-
Whatsapp: +86 13526572721
-
Email: info@zydiamondtools.com
-
Address: AUX Industrial Park, Zhengzhou City, Henan Province, China
-
Whatsapp: +86 13526572721
-
Email: info@zydiamondtools.com
-
Address: AUX Industrial Park, Zhengzhou City, Henan Province, China
What Are Diamond Cylindrical Grinding Wheels and How to Choose the Right One for Your Needs?
- Grinding Wheels Knowledge, Knowledge
- -2025-04-01
- - byKevin Ray
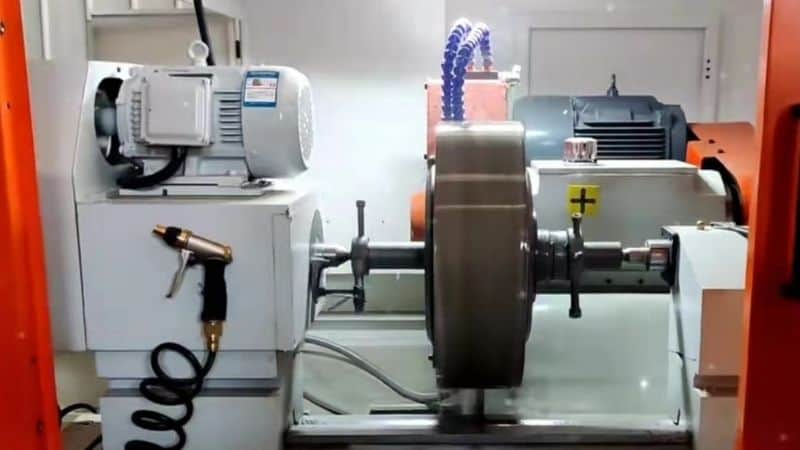
When tackling tough materials with cylindrical grinding, what exactly are diamond wheels, and how do you ensure you pick the perfect one for your job?
Diamond cylindrical grinding wheels are specialized abrasive tools utilizing diamond particles bonded within a matrix, specifically designed for precision grinding of external (OD) and internal (ID) diameters on extremely hard or brittle materials like carbide, ceramics, and glass using a cylindrical grinding machine1. Furthermore, their primary advantage lies in diamond’s exceptional hardness, enabling efficient material removal, high accuracy, and superior surface finishes on substances that conventional abrasives cannot effectively process.
Consequently, choosing the right wheel involves a systematic process of matching the wheel’s key characteristics—specifically diamond grit size, concentration, and bond type—to the workpiece material properties, the type of cylindrical operation (OD vs. ID), the required dimensional tolerances and surface finish, and the capabilities of the grinding machine itself. Careful consideration of these factors, along with proper operational practices like coolant use and wheel preparation, is crucial for optimal performance and achieving desired results in this demanding field.
Table of Contents
ToggleWhy Use Diamond Specifically for Cylindrical Grinding Applications?
So, when it comes to grinding really hard materials into perfect cylindrical shapes, why is diamond often the necessary choice?
Diamond cylindrical grinding wheels are essential because diamond ranks among the hardest materials known, making it uniquely capable of effectively shaping extremely hard and brittle substances like tungsten carbide, ceramics, and technical glass into precise cylindrical forms. Furthermore, its exceptional hardness allows for maintaining tight tolerance control and achieving superior surface finishes on materials that would rapidly wear down conventional abrasive wheels like aluminum oxide.
Consequently, using diamond ensures efficient material removal while preserving the wheel’s shape, which is critical for creating accurate geometric forms such as perfect rounds, tapers, or shoulders on cylindrical parts. This capability enables the production of high-quality surfaces required in demanding industries like aerospace (e.g., landing gear components), medical (e.g., ceramic implants), and advanced tooling (e.g., carbide cutting tools), where other abrasives simply cannot deliver the needed performance or precision.
Tackling Hard & Brittle Materials (Carbide, Ceramics, Glass) on Cylindrical Forms
Imagine trying to cut hardened steel with a wooden knife – it just wouldn’t work effectively. Similarly, conventional abrasives like aluminum oxide or silicon carbide struggle immensely when grinding materials such as tungsten carbide2, advanced engineering ceramics (like alumina or zirconia), or hardened glass. These workpiece materials are incredibly hard and often brittle.
