-
Whatsapp: +86 13526572721
-
Email: info@zydiamondtools.com
-
Address: AUX Industrial Park, Zhengzhou City, Henan Province, China
-
Whatsapp: +86 13526572721
-
Email: info@zydiamondtools.com
-
Address: AUX Industrial Park, Zhengzhou City, Henan Province, China
Choosing Your Diamond Tool: Polycrystalline (PCD) vs. Monocrystalline (MCD)
- Industry Knowledge, PCD & CBN Tools Knowledge
- -2025-04-21
- - byKevin Ray
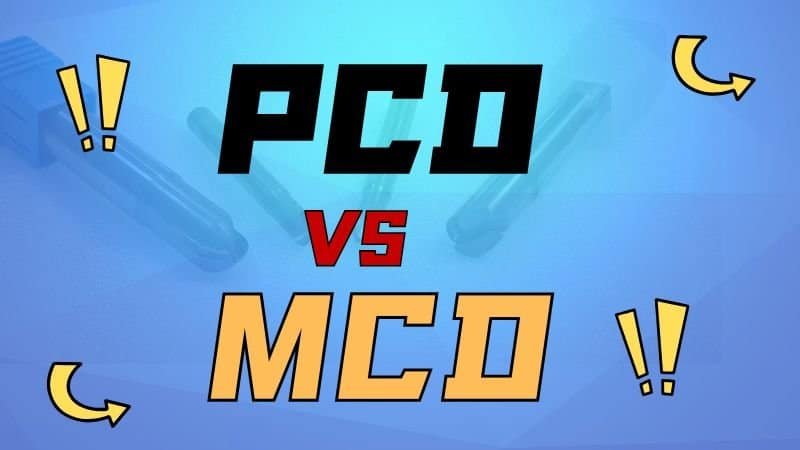
Trying to decide between Polycrystalline (PCD) and Monocrystalline (MCD) diamond tools for your machining needs?
Choosing between PCD and MCD diamond tools depends primarily on the material being machined, the required surface finish and tolerance, the specific machining operation, and cost-performance considerations; PCD excels in toughness and wear resistance for abrasive non-ferrous materials, while MCD offers unparalleled sharpness for mirror finishes on specific soft materials.
Table of Contents
ToggleWhat Are the Fundamental Differences Between PCD and MCD?
So, you’re looking at diamond tools and see “PCD” and “MCD”—what actually sets these two types of diamond apart at their core?
Polycrystalline Diamond (PCD)1 is made of many tiny synthetic diamond crystals fused together with a metal binder under high pressure and heat, creating a tough, wear-resistant composite. Monocrystalline Diamond (MCD)2, often called single-crystal diamond, is a single, continuous diamond crystal (either natural or synthetic) without grain boundaries or binders, allowing for an incredibly sharp edge but making it more brittle.
Let’s explore these fundamental distinctions in more detail.
Crystal Structure: Grain Boundaries vs. Single Crystal
The biggest difference between PCD and MCD lies right in their names and basic structure. Imagine looking at them under a powerful microscope.
- Polycrystalline Diamond (PCD): Think of PCD like a very strong composite material. It’s made up of many tiny, individual synthetic diamond crystals (the “grains”) that are randomly oriented and bonded together. Crucially, there’s also a metallic binder material (often cobalt) filling the spaces between the diamond grains. This structure means PCD has many “grain boundaries”—the interfaces where different diamond crystals meet each other and the binder.
- Monocrystalline Diamond (MCD): Now, picture a flawless natural diamond gemstone. MCD is just that—a single, unbroken diamond crystal lattice (natural or synthetic). There are no grain boundaries and no binder material. It’s pure diamond structure throughout.
This difference in structure—many grains with binder versus one continuous crystal—is the root cause of nearly all the other performance differences we’ll discuss.
Manufacturing Processes and Their Impact
How these materials are made also reveals key differences:
- PCD Manufacturing: PCD is typically produced through a process called High-Pressure High-Temperature (HPHT) sintering3. Fine diamond powder (micron-sized grains) is mixed with a metallic catalyst binder (like cobalt) and placed onto a carbide substrate. This assembly is subjected to extreme pressure (often over 5 GPa) and high temperature (around 1400-1600°C). Under these conditions, the binder melts and facilitates the bonding (sintering) between the diamond grains, forming a solid PCD layer bonded to the carbide base. The presence and type of binder significantly influence PCD’s properties.
- MCD Manufacturing: MCD tools historically used high-quality natural diamonds, carefully selected and oriented. Today, synthetic MCD is more common and consistent. Large, high-quality single diamond crystals are grown using either HPHT methods (different from PCD sintering, focused on growing one large crystal) or Chemical Vapor Deposition (CVD)4. These large crystals are then precisely cut using lasers or mechanical methods along specific crystallographic planes to create the tool’s shape and cutting edge. The orientation of the crystal lattice relative to the cutting edge is critical for MCD tool performance and wear characteristics.
