-
Whatsapp: +86 13526572721
-
Email: info@zydiamondtools.com
-
Address: AUX Industrial Park, Zhengzhou City, Henan Province, China
-
Whatsapp: +86 13526572721
-
Email: info@zydiamondtools.com
-
Address: AUX Industrial Park, Zhengzhou City, Henan Province, China
Machining Nickel-Based Superalloys: Tooling Selection and Case Studies
- Industry Knowledge, Knowledge, PCD & CBN Tools Knowledge
- -2025-07-18
- - byKevin Ray
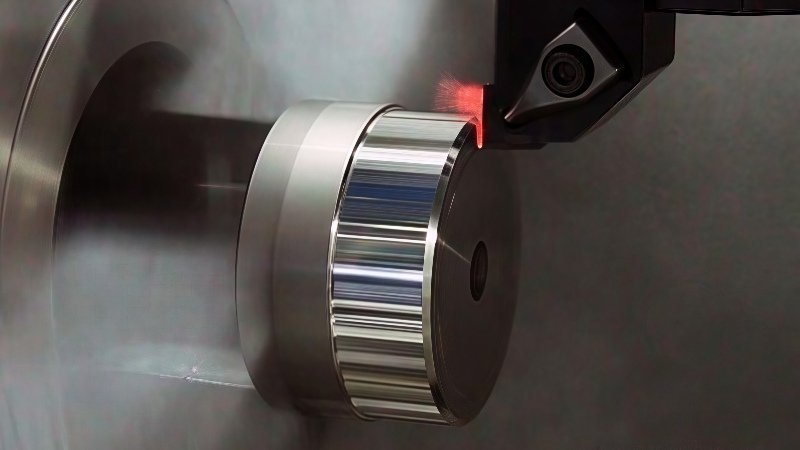
So, how can you successfully machine difficult nickel-based superalloys without constant tool failure and project delays?
Successfully machining nickel-based superalloys requires a systematic approach that addresses the material’s core challenges. This involves first understanding why they are difficult to cut—due to high-temperature strength, work hardening, and poor thermal conductivity. Next, it requires selecting the appropriate cutting tool material (carbide, ceramic, or PCBN) for the specific task. Finally, success is achieved by optimizing cutting parameters like speed and feed, implementing advanced coolant strategies, and learning from the practical application and failure analysis shown in real-world case studies.
Table of Contents
ToggleWhy is Machining These Alloys So Challenging?
So, what exactly makes nickel-based superalloys¹ so tough to machine?
Machining nickel-based superalloys is challenging primarily due to three material properties: their exceptional high-temperature strength, which resists deformation during cutting; their tendency to rapidly work-harden, which increases cutting forces and wears down tools; and their poor thermal conductivity, which concentrates intense heat at the cutting edge instead of dissipating it through the chip or workpiece.
The Core Problem of High-Temperature Strength
First and foremost, nickel-based superalloys are designed to perform in extreme heat. Think of a jet engine turbine blade spinning thousands of times per minute while glowing red-hot. These alloys must remain incredibly strong and resist changing shape under such conditions. This property is known as high-temperature strength or “hot hardness.”
The irony is that the very process of machining generates immense heat from friction between the cutting tool and the material. While this heat might soften a standard steel, making it easier to cut, it has little effect on a superalloy. You are essentially trying to cut a material that is engineered to resist the exact conditions you are creating.
For instance, Inconel 718, a widely used superalloy in the aerospace industry, retains approximately 80% of its room-temperature strength at temperatures up to 650°C (1200°F). This means the material maintains immense resistance to the cutting tool, demanding far greater cutting forces and putting enormous stress on the tool’s cutting edge.
Understanding Rapid Work Hardening
Have you ever bent a paperclip back and forth until it snapped? You might have noticed that the metal at the bend gets harder and more difficult to flex with each repetition. This is a simple example of work hardening. Nickel-based superalloys exhibit this behavior to an extreme degree, and it happens almost instantly during machining.
The pressure and heat from the cutting tool’s edge cause the crystal structure of the alloy to deform and harden on the spot. This means that with each pass, the tool is no longer cutting the original material but is instead engaging with a new, significantly harder surface that it just created.
