-
Whatsapp: +86 13526572721
-
Email: info@zydiamondtools.com
-
Address: AUX Industrial Park, Zhengzhou City, Henan Province, China
-
Whatsapp: +86 13526572721
-
Email: info@zydiamondtools.com
-
Address: AUX Industrial Park, Zhengzhou City, Henan Province, China
Why Choose PCD Tools for Graphite Machining and How to Select the Right One?
- Industry Knowledge, PCD & CBN Tools Knowledge
- -2023-04-03
- - byKevin Ray
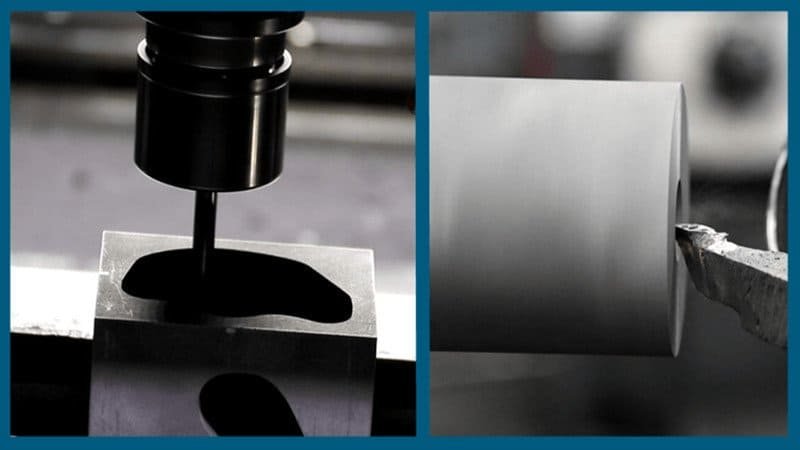
So, you’re working with graphite and wondering why Polycrystalline Diamond (PCD) tools1 are so often recommended, and how you pick the perfect one for your job?
PCD tools are essential for efficiently machining graphite due to its highly abrasive nature which rapidly wears down conventional tools; selecting the right PCD tool involves matching the specific PCD grade, tool geometry, and edge preparation to the type of graphite, the machining operation, and the desired quality outcomes to maximize performance and tool life.
Table of Contents
ToggleWhat Makes Graphite Challenging to Machine?
So, why exactly can machining graphite feel like such an uphill battle?
Graphite presents unique machining difficulties primarily due to its highly abrasive nature combined with its inherent brittleness. This combination leads to extremely rapid tool wear and potential workpiece damage if not approached with the right tools and techniques, significantly impacting production efficiency and costs.
Understanding Graphite Unique Properties (High Abrasiveness Despite Softness)
Graphite often feels soft to the touch, much like the lead in a pencil. In fact, its hardness on the Mohs scale2 is typically only 1-2. However, this softness is deceptive when it comes to machining. Why is that?
Firstly, natural graphite frequently contains impurities like silica (quartz)3 and other abrasive minerals. Even small amounts of these harder particles embedded within the softer graphite matrix act like tiny bits of sandpaper against a cutting tool edge.
Secondly, even pure, high-quality synthetic graphite has a crystalline structure that, at a microscopic level, can be quite abrasive to tool materials. While the overall material is soft and lubricious, the individual crystal structures present a challenging surface to the cutting edge, especially at the high speeds and pressures involved in machining.
Imagine trying to cut a stack of paper with scissors; while each sheet is flimsy, cutting through the whole stack requires effort and eventually dulls the blades. Similarly, the microstructure of graphite contributes significantly to wear, even though the bulk material isn’t hard like steel. Consequently, materials designed to cut metals, even hard ones, can wear down surprisingly quickly when machining graphite.
