-
Whatsapp: +86 13526572721
-
Email: info@zydiamondtools.com
-
Address: AUX Industrial Park, Zhengzhou City, Henan Province, China
-
Whatsapp: +86 13526572721
-
Email: info@zydiamondtools.com
-
Address: AUX Industrial Park, Zhengzhou City, Henan Province, China
Optimizing Piston Production: When and How Should You Apply PCD Tools in Automobile Piston Processing?
- Industry Knowledge, PCD & CBN Tools Knowledge
- -2024-10-16
- - byKevin Ray
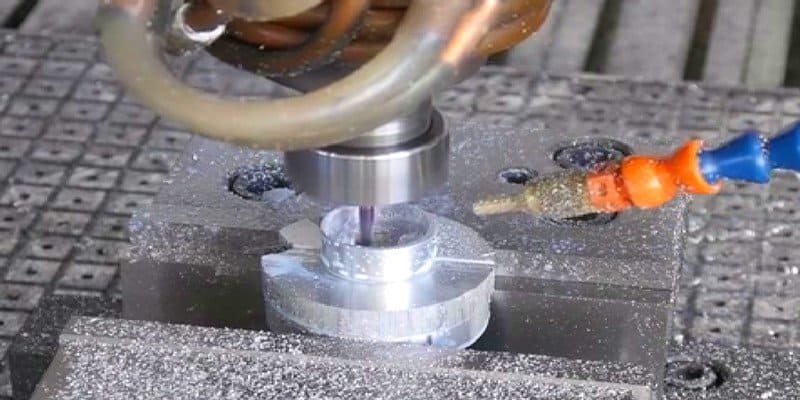
When exploring ways to improve how automobile pistons are manufactured, what’s the essential information regarding Polycrystalline Diamond (PCD) tools – when are they truly beneficial, and how can producers effectively use them?
Applying Polycrystalline Diamond (PCD)1 tools in automobile piston processing offers significant advantages, particularly when machining aluminum alloys, leading to enhanced part quality, extended tool life, and greater overall productivity. Successful implementation relies on identifying the specific piston features that benefit most, carefully managing key technical factors like tool selection and cutting parameters, reviewing real-world results, and choosing capable tooling suppliers.
Table of Contents
ToggleWhy Choose PCD Tooling Over Alternatives for Piston Machining?
So, when it comes to making crucial car parts like pistons, why should manufacturers strongly consider using PCD tools instead of other options they might already have?
PCD (Polycrystalline Diamond) tools provide major benefits for machining automobile pistons, mostly because they are incredibly hard and resist wearing down when cutting the aluminum alloys pistons are made from. This advantage leads directly to tools lasting much longer, creating smoother part surfaces, holding tighter size controls, boosting how many parts can be made, and finally, lowering the cost to produce each piston compared to older methods using carbide or other cutting tools.
Superior Performance and Wear Resistance on Aluminum Alloys
Think about cutting something soft like butter versus something with hard bits in it, like crunchy peanut butter. Aluminum alloys used in pistons, especially high-silicon aluminum (Al-Si), are a bit like that crunchy peanut butter for cutting tools. They contain hard silicon particles that can quickly wear down ordinary tools.
PCD, however, is one of the hardest materials known. It handles these hard silicon particles with ease.
- Exceptional Hardness: PCD’s structure allows it to cut through the hard silicon in the aluminum without rapidly dulling.
- Low Chemical Reactivity: Unlike some other tool materials, PCD doesn’t tend to chemically react with aluminum at high cutting temperatures. This prevents material from sticking to the tool edge (known as built-up edge), which helps maintain a clean cut and smooth surface.
- High Wear Resistance: This is where PCD truly shines on aluminum. It resists abrasion (wearing away) extremely well.
Consider how different tools hold up over time when machining high-silicon aluminum:
As the graph you can see here illustrates, PCD tools show very minimal flank wear (the wearing down of the tool’s side) even after extended cutting time. Compare this to other materials like CBN (Cubic Boron Nitride), which might be used for hard materials but wears down much faster when machining high-silicon aluminum. This dramatic difference in wear resistance is a primary reason PCD is preferred for this specific job.
Achieving Tighter Tolerances and Surface Finish Requirements
Why does less tool wear matter so much? Imagine trying to draw a perfect circle with a pencil point that keeps getting shorter and wider – it’s impossible! It’s similar with machining.
- Maintaining Size (Tolerance): Pistons have features like ring grooves and pin bores that must be machined to very precise sizes (tight tolerances) to work correctly in an engine. Because PCD tools wear down so slowly, they hold their exact cutting shape for a long time. This means piston after piston can be machined to the same precise dimensions, reducing scrap parts.
