-
Whatsapp: +86 13526572721
-
Email: info@zydiamondtools.com
-
Address: AUX Industrial Park, Zhengzhou City, Henan Province, China
-
Whatsapp: +86 13526572721
-
Email: info@zydiamondtools.com
-
Address: AUX Industrial Park, Zhengzhou City, Henan Province, China
Why Are PCD Tools Essential for Aerospace Machining and How Do You Choose the Right Ones?
- Industry Knowledge, PCD & CBN Tools Knowledge
- -2025-05-07
- - byKevin Ray
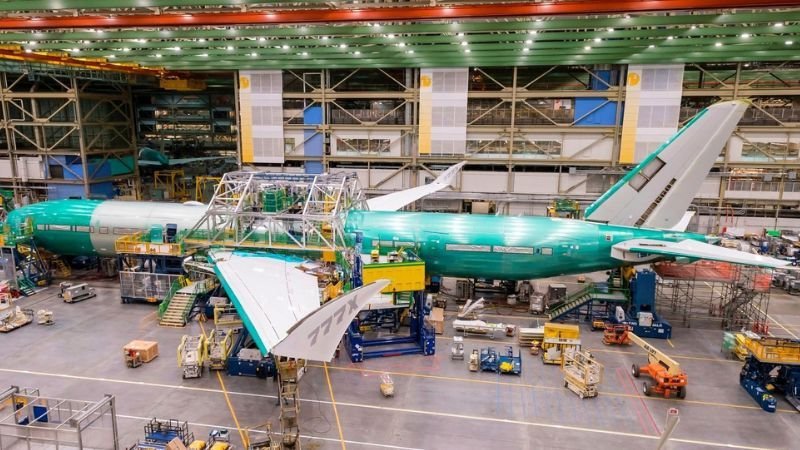
When it comes to building incredible machines like airplanes and spacecraft, why are Polycrystalline Diamond (PCD) tools such a big deal, and how can engineers and manufacturers make sure they’re picking the best ones for these critical jobs?
Polycrystalline Diamond (PCD) tools are essential for aerospace machining due to their unparalleled ability to efficiently cut tough and abrasive advanced materials like composites and specific non-ferrous alloys, leading to significant improvements in tool life, part quality, and overall productivity. Choosing the right PCD tools involves a careful assessment of the specific aerospace material, the machining application, machine capabilities, and a clear understanding of PCD grades, geometries, and critical tool design features to ensure optimal performance and cost-effectiveness.
Table of Contents
ToggleWhat Makes Polycrystalline Diamond (PCD) Tools Uniquely Suited for Aerospace Applications?
So, when we look at the complex and demanding world of aerospace manufacturing, what is it about Polycrystalline Diamond (PCD) tools that often makes them such a great choice for these tough jobs?
Polycrystalline Diamond (PCD) tools are uniquely suited for aerospace applications primarily because of their exceptional hardness, which gives them outstanding resistance to wear when cutting abrasive aerospace materials like composites and certain non-ferrous alloys. Furthermore, their ability to maintain incredibly sharp cutting edges ensures the high precision and quality essential for aerospace components, leading to more efficient machining and longer-lasting tools compared to many traditional options.
Understanding PCD: Composition and Key Properties
At its core, Polycrystalline Diamond, or PCD, isn’t a single giant diamond like you might see in jewelry. Instead, imagine countless tiny, man-made diamond crystals, like super-hard grains of sand, all fused together under extremely high heat and pressure. This process is called sintering1.
Usually, these diamond particles are bonded with a metallic material, often cobalt, which acts like a glue holding them together. This PCD layer is then typically attached (often brazed) to a tough base material, usually cemented carbide. The carbide base provides strength and support to the super-hard PCD cutting edge. Think of it like having the sharpest, hardest tip on a very strong knife body. For more general information, you might want to read an overview about Polycrystalline Diamond (PCD) Tools2.
This unique construction gives PCD several key properties vital for tough jobs:
- Exceptional Hardness: PCD is one of the hardest materials used for cutting tools, second only to natural single-crystal diamond. This extreme hardness is what allows it to tackle materials that would quickly dull other tools. For instance, on the Knoop hardness scale, PCD can measure around 5000-8000 HK, while tungsten carbide is typically in the 1300-2300 HK range. It’s important to note that specific hardness values can vary between PCD grades and manufacturers; therefore, consulting supplier specifications for precise details is always a sound approach.
- High Wear Resistance: Because it’s so hard, PCD resists wearing down even when cutting through very abrasive materials. This means the tool keeps its sharp edge for much longer.
- Good Thermal Conductivity: PCD is quite good at drawing heat away from the cutting edge. This is important because too much heat can damage both the tool and the part being made, especially sensitive aerospace materials. While this property leads to benefits we’ll discuss later, its ability to manage heat is a fundamental characteristic.
- Chemical Stability (with non-ferrous materials): PCD works best with materials that don’t react chemically with carbon (the element diamond is made of) at high cutting temperatures. This makes it excellent for non-iron-based materials.