Therefore, PCD is essentially a composite material engineered from diamond powder, while MCD is a shaped single crystal.
Hardness and Toughness Compared
Hardness (resistance to scratching or indentation) and toughness (resistance to fracture or chipping) are crucial mechanical properties for cutting tools. How do PCD and MCD stack up?
- Hardness: Both PCD and MCD are exceptionally hard, ranking among the hardest known materials. Pure diamond (like MCD) is technically the hardest. PCD’s hardness is very close, influenced slightly by the binder content and diamond grain size. For practical purposes in machining, both offer extreme resistance to abrasive wear.
- Toughness: This is where a major difference appears.
- PCD is significantly tougher than MCD. Think back to the structure: the randomly oriented grains and the metallic binder in PCD act like roadblocks for cracks. If a tiny crack starts, it has trouble traveling far because it keeps hitting grain boundaries, forcing it to change direction and expend more energy. The binder also adds some ductility compared to pure diamond. This makes PCD much more resistant to chipping and sudden fracture, especially under impact or vibration.
- MCD is very brittle. Because it’s a single, continuous crystal lattice, there are specific cleavage planes along which it can fracture relatively easily if subjected to impact, excessive force, or thermal shock. It’s very hard but can shatter more easily under adverse conditions.
Analogy: Trying to break a concrete block (PCD) versus a sheet of glass (MCD) illustrates the toughness difference. Both are hard, but the concrete takes much more abuse, while the glass can shatter from a sharp impact.
Important Note: Specific hardness (e.g., Knoop hardness values5) and fracture toughness values can vary between different grades of PCD (based on grain size and binder content) and specific orientations of MCD. Always consult the tool supplier’s specifications for the precise properties of the tool you are considering.
Thermal Conductivity Differences
Diamond boasts the highest thermal conductivity of any known material, meaning it’s excellent at drawing heat away from the cutting zone.
- MCD has higher thermal conductivity than PCD. As a pure, uninterrupted diamond lattice, heat can travel through MCD very efficiently.
- PCD’s thermal conductivity is lower (though still very high compared to other tool materials like carbide or steel). The presence of the metallic binder phase and the numerous grain boundaries act as slight barriers, scattering the heat flow (phonon scattering) and reducing the overall efficiency of heat transfer compared to a perfect single crystal.
What does this mean for machining? Better thermal conductivity helps pull heat away from the cutting edge more quickly. This can reduce the temperature right at the tip, potentially slowing down certain types of tool wear (like thermally activated chemical wear) and sometimes allowing for higher cutting speeds, especially in materials where heat generation is a major concern.
Achievable Edge Sharpness and Integrity
The ultimate sharpness of the cutting edge is dictated by the material’s structure at the microscopic level.
- MCD allows for an atomically sharp edge. Because it’s a single crystal, it can be cleaved or lapped along its crystallographic planes to produce an edge radius measured in nanometers (nm). There are no grain boundaries to interrupt the edge, resulting in a near-perfectly continuous and incredibly sharp cutting line.
- PCD edge sharpness is limited by grain size. The edge of a PCD tool is essentially formed by the profile of many tiny diamond grains held by the binder. The sharpness is therefore limited by the size of these grains (typically ranging from sub-micron to ~25 microns or more) and the slight irregularities where grains meet. While still very sharp compared to carbide, it cannot achieve the near-atomic sharpness of MCD.
This fundamental difference in achievable edge sharpness directly impacts the type of surface finish that can be generated and the minimum chip thickness possible, making MCD the go-to choice for applications demanding the absolute highest precision and mirror-like surfaces.
How Does Performance Vary in Machining Applications?
Okay, we know PCD and MCD are built differently, but how does that translate into actual results when the tool meets the workpiece?
In machining, PCD generally offers much longer tool life, especially in abrasive materials, and provides excellent finishes due to its toughness and wear resistance. MCD, while more fragile, delivers unparalleled mirror-like surface finishes and minimal cutting forces in specific applications owing to its extreme edge sharpness, but its tool life is highly conditional.
Let’s break down these performance differences across key areas.
Tool Life Expectancy: PCD vs. MCD
How long can you expect these tools to last? The answer heavily depends on what you’re cutting and how you’re cutting it.
- PCD Tool Life: When machining its preferred materials—highly abrasive non-ferrous metals like high-silicon aluminum alloys, metal matrix composites (MMCs), or even abrasive plastics and green ceramics—PCD offers exceptional tool life. It’s not uncommon for PCD tools to last 50 to 100 times longer (or even more) than comparable cemented carbide tools in these challenging applications. Its high hardness resists abrasive wear, and its toughness resists the chipping that quickly dulls other materials. This longevity leads to significant cost savings through reduced tool changes, less machine downtime, and more consistent part quality over long production runs. For example, in high-volume automotive machining of aluminum engine blocks or pistons, PCD is the standard choice precisely because of its predictable, extended lifespan.