This effect is not trivial. The work-hardened layer on an alloy like Inconel can be up to 100% harder than the parent material. This phenomenon is a primary cause of a specific type of tool wear known as “depth-of-cut notching,” where the tool wears down rapidly right at the point where it engages with this hardened layer. This requires specialized tool paths and strategies just to manage.
Dealing with Poor Thermal Conductivity and Heat Dissipation
Finally, a major challenge is that these materials are poor thermal conductors. In an ideal machining scenario, most of the heat generated would be carried away in the chips, protecting both the tool and the workpiece. With superalloys, the opposite happens.
Because the alloy doesn’t transfer heat well, the intense energy becomes concentrated in a very small area: the tool’s cutting edge. This can cause temperatures at the tool tip to skyrocket, often exceeding 1,100°C (2,000°F)—hot enough to compromise even the most advanced cutting tool materials. This localized heat is the main driver of tool failure through processes like diffusion wear, where atoms from the tool literally migrate into the workpiece material, dulling the edge.
To put this in perspective, consider how poorly these alloys conduct heat compared to more common metals.
Material | Thermal Conductivity (W/m·K) |
---|---|
Aluminum (6061) | ~167 |
Carbon Steel (1045) | ~51 |
Inconel 718 | ~11.4 |
As the table shows, Inconel 718 traps heat far more effectively than steel or aluminum. This single property fundamentally dictates the choice of cutting speeds, coolant strategies, and tool materials needed to successfully machine these advanced alloys.
Which Cutting Tool Material is Right for Your Application?
With these challenges in mind, how do you choose the right cutting tool material for the job?
Choosing the right cutting tool depends on the specific machining operation and budget. Coated carbides are the versatile choice for lower-speed operations and general-purpose work. Advanced ceramics, like SiAlONs, excel at high-speed roughing due to their superior hot hardness. For achieving the best surface finish and tightest tolerances, Polycrystalline Cubic Boron Nitride (PCBN) is the premium material for finishing operations.
Coated Carbides: The Reliable Workhorse
Think of coated carbides as the all-season tires of the machining world. They offer a fantastic balance of toughness (resistance to chipping) and wear resistance, making them a reliable and cost-effective choice for a wide range of applications. They are especially useful for operations with interruptions, such as milling, where the tool repeatedly enters and exits the material.
The real magic, however, lies in the coatings. Modern carbide inserts for superalloys use advanced multilayer coatings, most commonly PVD (Physical Vapor Deposition) TiAlN (Titanium Aluminum Nitride). Here’s how it works:
- At the high temperatures generated during cutting, this coating forms a microscopic, highly stable layer of aluminum oxide (Al₂O₃) on its surface.
- This new layer acts as an excellent thermal barrier, insulating the carbide substrate from the intense heat and slowing down wear.
Carbides are typically run at lower speeds than ceramics, often in the range of 25-60 m/min (80-200 SFM). Because specific coatings and carbide grades are highly engineered for different alloys and operations, it’s always wise to consult your tooling supplier’s recommendations to find the optimal parameters for your exact application.
Advanced Ceramics (SiAlONs & Whisker-Reinforced): For High-Speed Roughing
When the goal is to remove a large amount of material as quickly as possible (a process called roughing), advanced ceramics are the tool of choice. They possess incredible hot hardness, meaning they stay hard and sharp even at the extreme temperatures where carbides would fail. However, they are more brittle than carbides.
There are two main types you’ll encounter:
- SiAlONs: This is a special class of ceramic that offers excellent thermal shock resistance and maintains its strength at very high temperatures, making it ideal for high-speed machining of superalloys.
- Whisker-Reinforced Ceramics: These tools have a ceramic base (like aluminum oxide) that is reinforced with microscopic silicon carbide (SiC) “whiskers.” These whiskers act much like rebar in concrete, drastically increasing the tool’s toughness and stopping small cracks from spreading.
With ceramics, you can achieve remarkable metal removal rates by running at much higher speeds, often in the range of 200-350 m/min (650-1150 SFM). This makes them highly productive for roughing large components like aerospace engine casings. The trade-off? They require a very rigid and stable machine setup with continuous cutting paths to prevent the brittle inserts from fracturing.