Superior Performance on Aerospace Materials (Composites, Aluminum, Titanium Alloys)
The aerospace industry uses some truly amazing, but often very difficult-to-machine, materials. How does PCD stack up?
- Composite Materials (CFRP, GFRP):
Carbon Fiber Reinforced Polymers (CFRP) and Glass Fiber Reinforced Polymers (GFRP) are superstars in aerospace because they are strong yet lightweight. However, those carbon and glass fibers are incredibly abrasive – like cutting sandpaper, but much tougher!
PCD shines here because its extreme hardness directly counters this abrasiveness. You can explore if PCD tools are the optimal choice for machining your aerospace composites3 in more detail.- Clean Cutting: A sharp PCD edge can shear cleanly through the fibers rather than how a duller tool might push or tear them. This reduces issues like delamination4 (where the layers of the composite separate) and fiber pull-out.
- Maintained Edge: Because it resists wear from the abrasive fibers, the PCD tool stays sharp longer, ensuring consistent cutting performance. This is critical for the thousands of holes or long machined paths often required for components like wing sections or fuselage panels.
- Aluminum Alloys:
Aluminum alloys are also common in aircraft due to their low density and good strength. When machining aluminum, especially at the high speeds preferred for efficiency, other tools can suffer from built-up edge (BUE). This is where bits of the soft aluminum weld themselves to the tool tip, ruining the cut.
PCD’s very smooth, non-reactive surface (with aluminum) and its ability to maintain a sharp edge significantly reduce the tendency for BUE. This allows for:- High-Speed Machining: PCD tools can often cut aluminum alloys much faster than carbide tools.
- Excellent Surface Finish: The clean cutting action results in smoother surfaces on the aluminum parts, sometimes reducing the need for later polishing. Further insights can be found by asking, is PCD tooling the key to faster, cheaper, better aluminum machining?5
- Titanium Alloys:
Titanium is prized in aerospace for its high strength-to-weight ratio and corrosion resistance, especially at elevated temperatures. However, machining titanium with PCD presents significant challenges.- Chemical Reactivity: At the high temperatures generated when cutting titanium, a chemical reaction can occur between the carbon in the PCD and the titanium. This reaction causes the PCD to degrade very quickly, leading to rapid tool wear. For this reason, PCD is not typically the first choice for most titanium machining operations. Other materials like Cubic Boron Nitride (CBN)6 or specialized carbide grades are often preferred.
- Niche Applications: While not mainstream, some highly specialized PCD grades or application techniques (e.g., very specific cutting conditions, or when titanium is part of a material stack with composites or aluminum where PCD is beneficial for the other layers) might exist or be under development. However, for general titanium machining, PCD’s performance is limited by this chemical interaction. Users considering PCD for any titanium application should engage in thorough consultation with tool suppliers regarding the suitability of specific PCD products for that exact titanium alloy and process.
How PCD Differs from Traditional Carbide and Other Cutting Tool Materials
To really understand PCD’s place, it helps to see how it compares to other common cutting tool materials. Learning about the difference between PCD and Carbide tools7 can be very insightful.
Feature | Polycrystalline Diamond (PCD) | Tungsten Carbide (WC) | Coated Carbide |
---|---|---|---|
Primary Composition | Sintered diamond particles with binder | Tungsten carbide grains with cobalt binder | Carbide base with thin ceramic coating(s) (e.g., TiN, AlTiN) |
Hardness | Exceptional (highest among these) | Very Hard | Hard (coating); base is very hard |
Wear Resistance | Extremely High (especially on abrasives) | Good to High | High to Very High (coating dependent) |
Toughness (Brittleness) | More Brittle | Tougher | Coating can be brittle; base is tougher |
Thermal Conductivity | Good to Very Good | Moderate | Lower (coatings are often insulators) |
Chemical Stability | Best with non-ferrous, non-metallics | Generally good, can react with some materials | Coating adds stability, depends on coating type |
Typical Aerospace Use | Composites (CFRP/GFRP), Aluminum alloys | Steels, Titanium alloys, general purpose | Steels, Titanium, Superalloys, some Al alloys |
Key Advantage | Unmatched wear resistance on target materials | Good balance of hardness & toughness | Enhanced wear/heat resistance from coating |
Why the Differences Matter:
- PCD vs. Carbide: While tungsten carbide is very hard itself, PCD is significantly harder. This is why PCD excels on extremely abrasive materials like carbon fiber composites that would wear down even uncoated carbide relatively quickly. However, carbide is generally tougher (less prone to chipping from impact) than PCD, making it more forgiving in less stable machining conditions or for interrupted cuts in some metals.