Common Machining Issues (Rapid Tool Wear, Brittleness, Dust Control)
These unique properties lead directly to several common headaches in the workshop:
- Rapid Tool Wear: This is perhaps the most significant challenge. The abrasive nature of graphite causes cutting edges, even those made of tough materials like tungsten carbide, to dull very quickly through micro-abrasion4. It’s not uncommon for standard carbide tools to last only a short time, sometimes failing before even completing a single part, especially in demanding applications. This rapid wear makes maintaining dimensional accuracy and surface finish incredibly difficult without specialized tooling.
- Brittleness and Chipping: While graphite has good toughness in some respects, it’s also brittle, much like glass or ceramic. During machining, if the cutting forces are too high, the tool edge is dull, or the workpiece isn’t supported correctly, the graphite can easily chip or fracture. This is particularly problematic when creating fine details, sharp corners, or thin walls, often leading to scrapped parts. Think about how easily pencil lead snaps under pressure – graphite behaves similarly when machined improperly.
- Fine, Conductive Dust: Machining graphite produces a large amount of fine, black dust. Unlike many metal chips, this dust is pervasive and gets everywhere. Furthermore, graphite dust is electrically conductive. This poses a risk to machine tool electronics, potentially causing short circuits if it infiltrates control panels or sensitive components. Effective dust extraction and collection systems are therefore not just recommended, but essential for maintaining equipment reliability and a clean working environment.
Impact on Production Costs and Surface Finish Quality
These machining challenges directly translate into tangible impacts on the bottom line and the quality of the final product:
- Increased Production Costs:
- Tooling Expenses: Rapid tool wear means buying cutting tools far more frequently, significantly increasing tooling costs.
- Downtime: Constantly changing worn tools leads to machine downtime, reducing overall productivity.
- Scrap Rate: Parts damaged by chipping or fracturing due to brittleness increase the scrap rate, wasting material and machining time.
- Cycle Time: Often, to minimize wear or prevent chipping with inadequate tools, machinists must reduce cutting speeds and feeds, leading to longer cycle times per part.
- Maintenance: The need for robust dust collection adds equipment and maintenance costs.
- Compromised Surface Finish and Accuracy:
- A dull or worn cutting tool cannot produce a clean, smooth surface finish. It tends to rub or burnish the material rather than shearing it cleanly, leading to poor surface quality (Ra).
- Tool wear also makes it difficult to maintain tight dimensional tolerances, which is critical for applications like EDM electrodes where precision directly impacts the final molded part.
- Chipping or edge breakouts result in unacceptable part defects.
Addressing these challenges effectively is crucial for any operation looking to machine graphite efficiently and profitably. It necessitates moving beyond standard tooling and adopting solutions specifically designed for graphite’s unique and demanding characteristics.This is precisely where advanced tool materials like Polycrystalline Diamond (PCD) come into play, offering the necessary properties to handle graphite effectively.
Which Types of PCD Tools Are Best Suited for Graphite Processing?
Given graphite’s tricky nature, what kinds of Polycrystalline Diamond (PCD) tools are actually used to cut it effectively?
A variety of PCD cutting tools are specifically designed or well-suited for graphite machining, including milling cutters (like end mills, face mills, and ball nose mills), drilling and holemaking tools (drills, reamers, boring bars), turning tools and inserts for lathes, and specialized tools for tasks like engraving or creating custom profiles.
PCD Milling Cutters (End Mills, Face Mills, Ball Nose)
Milling involves using rotating cutters to remove material and shape a workpiece. Because graphite wears tools down so quickly, using PCD milling cutters is essential for efficiency and tool life. Common types include:
- PCD End Mills: These are versatile cutters used for making slots, cutting profiles on the sides of parts (profiling), creating pockets, and general material removal. They have cutting edges on the end face and along the sides. Using PCD tips ensures the edges stay sharp much longer when cutting abrasive graphite, maintaining accuracy. They come in various styles, like square-end for sharp corners or corner-radius for stronger corners and smoother transitions.
- PCD Face Mills: Typically larger in diameter, face mills are designed to machine large, flat surfaces quickly and efficiently. They usually feature multiple PCD inserts or brazed tips arranged around the cutter body. This allows for higher material removal rates when flattening graphite blocks or creating large, flat areas on molds or electrodes.
