-
Whatsapp: +86 13526572721
-
Email: info@zydiamondtools.com
-
Address: AUX Industrial Park, Zhengzhou City, Henan Province, China
-
Whatsapp: +86 13526572721
-
Email: info@zydiamondtools.com
-
Address: AUX Industrial Park, Zhengzhou City, Henan Province, China
What is the Difference Between PCD and Carbide Tools?
- Knowledge, PCD & CBN Tools Knowledge
- -2025-03-15
- - byKevin Ray
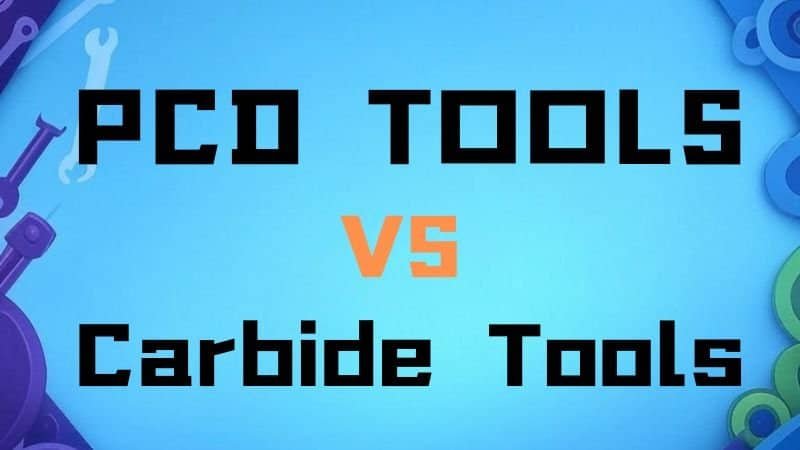
When you hear about cutting tools, what’s really the main difference between PCD and Carbide?
The primary difference between PCD (Polycrystalline Diamond) and Carbide (Tungsten Carbide) tools lies in their material composition and resulting properties: PCD is exceptionally hard and wear-resistant, ideal for non-ferrous metals and abrasives, while Carbide is tougher, more versatile across materials including steel, and generally less expensive upfront. These differences dictate their best applications, tool life, cost-effectiveness, and performance characteristics like achievable speed and surface finish.
Table of Contents
ToggleHow Do PCD and Carbide Differ in Material Properties?
So, when we look closely at these two tool materials, how exactly do their basic physical characteristics stack up against each other?
PCD (Polycrystalline Diamond) tools are fundamentally different from Carbide (typically Tungsten Carbide) tools in their core material makeup, leading directly to significant variations in key physical properties. PCD stands out for its exceptional hardness and wear resistance thanks to its diamond structure, whereas Carbide generally provides superior toughness, making it better at resisting chipping or breaking under impact. Their abilities to handle heat also differ, affecting how they perform, especially under demanding cutting conditions.
Hardness and Wear Resistance Showdown
Hardness basically means how well a material resists scratching or wear. Think about trying to scratch something hard like a rock versus something softer like wood.
- PCD (Polycrystalline Diamond1): Imagine trying to scratch a diamond – it’s incredibly difficult! PCD is made from tiny synthetic diamond particles fused together. Because diamond is the hardest natural material known, PCD tools are exceptionally hard. Scientists measure hardness using scales like Knoop or Vickers2, and PCD consistently scores much higher than carbide. This extreme hardness means PCD tools resist wearing down, even when cutting very abrasive materials that act like sandpaper.
- Industry Example: When machining high-silicon aluminum alloys (common in automotive engine blocks) or tough Metal Matrix Composites (MMCs used in aerospace), PCD tools can often outlast carbide tools by 50 to 100 times or more simply because they don’t wear away as quickly. This drastically reduces tool changes and improves consistency.
- Carbide (Tungsten Carbide): Carbide is also very hard – much harder than steel – but not nearly as hard as PCD. It’s made by mixing hard tungsten carbide particles with a softer metal binder, usually cobalt. This binder acts like glue, holding the hard particles together. While tough, it’s still susceptible to wear, especially from abrasive materials.
Important Note: The exact hardness can vary slightly between different grades of PCD (based on diamond grain size) and Carbide (based on tungsten carbide grain size and binder percentage). Always check the manufacturer’s specifications for the specific grade you are considering.
Toughness and Impact Resistance Comparison
Toughness isn’t the same as hardness. Toughness is about how well a material can resist breaking or chipping when it gets hit suddenly or undergoes stress. Think of the difference between glass (very hard but brittle) and rubber (not hard, but very tough).