- PCD vs. Coated Carbides: Coatings (like Titanium Nitride – TiN, or Aluminum Titanium Nitride – AlTiN) are applied to carbide tools to enhance their surface hardness, reduce friction, and improve heat resistance. These coatings can significantly improve carbide’s performance, making them very effective for many aerospace metals like steels and titanium alloys. However, for highly abrasive non-metallics like composites, the sheer volume hardness and wear resistance of bulk PCD often still wins out for the longest tool life. Once a coating wears through on a coated carbide tool, the underlying carbide wears more rapidly. PCD, on the other hand, has its hardness throughout its diamond layer.
Essentially, PCD is a specialized solution that offers peak performance in its ideal application window – primarily the machining of highly abrasive non-ferrous materials and composites common in aerospace. Its unique properties make it a problem-solver where other tools might fall short.
What Are the Tangible Benefits of Using PCD Tools in Aerospace Manufacturing?
So, we know that Polycrystalline Diamond (PCD) tools have some special characteristics, but what actual, real-world advantages do they bring when it comes to making critical parts for airplanes, helicopters, and spacecraft?
Using Polycrystalline Diamond (PCD) tools in aerospace manufacturing delivers several major tangible benefits. These primarily include drastically extended tool life which leads to significantly less machine downtime, the ability to achieve superior surface finishes and higher part accuracy, an overall boost in productivity allowing for faster production cycles, and the capability to effectively machine highly abrasive or difficult-to-cut materials that quickly wear down or defeat conventional tooling options.
Achieving Extended Tool Life and Reduced Downtime
One of the most significant advantages of using PCD tools, especially in demanding aerospace applications, is how incredibly long they can last. Why is this so important?
Remember how PCD tools are exceptionally hard and resistant to wear (as we discussed in their properties)? This means that when they are used to cut tough or abrasive aerospace materials, like carbon fiber composites, they don’t get dull nearly as quickly as tools made from materials like carbide.
- How much longer can they last?
It’s not uncommon for a PCD tool to last 10, 25, or even up to 50 times longer than a comparable carbide tool in the right application, particularly when machining abrasive composites or high-silicon aluminum. For example, in the mass production of aluminum aerospace components, a PCD-tipped milling cutter might machine tens of thousands of parts before needing replacement, whereas a carbide cutter might only last for a few thousand.
It’s crucial to understand that the exact increase in tool life can vary significantly. This depends on factors such as the specific PCD grade used, the exact material being machined (e.g., type of composite or aluminum alloy), the cutting speeds and feeds, the stability and condition of the machine tool, and the cooling or lubrication methods employed. Therefore, these figures are illustrative; obtaining performance estimates tailored to a specific application from tooling suppliers is always advisable. - Less Machine Downtime – More Parts Made:
When tools last longer, it means machines don’t have to be stopped as often to change them. Every time a machine is stopped for a tool change, it’s not making parts. This “machine downtime” can add up to a lot of lost production time.
Imagine drilling thousands of precise rivet holes in a large carbon fiber wing spar. If a PCD drill can complete the entire spar, or at least a very large section, before needing to be replaced, it saves a huge amount of time compared to using carbide drills that might need changing multiple times for the same job. This reduction in downtime directly translates to:- Increased machine availability: The machines are running and producing parts for a greater percentage of the time.
- Reduced labor for tool changes: Less time is spent by operators physically changing and setting up new tools.
- More consistent production flow: Fewer interruptions lead to a smoother and more predictable manufacturing process.
Enhancing Surface Finish Quality and Part Accuracy
The quality of every part in an aircraft or spacecraft is incredibly important for safety and performance. Can PCD tools actually help make parts better? Yes, they can!
This benefit comes directly from PCD’s ability to maintain a very sharp cutting edge for a long period.
- Smoother Surfaces:
Think about cutting wrapping paper with a brand-new, super-sharp pair of scissors versus an old, dull pair. The sharp scissors glide through, leaving a clean, smooth edge. The dull ones might snag, tear, or leave a fuzzy edge. It’s a similar idea in machining.
Because PCD tools stay sharp longer, they make cleaner cuts. This often results in a superior surface finish on the machined part. The surface will be smoother, with fewer tiny imperfections. In aerospace, a smoother surface can be important for aerodynamics, fatigue life, or the proper application of coatings. For instance, when milling aluminum alloys for aircraft skins, a PCD face mill can often produce a mirror-like finish that might reduce or even eliminate the need for later polishing operations. - Higher Part Accuracy and Consistency:
When a cutting tool starts to wear, the size and shape of the parts it makes can begin to change slightly. This is not acceptable for aerospace components, which often have very tight “tolerances” – meaning their dimensions must be extremely precise.
Since PCD tools wear down so slowly, they can produce many parts that are all very close to the exact same size and shape. This leads to:- Improved dimensional consistency: More parts meet the required specifications.
- Reduced scrap rates: Fewer parts have to be thrown away because they are not the right size or shape.
- Better assembly: Parts that are made accurately fit together more easily and reliably during the assembly of the aircraft or spacecraft. For example, precision-reamed holes for critical fasteners, when machined with PCD, will maintain their diameter and roundness for thousands of cycles, ensuring consistent joint integrity.