- PCD Ball Nose Mills: These cutters have a rounded cutting end, resembling a ballpoint pen tip. They are crucial for machining curved surfaces, complex 3D contours, and smooth blends, which are often required for graphite molds used in applications like glass forming or metal casting. The PCD edge ensures the complex shape is maintained accurately over long cutting times.
PCD Drilling and Holemaking Tools (Drills, Reamers, Boring Tools)
Creating accurate holes in graphite also demands the wear resistance of PCD. Key tools include:
- PCD Drills: Used to create the initial hole in solid graphite. Standard high-speed steel or even carbide drills dull almost immediately. Drills tipped with PCD maintain their cutting edge geometry and diameter far longer, resulting in more consistent and accurate holes before needing replacement. Common types include PCD-tipped twist drills.
- PCD Reamers: After a hole is drilled, a reamer is used to slightly enlarge it to a very precise diameter and achieve a very smooth internal surface finish. PCD reamers are essential when tight tolerances are required for graphite components, ensuring the hole size remains consistent over many parts due to the PCD’s wear resistance.
- PCD Boring Tools: Boring tools are used to enlarge existing holes (often larger ones than reaming) or to create specific internal features or profiles within a hole. These can be single-point cutters with a PCD tip adjusted to the desired diameter. They offer high precision for final hole sizing and finishing in graphite.
PCD Turning Tools and Inserts
Turning operations, typically performed on a lathe where the graphite workpiece rotates, also benefit greatly from PCD tooling:
- PCD Inserts: These are small, indexable (replaceable) cutting tips with PCD edges. They are mounted in a standard tool holder on the lathe. PCD inserts are widely used for turning outside diameters, facing off ends, boring inside diameters, and cutting grooves in graphite parts. Their replaceability makes them cost-effective for high-volume production, as a worn edge can be quickly indexed or the insert replaced without changing the entire tool holder.
- Brazed PCD Turning Tools: In this type, the PCD cutting tip is permanently bonded (brazed) onto a steel or carbide shank (the body of the tool). These tools can sometimes offer higher rigidity or allow for more complex custom cutting edge shapes compared to standard inserts. Depending on the design, they might be reground multiple times, though checking with the manufacturer about regrinding possibilities is recommended.
Specialized PCD Tools (Engraving, Grooving, Custom Profiles)
Sometimes, standard tool shapes aren’t sufficient for specific graphite machining tasks. Specialized PCD tools fill these needs:
- PCD Engraving Tools: These tools feature very fine, sharp points designed for creating precise patterns, logos, text, or identification marks directly onto graphite surfaces. The extreme hardness of PCD ensures the fine tip doesn’t wear down quickly, maintaining detail clarity.
- PCD Grooving Tools: Designed specifically to plunge into the material and cut channels or grooves of a precise width and depth. PCD is essential here to maintain the groove dimensions accurately over the tool’s life when machining abrasive graphite.
- Custom Profile PCD Tools: For complex shapes or features needed repeatedly on graphite parts (like intricate electrode details), manufacturers can create custom PCD tools. These tools have the desired profile ground onto the PCD edge, allowing the feature to be machined in a single pass or fewer operations. This greatly improves efficiency and ensures consistency for parts with unique geometric requirements. Discussing specific needs with a tool supplier is key for developing these custom solutions.
How Do PCD Tools Compare to Alternatives?
Okay, we know PCD tools work for graphite, but how do they stack up against other options like regular carbide or diamond-coated tools?
Compared to cemented carbide, PCD tools offer drastically longer tool life and allow much higher machining speeds for graphite, making them far more cost-effective despite a higher initial price. When compared to CVD diamond coated tools, PCD provides a thicker diamond section offering robustness, while CVD coating can achieve sharper edges on more complex or smaller geometries.
