-
Whatsapp: +86 13526572721
-
Email: info@zydiamondtools.com
-
Address: AUX Industrial Park, Zhengzhou City, Henan Province, China
-
Whatsapp: +86 13526572721
-
Email: info@zydiamondtools.com
-
Address: AUX Industrial Park, Zhengzhou City, Henan Province, China
What Is Diamond Polishing Paste and How Does It Solve Your Polishing Challenges?
- Industry Knowledge, Related Accessories Knowledge
- -2025-04-02
- - byKevin Ray
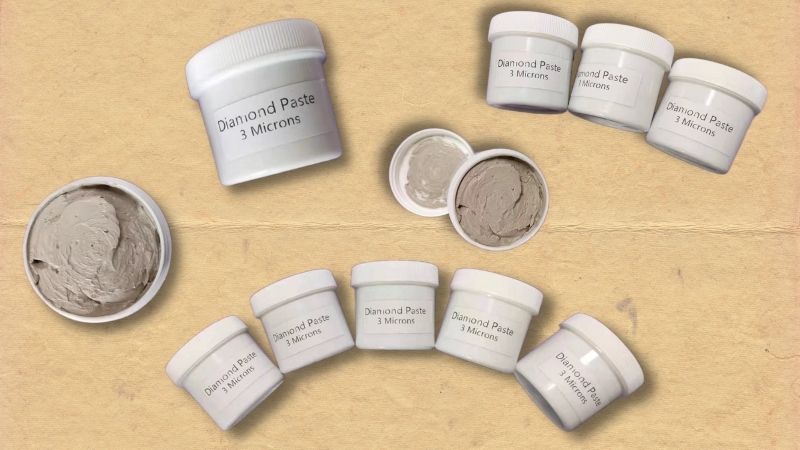
Ever wondered what diamond polishing paste actually is, and how it tackles those really tough polishing jobs?
Diamond polishing paste is a compound containing precisely sized diamond particles suspended in a carrier fluid (like oil or water), used for achieving high-quality surface finishes primarily on hard materials through controlled micro-abrasion; it solves polishing challenges by effectively cutting these tough surfaces to create exceptional flatness and luster, but selecting the right type based on grit size, diamond concentration, carrier formulation, and the specific material is crucial for success, while alternatives may be better suited for softer materials or when cost is a primary driver.
Table of Contents
ToggleUnderstanding the Composition of Diamond Polishing Paste
To effectively use this material, it’s essential to know its makeup. So, what are the key ingredients blended together inside that tube or syringe of diamond polishing paste?
Diamond polishing paste is essentially a mixture containing three main components: precisely sized diamond particles that act as the cutting abrasive, a carrier liquid or gel (commonly oil-based or water-based) that holds and distributes the diamonds, and specific concentrations of those diamond particles which dictate the paste’s cutting strength and speed.
Let’s break down each of these essential components.
The Role of Diamond Abrasive Particles (Grit Size/Micron Rating)
Imagine the diamond particles as the tiny “teeth” of the polishing paste. These microscopic bits of industrial diamond are what actually do the work of smoothing and shining a surface. Because diamond is the hardest known natural material, it can effectively grind away tiny amounts of even very hard materials like hardened steel or ceramics.
The size of these diamond particles is incredibly important and is measured in two common ways:
- Grit Size: This is similar to sandpaper grades. A lower grit number usually means larger, more aggressive particles. However, this system can sometimes be confusing as standards vary.
- Micron Rating (µm): This is a more precise measurement. One micron1 is one-millionth of a meter – extremely small! A higher micron number means larger particles (e.g., 45 µm), while a very low micron number means extremely fine particles (e.g., 1 µm or even 0.25 µm).
Think of it like this:
- Larger particles (higher micron / lower grit): Cut faster and remove more material. They are good for initial steps or removing deeper scratches but leave a rougher surface. For instance, a 60-micron paste might be used for initial shaping or significant stock removal on a metal mold.
- Smaller particles (lower micron / higher grit): Cut slower and remove less material per pass. They are used for final polishing steps to achieve a smooth, mirror-like shine. For example, a 1-micron paste is often used for the final polish on metallurgical samples or optical lenses.