- Creating Smooth Surfaces (Surface Finish): A sharp, unworn cutting edge produces a cleaner, smoother cut. PCD maintains its sharp edge far longer than materials like carbide when cutting aluminum. This results in pistons with exceptionally smooth surfaces (low Ra values), which is critical for engine performance and longevity, helping piston rings seal properly and reducing friction. Better surface finish can sometimes even reduce the need for later polishing steps.
Could you imagine an engine running efficiently if its piston rings couldn’t seal properly because the grooves were rough or the wrong size? That’s why consistent tolerances and finishes are non-negotiable.
Extending Tool Life and Reducing Downtime
This benefit follows directly from PCD’s incredible wear resistance.
- Longer Cutting Time: Simply put, PCD tools last much, much longer between changes than carbide tools when machining aluminum – often 10, 50, or even more times longer, depending on the specific application and material.
- Less Frequent Tool Changes: Every time a machine has to be stopped to change a worn tool, production halts. This is called downtime. Because PCD tools last so long, machines can run continuously for extended periods, drastically cutting down on non-productive time.
- Reduced Tool Inventory: While a single PCD tool might cost more initially than a carbide tool, far fewer PCD tools are needed over time.
Think about the impact: If a tool change takes 15 minutes and happens 10 times less often with PCD, that’s a significant amount of extra production time gained each shift. The actual tool life gains can vary based on the specific aluminum alloy, cutting conditions, and the PCD grade used, so it’s always wise to consult with your tooling supplier for expected performance in your specific setup.
Calculating the Impact
Let’s consider a simplified example (actual results will vary):
- Carbide tool life: 300 pistons
- PCD tool life: 15,000 pistons (50x longer)
- Tool change time: 10 minutes
Over 15,000 pistons:
- Carbide requires: 15,000 / 300 = 50 tool changes
- PCD requires: 15,000 / 15,000 = 1 tool change
- Time saved from fewer changes: (50 – 1) changes * 10 min/change = 490 minutes of extra production time.
This doesn’t even account for potentially faster cutting speeds with PCD!
Boosting Productivity and Lowering Cost-Per-Part
This is where all the previous benefits come together to impact the bottom line.
- Increased Throughput: Less downtime for tool changes directly means more pistons produced per hour or per shift. Furthermore, PCD’s ability to handle heat often allows for significantly higher cutting speeds and feed rates compared to carbide when machining aluminum, further boosting production output.
- Reduced Scrap: Tighter tolerances and more consistent machining mean fewer rejected parts.
- Lower Tooling Cost (Overall): Even though the upfront cost of a PCD tool is higher, its vastly longer life means the tooling cost per piston produced is often much lower than with carbide.
- Labor Savings: Less time spent changing tools means operators or automation systems can focus on other tasks.
Therefore, while the initial investment seems higher, the total cost to manufacture each piston often drops significantly when using PCD tools correctly. The specific percentage of cost savings or productivity increase depends heavily on the operation, so discussing your production goals with a tooling expert can help estimate the potential benefits accurately.
Comparing PCD vs. Carbide/Other Materials in Key Piston Applications
Let’s briefly summarize the matchup specifically for machining aluminum pistons, considering the key differences between PCD and Carbide2:
Feature | PCD (Polycrystalline Diamond) | Carbide (Tungsten Carbide) | CBN (Cubic Boron Nitride) |
---|---|---|---|
Wear Resistance (on Al-Si) | Excellent | Fair to Poor (esp. High Si) | Poor (not ideal for Al-Si) |
Tool Life (on Al-Si) | Very Long | Moderate to Short | Short |
Achievable Surface Finish | Excellent | Good (but degrades faster) | Good (but wears fast) |
Tolerance Holding | Excellent (very stable) | Good initially (degrades with wear) | Good initially (degrades fast) |
Potential Cutting Speed | Very High on Aluminum | Moderate | Moderate (limited by wear) |
Initial Tool Cost | Higher | Lower | Higher |
Cost Per Part | Often Lowest (due to life/speed) | Moderate | Often Highest (due to wear/cost) |
Primary Use | Non-ferrous (Al, Cu), Composites, Plastics | Ferrous (Steel, Iron), some Non-ferrous | Hardened Steels, Cast Iron, Superalloys |
(Note: Comparisons are relative and specific to machining typical aluminum piston alloys.)
As the table shows, while carbide is a versatile material, and CBN excels in hardened ferrous materials, PCD is uniquely suited for delivering top performance, longevity, and cost-effectiveness when machining the aluminum alloys used in automobile pistons. Its properties directly combat the challenges posed by this material, leading to the significant advantages discussed.