Boosting Productivity and Lowering Cost-Per-Part
In any manufacturing environment, doing things faster and more efficiently, without sacrificing quality, is a major goal. PCD tools can play a big role here.
- Faster Machining Speeds:
Because PCD is very hard and handles heat well (good thermal conductivity, as mentioned in its properties), it can often cut materials at higher speeds and feed rates than traditional tools. This is particularly true when machining aluminum alloys or when performing high-speed routing of composites. If you can cut faster, you can make more parts in the same amount of time. - Increased Throughput:
When you combine longer tool life (less downtime), faster cutting speeds, and fewer rejected parts (due to better accuracy and finish), the overall number of good parts coming off the machine in a day or a week – known as throughput – increases significantly. - Lowering the Cost-Per-Part:
Now, it’s true that PCD tools usually have a higher purchase price than carbide tools. This might make some people pause. However, it’s important to look at the bigger picture – the total cost to produce each individual part. This is often evaluated by looking at the Total Cost of Ownership (TCO)8.
Here’s a simplified way to think about it:- Even if a PCD tool costs, for example, five times more than a carbide tool…
- If it lasts 25 times longer (meaning you buy 25 carbide tools for every one PCD tool)…
- And if it allows you to make parts twice as fast (reducing machine time cost per part)…
- And if it reduces the number of bad parts you make…
…then the higher initial cost of the PCD tool is quickly offset. The actual cost attributed to tooling for each good part produced can become much lower with PCD. This is a critical calculation in high-volume aerospace production or when machining very expensive materials where scrap is costly.
Overcoming Challenges in Machining Abrasive and Difficult-to-Cut Materials
The aerospace industry is constantly pushing the boundaries with new materials that are lighter, stronger, or more heat resistant. The challenge is that these advanced materials are often incredibly difficult to machine with conventional tools.
- Tackling Extreme Abrasion:
As we’ve discussed, materials like Carbon Fiber Reinforced Polymers (CFRP) and Glass Fiber Reinforced Polymers (GFRP) are extremely abrasive. The hard carbon or glass fibers act like tiny grinding particles, rapidly wearing away standard tool edges.
PCD, with its diamond-like hardness, is one of the few tool materials that can effectively withstand this extreme abrasion for extended periods. This makes it possible to machine large composite structures, such as fuselage sections or wing skins, efficiently and with consistent quality, an operation that would be economically unfeasible or technically very challenging with rapidly wearing tools. - Handling Difficult Non-Ferrous Alloys:
Some aluminum alloys used in aerospace, particularly those with high silicon content (common in castings), are also very abrasive and can quickly wear down carbide tools. PCD excels in these applications, maintaining its edge and providing long life. It also helps avoid the “built-up edge” problem that can plague aluminum machining, ensuring clean cuts. - Enabling Complex Geometries in Tough Materials:
The ability to reliably machine these difficult materials means that aerospace engineers can design more complex and optimized parts. If a material couldn’t be machined economically or to the required quality, designers would be forced to use other, perhaps less ideal, materials or designs. PCD tooling, therefore, indirectly supports innovation in aerospace component design by making the “unmachinable” more manageable.
In essence, PCD tools provide a robust and reliable solution for the unique material challenges faced in aerospace manufacturing, allowing for processes that would be far less efficient, or even impossible, with other types of cutting tools.
Which Specific Aerospace Machining Operations Benefit Most from PCD Tooling?
Knowing that Polycrystalline Diamond (PCD) tools are incredibly hard and offer substantial advantages, which specific manufacturing tasks or jobs involved in building aircraft, satellites, and other aerospace vehicles truly reap the most significant rewards from using them?
Polycrystalline Diamond (PCD) tooling particularly excels and provides the most substantial benefits in several key aerospace machining operations. These prominently include the drilling of vast numbers of precision holes, especially in highly abrasive Carbon Fiber Reinforced Polymers (CFRP) and challenging multi-layer stack materials; various milling operations for both efficient high-volume roughing and the creation of high-quality finished surfaces on structural components; critical hole finishing tasks such as reaming for tight tolerances and countersinking for fastener seating; and the precise edge trimming and routing of composite parts to their final aerodynamic shapes and dimensions.
Drilling: Precision Holes in CFRP and Stack Materials
Drilling is perhaps one of the most common machining operations in aerospace, with a single aircraft requiring hundreds of thousands, if not millions, of holes for fasteners. Why is PCD a go-to for many of these drilling tasks?
- High-Volume Drilling in Abrasive Composites (CFRP):
Carbon Fiber Reinforced Polymer (CFRP) is a cornerstone of modern aerospace design due to its strength and low weight. However, it’s extremely abrasive. When drilling thousands of holes in CFRP components like wing spars, fuselage panels, or stringers, conventional carbide drills can wear out very quickly. This rapid wear leads to changes in hole size, poor surface finish inside the hole, and can cause defects like delamination (layers of the composite splitting apart) or fiber pull-out.
