everything new and exciting.