- Carbide (Tungsten Carbide): The metal binder (like cobalt) in carbide tools gives them significantly better toughness compared to PCD. This “glue” allows the material to absorb some impact energy without fracturing. This makes carbide a more forgiving material if the cutting conditions involve shocks or vibrations.
- Industry Example: Consider milling a part that has holes or slots. This creates an “interrupted cut” where the tool edge repeatedly slams into the material as it enters and exits the cut. Carbide’s higher toughness helps it withstand these repeated impacts without chipping as easily as PCD might.
- PCD (Polycrystalline Diamond): While incredibly hard, PCD is also more brittle than carbide. Like glass, it doesn’t handle shocks or heavy impacts as well. A sharp knock or excessive vibration during cutting can cause the PCD edge to chip or even break. This requires more stable machining setups and careful handling.
Which is better? It depends! If you need maximum wear resistance for abrasive materials in a smooth cut, PCD’s hardness wins. If you have interrupted cuts or need to withstand impacts, Carbide’s toughness is often preferred.
Understanding Thermal Conductivity and Stability
How a tool handles heat is crucial, as cutting generates a lot of friction and high temperatures right at the cutting edge.
- Thermal Conductivity3 (How well heat moves away):
- PCD: Diamond is an excellent conductor of heat. This means PCD tools can quickly transfer heat away from the cutting edge and into the tool body or machine. This helps keep the edge cooler, which is vital for maintaining hardness and preventing premature wear, especially at very high cutting speeds used with non-ferrous materials. Think of it like a good heatsink on a computer chip.
- Carbide: Carbide conducts heat reasonably well, but not as effectively as PCD. More heat tends to stay concentrated near the cutting edge.
- Thermal Stability (How well it stays strong when hot):
- Carbide: Tungsten carbide generally maintains its hardness very well even at the high temperatures generated when cutting materials like steel or cast iron. This property is often called “hot hardness.”
- PCD: PCD also has good thermal stability, but its performance can be affected by extremely high temperatures, especially when machining ferrous materials (like steel). At very high heat, a chemical reaction can occur between the diamond (carbon) and iron, causing the PCD structure to break down faster.
Key Takeaway: PCD’s ability to quickly dissipate heat allows for higher speeds in suitable materials. Carbide’s excellent hot hardness makes it reliable for machining materials that generate intense heat, like steels. Remember that specific grades from different suppliers might have slight variations in these thermal properties, so consulting technical datasheets is always a good practice.
When Should You Choose PCD vs. Carbide Tools?
Okay, knowing their different physical strengths, how do you actually decide which tool type is the right one for your specific machining job?
Choosing between PCD and Carbide tools primarily depends on the material you need to machine and your goals for speed and finish quality. PCD excels with non-ferrous metals (like aluminum) and highly abrasive non-metals (like composites), allowing for much higher cutting speeds and often yielding superior surface finishes. Carbide, conversely, is the go-to choice for ferrous metals (like steel and cast iron) and offers versatility across a wide range of general-purpose machining tasks.
Ideal Materials for PCD Tools (Non-Ferrous & Abrasives)
PCD tools truly shine when working with specific types of materials, mainly because of their incredible hardness and wear resistance we discussed earlier. They are the top choice for:
- Non-Ferrous Metals: These are metals that don’t contain significant amounts of iron.
- Aluminum and its alloys (especially high-silicon types common in automotive parts)
- Copper and Brass
- Magnesium alloys
- Precious metals like Gold and Platinum
- Abrasive Non-Metallic Materials: These materials act like sandpaper and quickly wear down less hard tools.
- Composites (Carbon Fiber Reinforced Polymers – CFRP, Glass Fiber Reinforced Polymers – GFRP, used heavily in aerospace and sporting goods)
- Graphite (used for EDM electrodes)
- Ceramics (in their ‘green’ or unfired state)
- Wood and Wood Composites (like MDF, HDF, particleboard)
- Certain plastics
Why PCD works here: Its extreme hardness resists the ‘sanding’ effect of abrasive materials. Also, PCD doesn’t have a negative chemical reaction with these non-ferrous metals, even at high cutting temperatures.
Crucial Limitation: PCD is generally not recommended for machining ferrous metals like steel or cast iron. At the high temperatures generated during cutting, the carbon in the PCD diamond structure can chemically react with the iron in the workpiece. This reaction actually breaks down the diamond edge, causing rapid tool failure.