It’s also worth knowing that diamonds used can be:
- Monocrystalline: Each particle is a single crystal. They tend to have sharper edges, cut aggressively initially, but may wear down slightly faster.
- Polycrystalline: Each particle is made of many smaller crystals bonded together. As they wear, new sharp edges can be exposed, leading to a more consistent cutting action, often a smoother finish, and potentially longer life, though they might cut slightly less aggressively at first. (Monocrystalline vs. Polycrystalline difference explained).
Important Note: The exact micron size corresponding to a grit number, and even the particle shape, can vary between manufacturers. Therefore, always check the supplier’s specifications for the precise micron rating to ensure you get the right abrasive size for your task.
Understanding Diamond Concentration Levels
Besides the size of the diamond particles, how many particles are packed into the paste also makes a big difference. This is called the diamond concentration. It’s usually described by weight percentage or simply categorized.
Higher concentration means more diamond particles are crammed into the carrier. This results in:
- Faster cutting: More diamond points are working on the surface at once.
- More aggressive action: Removes material more quickly.
- Often higher cost: Diamond is the expensive ingredient!
Lower concentration means fewer diamond particles are present. This typically leads to:
- Slower cutting: Fewer abrasive points are engaged.
- Less aggressive action: Often preferred for very fine finishing or delicate materials.
- Usually lower cost.
Manufacturers often use terms like:
- Light (L) or Low Concentration: For final finishing or light polishing.
- Medium (M) or Standard Concentration: A general-purpose balance.
- Strong (S) or Heavy (H) Concentration: For faster stock removal or working on very hard materials.
Important Note: There isn’t a universal standard for what percentage defines “Light,” “Medium,” or “Strong.” These terms, and the actual diamond weight percentage, can differ significantly between suppliers. Consequently, it’s crucial to refer to the manufacturer’s data sheet to understand the actual concentration you are purchasing and ensure it matches your process needs for efficiency and finish. For example, one brand’s ‘Medium’ might be 8% diamond by weight, while another’s could be 12%.
Oil-Based vs. Water-Based Carriers (The Paste Base)
The diamond particles need something to hold them together and allow them to be spread evenly on the workpiece or polishing tool. This is the job of the carrier, which forms the bulk of the paste. The two main types are oil-based and water-based2.
Oil-Based Carriers
- Composition: Uses various oils or oil-like synthetic fluids.
- Properties:
- Excellent lubrication: Reduces friction and heat buildup, which is crucial when polishing metals or during long polishing sessions.
- Stays put: Tends to adhere well to the polishing tool (like a felt bob or lap) and workpiece, requiring less frequent reapplication.
- Good suspension: Keeps diamond particles evenly dispersed for a longer time.
- Common Uses: Often preferred for polishing metals, molds (like injection molds), and general engineering components where heat resistance and longevity are beneficial.
- Cleanup: Requires solvents or specialized cleaners to remove residue.
Water-Based Carriers
- Composition: Uses water and often includes glycols or other agents to create a gel or liquid consistency.
- Properties:
- Easy cleanup: Washes away easily with water, which is a major convenience.
- Good for specific materials: Sometimes preferred for materials where oil contamination is a concern, such as certain optical components or some ceramics.
- May offer slightly different cooling properties compared to oil.
- Common Uses: Used in applications where easy cleanup is paramount or where oil residue is undesirable. Can be effective on glass, ceramics, and some composites.
- Consideration: May evaporate faster than oil-based carriers, potentially requiring more frequent application in some scenarios.
The choice between oil and water-based carriers depends heavily on the material being polished, the specific application requirements (like heat generation), and the ease of cleanup desired for the process. Both types effectively deliver the diamond particles to the surface; their differences lie mainly in lubrication, cleanup, and compatibility with certain materials and processes.
The Mechanism Behind Diamond Paste Superior Finish
Knowing the components is one thing, but understanding how it works is key. So, how exactly does diamond paste manage to create such smooth and shiny surfaces, especially on tough materials?
Diamond paste achieves a superior finish primarily through controlled micro-abrasion3; its incredibly hard diamond particles systematically remove microscopic high spots on a surface. This process leads to exceptional levels of surface flatness, which in turn creates high luster or shine.
Let’s explore the details of how this works.