PCD drills, thanks to their exceptional hardness and ability to maintain a sharp cutting edge (a key property discussed earlier), can drill significantly more holes in CFRP before showing signs of wear. This consistent sharpness is crucial for producing clean, accurate holes with minimal defects, operation after operation. Specialized PCD drill point designs are often employed to further minimize delamination at the hole entry and exit. - Navigating Challenging Stack Materials:
Aerospace manufacturing frequently involves drilling through “stacks” of different materials bonded together, such as CFRP layered with aluminum (CFRP/Al) or CFRP with titanium (CFRP/Ti). These stacks are incredibly challenging because each material ideally requires different cutting speeds, feeds, and tool geometries.- For CFRP/Al stacks, PCD can perform very well. It handles the abrasive composite and also machines the aluminum cleanly without the issue of built-up edge.
- For CFRP/Ti stacks, the situation is more complex due to PCD’s typical reactivity with titanium. However, specialized PCD drills with unique geometries or drills where PCD is strategically used for the CFRP layer while another material handles the titanium are sometimes employed.
Achieving optimal results when drilling stack materials often necessitates careful selection of cutting parameters (speeds, feeds) that may need adjustment as the tool transitions between layers. For these complex multi-material drilling applications, seeking specific guidance from tooling suppliers on PCD tool selection and operational parameters is highly recommended, as performance can be deeply influenced by the exact stack composition and PCD tool design.
Milling: Efficient Roughing and Finishing of Structural Components
Milling involves using rotating cutters to remove material and create flat or contoured surfaces, pockets, and slots. PCD tools are highly beneficial for milling many aerospace components.
- Efficient Roughing Operations:
In “roughing,” the goal is to remove a large amount of material quickly. When rough milling abrasive aluminum alloys (especially those with high silicon content) or even some composite structures, PCD’s wear resistance means the tool can maintain higher material removal rates for longer periods without needing frequent replacement. This significantly speeds up the initial shaping of parts like aluminum wing ribs or fuselage frames. - High-Quality Finishing Operations:
For “finishing,” the aim is to achieve the final precise dimensions and a smooth surface. PCD milling cutters, especially face mills or end mills like a PCD Ball End Mill Cutter9 designed for finishing, can produce excellent surface quality on aluminum and composite parts. Their ability to hold a sharp edge minimizes cutting forces and ensures a clean shear, reducing the need for secondary finishing processes.
For instance, when machining large aluminum structural components for an aircraft’s internal framework, PCD face mills can create flat, smooth mating surfaces at high speeds, ensuring a perfect fit during assembly. Similarly, PCD end mills are used for finishing pockets and contours in these parts with high accuracy.
Reaming and Countersinking: Critical Hole Finishing Operations
Once a hole is drilled, it often needs further processing to meet the very strict requirements of aerospace engineering.
- Reaming for Precision Hole Sizing:
Reaming is an operation used to slightly enlarge a pre-drilled hole to a very precise diameter and improve its internal surface finish and roundness. In aerospace, many holes for critical fasteners, bearings, or interference-fit pins demand extremely tight tolerances.
PCD reamers are ideal for these applications because their diamond edges resist wear exceptionally well. This means they maintain their precise cutting diameter for a very long time, ensuring that hundreds or even thousands of reamed holes are consistently within the specified tolerance. This is vital for ensuring the interchangeability of parts and the integrity of critical joints. - Countersinking for Flush Fasteners:
Countersinking creates a cone-shaped enlargement at the opening of a drilled hole, allowing the head of a countersunk screw or rivet to sit flush with the material surface. This is essential for aerodynamic smoothness on external aircraft surfaces and for preventing snagging hazards.
PCD countersinking tools, such as specialized countersink drills for CFRP/GFRP composite materials10, produce clean, precise, and chatter-free conical seats in composites and aluminum. The sharpness of the PCD edges prevents tearing or delaminating the material around the hole, which is especially important in composite materials. Imagine the skin of an aircraft; every external fastener must sit perfectly flush. PCD countersinks help achieve this consistently across the thousands of fastener locations, contributing to both aerodynamic efficiency and structural integrity.
Edge Trimming and Routing: Shaping Composite Parts
Composite aerospace parts, such as fairings, winglets, or interior panels, are often manufactured to a near-final shape but then require precise trimming of their edges or the creation of internal cutouts (a process known as routing).
- Clean and Precise Edge Trimming:
The cured edges of composite components can be highly abrasive and prone to fraying or delamination if not cut cleanly. PCD edge trimming tools, often specialized routers, are used to achieve a smooth, precise, and defect-free edge. Their high wear resistance ensures that the required dimensional accuracy and edge quality are maintained even over very long cutting paths on large components. - High-Speed Routing:
Routing involves using a high-speed rotating tool to cut complex shapes, slots, or patterns within a part. When working with abrasive composites, PCD routers are the tools of choice.
Specialized designs like compression routers are particularly beneficial. These tools have cutting edges that push the material towards the center from both the top and bottom surfaces simultaneously. This “compressing” action virtually eliminates chipping or fraying on both sides of the cut, which is crucial for parts requiring perfect edge quality.