Suitable Materials for Carbide Tools (Ferrous & General Purpose)
Carbide tools, typically Tungsten Carbide, are the workhorses for a broader range of materials, especially metals containing iron (ferrous metals). Their combination of good hardness, excellent toughness, and stability at high temperatures makes them suitable for:
- Ferrous Metals:
- Steels (Carbon steel, alloy steel, tool steel, stainless steel)
- Cast Iron (Gray iron, ductile iron)
- High-Temperature Alloys:
- Titanium alloys
- Nickel-based alloys (like Inconel, used in jet engines and turbines)
- Hardened Materials: Some grades can machine hardened steels.
- General Purpose: They can also effectively machine many non-ferrous metals, although perhaps not as efficiently or for as long as PCD in high-volume applications.
Why Carbide works here: Its toughness handles the cutting forces involved in machining strong metals. Its ‘hot hardness’ means it stays strong even when cutting generates intense heat. Importantly, it does not have the negative chemical reaction with iron that limits PCD. This makes Carbide a versatile and reliable choice for many common machining tasks.
Impact on Achievable Cutting Speeds
One of the most significant operational differences is the cutting speed each tool allows.
- PCD: Because PCD handles heat well (good thermal conductivity) and resists wear in suitable materials, it can often be run at much higher cutting speeds than carbide. This means you can remove material faster, leading to shorter cycle times and increased productivity.
- Example: When finish milling an aluminum automotive cylinder head, a PCD tool might run effectively at surface speeds of 1000 to 3000 meters per minute (approx. 3000-10000 SFM – Surface Feet per Minute).
- Carbide: Carbide tools operate at lower speeds compared to PCD in non-ferrous applications, but these speeds are appropriate for the tougher materials like steel and titanium they often machine. Running carbide too fast in any material can lead to rapid wear or tool failure due to heat buildup.
- Example: Machining steel with a carbide end mill might typically involve speeds in the range of 100 to 300 meters per minute (approx. 300-1000 SFM), depending heavily on the specific steel alloy and cutting operation.
Remember: Recommended cutting speeds are highly dependent on the specific grade of PCD or carbide, the exact workpiece material, the machine’s capability, and the type of cutting operation (roughing vs. finishing). Always consult the tool manufacturer’s recommendations and perform tests to find the optimal parameters for your application.
Differences in Surface Finish Quality
The quality of the machined surface is often critical. How do these tools compare?
- PCD: Due to its extreme hardness and ability to maintain a very sharp cutting edge for a long time (high wear resistance), PCD often produces superior and more consistent surface finishes on non-ferrous and abrasive materials. The edge simply doesn’t dull as quickly. In some cases, the finish achieved with PCD can be so good that it eliminates the need for later grinding or polishing operations.
- Example: Achieving a mirror-like finish on aluminum wheels or maintaining a very smooth surface on CFRP aerospace parts often relies on the consistent sharpness of PCD tooling.
- Carbide: Carbide tools can certainly produce excellent surface finishes, especially when new or freshly sharpened. However, because the cutting edge wears more quickly than PCD (in materials where both can be used), the surface finish may gradually degrade over a longer production run, potentially requiring more frequent tool changes to maintain consistency.
Ultimately, the choice often comes down to matching the tool’s strengths to the material being cut and the desired outcome in terms of speed and finish.
What Are the Key Differences in Tool Life and Cost-Effectiveness?
Beyond how they cut, how do PCD and Carbide tools compare when it comes to how long they last and how much they actually cost you in the long run?
While Carbide tools typically have a lower initial purchase price, PCD tools generally offer a significantly longer lifespan, especially when machining abrasive materials or non-ferrous metals. This extended tool life often translates to a lower overall cost per machined part for PCD, despite its higher upfront investment. This happens because of fewer tool changes, reduced machine downtime, and potentially higher productivity. However, maintenance factors, like the specialized regrinding needed for PCD, also play a role in the total cost picture.
Comparing Expected Tool Lifespan
One of the most dramatic differences lies in how long each tool can effectively cut before needing replacement or resharpening.
- PCD Tools: In their ideal applications (like machining aluminum, composites, or graphite), PCD tools are champions of longevity. Thanks to their incredible hardness and wear resistance, they can often last 10, 50, or even over 100 times longer than comparable carbide tools cutting the same material under optimal conditions. This lifespan advantage is most pronounced when dealing with highly abrasive materials that quickly wear down other tools.