The Mechanism: Controlled Micro-Abrasion Explained
Think of polishing with diamond paste as sanding, but on an incredibly tiny scale. This process is called micro-abrasion. Here’s how it functions:
- Tiny Cutting Tools: The diamond particles suspended within the paste carrier act like microscopic cutting tools or scrapers.
- Surface Leveling: When the paste is applied and worked across a surface (often with a polishing cloth, lap, or tool), these tiny, hard diamond particles shave off the microscopic “peaks” or high spots on the material’s surface.
- Gradual Smoothing: Each pass removes an infinitesimal amount of material, gradually leveling the surface. You typically start with larger diamond particles (coarser grit) to remove bigger imperfections and then move to progressively smaller particles (finer grit) for finer smoothing.
- Carrier’s Role: The paste carrier (oil or water-based) isn’t just holding the diamonds; it also helps to distribute them evenly, provides lubrication to reduce excess heat, and carries away the tiny bits of removed material (swarf).
Essentially, diamond paste doesn’t just rub a surface to make it shiny; it precisely cuts and planes it down at a microscopic level until it becomes exceptionally smooth.
Achieving High Levels of Surface Flatness and Luster
The main goal of this micro-abrasion is to achieve incredible surface flatness. Why is flatness so important?
Imagine the water surface of a lake. A wavy, uneven surface creates distorted reflections. However, a perfectly calm, flat water surface acts like a mirror. It’s the same with polishing:
- Removing Imperfections: Diamond paste removes the microscopic peaks and valleys that make a surface feel rough or look dull.
- Creating Uniformity: As these imperfections are leveled out, the surface becomes extremely uniform and flat.
- Boosting Reflectivity (Luster): A highly flat surface reflects light rays uniformly in the same direction, rather than scattering them. This uniform reflection is what our eyes perceive as luster, shine, or even a mirror finish.
In technical fields, this smoothness is often measured precisely using parameters like Ra (Roughness average). Industries requiring extremely smooth and flat surfaces rely heavily on diamond paste. For example:
- Metallography: Preparing metal samples for microscopic examination requires an incredibly flat, scratch-free surface to accurately view the material’s grain structure. Fine diamond pastes (e.g., 3 micron down to 1 micron) are essential here.
- Optics: Polishing lenses or fiber optic connectors demands extreme smoothness and flatness to ensure light transmits or reflects correctly with minimal scattering or signal loss.
Therefore, the superior finish from diamond paste comes directly from its ability to create exceptionally flat surfaces through controlled micro-abrasion.
Why Diamond Hardness is Key for Tough Materials
Why use diamond specifically? Couldn’t other hard particles work? The answer lies in diamond’s exceptional hardness.
Hardness is a measure of a material’s resistance to scratching or indentation. Scientists often use the Mohs scale4, ranging from 1 (like Talc) to 10 (Diamond).
- Diamond sits at 10: It is the hardest known natural substance.
- The Rule: To effectively cut or abrade a material, the abrasive must be significantly harder than the material itself.
This is crucial when working with modern engineered materials:
- Hardened Steels: Used in tools and molds, might be around 6-7 on the Mohs scale.
- Ceramics: Materials like alumina or zirconia used in electronics or wear parts can be 7-9 Mohs.
- Tungsten Carbide: Extremely hard material used for cutting tools, often around 9 Mohs.
- Sapphire: Used for watch crystals and optics, is also 9 Mohs.
Since diamond (Mohs 10) is harder than all these demanding materials, its particles can effectively scratch and remove material from their surfaces. Using a softer abrasive, like aluminum oxide (Mohs ~9, but often slightly less depending on form), might work on steel but would be very slow or ineffective on sapphire or tungsten carbide.
Consequently, diamond paste becomes the go-to solution when you need to achieve a fine finish on very hard substances where other abrasives simply can’t cut it efficiently. Its unparalleled hardness ensures effective micro-abrasion across the widest range of tough materials.
Common Polishing Problems Solved by Diamond Paste
Given its properties, it’s clear diamond paste is a problem-solver. So, what kinds of challenging polishing jobs is it actually used for in the real world?
Diamond paste excels at tackling several specific polishing problems, particularly those involving shaping and finishing extremely hard materials like carbides and ceramics, achieving high-gloss mirror finishes while removing fine scratches, meeting critical precision surface needs in fields like optics and mold making, and acting as an effective agent for demanding lapping and edge sharpening tasks.