- MCD Tool Life: MCD tool life is a different story; it’s highly conditional and application-specific. In its ideal niche—ultra-precision continuous turning or fly-cutting of soft, clean non-ferrous metals (like Oxygen-Free High Conductivity – OFHC copper or high-purity aluminum for optics) under very stable conditions—MCD can achieve respectable tool life. However, because it’s brittle, MCD is very sensitive. Any unexpected vibration, impact (like hitting a hard inclusion in the material), improper handling, or attempting to cut unsuitable materials can lead to sudden, catastrophic failure (chipping or fracture) and zero effective tool life. Its lifespan relies entirely on maintaining perfect cutting conditions.
Key Takeaway: If your priority is maximum tool life while cutting abrasive non-ferrous materials, PCD is typically the clear winner. MCD’s life depends critically on perfect conditions and suitable materials. Remember that factors like the specific PCD grade (grain size impacts toughness/wear balance), MCD crystal orientation, cutting speed, feed rate, depth of cut, coolant usage, and machine tool rigidity all significantly influence actual tool life. Always refer to supplier recommendations and consider running tests for your specific scenario.
Surface Finish Capabilities: Achieving Mirror vs. Standard Finishes
One of the most striking performance differences is the achievable surface finish.
- PCD Surface Finish: PCD tools can produce very good to excellent surface finishes on most non-ferrous metals. Surface roughness values (Ra)6 below 0.4 micrometers (µm) or even 0.2 µm are often achievable, significantly better than what carbide tools typically produce on the same materials. The quality depends somewhat on the PCD grain size; finer grain PCD generally yields smoother finishes. This level of finish is often sufficient for many high-precision automotive or aerospace components.
- MCD Surface Finish: This is where MCD truly shines. Thanks to its atomically sharp cutting edge, MCD is capable of producing true mirror finishes. It cuts via a clean shearing action at the micro-level, minimizing material tearing or plowing. On suitable materials like high-purity aluminum, copper, brass, gold, germanium, or plastics like acrylic (PMMA), MCD can achieve surface roughness values (Ra) below 0.025 µm (25 nanometers), and sometimes even down into the single-nanometer range. This is essential for applications like optical molds, laser mirrors, high-precision bearings, or decorative surfaces where visual perfection or functional optical properties are required.
Analogy: Comparing the finish from PCD to MCD is like comparing a surface smoothed with a sharp plane to one created with an impossibly sharp scalpel under perfect conditions – the latter achieves a reflective quality.
Important Note: Achieving these ultra-fine finishes with MCD requires not only the right tool but also ultra-precision machine tools with excellent vibration damping, precise motion control, and carefully optimized cutting parameters. Supplier guidance can be crucial here.
Cutting Edge Retention and Wear Patterns
How the cutting edge holds up over time also differs significantly.
- PCD Wear: PCD edges tend to wear relatively predictably through gradual abrasion. The tiny diamond crystals on the edge slowly become rounded or micro-fractured by the abrasive action of the workpiece material. Sometimes, the metallic binder material between the grains can also erode. Due to its toughness, PCD strongly resists gross chipping or breakage under normal conditions. The wear land (the flattened area behind the cutting edge) develops gradually.
- MCD Wear: MCD wear is often characterized by the development of a flank wear land, similar to other tools, but it is much more susceptible to micro-chipping along the extremely fine edge. Because it lacks toughness, any instability or hard particle encounter can cause small fragments to break away, instantly degrading the edge quality and surface finish capability. In severe cases, catastrophic fracture can occur. The orientation of the diamond crystal relative to the cutting forces significantly impacts how the wear progresses.
Here’s a simple comparison:
Feature | PCD Wear Characteristic | MCD Wear Characteristic |
---|---|---|
Primary Mode | Gradual Abrasion, Binder Erosion | Flank Wear, Micro-Chipping |
Edge Integrity | High resistance to gross chipping | Susceptible to chipping & fracture |
Predictability | Relatively predictable wear progression | Highly sensitive to conditions; can fail suddenly |
Understanding these wear patterns is crucial for process monitoring and determining optimal tool change intervals.
Impact on Cutting Forces and Chip Formation
The interaction at the cutting edge also affects the forces involved and how the material comes off as a chip.
- PCD Forces & Chips: Compared to carbide tools machining the same non-ferrous materials, PCD generally produces lower cutting forces. This is thanks to diamond’s inherent hardness and lower friction coefficient. Lower forces mean less stress on the workpiece, reduced heat generation, and potentially lower power consumption. Chip formation is typically well-controlled.