Which Specific Piston Features Benefit Most from PCD Machining?
Okay, we understand that PCD tools are generally beneficial for aluminum, but where exactly on an automobile piston do they make the biggest difference?
PCD tooling truly excels when machining several critical areas of an automobile piston that demand extreme precision. The most significant benefits are typically seen in the ring grooves, the pin bore, complex piston skirt profiles, and the piston top or crown, all features requiring very tight size control, superior surface finishes, and consistent shapes for peak engine performance and durability.
Precision Machining of Ring Grooves
Think of the rings on a piston like seals on a jar – they need a perfect groove to sit in to do their job. These grooves hold the piston rings3, which are vital for sealing the combustion chamber and controlling engine oil.
Why Precision Here is Critical
- Sealing: The width, depth, and especially the flatness and smoothness of the groove bottom directly impact how well the piston rings seal against the cylinder wall. Poor sealing means lost power and potentially burning oil.
- Ring Movement: The sides of the grooves must be perfectly perpendicular to the groove bottom to allow the rings to move freely without sticking or fluttering.
- Wear: A smooth, precise groove surface reduces wear on both the ring and the groove itself.
How PCD Excels with Ring Grooves
PCD tools, particularly specialized PCD grooving inserts, are ideal for this task because:
- They maintain sharp corners and the exact profile needed for the groove shape over long production runs due to minimal wear. Imagine trying to carve a perfect tiny square channel with a knife that stays perfectly sharp versus one that dulls quickly – the sharp knife wins every time.
- Their ability to create very smooth surface finishes (low Ra values) on the groove bottom and sides enhances sealing and reduces friction.
- They handle the interrupted nature of the cut (entering and exiting the material) very well without chipping easily.
Achieving the required tolerances, often measured in micrometers (µm), and surface finishes for ring grooves is significantly more consistent with PCD. Remember that specific achievable tolerances can depend on the machine, setup, and PCD tool specifics, so it’s good practice to verify expected results with your tooling provider.
Finishing Pin Bores to Exact Specifications
The pin bore is the hole running through the piston that holds the wrist pin (or gudgeon pin). This pin connects the piston to the connecting rod, which ultimately turns the crankshaft. It’s a crucial connection point.
Why Precision Here is Critical
- Alignment & Load: The pin bore must be perfectly round, straight, and precisely sized to ensure proper alignment and distribute the immense forces evenly. Any imperfection can lead to noise, excessive wear, or even failure.
- Smooth Operation: A very smooth surface finish inside the bore is necessary to allow the wrist pin to pivot smoothly with minimal friction and wear, ensuring quiet engine operation.
How PCD Excels with Pin Bores
PCD boring tools or reamers deliver outstanding results in pin bore finishing because:
- Their exceptional dimensional stability (due to low wear) ensures that hole after hole meets the tight diameter, roundness, and straightness specifications.
- They produce extremely fine surface finishes, often eliminating the need for subsequent operations like honing in some cases. This results in a bore surface perfect for the pin’s movement.
Think of drilling a hole with a high-quality, sharp drill bit versus a worn, wobbly one. The sharp bit creates a clean, round, smooth hole – that’s what PCD effectively achieves for the critical pin bore, maintaining consistency over thousands of parts.
Machining Complex Piston Skirt Profiles and Forms
The piston skirt is the side portion of the piston below the ring grooves. It guides the piston’s movement within the cylinder. Interestingly, piston skirts are often not perfectly round!
Why Precision Here is Critical
- Fit and Guidance: Skirts are frequently designed with complex profiles – slightly barrel-shaped or oval (cam-ground). This specific shape ensures the piston fits correctly in the cylinder bore across the engine’s wide operating temperature range, accounting for how different parts of the piston expand with heat. An incorrect profile can cause the piston to rock (piston slap) or scuff against the cylinder wall.
- Friction and Lubrication: The skirt’s surface finish and sometimes special coatings applied to it play a role in reducing friction and retaining oil for proper lubrication.
How PCD Excels with Skirt Profiles
Machining these complex, non-cylindrical shapes accurately requires a tool that maintains its cutting edge precisely.
- PCD turning inserts used in specialized machines can follow the complex programmed path to create the exact oval or barrel shape consistently, thanks to their high wear resistance.
- They produce the required smooth surface finish needed for proper lubrication and interaction with the cylinder wall, often being compatible with subsequent skirt coating processes.
Imagine tracing a complex shape – a tool that stays sharp and doesn’t wear allows for a much more accurate reproduction of the intended path compared to one that dulls and changes shape mid-cut.