PCBN/CBN Tooling: The Ultimate Choice for Finishing
When the final surface finish and dimensional accuracy are critical, Polycrystalline Cubic Boron Nitride (PCBN) tools are unmatched. Cubic Boron Nitride (CBN) is the second-hardest known material, surpassed only by diamond. Unlike diamond, however, PCBN is chemically stable when cutting iron-based materials, so it won’t degrade at high temperatures.
PCBN tools² is used almost exclusively for finishing operations. Its exceptional hardness allows it to create an incredibly smooth and accurate surface, often eliminating the need for later grinding operations, which saves significant time and money.
- Performance: It can achieve surface finishes of Ra 0.2–0.4 µm, which is exceptionally smooth.
- Application: Ideal for critical features like bearing journals, sealing faces, and other surfaces on high-value components where precision is non-negotiable.
While PCBN is the most expensive option per cutting edge, its long tool life in finishing applications and its ability to reduce the number of manufacturing steps often make it the most economical choice³ for producing high-precision parts.
How Can You Optimize Cutting Parameters to Prevent Tool Failure?
Once you’ve chosen the right tool, how do you set the machine’s parameters for the best results?
Optimizing cutting parameters involves a careful balance to manage heat and tool pressure. This means finding the right cutting speed to maximize productivity without prematurely burning out the tool, selecting an appropriate feed rate and depth of cut to ensure stability and prevent work hardening, and implementing an effective coolant strategy, such as high-pressure coolant (HPC), to control temperature and efficiently evacuate chips.
Balancing Cutting Speed vs. Tool Life
In machining, especially with superalloys, cutting speed is the single most significant factor affecting temperature and, consequently, tool life. Think of it as a trade-off between productivity and durability. While pushing the speed higher removes material faster, it exponentially increases heat at the cutting edge, which can destroy a tool in minutes.
The goal is to find the “sweet spot.” For example, while a ceramic insert might be rated for a top speed of 300 m/min (1000 SFM), operating at that limit might only yield 2-3 minutes of tool life. However, by reducing the speed by just 20% to 240 m/min (800 SFM), it’s often possible to double or even triple the tool life. This small sacrifice in cycle time results in fewer tool changes, less machine downtime, and more consistent parts.
Finding this balance is key to profitability. Always start with the cutting speeds recommended by your tooling supplier, as they are tailored to the specific tool grade and coating. Then, monitor the tool wear and adjust the speed up or down in small increments to optimize for your specific machine and material batch.
Selecting the Optimal Feed Rate and Depth of Cut
While cutting speed manages heat, feed rate and depth of cut (DOC) are used to manage pressure and chip formation. Getting these wrong can be just as damaging as running too fast.
Setting the Right Feed Rate
The feed rate determines the thickness of the chip being removed. A common mistake is to reduce the feed rate too much in an attempt to be “gentle” on the tool. This is often counterproductive. A feed rate that is too low causes the tool to rub against the material instead of cutting it cleanly. This rubbing action generates intense friction and heat, which in turn causes the rapid work hardening we seek to avoid.
It is crucial to use a feed rate that is high enough to ensure a proper “bite” into the material, forming a clean chip and minimizing this damaging rubbing effect.
Using Depth of Cut to Your Advantage
The depth of cut is a powerful tool for combating work hardening. As we learned earlier, machining creates a hardened layer on the part’s surface. To maintain efficiency and protect your tool, the next pass must cut underneath this layer.
A critical rule of thumb: Always set your depth of cut deeper than the work-hardened zone from the previous pass.
If your DOC is too shallow, your tool will be trying to cut through the hardest possible material, leading to rapid notching and failure. By taking a deeper—but stable—cut, the tool engages with the softer parent material beneath the hardened skin, dramatically improving tool life and performance.
Implementing Effective Coolant Strategies (HPC & Cryogenic)
With superalloys, managing heat is everything. Standard flood coolant, which simply pours fluid over the cutting area, is often not enough. The intense heat can create a vapor barrier around the tool, preventing the coolant from ever reaching the cutting edge. This is why more advanced strategies are necessary.