- MCD Forces & Chips: MCD takes this a step further. Its extreme sharpness and ultra-low coefficient of friction often result in the absolute lowest possible cutting forces for a given material removal scenario. This minimal force is critical in ultra-precision machining, as it minimizes deflection of the tool and workpiece, reduces residual stresses induced in the machined surface, and generates less heat. On ductile materials like pure copper or aluminum, MCD promotes ideal plastic deformation, leading to smooth, continuous, and often shiny chips, indicating a very clean cutting action.
This ability to cut with minimal force makes MCD indispensable when machining very delicate, thin-walled components or parts where minimizing any induced stress or surface damage is paramount (e.g., components for medical devices or high-energy physics experiments).
Which Materials and Operations Favor PCD Tools?
Knowing the basics, where does Polycrystalline Diamond (PCD) really prove its worth in the workshop?
PCD tools are the top choice when machining highly abrasive non-ferrous metals (like high-silicon aluminum, MMCs), composites, and certain non-metals, especially in demanding operations like high-speed milling, turning, and drilling where exceptional wear resistance and tool longevity are critical for productivity.
Let’s dive into the specific areas where PCD excels.
Ideal Materials: High-Silicon Aluminum, Metal Matrix Composites (MMCs), Ceramics (Green State)
PCD truly shines when faced with materials that act like sandpaper on other cutting tools. Its main advantage lies in combating abrasive wear.
- High-Silicon Aluminum Alloys: Think about common automotive engine blocks, pistons, or transmission housings often made from alloys like A380, A390 (typical example). These alloys contain hard, abrasive silicon particles. While great for the final component’s properties, these particles rapidly wear down conventional carbide tools. PCD, being much harder than silicon, cuts through these materials with significantly less wear, maintaining its edge for much longer.
- Metal Matrix Composites (MMCs)7: These advanced materials combine a metal (often aluminum) with reinforcing particles like Silicon Carbide (SiC) or Alumina (Al2O3). Found in high-performance automotive parts (like brake rotors or drive shafts) and aerospace components, MMCs are notoriously difficult to machine due to the extreme abrasiveness of the reinforcement. PCD is often the only viable tooling solution for achieving reasonable tool life and productivity when machining MMCs.
- Ceramics (Green State) & Other Abrasives: Before they are fully hardened (sintered), ceramic components can be machined, but the material is still highly abrasive. PCD performs well here. It’s also effective on other challenging materials like:
- Carbon Fiber Reinforced Polymers (CFRP) and Glass Fiber Reinforced Polymers (GFRP): Widely used in aerospace and automotive for their light weight and strength, but the fibers are very abrasive.
- Wood Composites: Materials like Medium Density Fiberboard (MDF), High Density Fiberboard (HDF), and particleboard contain abrasive resins and wood fibers.
- Certain Plastics with Abrasive Fillers: Plastics filled with glass or other hard particles.
- Important Restriction: PCD cannot be used effectively to machine ferrous materials like steels or cast irons. At the high temperatures generated during machining, the carbon in the diamond reacts chemically with the iron, leading to rapid tool breakdown (diffusion wear and graphitization). Stick to non-ferrous metals and abrasive non-metals for PCD.
Common Applications: Milling, Turning, Drilling of Abrasive Non-Ferrous Materials
Given its ideal materials, PCD finds widespread use in several common machining operations, particularly in high-volume industries like automotive and aerospace.
- Milling: This is a major application area. Think of face milling cylinder heads or engine blocks, shoulder milling transmission cases, or high-speed pocketing of aluminum structural components. PCD’s toughness allows it to handle the interrupted cuts inherent in milling operations better than more brittle materials.
- Turning: High-speed turning of aluminum pistons (including the complex ring grooves), turning MMC brake rotors, or machining composite shafts benefits greatly from PCD’s wear resistance.
- Drilling, Reaming, and Boring: Creating precise holes in abrasive aluminum alloys (e.g., for engine components like valve guides and seats) or composites is another key application. PCD drills and reamers provide the longevity needed for consistent hole quality over many parts.
Essentially, any operation involving the abrasive materials listed above, where maximizing tool life and maintaining consistent part quality over long runs is crucial, is a prime candidate for PCD tooling. It allows for significantly higher cutting speeds compared to carbide in these materials, boosting productivity.
Strengths: High Wear Resistance and Toughness
Let’s summarize PCD’s key advantages based on its structure and properties:
- Exceptional Abrasive Wear Resistance: This is PCD’s defining strength. Its high hardness directly counters the grinding action of hard particles in materials like high-Si aluminum and MMCs, leading to vastly superior tool life compared to carbide.
- Good Toughness (Relative to Diamond): The polycrystalline structure with its binder phase makes PCD much more resistant to chipping and fracture than single-crystal diamond (MCD). This allows it to be used in interrupted cuts (milling) and less stable conditions. It also permits the design of tools with more complex geometries.