Achieving Critical Flatness and Finish on Piston Tops
The piston top, also called the crown, faces the intense heat and pressure of combustion. Its shape and surface condition are crucial for engine efficiency and durability.
Why Precision Here is Critical
- Combustion: The shape of the piston crown (flat, domed, or with a recessed bowl, especially in diesel engines) directly influences how the air-fuel mixture burns. Precision ensures the intended combustion characteristics and compression ratio are achieved.
- Valve Clearance: Piston crowns often feature valve reliefs or pockets – indentations machined to provide clearance for engine valves as they open and close. The depth and location of these pockets must be exact to prevent catastrophic contact between the piston and valves.
- Heat Resistance & Carbon Buildup: A smooth, flat (or precisely contoured) surface resists uneven heating and reduces the tendency for carbon deposits to build up, which can harm performance over time.
How PCD Excels with Piston Tops
Whether face milling or turning the piston top:
- PCD tools can achieve excellent flatness specifications and very low surface roughness (Ra) values due to their sharp, durable cutting edges.
- When machining complex features like combustion bowls or valve pockets, PCD’s ability to maintain its form ensures these intricate geometries are reproduced accurately and consistently across many pistons.
Achieving a mirror-like finish or precise flatness on the piston crown using PCD contributes directly to optimized combustion and long-term engine health. As with other features, the exact level of flatness or finish achievable will depend on the entire machining system, and specific targets should be confirmed based on the tooling and machine capabilities.
What Are the Key Technical Considerations for Implementing PCD Tools Effectively?
Alright, so PCD tools sound promising for piston machining, but what technical details do engineers really need to nail down to make them perform reliably on the production floor?
Successfully using PCD tooling for making pistons isn’t just plug-and-play; it demands careful planning around several key technical points. Getting these right involves choosing the specific type (grade) of PCD and the tool’s shape (geometry) for the job, setting the machine’s cutting speeds and feeds correctly, using the best coolant approach, knowing how the tool wears down and keeping the process steady, and finally, making sure the machine tool itself is sturdy and precise enough for the task.
Selecting the Appropriate PCD Grade and Tool Geometry
Think of PCD like different types of sandpaper – some are fine for smooth finishing, others are coarse for heavy work. PCD tools also come in different “grades” and shapes (geometries). Understanding the main types of PCD cutting tools4 is essential.
Understanding PCD Grades
PCD grades mainly differ in the size of the tiny diamond crystals packed together and the type of material (binder) holding them.
- Finer Diamond Grains: These generally produce a sharper cutting edge, leading to smoother surface finishes. They are often excellent for finish machining operations like pin bores. However, they might be slightly less resistant to chipping in rough or interrupted cuts.
- Coarser Diamond Grains: These grades are typically tougher and more resistant to chipping. This makes them suitable for rougher machining or cuts where the tool repeatedly enters and exits the material (interrupted cuts), like some grooving operations. The edge might not be quite as razor-sharp, potentially affecting the ultimate surface finish compared to fine grades.
- Binder Material: The metallic binder holding the diamond particles also influences the tool’s toughness and wear characteristics.
Key Tool Geometry Aspects
The shape of the cutting edge also matters greatly:
- Rake Angle: Influences how the metal chip flows away from the cut and affects cutting forces.
- Clearance Angle: Prevents the non-cutting part of the tool from rubbing against the freshly machined surface.
- Edge Preparation: Sometimes the very edge of the PCD is slightly rounded (honed) or angled (chamfered) to make it stronger and prevent tiny chips. For the best finish on aluminum, however, a very sharp, unprepared edge is often preferred.
Making the Right Choice
The key is matching the grade and geometry to the specific task on the piston. A fine-finishing operation needs a different tool design than a rough-machining step. Because the options and their performance can differ between manufacturers, it’s crucial to consult with your tooling supplier. They can recommend the best PCD grade and geometry for your specific aluminum alloy, the feature you’re machining (e.g., groove, bore), and your desired outcome.
Optimizing Cutting Parameters (Speeds, Feeds, Depth of Cut)
Once you have the right tool, you need to tell the machine how fast to use it. This involves setting the cutting parameters:
- Cutting Speed: How fast the tool edge moves across the material surface (often measured in meters per minute or surface feet per minute). PCD generally thrives at much higher cutting speeds on aluminum compared to carbide tools, thanks to its heat resistance.
- Feed Rate: How quickly the tool advances along its path or into the material (often measured in millimeters per revolution or per minute). This impacts surface finish and how quickly the job gets done.
- Depth of Cut: How much material the tool removes in a single pass. Deeper cuts remove material faster but put more stress on the tool and machine.