Let’s look at these specific areas where diamond paste truly shines.
Overcoming Challenges with Extremely Hard Materials (Carbides, Ceramics, Hardened Steel)
One of the biggest challenges in manufacturing and maintenance is working with materials that are incredibly hard and resist wear. Think about materials like:
- Tungsten Carbide5: Used for cutting tools (like drill bits or end mills), wear-resistant parts, and drawing dies because it’s extremely hard and keeps its edge.
- Technical Ceramics6: Materials such as alumina, zirconia, or silicon carbide are used for things like pump seals, electronic substrates, bearing components, and heat-resistant parts due to their hardness, wear resistance, and stability at high temperatures.
- Hardened Steels: Tool steels, die steels, and bearing steels are heat-treated to be very hard and tough for demanding applications like injection molds, stamping dies, and high-performance bearings.
Trying to polish or precisely shape these materials with conventional abrasives (like aluminum oxide) can be incredibly slow or simply ineffective. Because diamond is harder than these materials (as discussed earlier), diamond paste provides an efficient solution. It allows technicians to:
- Shape and finish carbide cutting tool edges for optimal performance.
- Smooth ceramic seal faces to ensure leak-proof operation.
- Polish hardened steel mold cavities to precise dimensions and smooth finishes.
Therefore, diamond paste is often the essential choice when the material itself poses a significant hardness challenge.
Achieving True Mirror Finishes and Removing Fine Scratches
Sometimes, the goal isn’t just to shape a hard material, but to achieve an exceptionally smooth, reflective surface – a mirror finish. This is critical for both function and appearance in many applications. Diamond paste, especially in very fine micron sizes (like 3 µm down to 0.25 µm), excels at this by removing the finest microscopic scratches left by previous steps. Common examples include:
- Plastic Injection Molds: A mirror-polished mold cavity surface transfers that same glossy finish to the plastic part, improving its appearance and often helping the part release more easily from the mold.
- Decorative Metal Surfaces: Achieving a brilliant shine on jewelry, watch cases, or architectural metalwork.
- Scratch Removal: Gently polishing out fine scratches on hard, transparent materials like sapphire watch crystals or optical lenses (if the scratch isn’t too deep).
The controlled micro-abrasion action allows diamond paste to level surfaces to such a degree that light reflects almost perfectly, creating that desired brilliant shine.
Solving Precision Polishing Needs (Molds, Optics, Gemstones, Metallurgy Samples)
In many high-tech fields, the quality and precision of a surface finish are absolutely critical for performance. Diamond paste provides the necessary control for these demanding tasks:
- Mold & Die Polishing: Beyond just a mirror finish, molds often require specific textures or extremely precise dimensions. Diamond paste allows toolmakers to achieve the exact surface profile needed for optimal part production.
- Optical Components: Polishing lenses, prisms, mirrors, and fiber optic connectors requires achieving surface smoothness often measured in nanometers (billionths of a meter). Diamond slurries and pastes are standard for achieving the low-scatter, high-transmission/reflection surfaces needed. For instance, polishing the end-face of a fiber optic connector with fine diamond paste ensures minimal signal loss.
- Gemstone Faceting: Lapidarists use diamond laps and pastes to cut and polish facets on gemstones, maximizing their brilliance and value by controlling angles and achieving a flawless polish.
- Metallurgical Sample Preparation: When examining a material’s microstructure under a microscope, the sample surface must be perfectly flat and free from polishing artifacts (like scratches or distorted layers). Progressively finer diamond pastes are used to prepare samples for accurate analysis of grain size, phases, and defects.
In these precision applications, the predictability and effectiveness of diamond paste are invaluable.
Effective Lapping and Edge Sharpening Solutions
Diamond paste also plays a key role in processes focused on flatness and sharpness:
- Lapping7: This process creates extremely flat surfaces by rubbing a workpiece against a precision flat plate (the lap) coated with an abrasive compound. Diamond paste is often used as the lapping compound when working with hard materials that need exceptional flatness, such as mechanical seal faces, valve seats, or gauge blocks. The diamond effectively abrades the high spots across the entire surface against the reference flat lap.