Here’s why diamond excels:
- Unmatched Hardness: Diamond is significantly harder than conventional abrasives, topping the Mohs hardness scale3. This hardness allows the diamond crystals on the grinding wheel to penetrate and cut these challenging materials efficiently, rather than just rubbing or quickly wearing away.
- Wear Resistance: Because diamond is so hard, it resists wear far better than other abrasives when grinding these tough materials. This means the diamond cylindrical wheel maintains its shape and cutting ability for much longer. Maintaining the wheel’s profile is absolutely critical in cylindrical grinding to produce accurate diameters, straightness, and specific forms on the workpiece. For instance, grinding the precise cylindrical shape of a carbide drill blank requires a wheel that doesn’t easily lose its form.
- Effective on Brittleness: While hard materials are often brittle (meaning they can chip or fracture easily), the sharp, strong cutting points of diamond crystals can shear the material cleanly when used correctly (with appropriate machine settings and coolant). This minimizes subsurface damage compared to using duller, less hard abrasives that might crush or fracture the material unpredictably.
Achieving High Precision and Surface Finish on OD/ID Grinding
Precision is often the name of the game in cylindrical grinding, whether you’re working on the outside diameter (OD) or inside diameter (ID) of a part. Diamond wheels make it possible to achieve levels of accuracy and surface quality that are difficult or impossible with other methods on hard materials.
Here’s how:
- Holding Tight Tolerances: Because diamond wheels wear slowly and maintain their shape (form holding), they can consistently produce parts with very tight dimensional tolerances, often measured in micrometers (µm). This is crucial for components like fuel injector nozzles, bearing races, or hydraulic pistons where exact size and geometry are vital for performance. The wheel’s stability directly translates to the workpiece’s accuracy.
- Superior Surface Finish: The sharp, precise cutting action of diamond grains can produce exceptionally smooth surfaces. Surface finish is often measured by Ra (Roughness average). Diamond cylindrical grinding can achieve very low Ra values, sometimes resulting in mirror-like finishes on materials like ceramics or carbide. This is essential for applications requiring low friction (like seals or bearings) or specific optical properties. For example, finishing a ceramic seal face might require an Ra below 0.1 µm.
- Geometric Accuracy: Beyond just diameter size, cylindrical grinding often requires high geometric accuracy – ensuring the part is perfectly round (roundness), perfectly straight along its axis (cylindricity), and that different features are correctly positioned relative to each other (concentricity). The rigidity and wear resistance of diamond wheels contribute significantly to achieving these demanding geometric tolerances during both OD and ID operations.
Understanding the Limitations: Heat Sensitivity and Material Interactions
While diamond is incredibly effective, it’s not a universal solution for all cylindrical grinding tasks. Understanding its limitations is just as important as knowing its strengths.
- Heat Sensitivity: Diamond is a form of carbon. At elevated temperatures (typically above 700°C or about 1300°F, though this varies), especially in the presence of oxygen, diamond can begin to degrade or convert back into other forms of carbon like graphite, losing its hardness and cutting ability. Grinding generates significant heat, making temperature control absolutely critical. This is a major reason why effective cooling systems are non-negotiable in diamond grinding, a topic explored further in practical considerations.
- Chemical Reactivity with Ferrous Metals: This is perhaps the most significant limitation. At the high temperatures generated during grinding, diamond (carbon) has a strong chemical affinity for iron and iron-based alloys (like steel). The carbon from the diamond tends to dissolve into the steel workpiece. This chemical reaction causes extremely rapid wear of the diamond wheel, making it generally unsuitable and uneconomical for grinding most steels.
- Key Takeaway: For grinding steels and ferrous alloys, Cubic Boron Nitride (CBN), another superabrasive, is typically the preferred choice4 due to its higher thermal stability and lower chemical reactivity with iron. Diamond excels on non-ferrous metals, carbides, ceramics, glass, and composites.
- Brittleness Under Impact: Despite its extreme hardness, diamond is also somewhat brittle. Sudden impacts or excessive grinding pressure can cause the diamond crystals to fracture or dislodge from the bond material. This requires careful machine setup, stable workpiece holding, and controlled grinding parameters to avoid damaging the wheel or workpiece.
Which Industries Rely Heavily on Diamond Cylindrical Grinding?
Given diamond’s unique capabilities for hard materials, which specific industries depend most on this precision cylindrical grinding technology?
Diamond cylindrical grinding is indispensable across several advanced manufacturing sectors where precision processing of extremely hard or brittle materials is paramount. Key industries relying heavily on this technology include aerospace, automotive, medical device manufacturing, cutting tool production, and the processing of advanced ceramics, glass, and semiconductor materials.