Finding the “sweet spot” for these parameters is essential. Running too fast or feeding too aggressively can risk breaking the PCD tool or causing rapid wear. Running too slowly makes the process inefficient. Exploring resources on specific tool types, like PCD reamer cutting parameters5, can provide valuable insights.
Suppliers provide recommended starting parameters, but optimization often involves careful testing. You adjust the settings incrementally to find the best balance between making parts quickly (productivity), ensuring the parts meet quality standards (finish and tolerance), and making the tool last as long as possible (tool life). Keep in mind that optimal parameters aren’t universal; they depend heavily on the PCD tool details, the machine’s condition, the coolant used, and the exact type of aluminum being cut. Always use supplier recommendations as a starting point and perform controlled tests to fine-tune for your specific production environment.
Effective Coolant and Lubrication Strategies for PCD
Using the right fluid during machining (coolant/lubricant) is important for several reasons:
- Cooling: It carries away heat generated during cutting, helping to maintain consistent temperatures and prolong tool life (even though PCD handles heat well, stability helps).
- Lubrication: It reduces friction between the tool, the chip, and the workpiece.
- Chip Evacuation: Critically important with aluminum! Coolant helps flush away the metal chips produced during cutting, preventing them from clogging up the cutting zone, damaging the tool edge, or marring the part surface.
Coolant Options for PCD on Aluminum
- Flood Coolant: The most common method uses water-soluble oil emulsions flooded over the cutting area. Good filtration is vital to keep the coolant clean.
- High-Pressure Coolant (HPC): Directing coolant at high pressure precisely at the cutting zone is very effective for removing sticky aluminum chips, especially in confined spaces like grooves or deep bores. Sometimes this is delivered through channels inside the tool itself (through-tool coolant).
- Minimum Quantity Lubrication (MQL): Uses a tiny amount of oil mixed with compressed air, creating a mist, a technique known as Minimum Quantity Lubrication (MQL). This can be effective, reduces fluid consumption, and leaves parts cleaner, but may offer less cooling and chip flushing than flood coolant.
The choice depends on the machine, the specific operation (grooving vs. face milling), and desired outcome. For instance, HPC might be essential for deep pin bore finishing. Consulting with both your tooling supplier and a coolant specialist can help determine the most effective strategy, including coolant type, concentration, pressure, and delivery method.
Managing Tool Wear Mechanisms and Ensuring Process Stability
Even super-hard PCD tools don’t last forever. Understanding how they wear helps you plan for tool changes before problems occur.
Common Ways PCD Wears (Simplified)
- Abrasive Wear: This is the most common type when machining aluminum. The hard silicon particles in the alloy gradually grind away the diamond edge over time, a classic example of abrasion6. This is usually slow and predictable with the right PCD grade.
- Chipping: Small pieces of the cutting edge break away. This can happen due to vibrations, an unstable setup, hitting a hard spot in the material, or using a PCD grade that isn’t tough enough for the application (e.g., a very fine grade in a heavy cut).
- Fracture: Complete breakage of the PCD tip. This is rare if everything is set up correctly and usually points to a major issue like a machine crash, a defective tool, or severe instability.
Keeping the Process Stable
Predictable abrasive wear is manageable. Unpredictable chipping or fracture causes scrap parts and stops production unexpectedly. Process stability aims for predictable wear. This comes from:
- Using the correct PCD grade and geometry.
- Running optimized, stable cutting parameters.
- Ensuring the machine and workholding are rigid (see next point).
- Monitoring the tool edge condition (visually with magnification) or tracking changes in part size or surface finish.
- Planning tool changes based on expected life, rather than running until failure.
Understanding Machine Tool Requirements and Rigidity Needs
Using advanced tools like PCD effectively often requires capable machinery. PCD tools perform best in a stable, precise environment. Because PCD is very hard but also somewhat brittle compared to steel tools, it doesn’t tolerate excessive vibration or instability well.
- Machine Rigidity: The machine tool itself – its base, columns, and spindle housing – must be stiff and robust. Machine Rigidity is essential to resist bending or vibrating under the cutting forces. Older or less rigid machines might limit the potential cutting parameters for PCD.
- Spindle Quality: A high-quality machine spindle is essential. It should be well-balanced for high speeds, have minimal runout (meaning the tool tip doesn’t wobble as it spins), and provide consistent power.
- Workholding: How the piston is held during machining is critical. The fixture must clamp the piston securely and rigidly, preventing any vibration or movement during the cut. Any looseness here will likely lead to poor surface finish, inaccurate dimensions, and potentially damaged PCD tools.
- CNC Control: Modern, fast Computer Numerical Control (CNC)7 systems are needed to handle the high speeds and precise movements often used with PCD tooling, especially when machining complex profiles like piston skirts.