- High Thermal Conductivity: Efficiently draws heat away from the cutting zone, beneficial for high-speed machining of non-ferrous metals and reducing thermal damage to the tool and workpiece.
- Productivity Enabler: The combination of long tool life and the ability to run at high cutting speeds translates directly into increased machine uptime, higher output, reduced tooling costs per part, and more predictable manufacturing processes.
These strengths make PCD an economic and technical necessity in many demanding, high-volume machining scenarios involving abrasive non-ferrous materials.
Limitations: Edge Sharpness and Certain Material Interactions
Despite its strengths, PCD isn’t perfect for every situation. Here are its main limitations:
- Limited Edge Sharpness: As discussed earlier, the polycrystalline structure prevents PCD from achieving the near-atomic sharpness possible with MCD. This means it cannot produce true mirror finishes; surface quality is excellent but not optically perfect.
- Inability to Machine Ferrous Metals: This is a hard limitation due to the chemical reaction between diamond (carbon) and iron at high temperatures. Using PCD on steel will destroy the tool very quickly.
- Potential Binder Issues: The metallic binder (usually cobalt) can sometimes react negatively with certain workpiece materials or specific coolant chemistries. In some applications (like medical or certain electronics), the presence of cobalt binder might be undesirable. (Binderless PCD variants exist but have different property trade-offs).
- Higher Initial Cost: PCD tools typically have a higher purchase price than comparable carbide tools8. However, this is often offset by significantly longer tool life and increased productivity, leading to a lower overall cost per part in the right applications.
Understanding these limitations helps define the boundaries of where PCD is the optimal choice and where other materials, like MCD or even traditional carbide, might be more suitable.
When Are MCD Tools the Superior Choice?
We’ve seen where PCD excels, but what about Monocrystalline Diamond (MCD)? When does this ultra-sharp tool take the lead?
MCD tools are the superior choice primarily for ultra-precision machining applications demanding mirror-like surface finishes and extremely tight tolerances, especially when working with specific soft, non-abrasive non-ferrous metals (like high-purity aluminum, copper, gold) and certain plastics.
Let’s explore the specific niche where MCD truly stands out.
Ideal Materials: High-Purity Aluminum, Copper, Brass, Gold, Plastics (Acrylics)
MCD tools thrive when machining materials that are relatively soft, non-abrasive, and allow for clean shearing action without causing rapid tool wear or edge chipping. Think materials where the ultimate surface quality is paramount.
- High-Purity Non-Ferrous Metals:
- Aluminum: Especially high-purity grades or alloys like 6061 after proper heat treatment. Used extensively for optical mirrors, computer memory disks, and precision housings.
- Copper & Copper Alloys: Oxygen-Free High Conductivity (OFHC) copper9 is a classic MCD application, used for injection molds (especially for optics), high-frequency electronics components, and decorative items. Brass and certain bronzes also machine well.
- Precious Metals: Gold, silver, and platinum can be machined to brilliant finishes for jewelry, luxury goods, and specialized scientific or electronic applications.
- Specific Plastics & Polymers:
- Acrylic (PMMA)10 is widely used for lenses, light pipes, and optical windows. MCD turning can produce optically clear surfaces directly.
- Polycarbonate (PC): Another common optical plastic machinable with MCD.
- Other thermoplastics suitable for single-point diamond turning may include COC, COP, and specific polystyrenes.
- Other Specialty Materials:
- Infrared Optical Materials: Germanium (Ge), Silicon (Si – for specific applications), Zinc Sulfide (ZnS), Zinc Selenide (ZnSe).
- Electroless Nickel Plating: A hard plating often applied to molds or mirrors, which can be diamond turned to a fine finish.
Critical Factor: The key is the lack of hard, abrasive inclusions (like high silicon content in aluminum) and the material’s ability to be sheared cleanly by the ultra-sharp MCD edge without excessive built-up edge formation. Material consistency and purity are vital for success.
Common Applications: Ultra-Precision Machining, Mirror Finishing, Optics Manufacturing
MCD’s unique properties make it indispensable in highly specialized fields and operations.
- Ultra-Precision Machining, Mirror Finishing: This involves achieving dimensional tolerances in the sub-micron range (less than 0.001 mm or 0.00004 inches) and surface finishes at the nanometer level. MCD is often the only tool capable of reaching these specifications directly through machining. Creating highly reflective surfaces on metals or plastics without the need for subsequent polishing is achieved through specialized operations like single-point diamond turning (SPDT) on ultra-precision lathes or diamond fly-cutting.
- Optics Manufacturing: A major application area. MCD is used to directly machine:
- Lenses and lens arrays (especially from plastics or infrared materials).
- Molds and inserts for casting or injection molding optical components (like contact lenses or smartphone camera lenses).