PCD vs. Cemented Carbide5 for Graphite Machining
Let’s first look at how PCD compares to the most common cutting tool material, cemented carbide (often just called carbide). Carbide tools are made from hard tungsten carbide particles glued together with a binder, usually cobalt. They are tough and relatively inexpensive.
However, when it comes to machining abrasive graphite:
- Wear Resistance: This is the biggest difference. Standard carbide tools wear down incredibly quickly when cutting graphite. The abrasive particles just grind away the cutting edge. PCD, being nearly as hard as natural diamond, resists this abrasive wear far better. You can expect PCD tools to last significantly longer – potentially many times longer than carbide in the same graphite application, though the exact improvement varies greatly depending on conditions.
- Speed and Feed: Because PCD holds its edge longer and handles heat better, you can run machines much faster. Higher cutting speeds and feed rates are possible with PCD compared to the slow speeds needed to preserve a carbide edge even slightly. This directly translates to shorter cycle times and more parts produced per hour.
- Initial Cost: Carbide tools are cheap to buy initially. PCD tools cost considerably more upfront.
- Overall Economics: Despite the higher purchase price, the dramatically longer life and faster machining speeds mean PCD tools almost always result in a lower overall cost per part when machining graphite in any significant quantity. The savings from fewer tool changes, less downtime, and faster production quickly outweigh the initial investment. For serious graphite production, carbide is generally not a viable option due to performance limitations.
PCD vs. CVD Diamond Coated Tools6: Key Differences and Use Cases
Another important alternative is the CVD diamond coated tool. Here, instead of a solid PCD tip, a very thin layer (measured in micrometers, or µm) of pure diamond is grown directly onto a carbide tool’s surface using a process called Chemical Vapor Deposition (CVD)7. How do they compare?
Feature | PCD (Polycrystalline Diamond) | CVD Diamond Coated |
---|---|---|
Structure | Solid composite of diamond particles & binder | Thin diamond coating on carbide substrate |
Diamond Thickness | Relatively thick (e.g., 0.5 mm+) | Very thin (e.g., 5-25 µm) |
Hardness | Extremely hard | Pure diamond coating is extremely hard |
Robustness | Generally more robust due to thicker structure | Coating thinness can make it prone to chipping |
Edge Sharpness | Very sharp, achievable through grinding | Can achieve extremely sharp edges initially |
Geometry Limits | Best for inserts, simpler brazed geometries | Excellent for complex shapes, very small tools |
Regrinding | Often possible (check with supplier) | Generally not possible |
Key Differences Explained:
- The main difference lies in the structure. PCD tools have a substantial diamond layer, offering good toughness and resistance to chipping. CVD coatings are pure diamond, technically harder, but very thin, making them potentially more fragile under high impact or if the coating bond fails.
- CVD coating can perfectly conform to intricate shapes and very small tool bodies (like micro-drills under 3mm diameter), where manufacturing or brazing a solid PCD tip might be impractical or too costly.
- PCD tools, especially brazed types, can often be resharpened or reground (though verification with the tool supplier is essential), potentially extending their usable life further. CVD coatings typically cannot be reground once worn.
Typical Use Cases:
- Choose PCD for Graphite When: You need robustness for general-purpose milling, turning, or drilling of graphite parts, especially for standard-to-larger tool sizes (e.g., >3-6mm diameter). Its thicker diamond layer provides excellent resistance to the abrasiveness of graphite, making it suitable for both roughing and finishing where extreme geometric complexity isn’t the primary driver. It’s often the preferred choice for applications where potential micro-chipping due to graphite inconsistencies is a concern, and where the possibility of regrinding offers economic advantages in producing common graphite electrodes and molds.
- Choose CVD Coated for Graphite When: Machining intricate details on graphite electrodes or molds, requiring very small diameter tools (e.g., micro-drills or end mills <3mm) or tools with highly complex cutting geometries that are difficult to fabricate with PCD. Its ability to achieve extremely sharp edges is beneficial when the highest surface finish is critical on the graphite workpiece. However, due to the thin coating, it might be less suitable for heavy roughing operations in highly abrasive graphite grades compared to robust PCD tools.