Consequently, the demand stems from the need to produce high-tolerance, high-performance components like carbide cutting tools, ceramic bearings and seals, aerospace engine parts, medical implants, and precision glass optics, where conventional grinding methods fall short due to the challenging nature of the workpiece materials.
Here are some primary examples of where this technology is critical:
- Cutting Tool Industry: Arguably the largest user, essential for manufacturing and re-sharpening solid carbide drills, end mills, reamers, inserts, and PCD/PCBN tools, requiring sharp edges and precise geometries.
- Aerospace & Defense: Grinding hard coatings (e.g., thermal barriers), ceramic matrix composites (CMCs), and specific superalloys for turbine engine components, landing gear parts, and other critical structural elements needing tight tolerances.
- Medical Device Manufacturing: Shaping and finishing medical implants made from ceramics (like zirconia or alumina hip/knee joints), surgical instruments made from hardened alloys or carbides, and components for diagnostic equipment.
- Automotive: Used for precision grinding of hard-wearing components such as certain valve train parts, fuel injection nozzles, transmission components, and sometimes ceramic parts where high performance and longevity are needed (primarily non-steel applications).
- Ceramics and Glass Processing: Essential for grinding technical ceramics used in seals, bearings, pump parts, electronic substrates, and wear components. Also vital for precision shaping of optical glass lenses, prisms, mirrors, and specialty glass products.
- Electronics & Semiconductor: Processing hard, brittle materials like silicon carbide (SiC), sapphire wafers, ferrites, or specific ceramics used in semiconductor manufacturing equipment and electronic components.
Understanding these key application areas highlights the importance of selecting the right diamond cylindrical wheel to meet stringent industry demands.
What Are the Key Building Blocks of a Diamond Cylindrical Wheel?
Thinking about a diamond cylindrical wheel, what are the crucial ingredients that determine how it cuts and what kind of results you’ll get?
The key building blocks defining a diamond cylindrical wheel’s performance are fundamentally the diamond grit size, the diamond concentration, and the bond system that holds the diamonds in place. Essentially, grit size dictates the coarseness of the diamond particles affecting removal rate and finish, while concentration controls how much diamond is packed into the wheel, influencing cutting pressure, lifespan, and cost.
Furthermore, the bond system—commonly resin, vitrified (ceramic), metal, or electroplated—acts as the matrix securing the diamond grit. Importantly, the choice of bond governs the wheel’s overall characteristics, such as its hardness, wear resistance, heat management ability, and suitability for specific cylindrical grinding conditions like maintaining precise forms or operating wet versus dry.
Diamond Grit Size: Balancing Removal Rate and Finish in Cylindrical Grinding
Imagine grit size like the difference between coarse and fine sandpaper. In a diamond wheel, the grit size refers to the physical size of the individual diamond crystals embedded in the bond. This is one of the most critical factors influencing how the wheel interacts with your workpiece during cylindrical grinding.
- Understanding the Scale: Grit sizes are typically designated by numbers (mesh sizes) or sometimes micron ratings. Larger diamond particles correspond to a coarser grit (e.g., 60, 80, 100 mesh), while smaller particles make up a finer grit (e.g., 200, 400, 600 mesh or even finer micron sizes for polishing). It’s worth noting that standard grit size scales (like ANSI or FEPA) exist, but the specific numbering and the range available can sometimes vary between manufacturers, so it’s always wise to confirm the details with your wheel supplier.
- Impact on Material Removal: Coarser grit wheels have larger, more widely spaced diamond particles that take bigger “bites” out of the material. Consequently, they remove material more quickly, which is ideal for roughing operations in cylindrical grinding where the primary goal is rapid stock removal to get close to the final dimension.
- Impact on Surface Finish: Finer grit wheels have smaller, more densely packed diamonds that take much smaller “bites.” This action results in smaller scratches on the workpiece surface, leading to a smoother, finer finish (a lower Ra value). Therefore, finer grits are essential for finish grinding operations where achieving a specific surface quality and precise final dimension is the priority. For example, you might rough grind a ceramic shaft with an 80-grit wheel and then switch to a 500-grit wheel for the final polishing pass.
Diamond Concentration: Impact on Cutting Pressure, Life, and Cost for Cylindrical Tasks
Diamond concentration refers to the amount of diamond abrasive contained within the working layer of the grinding wheel, relative to the volume of the bond material. It doesn’t mean the percentage of the entire wheel, just the abrasive section.