- Reflective mirrors (parabolic, spherical, aspheric) for telescopes, lasers, scanners, and scientific instruments.
- High-End Decorative Surfaces: Achieving brilliant, flawless finishes on luxury watch components, jewelry facets, writing instruments, and premium hardware.
- Specialized Scientific & Medical Components: Parts requiring extreme smoothness, precision, and potentially biocompatibility (using pure diamond without binder), such as components for fluidic devices, analytical instruments, or certain implantable prototypes.
Operational Note: These applications almost always involve continuous cutting processes like turning, facing, or fly-cutting, performed on highly rigid, precise, and vibration-damped machine tools specifically designed for diamond turning. Milling with MCD is extremely rare and risky due to the tool’s brittleness.
Strengths: Ultimate Edge Sharpness and Surface Finish Quality
MCD’s advantages stem directly from its single-crystal nature:
- Ultimate Edge Sharpness: The ability to achieve a cutting edge radius measured in nanometers is MCD’s defining strength. This allows for incredibly fine cuts and the generation of extremely smooth surfaces.
- Unmatched Surface Finish Quality: Directly produces mirror finishes (Ra < 25 nm, sometimes < 5 nm) on suitable materials, often eliminating the need for post-machining polishing processes, saving time and potentially preserving form accuracy.
- Minimal Cutting Forces: The sharp edge and low friction result in very low cutting forces, minimizing distortion of delicate workpieces, reducing residual stress, and generating minimal heat.
- Superior Dimensional Accuracy: The combination of a sharp, stable edge (under proper conditions) and low cutting forces allows for the achievement of sub-micron dimensional tolerances.
- Purity (No Binder): Being pure diamond, it introduces no metallic binder contamination, which can be crucial for certain optical, electronic, or medical applications.
These strengths make MCD the enabling technology for many cutting-edge products and scientific endeavors.
Limitations: Brittleness, Sensitivity to Vibration, Material Restrictions
However, MCD’s strengths come with significant trade-offs and limitations:
- Extreme Brittleness: This is the primary drawback. MCD tools are highly susceptible to chipping or catastrophic fracture if subjected to impact, vibration, thermal shock, or attempts to cut unsuitable (hard or abrasive) materials. Requires extremely careful handling and use.
- High Sensitivity to Vibration: Demands the use of ultra-precision machine tools with exceptional stiffness, damping, and environmental control (temperature, air quality) to prevent edge damage and achieve desired results.
- Strict Material Restrictions: Can only effectively machine a limited range of relatively soft, non-abrasive non-ferrous metals, specific plastics, and certain crystalline materials. It cannot machine steels, cast irons, MMCs, high-silicon aluminum, ceramics, or most composites.
- Demanding Operating Conditions: Success requires meticulous setup, precise control over cutting parameters (depth of cut, feed rate, speed), appropriate coolant/lubricant application, and often a cleanroom-like environment.
- Cost and Expertise: MCD tools can be expensive, and effectively utilizing them requires specialized knowledge, high-end equipment, and experienced operators. Tool resharpening is also a specialized process.
These limitations confine MCD to a specialized, high-value niche, contrasting sharply with the broader applicability of the more robust PCD.
How Do You Select the Right Tool for Your Specific Needs?
After learning about the differences and performance, how do you actually decide whether PCD or MCD is the right choice for your specific job?
Selecting the right diamond tool involves carefully analyzing your workpiece material’s properties (especially abrasiveness), defining your required surface finish and tolerances, considering the machining operation and stability, and evaluating the overall cost versus performance trade-off for your specific application.
Let’s walk through the key factors to guide your decision.
Factor 1: Analyze the Material Being Machined
The material you need to cut is often the most critical factor dictating your choice. Ask yourself:
- Is it a ferrous metal (steel, cast iron)? If yes, neither PCD nor MCD is generally suitable due to chemical reactions at high temperatures. You’ll likely need carbide, ceramic, or CBN tooling.
- Is it a non-ferrous metal, composite, plastic, or other non-metal? If yes, diamond tooling is a possibility. Now, consider its abrasiveness:
- Highly Abrasive? (e.g., High-silicon aluminum like A390, MMCs like Al/SiC, carbon fiber composites (CFRP), glass-filled plastics, green ceramics) -> Lean heavily towards PCD. Its toughness and excellent wear resistance are designed specifically for these challenging materials where carbide wears out too quickly.
- Soft, Non-Abrasive, High Purity? (e.g., OFHC copper, high-purity aluminum, gold, silver, brass, acrylics, pure polymers) -> MCD becomes a strong candidate, especially if surface finish is critical. PCD can also machine these materials, but MCD offers unique advantages here.