- Edge Sharpening: Achieving a razor-sharp edge on tools made from hard steels (like high-carbon or stainless tool steels) or even ceramics requires a very fine abrasive. Diamond paste applied to a strop (leather or wood) or a hard lapping surface (like cast iron or even glass) is highly effective. It quickly cuts the hard steel or ceramic, refining the very apex of the edge to a high degree of sharpness suitable for knives, surgical instruments, chisels, or industrial blades.
Whether creating ultra-flat surfaces or ultra-sharp edges on challenging materials, diamond paste provides a powerful and controllable solution.
Selecting the Ideal Diamond Paste: Key Considerations
Now that you know what diamond paste is and what it can do, the practical question arises: how do you choose the right one? With all the options available in terms of diamond size, concentration, and carrier type, how do you figure out the right diamond paste for your specific job?
Selecting the ideal diamond paste involves considering four key factors: matching the diamond grit size (micron rating) to your current polishing stage (from coarse stock removal to fine final polish), accounting for the type and hardness of the material you are working with, deciding between oil-based or water-based formulations based on process needs like cleanup and heat tolerance, and choosing the diamond concentration level to balance polishing speed and efficiency against the desired final finish.
Making the right choice ensures you work efficiently and achieve the surface quality you need. Let’s explore each factor.
Matching Grit Size to Your Polishing Stage (From Stock Removal to Final Polish)
Polishing is almost always a step-by-step process. You rarely jump straight to a mirror finish from a rough surface. Therefore, you need to match the diamond particle size (micron rating) to the goal of each stage:
- Stock Removal / Heavy Grinding: If you need to remove significant material, smooth out deep scratches, or level a very uneven surface, start with a coarse grit.
- Typical Range: Roughly 40 to 90 microns (µm).
- Goal: Remove material quickly, establish basic shape/flatness. Leaves a visibly scratched or hazy surface.
- Intermediate Polishing / Pre-polishing: After the initial rough work, you move to medium grits to remove the scratches left by the coarser stage and further refine the surface. You might use one or two steps in this range.
- Typical Range: Roughly 6 to 30 microns (µm).
- Goal: Remove previous scratches, improve flatness, prepare for final polish. Leaves a smoother, possibly semi-reflective surface.
- Final Polishing / Mirror Finishing: The last steps use very fine diamond particles to achieve the final desired smoothness and luster.
- Typical Range: Roughly 0.25 to 3 microns (µm).
- Goal: Achieve high reflectivity (mirror finish), remove the finest scratches, reach final surface specification.
General Guideline: A common rule is that each subsequent polishing step should use a diamond paste with roughly half the micron size of the previous step. For example, you might progress from 30 µm -> 15 µm -> 6 µm -> 3 µm -> 1 µm.
Important Reminder: These micron ranges are general guidelines. The optimal sequence and specific micron sizes can vary depending on the material, the desired finish, and the specific product line from the supplier. Always consult the manufacturer’s recommendations for their paste series and your application.
Considering the Material You Are Working With
The material of your workpiece significantly influences your paste selection:
- Material Hardness: As discussed before, extremely hard materials (carbides, ceramics, hardened steels, sapphire) generally require diamond paste. Softer materials like aluminum, brass, copper, or standard plastics might be polished effectively with less aggressive diamond grits, or sometimes other abrasives might be more suitable (see the next section). Using too coarse a diamond grit on a soft material can remove too much material too quickly or embed abrasive particles.
- Material Properties: Some materials might react better with a specific carrier type. For instance, certain plastics or optical materials might be sensitive to oil-based carriers, making water-based a better choice. Porous materials might trap oil-based residues, making water-based preferable for easier cleaning.
Therefore, always consider the workpiece material’s hardness and characteristics when selecting both the grit size progression and the carrier type.
Deciding Between Oil-Based and Water-Based Formulations
Choosing the right carrier fluid depends on your process requirements and preferences:
Feature | Choose OIL-Based If… | Choose WATER-Based If… |
---|---|---|
Cleanup | Easy cleanup is not the top priority. | Easy cleanup with water is essential. |
Heat | Significant heat generation is expected. | Lower heat generation is desired. |
Work Time | You want the paste to stay on the tool longer. | Faster evaporation is acceptable. |
Material | Working on most metals, molds, some ceramics. | Oil contamination is a concern (optics, etc.). |
Lubrication | Maximum lubrication and cooling are needed. | Moderate lubrication is sufficient. |
Think about your specific task: Are you polishing a large mold where paste longevity is key (likely oil)? Or are you polishing delicate electronic components where residue is unacceptable (likely water)?