- Understanding Concentration Values: Concentration is often expressed using codes like C50, C75, C100, or C125. It’s important to understand that C100 is generally considered a standard or reference concentration, but it doesn’t necessarily mean 100% diamond content. C75 has relatively less diamond than C100, while C125 has more. The exact diamond content corresponding to these values can differ slightly based on the manufacturer’s standards, so consulting their specifications is recommended.
- Effect on Cutting Action: A higher concentration means more diamond cutting points are engaged with the workpiece at any given time. This can distribute the grinding load across more points, potentially leading to smoother cutting and better form holding, especially in precision cylindrical grinding. Conversely, lower concentrations mean fewer cutting points, with each point potentially experiencing higher pressure. This can sometimes be beneficial for self-sharpening in certain bond types but might lead to faster wear.
- Influence on Wheel Life and Cost: Generally, a higher diamond concentration results in a longer wheel lifespan because there’s more abrasive available to do the work. However, diamond is expensive, so higher concentration wheels inevitably come with a higher initial purchase price. Choosing the right concentration often involves balancing the desired wheel life and performance against the budget. For instance, a high-volume production grinding of carbide rods might justify a higher concentration wheel for longer life, while a lower volume or less critical task might use a lower concentration to manage costs. The required cutting pressure also ties in – sometimes a lower concentration works better if the grinding machine has limited power.
Bond Systems (Resin, Vitrified, Metal, Electroplated): How They Behave in Cylindrical Grinding
The bond system is the “glue” or matrix that holds the diamond abrasive particles together and attaches them to the wheel’s core. The bond’s role is twofold: securely hold the diamond long enough for it to cut effectively, but also erode controllably to expose new, sharp diamond crystals as the old ones dull or fracture. The type of bond significantly influences the wheel’s overall behavior in cylindrical grinding. Here are the common types used:
- Resin Bond:
- Characteristics: These bonds use synthetic resins. They offer good elasticity (a slight “cushioning” effect), leading to excellent surface finishes. They are versatile, suitable for both wet and dry grinding, and perform well on tungsten carbide and some ceramics. Learn more about resin bonded grinding wheels5.
- Cylindrical Behavior: Often preferred for finish grinding operations on OD and ID due to the fine finishes achievable. Their relative softness allows them to conform slightly, which can be beneficial but means form holding might be less rigid than vitrified bonds.
- Vitrified Bond (Ceramic Bond):
- Characteristics: These bonds use fused glassy or ceramic materials, creating a strong, rigid, porous structure. They offer excellent form holding, aggressive cutting action, and good chip clearance due to porosity (helpful for coolant delivery). They are typically used in wet grinding.
- Cylindrical Behavior: Ideal for high-precision cylindrical grinding where maintaining an exact profile (like a sharp corner on a shoulder) and achieving high material removal rates are key. Their rigidity is advantageous for OD grinding demanding tight tolerances, but they can be more brittle than resin bonds.
- Metal Bond:
- Characteristics: Diamond particles are sintered within a metal matrix (often bronze or steel alloys). These bonds are extremely tough, durable, and offer excellent diamond retention and heat conductivity. They generally require wet grinding.
- Cylindrical Behavior: Best suited for grinding highly abrasive non-metallic materials like glass tubes, quartz, or some very hard ceramics where longevity is paramount. They provide the longest wheel life but typically produce rougher finishes compared to resin or vitrified bonds and may require higher grinding forces. Less common for ultra-high precision form grinding compared to vitrified.
- Electroplated:
- Characteristics: Features a single layer of diamond particles held onto the wheel core by a layer of nickel plating. This structure provides very free cutting action initially and excellent form holding for creating specific profiles.
- Cylindrical Behavior: Often used for small diameter ID grinding (internal grinding wheels or ‘quills’) or for grinding specific forms where only a single abrasive layer is practical. Their lifespan is limited because once the single diamond layer wears down, the wheel is expended – there’s no underlying diamond to expose.
How Does Your Specific Cylindrical Task Dictate Wheel Choice?
You understand the building blocks like grit, concentration, and bond – but how do you translate your specific grinding job requirements into selecting the actual diamond cylindrical wheel?