Evaluating Cost vs. Performance and Tool Life
Choosing the right tool often comes down to balancing the upfront cost with the long-term performance and resulting economics.
- Thinking Beyond Initial Price: It’s easy to focus on the purchase price. Carbide is cheapest, followed usually by CVD coated tools, with PCD often having the highest initial cost. However, this initial cost is only a small part of the total machining cost.
- The Power of Tool Life: As discussed, PCD and CVD tools last dramatically longer than carbide in graphite. Fewer tool changes mean less machine downtime, less operator intervention, and more consistent production.
- Calculating Cost Per Part: The most accurate way to compare is by looking at the cost per part8. This includes:
- (Tool Cost / Number of Parts per Tool Edge) + (Machine Time Cost per Part) + (Labor Cost per Part)
- While PCD/CVD tools cost more upfront, they produce vastly more parts per cutting edge and often allow for faster cycle times (reducing machine time and labor cost per part). In nearly all production scenarios involving graphite, this leads to a significantly lower cost per part compared to using carbide.
- Making the Final Decision:
- For prototyping or extremely low volumes where minimizing initial spend is the absolute priority, and performance/speed are secondary, carbide might be considered, but its limitations must be understood.
- For any regular production, the choice is effectively between PCD and CVD.
- Select PCD for its robustness, potential for regrinding, and often better economics on standard or larger tools.
- Select CVD Coated for micro-tools, highly complex geometries, or when the ultimate edge sharpness and surface finish are paramount.
Ultimately, understanding the trade-offs between initial cost, tool life, cycle time, and specific application requirements will guide the most economical and productive choice for your graphite machining needs.
What Key Factors Determine the Ideal PCD Tool Specification?
Knowing you need a PCD tool is one thing, but how do you choose the exact right one with the correct specifications?
Selecting the ideal PCD tool specification involves carefully considering the PCD grade and grit size appropriate for the task, optimizing the tool’s cutting geometry (like rake and clearance angles), ensuring proper cutting edge preparation (passivation), and matching all these factors to the specific type of graphite and the machining operation being performed.
Selecting the Appropriate PCD Grade and Grit Size
PCD isn’t just one single material; it comes in various “grades.” These grades are primarily defined by the average size of the diamond particles (grit size) sintered together to make the PCD structure. Think of it like sandpaper – different grits for different jobs.
- Fine Grit PCD (e.g., ~2-10 µm): Contains smaller diamond particles.
- Pros: Can produce sharper cutting edges, leading to better surface finishes. Generally preferred for finishing operations.
- Cons: May have slightly lower abrasion resistance or toughness compared to coarser grades.
- Medium Grit PCD (e.g., ~10-25 µm): Offers a balance between toughness, wear resistance, and the ability to achieve a good surface finish. Often used as a versatile, general-purpose grade for many graphite milling and turning tasks.
- Coarse Grit / Mixed Grit PCD (e.g., ~25-30 µm or blends): Contains larger diamond particles or a mix of sizes.
- Pros: Provides the highest toughness and resistance to abrasive wear. Ideal for roughing operations (removing lots of material quickly) or machining particularly abrasive or lower-quality graphite grades.
- Cons: May result in a slightly rougher surface finish compared to finer grades.
Important Note: Grade designations are often specific to the tool manufacturer. Therefore, it’s highly recommended to consult the manufacturer’s technical data and recommendations to choose the best grade from their specific offerings for your application (roughing, finishing, specific graphite type).
Optimizing Tool Geometry (Rake, Clearance, and Helix Angles)
The shape and angles ground onto the cutting tool – its geometry – play a massive role in how it cuts graphite. Key angles include:
- Rake Angle: This is the angle of the cutting face relative to the workpiece.