Choosing the Right Concentration for Efficiency vs. Finish
Finally, select the diamond concentration based on the balance you need between speed and control:
- Choose Higher Concentration (Strong/Heavy) When:
- You need faster polishing speed and quicker material removal.
- You are working on very hard materials that resist cutting.
- You are in the earlier stages of polishing (stock removal, intermediate).
- Efficiency and reducing polishing time are major goals.
- Choose Lower Concentration (Medium/Light) When:
- You need finer control over the polishing process, especially in final stages.
- You are working on more delicate or sensitive materials.
- You want to achieve the absolute best possible finish (sometimes lower concentration allows for a gentler action).
- Cost is a significant factor (lower concentration is usually less expensive).
Important Reminder: As mentioned before, the terms “Light,” “Medium,” and “Heavy” concentration aren’t standardized across the industry. Always check the manufacturer’s specifications for the actual diamond content and their recommendations for use to ensure you get the cutting performance you expect.
By carefully considering these four factors – polishing stage (grit), material, carrier type, and concentration – you can effectively select the ideal diamond paste combination to tackle your specific polishing challenge efficiently and achieve the desired result.
Limitations and Alternatives: When Diamond Paste Is Not Optimal
It’s powerful, but is diamond paste always the best choice for every polishing task, or are there situations where different methods or materials might actually be a better fit?
While powerful, diamond paste isn’t always the ideal solution; other polishing methods may indeed be more suitable when working with softer materials susceptible to damage from its aggressiveness, when overall cost is a primary concern and less expensive alternatives like aluminum oxide are sufficient for the job, or when only a very gentle, less aggressive polishing or final buffing action is truly required.
Understanding these situations helps you choose the most effective and appropriate method for your specific challenge.
Considerations for Softer Materials (Risk of Over-Abrasion)
Diamond paste is incredibly effective because diamond is so hard. However, that same hardness can be a disadvantage when working with softer materials. Trying to use diamond paste, especially coarser grits, on materials like certain plastics, wood, or soft metals can lead to problems:
- Excessive Material Removal: Diamond can easily gouge or remove too much material from soft surfaces.
- Deep Scratches: Instead of polishing, coarser diamond might create deep scratches that are hard to remove.
- Embedding: Diamond particles can sometimes get embedded into the surface of very soft materials rather than cutting them cleanly.
For materials like:
- Soft Plastics: Such as acrylic (Plexiglas) or polycarbonate.
- Wood: Especially for fine finishing.
- Soft Metals: Including copper, brass, gold, silver, or pure aluminum.
it’s often better to use gentler alternatives:
- Specialized Plastic Polishes: These are formulated specifically for plastics, often using much softer abrasives or chemical actions.
- Fine Grades of Conventional Abrasives: Very fine grit aluminum oxide or silicon carbide papers or compounds might be suitable.
- Non-Abrasive Buffing Compounds: Materials like Tripoli or rouge used on a buffing wheel can polish soft metals without significant material removal.
So, if your workpiece is relatively soft, diamond paste might be overkill and could potentially cause damage. Assess the material carefully before choosing diamond.
Evaluating Cost-Effectiveness vs. Alternatives (e.g., Aluminum Oxide)
Let’s be practical: diamond paste is generally more expensive than many other common abrasive materials due to the cost of the industrial diamond itself. While its effectiveness on hard materials often justifies the cost, it might not be the most economical choice if a cheaper alternative can do the job adequately.
Consider these common alternatives:
- Aluminum Oxide (Alumina, Al₂O₃): This is a very common and cost-effective abrasive. It’s quite hard (around 9 on the Mohs scale, though this varies), making it suitable for many tasks like:
- General purpose polishing of ferrous metals (steels) and non-ferrous metals (aluminum).
- Finishing some types of ceramics.
- Deburring operations.
(Compared to diamond tools, it offers lower cost for suitable applications).
- Silicon Carbide (SiC): Harder than aluminum oxide but still softer than diamond (Mohs ~9-9.5). It’s sharp and cuts well, often used for:
- Polishing cast iron.