Coolant Strategy | How It Works | Primary Benefit |
---|---|---|
Flood Coolant | Low-pressure fluid flows over the part. | General cooling and chip flushing. |
High-Pressure Coolant (HPC) | A high-pressure jet (70-140 bar / 1000-2000 PSI) is aimed directly at the cutting edge. | Breaks the vapor barrier, cools effectively, and aggressively evacuates chips. |
Cryogenic Machining | Liquid nitrogen (-196°C / -321°F) is used as a coolant. | Drastically reduces heat, improves tool life, and enhances surface integrity. |
High-Pressure Coolant (HPC) is now a standard practice for serious superalloy machining. The high-pressure stream acts like a hydraulic wedge, getting under the chip to cool the insert directly and blast the chip away from the cutting zone. This prevents the hot chip from damaging the workpiece and stops the tool from recutting chips—a major cause of unpredictable tool failure.
Cryogenic Machining is an even more advanced method. By using liquid nitrogen to super-cool the cutting zone, it offers the ultimate in thermal control. While more complex and costly to implement, it can provide significant gains in tool life and part quality, especially for next-generation alloys.
What Can We Learn From Real-World Machining Examples?
So how does all this theory apply to a real-world machine shop?
Real-world examples demonstrate how a systematic approach leads to success. A case study on turning Inconel 718 for aerospace can demonstrate a high-performance, hard-turning strategy using PCBN tooling to achieve a superior finish and eliminate grinding. In contrast, milling GH4169 will showcase a high-speed roughing strategy with ceramic tools.
Case Study 1: Turning Inconel 718 for Aerospace Components
This example focuses on a high-performance finishing strategy for a critical turbine component made from Inconel 718. The primary goals are to achieve exceptional surface finish and tight tolerances in a single operation, thereby eliminating a costly and time-consuming subsequent grinding process.
The chosen strategy leverages the superior hot hardness and wear resistance of PCBN tooling, allowing for higher cutting speeds and resulting in a mirror-like finish.
Parameter | Specification |
---|---|
Material | Inconel 718 (Aged Condition) |
Operation | CNC Lathe Finishing (Hard Turning⁴) |
Tool | PCBN Insert (with solid CBN tip) |
Cutting Speed | 220 m/min (720 SFM) |
Feed Rate | 0.10 mm/rev (0.004 in/rev) |
Depth of Cut | 0.25 mm (0.010 in) |
Coolant | High-Pressure Coolant @ 80 bar (1160 PSI) |
Result: This high-speed finishing strategy was a remarkable success. It produced a consistent surface finish of Ra 0.3 µm, meeting the most stringent aerospace specifications. The tool life was excellent, averaging 25 minutes per cutting edge. Most importantly, the quality achieved completely eliminated the need for a separate grinding operation, which simplified the entire manufacturing workflow and reduced the total cost per part significantly. This case perfectly illustrates the economic and quality benefits of applying the right advanced tooling.
Case Study 2: Milling GH4169 with Ceramic Inserts
Here, the objective is different: high-efficiency roughing of a forged block of GH4169 (an alloy similar to Inconel 718) for a power generation component. The main goal is the highest possible Metal Removal Rate (MRR)⁵ to reduce cycle time.
This application is perfect for whisker-reinforced ceramics, which thrive at high temperatures. The strategy uses very high speeds with a lighter depth of cut.
Parameter | Specification |
---|---|
Material | GH4169 (Forged) |
Operation | 5-Axis Face Milling (Roughing) |
Tool | Whisker-Reinforced Ceramic (RNGN geometry) |
Cutting Speed | 280 m/min (920 SFM) |
Feed Rate | 0.1 mm/tooth (0.004 in/tooth) |
Depth of Cut | 2.0 mm (0.080 in) |
Coolant | High-volume compressed air (to clear chips) |
Result: This high-speed strategy increased the MRR by over 300% compared to the previous carbide process. Tool life was a predictable 20 minutes of in-cut time, allowing for scheduled tool changes before failure. The success depended on two factors: the extreme rigidity of the 5-axis machine and a tool path that kept the ceramic insert constantly engaged in the material to avoid thermal shock from repeated entry and exit.