- Negative Rake: Creates a stronger cutting edge, often better for heavy cuts (roughing) or interrupted cuts, reducing the risk of chipping the PCD edge.
- Neutral or Positive Rake: Can reduce cutting forces, potentially leading to a better surface finish and less stress on the brittle graphite workpiece, making it suitable for finishing. However, a positive rake slightly reduces edge strength.
- The choice involves balancing edge strength and cutting forces for the specific task.
- Clearance Angle: This is the angle ground behind the cutting edge, allowing it to cut freely without the tool body rubbing against the newly machined surface. Enough clearance is vital to prevent friction, heat buildup, and poor finish. Too much clearance, however, can weaken the cutting edge.
- Helix Angle (Milling Tools): For tools like end mills, the helix angle is the spiral angle of the cutting edges. It affects how smoothly the tool enters and exits the cut, influences chip evacuation, and impacts cutting forces. Specific helix angles are often recommended for graphite to optimize performance.
Manufacturers invest considerable effort in determining the optimal combination of these angles specifically for graphite machining. Relying on tools designed with graphite-specific geometries is often the best approach.
The Role of Cutting Edge Preparation (Passivation)
Even after grinding, a PCD cutting edge can have microscopic inconsistencies or be too sharp, making it prone to tiny fractures (micro-chipping) when it first engages the abrasive graphite. Edge preparation, often called passivation or honing, addresses this.
- What it is: A controlled process that creates a tiny, precise radius on the very tip of the cutting edge.
- Why it’s done:
- Increases Edge Strength: Removes micro-defects and slightly rounds the apex, making it less likely to chip under cutting pressure.
- Improves Tool Life: A more stable, stronger edge resists wear and damage better, leading to longer and more predictable tool life.
- Enhances Consistency: Ensures the tool performs reliably from the start.
- Importance: Proper edge preparation is a critical step for maximizing PCD tool performance and longevity in demanding graphite applications, especially for high-speed machining. It’s often performed before any coating (like CVD) is applied.
Matching the Tool to the Specific Graphite Material and Application
Finally, selecting the ideal specification isn’t just about the tool in isolation; it’s about the entire system:
- Graphite Varies: Remember that “graphite” covers a range of materials. Isostatic graphite, extruded graphite, and vibration-molded graphite all have different densities, grain structures, purity levels, and hardness characteristics. These differences significantly impact how they machine. A tool optimized for a fine-grain isostatic graphite might not perform as well on a coarser extruded grade.
- Application Demands: The specific machining operation is crucial.
- Roughing vs. Finishing: Roughing prioritizes material removal rate and toughness (suggesting coarser PCD grades, possibly negative rake), while finishing prioritizes surface quality and accuracy (suggesting finer grades, optimized edge sharpness).
- Operation Type: Milling, drilling, turning, and engraving each put different stresses on the tool, potentially favoring different geometries or grades.
- Quality Needs: Required tolerances and surface finish specs will heavily influence the choice of PCD grade and edge preparation.
Therefore, the best approach is holistic: Understand the specific grade and properties of the graphite you’re machining, define the operation and quality requirements clearly, and then discuss these details with your PCD tool supplier. They can provide the most informed recommendation based on their tool specifications and experience with similar applications.
How Can You Maximize Performance and Lifespan of PCD Tools on Graphite?
You’ve selected the right PCD tool – now, how do you make sure you get the absolute best performance and longest life out of it when machining graphite?
Maximizing PCD tool performance and lifespan in graphite involves establishing optimal cutting parameters, ensuring highly effective chip and dust evacuation, practicing careful tool handling and setup routines, and diligently monitoring tool wear to know precisely when to replace or regrind the tool.
Establishing Optimal Cutting Parameters (Speed, Feed, Depth of Cut)
Using the right speeds and feeds is fundamental to getting the most out of your PCD tools without damaging them. Think of it like driving a car – there’s an optimal speed for fuel efficiency and engine health.