For example, shaping the complex aerodynamic contours of a composite helicopter rotor blade or trimming the window cutouts in a composite fuselage panel often relies on the precision and durability of PCD routing tools to ensure the final part meets stringent aerospace standards without damage.
In all these operations, the fundamental properties of PCD—its hardness and wear resistance—are leveraged to handle the challenging materials and demanding precision inherent in aerospace manufacturing.
How Can You Select the Optimal PCD Tools for Your Specific Aerospace Needs?
Alright, we’ve seen that Polycrystalline Diamond (PCD) tools are quite special and offer some impressive advantages for aerospace work, but with various options out there, how do you actually go about picking the perfect PCD tool for the specific job you need to do?
Selecting the optimal Polycrystalline Diamond (PCD) tool for your specific aerospace needs requires a careful evaluation of several key interacting factors. These primarily include the exact workpiece material and its specific characteristics, the nature of the machining application or operation to be performed, and the capabilities of your machine tool. Furthermore, a solid understanding of the different available PCD grades and their distinct properties, along with careful consideration of crucial tool geometries and specialized design features like coolant delivery systems or chip control mechanisms, is essential for making an informed and effective choice.
Key Factors to Consider: Workpiece Material, Application, Machine Capability
Choosing the right PCD tool isn’t a one-size-fits-all situation. It’s like picking the right tires for a car – you need to know what kind of car it is, where you’ll be driving, and the road conditions. Similarly, for PCD tools, several big-picture factors guide your decision:
- Workpiece Material:
This is a primary driver. As we learned earlier, PCD performs differently on various aerospace materials.- For Composites (CFRP, GFRP): You’ll need PCD tools designed to handle extreme abrasiveness. The focus will be on wear resistance and geometries that prevent delamination or fiber pull-out.
- For Aluminum Alloys: The choice might lean towards PCD grades that provide a very fine surface finish and resist built-up edge (BUE) formation, especially if high-speed machining is planned. The specific alloy of aluminum also matters, as some (like those with high silicon content) are much more abrasive than others.
- For Stack Materials (e.g., CFRP/Aluminum): Tool selection becomes more complex. You’ll need a tool, or a strategy, that can cope with the vastly different machining characteristics of each layer. This might involve specialized PCD tool designs or specific grades that offer a compromise in performance across the layers.
Always consider the material’s hardness, abrasiveness, thermal sensitivity, and how it tends to form chips.
- Application (Machining Operation):
What exactly are you trying to do with the tool? The specific machining operation dictates the fundamental type and design of the PCD tool.- Drilling: Requires a tool designed to create holes, often with specific point geometries for clean entry and exit.
- Milling: Needs a tool with cutting edges on its periphery and/or face to remove material from surfaces or create pockets.
- Reaming/Countersinking: These are finishing operations requiring tools designed for high precision and specific feature creation (e.g., a conical shape for a countersink).
- Edge Trimming/Routing: Involves tools designed to follow contours and shape edges, often at high speeds in composite materials.
The demands of each operation – like deep hole drilling versus shallow pocket milling, or roughing versus finishing – will point you towards different PCD tool characteristics.
- Machine Capability:
Your machine tool itself plays a huge role.- Rigidity and Stability: PCD is very hard but also more brittle than carbide. A machine that is very rigid and has minimal vibration will allow PCD tools to perform at their best and prevent premature chipping of the cutting edges. An older, less rigid machine might necessitate using tougher PCD grades or more conservative cutting parameters. CNC machining centers used in aerospace are typically designed for high rigidity.
- Spindle Speed and Power: Some PCD tools are designed for very high-speed machining, especially in aluminum. Your machine must be capable of reaching and maintaining these speeds safely and effectively. Sufficient spindle power is also needed, particularly for roughing operations or when using larger diameter tools.
- Coolant/Lubrication System: Does your machine have through-spindle coolant capability? Can it deliver Minimum Quantity Lubrication (MQL) if needed? The type of coolant system available can influence the PCD tool design you choose, especially regarding internal coolant channels.
- Workpiece Fixturing: While not part of the machine itself, how securely the workpiece is held is critical. Poor fixturing can lead to vibrations that damage PCD tools.
Thinking through these three areas – what you’re cutting, what you’re doing to it, and what you’re doing it with – will narrow down your options considerably.
Understanding Different PCD Grades and Geometries
Once you’ve considered the broad factors, it’s time to get into the details of the PCD itself. Not all PCD is created equal!
- PCD Grades – Not Just One Type of Diamond:
PCD is made from diamond particles, but the size of these particles and how they are bonded together (the binder content, typically cobalt) create different “grades” of PCD. Each grade has a unique balance of properties. Think of it like different kinds of sandpaper – some are coarse for heavy removal, others are fine for a smooth finish.