- Working with non-ferrous metals like brass, aluminum, copper.
- Finishing glass, stone, and some ceramics.
The Key Question: Can a less expensive abrasive like aluminum oxide or silicon carbide achieve the surface finish you need on your specific material in an acceptable amount of time? If the answer is yes, then using diamond paste might be an unnecessary expense, especially for high-volume production or less critical applications. Always weigh the required performance against the cost of the abrasive.
Situations Where Less Aggressive Polishing is Required
Sometimes, the goal isn’t to remove material, flatten a surface significantly, or achieve the absolute highest possible mirror finish. You might just need to:
- Clean a surface lightly.
- Improve luster slightly on an already decent finish.
- Apply a final protective coating or wax.
- Perform a final buff after plating or painting.
In these cases, the aggressive cutting action of diamond paste is simply not needed and might even be counterproductive (e.g., slightly altering a surface you just wanted to clean). More suitable approaches could include:
- Buffing with Non-Abrasive Compounds: Using a soft buffing wheel with compounds like jeweler’s rouge (for precious metals) or a finishing wax can enhance shine without removing material.
- Chemical Polishing/Electropolishing: Industrial processes that use chemical reactions to smooth surfaces, often used for stainless steel or other specific alloys.
- Mild Cleaning Agents: Sometimes, a thorough cleaning is all that’s needed to restore appearance.
If your goal is gentle cleaning or final buffing rather than corrective polishing or finishing hard materials, diamond paste is likely not the right tool for the job. Choose a method appropriate for the light touch required.
Conclusion
Diamond polishing paste is clearly a highly effective tool for achieving superior surface finishes, especially when dealing with hard materials or requiring extreme precision and luster. Understanding its composition, how it works through micro-abrasion, and its specific strengths allows you to leverage its power. However, successful polishing also hinges on careful selection – matching the grit size, concentration, and carrier type to your specific material and polishing stage is essential. Furthermore, recognizing situations where its aggressiveness or cost makes alternatives more suitable ensures you always choose the most appropriate and efficient method for your polishing challenges.
References
- micron1 – Wikipedia page defining the micrometre (micron) unit of measurement.
- oil-based and water-based2 – ZYDiamondTools product page for oil-soluble and water-soluble diamond polishing paste.
- micro-abrasion3 – Wikipedia page explaining the general concept of mechanical abrasion.
- Mohs scale4 – Geology.com article explaining the Mohs scale of mineral hardness.
- Tungsten Carbide5 – Wikipedia page detailing the properties and applications of tungsten carbide.
- Technical Ceramics6 – CeramTec resource page providing information on advanced technical ceramics.
- Lapping7 – Wikipedia page explaining the lapping process used in manufacturing.
ZY Superhard Tools Co., Ltd.
Do you have any needs for PCD tools or diamond grinding wheels? We can customize products to meet your specific requirements. If you have any ideas or requests, feel free to reach out—we’ll respond within 24 hours!
Do you have any needs for PCD & CBN tools or diamond grinding wheels? We can customize products to meet your specific requirements. If you have any ideas or requests, feel free to reach out—we’ll respond within 24 hours!
Do you have any needs for PCD & CBN tools or diamond grinding wheels? We can customize products to meet your specific requirements. If you have any ideas or requests, feel free to reach out—we’ll respond within 24 hours!
Post Categories
Product Categories
About Company
Related Posts
Which Turning Insert Shape Should You Choose?
Master turning insert selection. Our guide covers choosing the right shape for your job, decoding ISO codes, and selecting the
How Do You Solve Vibration, Chip Control, and Surface Finish Issues in PCD Grooving?
Solve common PCD grooving problems. This guide details how to fix vibration, improve chip evacuation, and achieve a flawless sidewall
Why Is Your Tooling Wearing Out Prematurely? A Machinist’s Guide to Key Causes & Proven Solutions
Facing premature tool wear? Learn the key causes like heat, vibration, & wrong parameters. Discover proven solutions from setup to
How Do You Select the Optimal PCD Tools for Scroll Compressor Machining?
Learn how to select the right PCD tools for scroll compressor machining. This guide covers the benefits over carbide, key
Subscribe
Simply enter your email below and click “Subscribe” to stay connected with everything new and exciting.