- Moderately Abrasive / Standard Non-Ferrous? (e.g., standard aluminum alloys like 6061, some copper alloys) -> PCD is often the default choice for good tool life and finish. MCD is generally unnecessary unless extreme finish/tolerance is required.
Also, consider material consistency. MCD performs best on materials with uniform structure and minimal hard inclusions, which could chip its delicate edge.
Factor 2: Define Your Surface Finish and Tolerance Requirements
What level of precision and smoothness does the final part require?
- Standard to Good Surface Finish (e.g., Ra ≈ 0.4 – 1.6 µm): PCD tools are typically more than capable of achieving this level on suitable materials, offering a robust and economical solution.
- Excellent Surface Finish (e.g., Ra < 0.4 µm): Fine-grain PCD grades can often achieve this, providing a balance of good finish and tool life.
- Mirror Finish / Optical Quality (e.g., Ra < 0.025 µm or down to nanometers): If you need a reflective surface or near-perfect smoothness directly from machining, MCD is essentially the only option. This is its primary performance advantage.
Similarly, consider dimensional tolerances:
- Standard Engineering Tolerances: PCD generally holds size well due to its low wear rate.
- Ultra-Precision Tolerances (Sub-micron): MCD’s ability to maintain an extremely sharp edge and cut with minimal forces often allows for tighter achievable tolerances, crucial in optics and high-precision fields.
Be realistic about your needs. Don’t specify MCD for a mirror finish if an excellent PCD finish is perfectly adequate – the extra cost and process demands for MCD may not be justified.
Factor 3: Consider the Machining Operation and Parameters
How you intend to cut the material also plays a vital role.
- Type of Operation:
- Milling, Drilling, Reaming, Heavy Turning (Interrupted Cuts): These operations often involve impacts or varying chip loads. PCD’s superior toughness makes it the much safer and more reliable choice here. Using MCD in milling is generally avoided due to the high risk of edge fracture.
- Continuous Turning, Facing, Fly-Cutting (Stable, Finishing Cuts): These smooth operations are where MCD is applicable and excels, especially when aiming for the highest surface quality on suitable materials.
- Machine and Setup Stability:
- Ultra-Precise, Rigid, Well-Damped Machine Tools: These are required to successfully use MCD and prevent vibration-induced edge chipping.
- General Purpose or Less Rigid Machines: PCD is more forgiving of minor vibrations and less-than-perfect stability due to its toughness.
- Cutting Parameters:
- While both PCD and MCD can often run at higher speeds than carbide in non-ferrous materials, MCD typically requires very light depths of cut and feed rates to protect its delicate edge.
- PCD offers more flexibility in choosing parameters for balancing productivity and tool life.
Factor 4: Evaluate the Cost-Performance Trade-off
Diamond tools represent a significant investment compared to traditional tooling. A cost-benefit analysis11 is essential.
- Initial Tool Cost: Carbide < PCD < MCD (MCD often being substantially more expensive).
- Tool Life & Cost Per Part: This is often the deciding economic factor.
- In highly abrasive materials, PCD’s dramatically longer tool life compared to carbide frequently results in a lower overall cost per part, despite the higher initial price, due to fewer tool changes and less downtime.
- MCD’s cost justification usually hinges on its ability to achieve finishes or tolerances unattainable by other methods, potentially eliminating costly and time-consuming secondary operations like polishing, or by enabling the production of high-value components (like optics). Its tool life is very conditional.
- Productivity Impact: Faster cycle times possible with diamond tooling can reduce overall manufacturing costs.
- Process Reliability & Risk: PCD generally offers higher process security due to its robustness. MCD applications carry a higher risk of tool failure if conditions aren’t meticulously controlled, potentially leading to scrap or rework costs.
- Infrastructure & Expertise: Using MCD effectively often requires investment in ultra-precision machines, controlled environments, and specialized operator training, adding to the overall cost.
Reminder: Costs for specific PCD grades or MCD tools (considering size, geometry, quality, orientation) can vary significantly between suppliers. Always perform a detailed cost analysis tailored to your specific part, material, volume, and machining capabilities.
Quick Comparison Chart: PCD vs. MCD Selection Guide
This table summarizes the key points to help guide your selection:
Feature / Criterion | Polycrystalline Diamond (PCD) | Monocrystalline Diamond (MCD) |
---|---|---|
Primary Strength | High Wear Resistance, Toughness | Ultimate Edge Sharpness, Surface Finish |
Key Weakness | Limited Edge Sharpness vs. MCD, Can’t Cut Ferrous | Extreme Brittleness, Material/Operation Limits |
Ideal Materials | Abrasive Non-Ferrous (High-Si Al, MMCs), Composites | Soft, Pure Non-Ferrous (Cu, Al, Au), Specific Plastics |
Typical Operations | Milling, Turning, Drilling (General Purpose) | Ultra-Precision Turning, Fly-Cutting (Finishing) |
Achievable Finish (Ra) | Excellent (< 0.4 µm possible) | Mirror Finish (< 0.025 µm to nm range) |
Toughness | Good (for diamond) | Very Low (Brittle) |
Edge Sharpness | Limited by Grain Size | Near-Atomic Sharpness Possible |
Tool Life Expectancy | Very Long (in abrasive materials) | Highly Conditional (can be good in ideal niche) |
Initial Cost Level | High (vs. Carbide) | Very High (often >> PCD) |
Sensitivity/Robustness | Relatively Robust, More Forgiving | Highly Sensitive to Conditions, Requires Care |
By carefully considering these four factors and using this chart as a reference, you can make an informed decision about whether PCD or MCD is the optimal diamond tooling solution for your specific machining challenge.