Common PCD Grade Categories and Their General Characteristics
PCD Grade Category | Typical Diamond Grain Size | Key Characteristics | Common Aerospace Applications |
---|---|---|---|
Coarse Grades | ~20-50 micrometers (µm) | Highest abrasion resistance, highest toughness/impact resistance within PCD family | Roughing highly abrasive composites (CFRP), high-silicon aluminum |
Medium Grades | ~10-25 micrometers (µm) | Good balance of abrasion resistance and edge quality | General purpose machining of composites, aluminum alloys; some milling and drilling |
Fine Grades | ~2-10 micrometers (µm) | Excellent edge sharpness, capable of producing very good surface finishes | Finishing operations on aluminum alloys, machining less abrasive non-metallics |
Ultrafine/Sub-micron | < 1-2 micrometers (µm) | Sharpest possible cutting edges, best surface finish, but less abrasion resistant | High-precision finishing of non-ferrous metals, applications requiring mirror-like finishes |
It’s very important to note that PCD grade classifications, their specific diamond grain sizes (e.g., 2µm, 5µm, 10µm, 25µm, etc.), and associated properties can vary significantly between different tooling manufacturers and suppliers. Direct consultation with your tooling supplier for their detailed specifications and expert recommendations on which of their particular grades is best suited for your material and application is crucial. The choice often involves a trade-off: finer grains generally allow for sharper edges and better finishes but may wear faster in highly abrasive materials compared to coarser, more wear-resistant grades.
- Tool Geometries – The Shape of Performance:
The “geometry” of a cutting tool refers to the specific angles and shapes of its cutting edges and flutes. For PCD tools in aerospace, getting the geometry right is crucial for success.- Rake Angle: This is the angle of the cutting face. For PCD tools, especially when machining composites, low positive or even negative rake angles are often used. This provides a stronger cutting edge to withstand the cutting forces and helps control how the chip (or dust, in the case of composites) is formed, minimizing forces that could cause delamination.
- Clearance Angle: This is the angle behind the cutting edge, providing space so the tool doesn’t rub against the freshly cut surface. Enough clearance is needed to avoid friction and heat, but too much can weaken the edge.
- Helix Angle (for drills and end mills): This is the angle of the spiral flutes. For drilling composites or stack materials, low helix angles or even straight flutes (0° helix) are sometimes preferred to reduce axial pulling forces that can contribute to delamination. For milling aluminum, higher helix angles might be used for better chip evacuation and smoother cutting.
- Cutting Edge Preparation: PCD cutting edges can be very sharp, but sometimes a slight rounding (hone) or a small flat (chamfer or K-land) is applied. This practice, sometimes referred to as edge radiusing on PCD inserts11, can strengthen a very delicate edge to prevent micro-chipping, especially in tougher PCD grades or when dealing with interrupted cuts. The specifics of edge preparation are often tailored by the tool manufacturer for optimal performance in the intended application.
- Point Geometry (for drills): As mentioned previously, drilling composites successfully often relies on specialized point designs. When selecting a PCD drill for composites, consider features like multi-facet points (e.g., 8-facet, 12-facet), dagger points, or brad points. These are engineered to shear the composite fibers cleanly at the hole’s periphery before the main cutting action begins, thereby reducing delamination. The exact point angle will also be critical.
Evaluating Tool Design Features for Aerospace (e.g., Coolant Delivery, Chip Control)
Beyond the PCD grade and basic geometry, other design aspects of the tool itself are vital for performance in aerospace applications.
- Coolant Delivery Systems:
Effectively managing temperature and removing chips from the cutting zone is crucial.- Through-Tool Coolant: Many PCD tools, especially drills and end mills intended for machining metals or deeper holes, are designed with internal coolant channels. These channels deliver coolant (liquid or air/MQL) directly to the cutting edges. This is highly effective for flushing chips away, reducing heat buildup, and prolonging tool life. When selecting a tool, ensure its coolant delivery design is compatible with your machine’s capabilities and suitable for your application (e.g., MQL for composites/stacks to avoid material contamination, or flood coolant for some aluminum machining).
- Nozzle Design: For externally applied coolant or air blast, the tool body design might influence how effectively the stream can reach the cutting zone.
- Chip/Dust Control and Evacuation Features:
Getting chips (or the fine dust from composites) away from the cutting area is essential.- Flute Design: The shape, size, and number of flutes on a drill or end mill significantly impact chip evacuation. For composite dust, open and polished flutes can help prevent clogging. For stringy aluminum chips, deeper flutes with specific helix angles might be needed.
- Chip Breakers: For materials that produce long, problematic chips, some PCD inserts might incorporate chip breaker geometries to break these into smaller, more manageable pieces, a feature particularly useful when considering PCD chipbreaker inserts for optimal machining performance12.
- Overall Tool Construction and Quality:
- PCD Tip Brazing: Most PCD tools involve a PCD tip brazed onto a carbide body. The quality and integrity of this braze are critical. A strong, void-free braze ensures the PCD tip remains securely attached under demanding cutting forces. Look for suppliers with proven brazing expertise.