Selecting the optimal diamond cylindrical wheel requires carefully matching its specifications—primarily grit size, concentration, and bond type—to the unique demands of your specific task. Crucially, key factors dictating this choice include the inherent properties of the workpiece material (such as its hardness and tendency to chip), whether you are performing external (OD) or internal (ID) grinding, and ultimately, the required final dimensional tolerances and surface finish (Ra).
Furthermore, the capabilities of your cylindrical grinding machine itself, particularly its available surface speeds, spindle power, and overall structural rigidity, play a critical role in determining which wheel will perform best. Effectively aligning the wheel’s characteristics with both the material being ground and the machine performing the work is absolutely essential for achieving efficient, precise, and high-quality results in diamond cylindrical grinding.
Matching the Wheel to Your Workpiece Material Properties
While diamond wheels are generally chosen for hard, brittle materials like carbide, ceramics, and glass, the specific type and grade of that material significantly influence the ideal wheel choice. You need to consider more than just the general category.
- Hardness and Toughness: Different grades of tungsten carbide or types of ceramics (e.g., alumina vs. zirconia vs. silicon nitride) possess varying levels of hardness and toughness (resistance to fracture).
- Extremely Hard Materials: May require tougher bonds (like specific vitrified or metal bonds) that can withstand the high stresses, or perhaps finer grits to limit penetration depth and reduce chipping risk.
- More Brittle Materials: Benefit from “softer” acting wheels – perhaps a more forgiving resin bond or a finer grit size to minimize impact and prevent micro-cracking. Think about grinding delicate ceramic components versus robust carbide tooling.
- Thermal Properties: How well the material conducts heat matters. Materials that insulate heat well can lead to higher temperatures at the grinding point, potentially requiring bonds designed for cooler cutting or specific coolant strategies (which we touch on later).
- Example: Grinding a relatively tough grade of cemented carbide for a cutting tool insert might allow for a productive vitrified bond wheel. In contrast, grinding a highly brittle, heat-sensitive advanced ceramic might necessitate a specific resin bond formulation and a finer grit to ensure integrity.
Critical Differences: Selecting for External (OD) vs. Internal (ID) Grinding
The geometry of the grinding operation itself—whether you’re grinding the outside or inside diameter—presents very different challenges and often calls for different wheel strategies.
- External (OD) Grinding:
- Characteristics: Usually involves a larger contact area between the wheel and workpiece, easier access for coolant application, and allows for larger, more rigid wheels. Maintaining straightness, roundness, and profile accuracy over potentially long lengths is often key.
- Wheel Selection Tendencies: Can often utilize harder, more durable bonds (vitrified, sometimes metal) for better form holding and higher stock removal. Higher concentrations and coarser grits might be suitable for roughing stages.
- Internal (ID) Grinding:
- Characteristics: Operates within a confined space, requiring smaller diameter wheels (often mounted on ‘quills’). The contact arc is smaller, coolant delivery and chip removal are more challenging, and the wheel assembly (quill + wheel) is inherently less rigid.
- Wheel Selection Tendencies: Often requires “freer cutting” wheels to minimize grinding pressure and heat buildup in the confined space. This frequently means softer bonds (like specific resin formulations), potentially lower diamond concentrations, and finer grits. Electroplated wheels are very common for ID grinding, especially in small bores, due to their free-cutting nature and ability to be made in small diameters.
- Example: Grinding the OD of a hydraulic cylinder rod demands rigidity and might use a 300mm diameter vitrified wheel. Grinding the ID of a 10mm bore in a carbide die might use a 6mm diameter electroplated or specialized resin bond quill.
Defining Wheel Specs Based on Required Tolerances and Surface Roughness (Ra)
Ultimately, the quality specifications of the finished part are major drivers in wheel selection. What level of precision and smoothness do you need to achieve?
- Dimensional Tolerances: If the part requires very tight tolerances (e.g., dimensions held within a few micrometers, +/- 0.005mm), you typically need:
- Finer Grit Sizes: To ensure controlled material removal and minimize surface irregularities.
- Rigid Bonds: Vitrified bonds are often preferred for their ability to hold shape accurately, which translates directly to dimensional precision on the workpiece.
- Optimized Concentration: Concentration might be adjusted to ensure consistent cutting action and maintain form.
- Surface Roughness (Ra): If a very smooth surface (low Ra value) is required for sealing, bearing applications, or aesthetics, the primary choice is:
- Finer Diamond Grit Sizes: The smaller the grit, the smaller the scratches it leaves, resulting in a lower Ra value. Polishing operations might use grit sizes in the micron range.