- Start with Recommendations: The best starting point is usually the cutting tool manufacturer’s recommendations. They provide suggested ranges for surface speed (SFM or m/min), feed rate (IPR, IPT, mm/rev, or mm/tooth), and depth of cut (DOC) based on the specific PCD tool grade and geometry for graphite. Keep in mind that these are often starting points; optimal parameters can vary based on your specific machine, setup rigidity, and the exact graphite grade, so referring to the supplier’s data for detailed ranges is advisable.
- Key Influences:
- Tool & Grade: Different PCD grades and tool diameters have different sweet spots.
- Machine Rigidity: A very stable and rigid machine can often handle more aggressive parameters than a lighter-duty machine.
- Operation Type: Roughing allows for deeper cuts and potentially higher feeds, while finishing requires lighter cuts and potentially adjusted speeds for surface quality.
- Fine-Tuning: Begin conservatively within the recommended range. Then, carefully listen to the cut, observe the chip formation (or dust), and inspect the surface finish and tool edge periodically. You can make small, incremental adjustments to optimize for speed or tool life based on these observations, but avoid drastic changes that could overload or chip the PCD edge.
Implementing Effective Chip and Dust Evacuation
As we’ve discussed, graphite machining produces fine, abrasive dust. Getting this dust away from the cutting zone immediately is critical.
- Why It’s Crucial:
- Prevents Recutting: If dust builds up, the tool ends up cutting the same particles multiple times, accelerating wear.
- Reduces Heat: Trapped dust can insulate the cutting zone, increasing heat and potentially harming the tool or workpiece.
- Protects Machinery: Keeps conductive dust out of sensitive machine components.
- Essential Methods:
- High-Efficiency Dust Collection: A powerful vacuum system specifically designed for fine dust is non-negotiable. Position the suction nozzle as close as physically possible to the cutting edge to capture dust at the source.
- Targeted Air Blast: Using compressed air directed at the cutting zone can help dislodge particles, especially from pockets or tight corners. However, ensure this works in conjunction with the vacuum system, directing dust towards the suction, not just blowing it around the machine.
Effective evacuation isn’t just about cleanliness; it’s a core part of optimizing the cutting process and protecting your tool investment.
Best Practices for Tool Handling, Setup, and Maintenance
PCD tools are tough in cutting but can be fragile if mishandled. Treat them with care:
- Careful Handling: PCD is extremely hard but also more brittle than carbide or steel. Never drop PCD tools or allow the cutting edges to bang against hard surfaces. Keep them in protective packaging when not in use.
- Quality Tool Holding: Use high-precision, clean, and well-maintained tool holders (collet chucks, hydraulic chucks, shrink-fit holders). Ensure the holder bore and tool shank are perfectly clean before assembly.
- Minimize Runout: Runout is the wobble of the tool as it rotates because it isn’t perfectly centered in the holder or spindle. Even tiny amounts of runout cause uneven loading on the PCD cutting edges – one edge does more work, wears faster, and can lead to vibration, poor finish, and drastically reduced tool life. Always check tool runout with a dial indicator after setup and aim for the lowest possible value.
- Machine Stability: Ensure your machine tool is rigid and well-maintained. Spindle bearing condition, machine level, and overall stability directly impact how well the PCD tool can perform without vibration or chatter, which accelerates wear.
Recognizing Wear Patterns and Knowing When to Replace Tools
Don’t wait for a tool to fail completely. Proactive monitoring and replacement are key to consistent results and preventing damage.
- Regular Inspection: Make it a routine to inspect PCD tool edges, especially in high-volume production. Use good lighting and magnification (a toolmaker’s microscope or a high-power loupe) as early wear can be hard to see with the naked eye.
- Common Wear Types in Graphite:
- Flank Wear: This is the most common, gradual wear land that forms on the relief face just behind the cutting edge due to abrasion. It typically grows predictably.