- Carbide Shank/Body: The carbide body provides the overall strength and rigidity for the tool. High-quality carbide that is ground precisely will contribute to better performance and tool life.
- Tool Balancing: For PCD tools intended for high-speed machining (common in aerospace aluminum milling or composite routing), proper tool balancing is essential to minimize vibration, ensure accuracy, and protect both the tool and the machine spindle.
- Shank and Holder Interface: Ensure the tool shank (the part that goes into the machine spindle) is manufactured to tight tolerances for a good fit and concentricity in the tool holder. The type of tool holder used also plays a significant role.
By carefully considering these factors – the workpiece, application, machine, PCD grade, tool geometry, and overall design features – you can make a much more informed decision and select a PCD tool that is truly optimized for your specific aerospace manufacturing challenge. This process often benefits from close collaboration with knowledgeable tooling suppliers who can provide expert advice for specific situations.
Conclusion
In the demanding and precision-driven world of aerospace manufacturing, Polycrystalline Diamond (PCD) tools have clearly established themselves as essential technology. Their unique combination of extreme hardness, exceptional wear resistance, and favorable thermal properties makes them uniquely suited for tackling the challenges posed by advanced aerospace materials like composites and specific non-ferrous alloys.
From achieving significantly longer tool life and reducing costly machine downtime, to enhancing surface finish quality and part accuracy, the tangible benefits of using PCD tooling translate directly into improved productivity and lower overall costs per part. Furthermore, PCD tools empower manufacturers to effectively machine materials and undertake operations that would be far less efficient or even unfeasible with conventional tooling.
Successfully leveraging this advanced tooling, however, requires more than just acknowledging its potential. It demands a thoughtful approach to selection, considering the specific material, the application at hand, and machine capabilities. Understanding the nuances of different PCD grades, appropriate tool geometries, and critical design features is key to unlocking the full performance potential. When chosen wisely and applied correctly, PCD tools are not just cutting tools; they are vital enablers of innovation and efficiency in the aerospace industry.
References
- sintering1 – ScienceDirect topic page explaining the sintering process in materials science.
- Polycrystalline Diamond (PCD) Tools2 – ZYDiamondTools blog post providing a comprehensive overview of PCD tools.
- PCD tools are the optimal choice for machining your aerospace composites3 – ZYDiamondTools blog post discussing PCD suitability for aerospace composites.
- delamination4 – ScienceDirect topic page explaining delamination, particularly relevant to composite materials.
- is PCD tooling the key to faster, cheaper, better aluminum machining?5 – ZYDiamondTools blog post on the benefits of PCD for aluminum machining.
- Cubic Boron Nitride (CBN)6 – ZYDiamondTools blog post comparing PCD and CBN cutting tools.
- difference between PCD and Carbide tools7 – ZYDiamondTools blog post detailing the comparison between PCD and Carbide cutting tools.
- Total Cost of Ownership (TCO)8 – ZYDiamondTools blog post explaining TCO for superhard tooling.
- PCD Ball End Mill Cutter9 – ZYDiamondTools product page for PCD ball end mill cutters.
- countersink drills for CFRP/GFRP composite materials10 – ZYDiamondTools product page for specialized countersink drills.
- edge radiusing on PCD inserts11 – ZYDiamondTools blog post on the use and benefits of edge radiusing for PCD inserts.
- PCD chipbreaker inserts for optimal machining performance12 – ZYDiamondTools blog post on selecting and applying PCD chipbreaker inserts.
ZY Superhard Tools Co., Ltd.
Do you have any needs for PCD tools or diamond grinding wheels? We can customize products to meet your specific requirements. If you have any ideas or requests, feel free to reach out—we’ll respond within 24 hours!
Do you have any needs for PCD & CBN tools or diamond grinding wheels? We can customize products to meet your specific requirements. If you have any ideas or requests, feel free to reach out—we’ll respond within 24 hours!
Do you have any needs for PCD & CBN tools or diamond grinding wheels? We can customize products to meet your specific requirements. If you have any ideas or requests, feel free to reach out—we’ll respond within 24 hours!
Post Categories
Product Categories
About Company
Related Posts
Which Turning Insert Shape Should You Choose?
Master turning insert selection. Our guide covers choosing the right shape for your job, decoding ISO codes, and selecting the
How Do You Solve Vibration, Chip Control, and Surface Finish Issues in PCD Grooving?
Solve common PCD grooving problems. This guide details how to fix vibration, improve chip evacuation, and achieve a flawless sidewall
Why Is Your Tooling Wearing Out Prematurely? A Machinist’s Guide to Key Causes & Proven Solutions
Facing premature tool wear? Learn the key causes like heat, vibration, & wrong parameters. Discover proven solutions from setup to
How Do You Select the Optimal PCD Tools for Scroll Compressor Machining?
Learn how to select the right PCD tools for scroll compressor machining. This guide covers the benefits over carbide, key
Subscribe
Simply enter your email below and click “Subscribe” to stay connected with everything new and exciting.