Conclusion
Choosing between Polycrystalline Diamond (PCD) and Monocrystalline Diamond (MCD) tooling ultimately comes down to a clear understanding of your specific application requirements. PCD stands out as the robust, workhorse solution for achieving long tool life and high productivity when machining abrasive non-ferrous metals and composites. Its toughness makes it suitable for a wide range of operations, including interrupted cuts. Conversely, MCD offers unparalleled performance in a specialized niche, providing the ultimate edge sharpness needed for mirror finishes and ultra-precision tolerances on specific soft, non-abrasive materials, but demands highly controlled conditions due to its inherent brittleness. By carefully weighing the factors of material, required finish and tolerance, operation type, and cost-effectiveness, you can confidently select the diamond tool that best matches your needs, optimizing both performance and economy.
References
- Polycrystalline Diamond (PCD)1 – A comprehensive guide from ZYDiamondTools detailing the basics, properties, types, and applications of PCD cutting tools.
- Monocrystalline Diamond (MCD)2 – ZYDiamondTools article explaining MCD tools, focusing on their properties, manufacturing, and role in achieving ultra-precision and mirror finishes.
- High-Pressure High-Temperature (HPHT) sintering3 – Wikipedia section explaining pressure sintering, a key process for PCD manufacturing.
- Chemical Vapor Deposition (CVD)4 – ScienceDirect topic page providing an overview of the Chemical Vapor Deposition process used for synthetic diamond growth.
- Knoop hardness values5 – Wikipedia article detailing the Knoop hardness test used for measuring material hardness, relevant for diamond tools.
- Surface roughness values (Ra)6 – Wikipedia section explaining surface roughness parameters, including Ra (Average Roughness), crucial for defining finish quality.
- Metal Matrix Composites (MMCs)7 – Wikipedia article defining Metal Matrix Composites, highlighting their composition and properties relevant to machining challenges.
- higher purchase price than comparable carbide tools8 – ZYDiamondTools blog post comparing PCD and Carbide tools, including cost considerations.
- Oxygen-Free High Conductivity (OFHC) copper9 – Wikipedia article defining OFHC copper, a common high-purity material machined with MCD tools.
- Acrylic (PMMA)10 – Wikipedia article describing Poly(methyl methacrylate) or Acrylic, a plastic often machined with MCD for optical applications.
- cost-benefit analysis11 – ZYDiamondTools blog post explaining Total Cost of Ownership (TCO) analysis for superhard tooling, relevant to comparing PCD/MCD costs.
ZY Superhard Tools Co., Ltd.
Do you have any needs for PCD tools or diamond grinding wheels? We can customize products to meet your specific requirements. If you have any ideas or requests, feel free to reach out—we’ll respond within 24 hours!
Do you have any needs for PCD & CBN tools or diamond grinding wheels? We can customize products to meet your specific requirements. If you have any ideas or requests, feel free to reach out—we’ll respond within 24 hours!
Do you have any needs for PCD & CBN tools or diamond grinding wheels? We can customize products to meet your specific requirements. If you have any ideas or requests, feel free to reach out—we’ll respond within 24 hours!
Post Categories
Product Categories
About Company
Related Posts
Which Turning Insert Shape Should You Choose?
Master turning insert selection. Our guide covers choosing the right shape for your job, decoding ISO codes, and selecting the
How Do You Solve Vibration, Chip Control, and Surface Finish Issues in PCD Grooving?
Solve common PCD grooving problems. This guide details how to fix vibration, improve chip evacuation, and achieve a flawless sidewall
Why Is Your Tooling Wearing Out Prematurely? A Machinist’s Guide to Key Causes & Proven Solutions
Facing premature tool wear? Learn the key causes like heat, vibration, & wrong parameters. Discover proven solutions from setup to
How Do You Select the Optimal PCD Tools for Scroll Compressor Machining?
Learn how to select the right PCD tools for scroll compressor machining. This guide covers the benefits over carbide, key
Subscribe
Simply enter your email below and click “Subscribe” to stay connected with everything new and exciting.