Essentially, trying to use high-performance PCD tools on an old, worn, or insufficiently rigid machine may not yield the expected benefits and could even lead to tool failures. The entire system – machine, fixture, tool holder, and PCD tool – must work together harmoniously.
How Have Others Successfully Integrated PCD Tools into Piston Production Lines?
It’s great to know the theory, but have automotive companies actually put PCD tools to work on pistons and seen real, positive results in their factories?
Absolutely. Many automotive manufacturers and their suppliers have successfully adopted PCD tooling for piston machining, reporting significant and measurable improvements. Real-world applications consistently demonstrate better quality control for critical features like ring grooves, dramatic increases in production speed for operations like pin bore finishing, and substantial overall gains in how long tools last and how efficiently the process runs.
Case Study Example: Improving Ring Groove Quality and Consistency
(Note: This example is illustrative of typical results achieved in the industry. Specific figures vary.)
Imagine a manufacturer making pistons for passenger cars. They were using traditional carbide tools to machine the ring grooves. However, they faced challenges:
- The width of the grooves sometimes varied slightly outside the allowed tiny tolerance.
- The surface finish inside the grooves wasn’t always smooth enough, potentially affecting how well the piston rings could seal.
- The carbide tools wore down relatively quickly, needing frequent changes, which sometimes introduced slight variations in the groove dimensions after a tool change.
The Shift to PCD
Working with a tooling specialist, they decided to implement PCD grooving tools specifically designed for their high-silicon aluminum pistons. This involved:
- Selecting the right PCD grade known for edge retention and finish quality.
- Ensuring their machines were rigid and stable enough (as discussed in technical considerations).
- Optimizing the cutting speed and feed rate for the PCD tool.
The Reported Outcomes
After implementing the PCD solution, the manufacturer observed significant improvements:
- Improved Quality: The ability to hold the tight width tolerance for the ring grooves became much more consistent, drastically reducing the number of rejected pistons. Process capability studies showed a marked improvement. The surface finish inside the grooves was also consistently smoother, meeting the demanding specifications required for optimal ring sealing.
- Enhanced Consistency: The most dramatic change was tool life. Where the carbide tools might have reliably machined, say, 500-1000 pistons per cutting edge, the PCD tools often lasted for 20,000-30,000 pistons or more. This huge increase meant far fewer machine stops for tool changes, leading to a much more stable and predictable production flow.
This type of outcome – better quality and consistency through dramatically longer tool life – is a common report when PCD is correctly applied to demanding features like ring grooves. Of course, the exact tool life and quality improvements depend heavily on the specific application, so consulting with a supplier for projections based on your setup is recommended.
Case Study Example: Increasing Throughput in Pin Bore Finishing Operations
(Note: This example is illustrative of typical results achieved in the industry. Specific figures vary.)
Consider another scenario: a high-volume piston producer needed to increase the speed of their pin bore finishing operation. The pin bore requires excellent roundness, straightness, and a very fine surface finish. Their existing process using carbide reaming or boring was accurate but relatively slow, creating a bottleneck in the production line. Tool life was also a limiting factor, causing frequent downtime.
Implementing a PCD Solution
They explored using PCD tooling, either PCD-tipped reamers or PCD fine boring tools. The goal was to leverage PCD’s ability to cut aluminum at much higher speeds while maintaining accuracy and finish. This involved:
- Selecting PCD tools designed for high-speed finishing of bores.
- Confirming their boring machines and spindles could handle the higher rotational speeds accurately.
- Adjusting cutting parameters significantly – increasing cutting speed substantially while setting the feed rate to achieve the target surface finish.
The Reported Outcomes
The transition to PCD yielded major gains in production speed:
- Faster Cutting: They were able to increase cutting speeds significantly, sometimes two to three times faster (or more) than what was reliably possible with their previous carbide tools.
- Reduced Cycle Time: The combination of faster cutting and the elimination of most tool-change downtime slashed the time it took to finish the pin bore on each piston.
- Increased Throughput: The overall output of finished pistons from the pin bore station increased substantially – perhaps by 30-50% or even more in some optimized cases – effectively removing the production bottleneck. Tool life, similar to the grooving example, increased exponentially, further contributing to the uptime.
This demonstrates how PCD doesn’t just improve quality; it can fundamentally increase the production capacity of existing equipment when applied strategically to operations like pin bore finishing. Again, actual speed and throughput gains are application-specific, and validation with your tooling provider is key.