- Appropriate Bond: Resin bonds generally produce better surface finishes than metal bonds due to their slight elasticity. Specific vitrified bond formulations can also achieve excellent finishes. Keep in mind that the achievable Ra is highly dependent on the entire system, including material, machine stability, and coolant; it’s advisable to discuss specific Ra targets with wheel suppliers.
- Example: A carbide punch requiring a tolerance of +/- 0.002mm and a surface finish of Ra 0.1 µm will demand a significantly different (likely finer grit, precision vitrified bond) wheel compared to a component needing +/- 0.02mm tolerance and Ra 0.8 µm finish.
Aligning Wheel Choice with Your Cylindrical Grinder Capabilities (Speed, Rigidity)
You can specify the theoretically perfect wheel, but it won’t perform well if it’s not compatible with your grinding machine. The machine and wheel must work together as a system.
- Wheel Surface Speed: Diamond wheels have recommended operating speed ranges (often expressed in surface feet per minute (SFPM) or meters per second (m/s)) for optimal performance and safety.
- Machine Capability: Ensure your grinder can achieve and maintain the speed recommended for the wheel’s diameter and bond type. Running a wheel too slow reduces cutting efficiency, while running it too fast is dangerous and can damage the wheel or machine. Always check and adhere to the maximum safe operating speed marked on the wheel, and consult manufacturer guidelines for optimal speeds, as these can vary significantly.
- Spindle Power (HP / kW): Aggressive grinding (coarse grits, high concentrations, hard bonds, fast removal rates) demands more power.
- Machine Limit: Select a wheel specification that your machine’s spindle motor can handle without excessive load or stalling. A low-power machine might necessitate a freer-cutting wheel (e.g., softer bond, lower concentration) even if a harder bond might theoretically last longer.
- Machine Rigidity and Condition: The overall stiffness of the machine (bed, slides, spindle bearings) is critical for precision cylindrical grinding.
- Impact on Choice: A highly rigid, well-maintained machine can effectively utilize harder bonds and achieve tighter tolerances because it resists vibration and deflection under load. A less rigid or worn machine may produce poor results (chatter, inaccurate dimensions) with harder wheels; in such cases, a softer, freer-cutting wheel might be a better compromise to minimize grinding forces.
- Example: Trying to use a hard, high-concentration vitrified bond wheel designed for high productivity on a lightweight, low-power, older cylindrical grinder is unlikely to succeed; a softer resin bond wheel might be the only viable option for that machine, even if wheel life is shorter.
What Practical Considerations Ensure Optimal Diamond Cylindrical Grinding?
You’ve selected the ideal diamond cylindrical wheel based on your task – so what practical steps do you need to take during the grinding process itself to guarantee top performance and quality?
Achieving optimal results in diamond cylindrical grinding goes beyond just selecting the correct wheel; it critically depends on disciplined attention to practical operational factors. Crucially, implementing effective coolant strategies to manage the intense grinding heat and efficiently flush away debris, performing essential wheel preparation through proper truing and dressing procedures to maintain wheel geometry and sharpness, and knowing how to identify and troubleshoot common issues like glazing, loading, or chatter are all vital for success.
Consequently, consistently applying these practical considerations ensures that your diamond wheel cuts efficiently, maintains its cutting ability over time, achieves the desired part quality and precision, and ultimately reaches its potential service lifespan. Overlooking these critical steps, conversely, can quickly lead to poor surface finishes, dimensional inaccuracies, premature or uneven wheel wear, excessive heat generation, or even damage to the workpiece or the grinding machine itself.
Effective Coolant Strategies: Why It Is Crucial for Diamond Wheels
As mentioned earlier, diamond is sensitive to high temperatures, and grinding extremely hard materials generates significant heat right at the cutting zone. This makes coolant (or grinding fluid) absolutely essential, not just helpful, in most diamond cylindrical grinding operations. Its roles are critical:
- Cooling: This is paramount. Coolant carries away heat from the grinding zone, protecting both the diamond crystals from thermal damage (which degrades their hardness) and the workpiece from thermal expansion or metallurgical changes (burning).
- Lubrication: Coolant reduces friction between the diamond grit, the bond, the workpiece, and the removed chips (swarf). Lower friction means less heat generation and requires less grinding power.