Key Takeaways and Failure Analysis from Worn Tools
The most important lessons often come from examining a tool after it has been used. A worn tool tells a story about the process. Here’s how to read the evidence:
Flank Wear (The Good Wear)
- What it looks like: A uniform, flat, shiny area along the side of the cutting edge.
- What it means: This is predictable wear. It shows that your parameters are well-balanced, and heat and pressure are under control. This is the type of wear you want to see.
Depth-of-Cut Notching (The Bad Wear)
- What it looks like: A distinct, localized groove chipped into the cutting edge, right at the depth of the cut.
- What it means: This is the classic signature of work hardening. Your tool is rubbing on the hardened layer from the previous pass. The most likely cause is a depth of cut that is too shallow.
- How to fix it: Increase the depth of cut to get underneath the hardened zone.
Chipping or Fracture (The Ugly Wear)
- What it looks like: The cutting edge is broken, chipped, or has completely fractured. This is a catastrophic failure.
- What it means: The tool experienced excessive pressure or shock. Common causes include an unstable setup, a feed rate that is too high, or using a brittle tool (like ceramic) in a heavily interrupted cut.
- How to fix it: Check the rigidity of your setup, reduce the feed rate, or switch to a tougher tool grade.
Conclusion
Mastering the machining of nickel-based superalloys is not about finding a single secret weapon. Instead, it is about building a comprehensive strategy. Success comes from methodically layering knowledge: understanding the fundamental challenges the material presents, selecting the correct tool for the specific job—whether for roughing or finishing—and carefully optimizing cutting parameters to balance productivity with reliability.
By treating each application as a system and learning to read the feedback from your worn tools, you can move from struggling with these materials to machining them with confidence and predictability. The principles and case studies outlined here provide a roadmap to developing that expertise and achieving consistent, high-quality results.
References
- nickel-based superalloys¹ – An academic overview of nickel-based superalloys from ScienceDirect, covering their properties and applications.
- PCBN tools² – The main product category page for all PCBN and PCD tools offered by ZYDiamondTools.
- most economical choice³ – An article from ZYDiamondTools explaining the concept of Total Cost of Ownership (TCO) for tooling.
- Hard Turning⁴ – A detailed ZYDiamondTools guide explaining the hard turning process and its advantages over grinding.
- Metal Removal Rate (MRR)⁵ – A Wikipedia article providing a clear definition and formulas for Material Removal Rate in machining.
ZY Superhard Tools Co., Ltd.
Do you have any needs for PCD tools or diamond grinding wheels? We can customize products to meet your specific requirements. If you have any ideas or requests, feel free to reach out—we’ll respond within 24 hours!
Do you have any needs for PCD & CBN tools or diamond grinding wheels? We can customize products to meet your specific requirements. If you have any ideas or requests, feel free to reach out—we’ll respond within 24 hours!
Do you have any needs for PCD & CBN tools or diamond grinding wheels? We can customize products to meet your specific requirements. If you have any ideas or requests, feel free to reach out—we’ll respond within 24 hours!
Post Categories
Product Categories
About Company
Related Posts
How Do You Solve Vibration, Chip Control, and Surface Finish Issues in PCD Grooving?
Solve common PCD grooving problems. This guide details how to fix vibration, improve chip evacuation, and achieve a flawless sidewall
Why Is Your Tooling Wearing Out Prematurely? A Machinist’s Guide to Key Causes & Proven Solutions
Facing premature tool wear? Learn the key causes like heat, vibration, & wrong parameters. Discover proven solutions from setup to
How Do You Select the Optimal PCD Tools for Scroll Compressor Machining?
Learn how to select the right PCD tools for scroll compressor machining. This guide covers the benefits over carbide, key
How Do You Choose the Right Cutting Tool for Your Mold Steel Machining?
Learn how to choose the right cutting tools for mold steel machining. This guide covers steel hardness, tool materials, coatings,
Subscribe
Simply enter your email below and click “Subscribe” to stay connected with everything new and exciting.