Real-world Data Snapshot: Documented Performance Gains
Looking across various applications in the automotive industry, the successful implementation of PCD tooling for aluminum piston machining typically yields performance gains in several key areas. While specific numbers vary widely, here’s a general snapshot of commonly reported improvements compared to traditional carbide tooling:
- Tool Life: Increases are often dramatic, ranging anywhere from 10x to over 100x longer life per cutting edge. This is arguably the most significant and consistent benefit reported.
- Cutting Speeds: Depending on the operation and machine capability, speeds can often be increased by 2x to 5x, sometimes even more, leading to shorter cycle times.
- Surface Finish: PCD consistently produces smoother surface finishes (lower Ra values) on aluminum alloys, often meeting specifications that are difficult or impossible to maintain consistently with carbide as it wears.
- Dimensional Stability: Due to minimal wear, PCD tools hold size much more accurately over long runs, leading to improved process capability indices (Cpk)8 and reduced scrap rates.
- Productivity & Cost-Per-Part: The combined effects of longer tool life, faster speeds, and reduced scrap almost always result in higher overall productivity and a lower manufacturing cost for each finished piston, despite the higher initial cost of PCD tools.
It is crucial to remember that these are general industry observations. The actual results achievable in your specific production environment depend heavily on factors like:
- The exact aluminum alloy being machined.
- The condition and rigidity of your machine tools.
- The specific PCD grade and tool geometry selected.
- The optimized cutting parameters used.
- The effectiveness of the coolant strategy.
Therefore, while these snapshots show the potential, working closely with experienced tooling suppliers and conducting performance trials on your own equipment are essential steps to verify the benefits for your unique situation.
Where Can You Source Reliable PCD Tooling Solutions for Piston Processing?
Now that you understand the benefits and technical aspects, if you’re considering PCD tools for piston machining, how do you go about finding the right tools and a dependable supplier?
Finding the best PCD tooling for making pistons involves carefully checking potential suppliers for important qualities like their technical know-how and support, and also understanding the key differences between standard, ready-made tools and custom tools designed specifically for your factory’s needs.
Key Factors When Evaluating a PCD Tool Supplier
Choosing a supplier for something as critical as PCD tooling, especially for high-volume automotive parts like pistons, goes beyond simply looking at the price tag on a tool. Here are some key things to consider:
- Technical Expertise: Does the supplier truly understand piston machining? Do they know the challenges of cutting high-silicon aluminum alloys? Can they discuss specific features like ring grooves or pin bores intelligently? A good supplier acts more like a knowledgeable partner than just a salesperson. Think of it like choosing a specialist doctor – you want one who deeply understands your specific condition.
- Application Knowledge: Can they recommend the right PCD grade and tool geometry for your specific piston design and material? Can they offer advice based on experience with similar applications?
- Product Quality and Consistency: How do they guarantee that every tool performs reliably? Ask about their quality control processes and how they ensure the PCD material itself is consistent from batch to batch. A tool that works great once but poorly the next time isn’t helpful.
- Technical Support: What happens if you run into challenges during setup or production? Does the supplier have technical staff who can help troubleshoot issues, optimize cutting parameters, or analyze why a tool might be wearing unexpectedly? This support can be incredibly valuable.
- Customization Ability: Can they design and build special tools if a standard item isn’t quite right for your needs? (We’ll discuss this more next).
- Reliability and Lead Time: Can they deliver high-quality tools consistently and within a reasonable timeframe to keep your production line running smoothly? Unexpected delays can be costly.
- Industry Experience: Do they have a proven track record working with automotive companies, or specifically with piston manufacturers? Experience in your industry often means they better understand the demands and standards.
Evaluating suppliers on these factors helps ensure you find a partner who can provide not just tools, but effective tooling solutions.
Navigating Standard vs. Custom PCD Tooling Options
When you look for PCD tools, you’ll generally encounter two main categories: standard tools and custom tools. Understanding the difference helps you choose wisely.
Standard (Catalog) PCD Tools
- What They Are: These are pre-designed tools, often based on industry standards (like ISO specifications for turning inserts), that a supplier keeps in stock or lists in their regular catalog. Examples might include common sizes of PCD-tipped turning inserts, end mills, or standard reamer diameters.
- The Upside: They usually have a lower purchase price per tool compared to custom ones. They are often available much more quickly since they don’t need to be designed from scratch. They can be great for general applications, initial trials, or less complex machining tasks.
- The Downside: A standard tool might not be perfectly optimized for your unique piston feature or machining process. The available choices for specific PCD grades or exact geometries might be limited compared to what could be custom-made.
Custom (Engineered) PCD Tools
- What They Are: These tools are designed and manufactured specifically for one customer’s particular application. This could mean:
- A grooving tool with a unique profile to match a special ring groove shape.