- Cleaning/Flushing: A sufficient flow of clean coolant washes away the grinding swarf and dislodged abrasive particles from the cutting zone and the wheel face. This prevents chips from interfering with the cut or loading (clogging) the wheel.
Coolant Selection and Application
Choosing and applying coolant effectively involves several considerations:
- Coolant Type: Common types include synthetics (water-based, good cooling), semi-synthetics (blend oil and synthetics, balanced properties), and straight oils (excellent lubrication, less cooling). The best choice depends on the material being ground (e.g., carbide vs. glass), the bond type (some bonds react negatively to certain coolant chemistries), and the specific operation. Crucially, the ideal coolant type, its concentration when mixed with water, and the required filtration level can vary significantly; always consult recommendations from both the coolant manufacturer and the grinding wheel supplier for your specific application.
- Delivery Method: It’s not enough to just have coolant; it must reach the precise point where cutting occurs. In cylindrical grinding, flood cooling using well-aimed nozzles is typical. Ensure adequate flow rate and pressure to penetrate the grinding zone effectively, especially in challenging ID grinding situations where space is limited. Poor coolant delivery is a common cause of grinding problems.
- Filtration: Keeping the coolant clean is vital. Effective filtration systems remove fine swarf and abrasive particles. If these particles are recirculated, they can scratch the workpiece surface, interfere with the grinding action, and contribute to wheel loading.
Essential Wheel Preparation: Truing and Dressing Procedures
Unlike some conventional wheels that might break down slightly during use to expose new grit, diamond wheels require deliberate preparation and maintenance steps to keep them cutting efficiently and accurately. The two key procedures are truing and dressing:
- Truing: This process ensures the grinding wheel runs perfectly round and concentric with the machine’s spindle axis. It also establishes or corrects the wheel’s profile (e.g., ensuring a perfectly flat face for cylindrical grinding or creating a specific radius). Truing eliminates runout and vibration, which is essential for achieving dimensional accuracy and good surface finish. It’s typically done less frequently than dressing, often using specialized tools like rotary diamond dressers or brake truing devices, particularly for vitrified or metal bond wheels. Think of it like ensuring a tire is perfectly round and balanced on a car.
- Dressing: This process “sharpens” the wheel face. It involves removing a small amount of the bond material to expose fresh, sharp diamond cutting edges and to clear away any embedded workpiece material (loading) or flattened/dull diamond grits (glazing). Dressing restores the wheel’s free-cutting ability. The method depends heavily on the bond type: resin and some vitrified wheels might be dressed using abrasive dressing sticks, while metal bond wheels might require different techniques. Guidance on how to dress diamond wheels6 specifically can provide practical steps. Think of this like sharpening a dull knife.
Why They Matter
Without proper truing, achieving precise dimensions and avoiding vibration is impossible. Without regular dressing, the diamond wheel will eventually stop cutting efficiently (it will glaze or load), leading to increased grinding forces, excessive heat, poor surface finish, and potential damage. The correct tools, parameters (like infeed rate and traverse speed during truing/dressing), and the necessary frequency for these procedures vary widely depending on the specific wheel bond, grit size, application, and material. Always follow the grinding wheel manufacturer’s detailed recommendations for preparing and maintaining your specific wheel.
Troubleshooting Common Cylindrical Grinding Issues (Glazing, Loading, Chatter)
Even with careful selection and preparation, grinding issues can arise. Recognizing the common problems (glazing, loading, etc.) and knowing potential causes helps resolve them quickly:
- Glazing:
- Symptoms: The wheel face appears smooth, shiny, or “closed.” It stops cutting effectively, often makes more noise, and generates excess heat.
- Common Causes: Diamond grits have become dull or flattened; the bond material is not eroding properly to expose new grit (bond may be too hard for the application or parameters); inadequate dressing.
- Possible Solutions: Dress the wheel using the recommended procedure; review grinding parameters (consider increasing feed rate slightly if appropriate); if persistent, evaluate if a softer bond grade or different specification is needed.
- Loading:
- Symptoms: The wheel face becomes clogged with workpiece material (swarf). Results in poor cutting, high heat, chatter, and a poor surface finish. You might visually see material packed between the grits.
- Common Causes: Ineffective coolant application (flow, pressure, direction); incorrect coolant type or concentration; inadequate coolant filtration; wheel grit size too fine or bond too dense for the stock removal rate; dressing needed.
- Possible Solutions: Optimize coolant delivery and ensure cleanliness/filtration; dress the wheel thoroughly; consider a coarser grit or more open bond structure if appropriate for the task; adjust grinding parameters (e.g., reduce feed rate).