- Edge Chipping: Small nicks or fractures along the cutting edge. This indicates the edge might be overloaded, experiencing impact/vibration, or that flank wear has progressed too far, weakening the edge. Immediate attention is needed if chipping occurs.
- Establish Wear Limits: Determine a maximum acceptable flank wear land size (e.g., 0.005″ – 0.015″ or 0.1 – 0.4 mm, but this varies significantly; it’s best to consult your tool supplier for limits specific to their tools and your application). You might also monitor changes in surface finish, cutting noise, or spindle load as indicators of wear.
- Replace or Regrind Promptly: Once the wear limit is reached, replace the tool or insert, or send the tool for regrinding if applicable and economical. Pushing a worn tool further risks:
- Poor part quality (dimensions, finish)
- Scrapping parts
- Catastrophic tool failure (breakage)
- Potential damage to the workpiece or machine spindle
By carefully controlling how you use and maintain your PCD tools, you can significantly extend their productive life and achieve the best possible results when machining challenging graphite materials.
Conclusion
Successfully machining graphite hinges on understanding its unique challenges and leveraging the right cutting tool technology. PCD tools offer a powerful solution, providing the necessary wear resistance to overcome graphite’s abrasiveness effectively. By carefully selecting the appropriate PCD tool type, grade, and geometry, and then diligently applying best practices for cutting parameters, dust evacuation, handling, and wear monitoring, you can unlock significant gains in productivity, tool life, and overall cost-effectiveness for your graphite processing operations.
References
- Polycrystalline Diamond (PCD) tools1 – Explore the comprehensive range of standard and custom PCD & PCBN tools from ZYDiamondTools.
- Mohs scale2 – National Park Service explanation of the Mohs scale of mineral hardness.
- silica (quartz)3 – Geology.com page describing the properties and uses of Quartz (Silica).
- micro-abrasion4 – ScienceDirect topic page explaining abrasive wear mechanisms in engineering.
- PCD vs. Cemented Carbide5 – ZYDiamondTools blog post comparing PCD and Carbide cutting tools.
- PCD vs. CVD Diamond Coated Tools6 – ZYDiamondTools blog post comparing PCD and CVD diamond cutting tools.
- Chemical Vapor Deposition (CVD)7 – ScienceDirect topic page explaining the Chemical Vapor Deposition process.
- cost per part8 – ZYDiamondTools guide explaining the TCO concept and application for superhard tooling & abrasives.
ZY Superhard Tools Co., Ltd.
Do you have any needs for PCD tools or diamond grinding wheels? We can customize products to meet your specific requirements. If you have any ideas or requests, feel free to reach out—we’ll respond within 24 hours!
Do you have any needs for PCD & CBN tools or diamond grinding wheels? We can customize products to meet your specific requirements. If you have any ideas or requests, feel free to reach out—we’ll respond within 24 hours!
Do you have any needs for PCD & CBN tools or diamond grinding wheels? We can customize products to meet your specific requirements. If you have any ideas or requests, feel free to reach out—we’ll respond within 24 hours!
Post Categories
Product Categories
About Company
Related Posts
Which Turning Insert Shape Should You Choose?
Master turning insert selection. Our guide covers choosing the right shape for your job, decoding ISO codes, and selecting the
How Do You Solve Vibration, Chip Control, and Surface Finish Issues in PCD Grooving?
Solve common PCD grooving problems. This guide details how to fix vibration, improve chip evacuation, and achieve a flawless sidewall
Why Is Your Tooling Wearing Out Prematurely? A Machinist’s Guide to Key Causes & Proven Solutions
Facing premature tool wear? Learn the key causes like heat, vibration, & wrong parameters. Discover proven solutions from setup to
How Do You Select the Optimal PCD Tools for Scroll Compressor Machining?
Learn how to select the right PCD tools for scroll compressor machining. This guide covers the benefits over carbide, key
Subscribe
Simply enter your email below and click “Subscribe” to stay connected with everything new and exciting.