- A “combination tool” designed to machine multiple features (like drilling and chamfering) in a single step to save time.
- A tool body shaped uniquely to reach difficult areas on the piston.
- A specific blend of PCD grade and edge preparation optimized through testing for maximum life on your specific aluminum alloy.
- The Upside: They are designed for maximum performance in your specific situation. This can lead to significantly better tool life, faster cycle times, improved part quality, or the ability to solve a machining challenge that standard tools couldn’t handle. They can sometimes consolidate multiple steps into one, simplifying the process.
- The Downside: Custom tools naturally cost more upfront due to the design and engineering effort involved. They also take longer to get initially because they need to be designed, approved, manufactured, and sometimes tested. Success with custom tools relies on clear communication and collaboration between your engineers and the supplier’s technical team.
Which Path to Choose?
The choice often depends on the specific operation and production volume.
- For straightforward tasks or lower volume production, standard PCD tools might be perfectly adequate and cost-effective.
- For high-volume, critical operations where small improvements in cycle time or tool life translate into large cost savings, or where unique features require specialized solutions, investing in custom PCD tools is often easily justified by the long-term performance benefits and lower cost-per-part.
Discussing your specific needs, production goals, and challenges with knowledgeable suppliers will help you determine whether standard or custom PCD tools are the right fit for each step in your piston machining process. Remember that factors like lead time and cost for custom tooling can vary, so getting clear quotes and timelines from potential suppliers is essential.
Conclusion
In summary, Polycrystalline Diamond (PCD) tooling represents a powerful technology for optimizing the production of automobile pistons, particularly when machining the challenging aluminum alloys commonly used. By offering superior wear resistance, enabling tighter tolerances and finer finishes, extending tool life dramatically, and boosting overall productivity, PCD tools can lead to significant improvements in both part quality and manufacturing cost-effectiveness. However, realizing these benefits requires a thoughtful approach: understanding which specific piston features gain the most, carefully managing the technical aspects of implementation like tool selection and cutting parameters, learning from real-world applications, and selecting the right tooling partner and solution type – whether standard or custom – for your specific needs. When applied correctly, PCD tooling is a key enabler for efficient, high-quality piston manufacturing.
References
- Polycrystalline Diamond (PCD)1 – Wikipedia article defining Polycrystalline Diamond and its properties.
- differences between PCD and Carbide2 – ZYDiamondTools blog post comparing PCD and Carbide cutting tools.
- piston rings3 – Wikipedia article explaining the function and types of piston rings in internal combustion engines.
- types of PCD cutting tools4 – ZYDiamondTools blog post discussing different types of PCD tools and selection criteria.
- PCD reamer cutting parameters5 – ZYDiamondTools blog post providing information on cutting parameters specifically for PCD reamers.
- abrasion6 – Wikipedia section defining abrasive wear as a mechanism of material loss.
- Computer Numerical Control (CNC)7 – Wikipedia section defining Computer Numerical Control in manufacturing.
- process capability indices (Cpk)8 – American Society for Quality (ASQ) resource page explaining process capability, including Cpk.
ZY Superhard Tools Co., Ltd.
Do you have any needs for PCD tools or diamond grinding wheels? We can customize products to meet your specific requirements. If you have any ideas or requests, feel free to reach out—we’ll respond within 24 hours!
Do you have any needs for PCD & CBN tools or diamond grinding wheels? We can customize products to meet your specific requirements. If you have any ideas or requests, feel free to reach out—we’ll respond within 24 hours!
Do you have any needs for PCD & CBN tools or diamond grinding wheels? We can customize products to meet your specific requirements. If you have any ideas or requests, feel free to reach out—we’ll respond within 24 hours!
Post Categories
Product Categories
About Company
Related Posts
Which Turning Insert Shape Should You Choose?
Master turning insert selection. Our guide covers choosing the right shape for your job, decoding ISO codes, and selecting the
How Do You Solve Vibration, Chip Control, and Surface Finish Issues in PCD Grooving?
Solve common PCD grooving problems. This guide details how to fix vibration, improve chip evacuation, and achieve a flawless sidewall
Why Is Your Tooling Wearing Out Prematurely? A Machinist’s Guide to Key Causes & Proven Solutions
Facing premature tool wear? Learn the key causes like heat, vibration, & wrong parameters. Discover proven solutions from setup to
How Do You Select the Optimal PCD Tools for Scroll Compressor Machining?
Learn how to select the right PCD tools for scroll compressor machining. This guide covers the benefits over carbide, key
Subscribe
Simply enter your email below and click “Subscribe” to stay connected with everything new and exciting.