- Chatter:
- Symptoms: Distinct, often regularly spaced marks or wavy patterns appear on the workpiece surface; often accompanied by audible vibration or humming during grinding.
- Common Causes: Vibration within the grinding system – this could stem from an unbalanced wheel, worn machine spindle bearings, loose workpiece clamping, machine components vibrating at their natural frequency, wheel being out-of-true, or incorrect grinding speeds/feeds exciting vibration.
- Possible Solutions: Ensure the wheel is properly trued and balanced; check the rigidity and condition of the machine (spindle, slides, work holding); adjust wheel speed or workpiece speed (sometimes small changes can move away from a resonant frequency); ensure dressing is appropriate (a poorly dressed wheel can induce chatter).
- Poor Surface Finish / Burning:
- Symptoms: Surface roughness (Ra) is higher than expected; visible scratch marks; discoloration or burn marks on the workpiece indicating excessive heat.
- Common Causes: Wheel grit size too coarse for the required finish; improper dressing technique leaving an uneven surface; wheel glazing or loading causing rubbing and heat; inadequate coolant delivery; grinding parameters (speed, feed) too aggressive.
- Possible Solutions: Select a finer grit wheel for the finishing pass; ensure proper dressing technique; address any glazing or loading issues; optimize coolant delivery; reduce feed rates or adjust speeds as needed.
Conclusion
Navigating the world of diamond cylindrical grinding wheels involves understanding not just what they are, but why their unique properties are essential for processing challenging materials. Successfully choosing the right wheel hinges on a clear grasp of its core components—grit, concentration, and bond—and methodically matching these elements to the specific demands of your material, operation (OD vs. ID), required quality (tolerance and finish), and machine capabilities. However, selection alone isn’t enough. Achieving optimal performance, longevity, and the desired results truly depends on diligent application of practical considerations, including effective coolant management, proper wheel truing and dressing, and the ability to troubleshoot common grinding problems. By integrating this knowledge of selection criteria with sound operational practices, you can confidently harness the power of diamond cylindrical grinding wheels for your precision manufacturing needs.
References
- cylindrical grinding machine1 – Wikipedia overview of cylindrical grinders and the process.
- tungsten carbide2 – Encyclopedia Britannica entry defining tungsten carbide and its properties.
- Mohs hardness scale3 – Geology.com explanation and chart of the Mohs scale for mineral hardness.
- typically the preferred choice4 – ZYDiamondTools internal blog post comparing CBN and Diamond grinding wheels for different needs.
- resin bonded grinding wheels5 – ZYDiamondTools comprehensive guide to mastering the selection and application of resin bond diamond/CBN grinding wheels.
- how to dress diamond wheels6 – ZYDiamondTools internal blog post providing guidance on dressing procedures.
ZY Superhard Tools Co., Ltd.
Do you have any needs for PCD tools or diamond grinding wheels? We can customize products to meet your specific requirements. If you have any ideas or requests, feel free to reach out—we’ll respond within 24 hours!
Do you have any needs for PCD & CBN tools or diamond grinding wheels? We can customize products to meet your specific requirements. If you have any ideas or requests, feel free to reach out—we’ll respond within 24 hours!
Do you have any needs for PCD & CBN tools or diamond grinding wheels? We can customize products to meet your specific requirements. If you have any ideas or requests, feel free to reach out—we’ll respond within 24 hours!
Post Categories
Product Categories
About Company
Related Posts
Why Is Your Tooling Wearing Out Prematurely? A Machinist’s Guide to Key Causes & Proven Solutions
Facing premature tool wear? Learn the key causes like heat, vibration, & wrong parameters. Discover proven solutions from setup to
How Do You Select the Optimal PCD Tools for Scroll Compressor Machining?
Learn how to select the right PCD tools for scroll compressor machining. This guide covers the benefits over carbide, key
How Do You Choose the Right Cutting Tool for Your Mold Steel Machining?
Learn how to choose the right cutting tools for mold steel machining. This guide covers steel hardness, tool materials, coatings,
Machining Nickel-Based Superalloys: Tooling Selection and Case Studies
Learn to master machining nickel-based superalloys. This guide covers tooling selection (CBN, ceramics), parameter optimization, and real-world case studies. Read
Subscribe
Simply enter your email below and click “Subscribe” to stay connected with everything new and exciting.