- Industry Example: In high-volume automotive manufacturing, such as machining aluminum engine blocks or transmission cases, a single PCD insert might machine thousands, or even tens of thousands, of components before needing attention. A carbide tool in the same operation might only last for a few hundred parts.
- Carbide Tools: Carbide tools offer a respectable lifespan, especially considering their lower cost and versatility. Their life is generally sufficient for many common machining tasks, particularly in ferrous metals (where PCD isn’t suitable) or in lower-volume production runs. However, when directly compared against PCD in abrasive or non-ferrous materials, their lifespan is significantly shorter.
It’s crucial to remember that actual tool life depends heavily on the specific material being cut, the cutting parameters used (speed, feed rate, depth of cut), the machine’s condition, and the specific grade of the tool material itself.
Analyzing Initial Investment vs. Long-Term Value (Cost per Part)
At first glance, the price tags for these tools look very different.
- Initial Investment: PCD tools are considerably more expensive to buy initially than carbide tools. The complex manufacturing process for synthetic diamond means a PCD tool can cost anywhere from 2 to 10 times more (or even higher) than a similar carbide tool.
- Carbide Tools: Their lower upfront cost makes them very attractive, especially for job shops, prototyping, or short production runs where minimizing the initial tooling expense is important.
However, the initial price tag doesn’t tell the whole story. To understand the true cost, we need to think about the cost per part produced.
Thinking About Cost Per Part
Cost per part isn’t just the tool’s purchase price. It includes:
- The initial tool cost.
- The number of parts produced before the tool wears out or needs service.
- The cost of machine downtime needed for tool changes.
- The cost of labor involved in changing tools.
- The cost of regrinding or replacing the tool.
- Long-Term Value (PCD): Even though PCD costs more upfront, its vastly longer tool life in the right applications means it produces many more parts per tool edge. This significantly reduces the number of tool changes needed, cutting down on machine downtime and labor costs associated with changes. When you divide the total costs over the huge number of parts a PCD tool can make, the cost per part can often be substantially lower than with carbide, especially in mass production scenarios or when machining difficult, abrasive materials.
- Long-Term Value (Carbide): If the production volume is low, or if the material isn’t particularly abrasive, the high initial cost of PCD might not be recovered through longer life. In these cases, carbide’s lower initial cost can result in a lower overall cost for the job.
The most cost-effective choice depends entirely on the specific application, production volume, and material.
Maintenance and Regrinding Considerations
Most cutting tools don’t last forever, but many can be given a new lease on life through regrinding or resharpening4.
- Carbide Tools: Regrinding carbide is a common, relatively straightforward process. It can typically be done using standard grinding machines with appropriate grinding wheels (like silicon carbide or diamond wheels). Many machine shops have this capability in-house, or specialized regrinding services are widely available at a moderate cost.
- PCD Tools: Regrinding PCD is possible, but it’s a more specialized and demanding process. Because PCD is so hard, it requires special grinding machines equipped with specific types of diamond grinding wheels. This process takes longer and typically costs more per regrind than carbide. Furthermore, improper regrinding can easily damage the delicate PCD edge.
- Frequency Matters: While PCD regrinding is more complex and costly per instance, remember that PCD tools need this service much less frequently than carbide tools due to their extended lifespan.
- Feasibility: Not all PCD tools can be effectively reground multiple times; it depends on the tool’s design, the amount of wear, and the type of PCD edge.
Recommendation: Always consult with the tool manufacturer or a reputable, specialized tool regrinding service to understand the feasibility, cost, and expected performance of reground PCD or carbide tools for your specific needs. They can advise on how many regrinds are typically possible and the expected life after each service.
What Are the Main Pros and Cons of Each Tool Type?
So, putting it all together, what are the main good points and bad points to keep in mind for both PCD and Carbide tools when making a choice?
PCD tools offer major advantages like extremely long tool life, the ability to machine abrasive materials effectively, and potential for very high cutting speeds and excellent surface finishes; however, they come with a high initial cost and are generally unsuitable for ferrous metals. Conversely, Carbide tools provide versatility across many materials including steels, better toughness for interrupted cuts, and lower upfront cost, though they typically have shorter tool life in abrasive applications and lower maximum cutting speeds compared to PCD.
Here’s a breakdown of the key advantages and disadvantages for each:
Key Advantages of Using PCD Tools
- Exceptional Tool Life: Can last significantly longer (often 10x to 100x or more) than carbide in suitable materials, especially abrasives.
- Superior Wear Resistance: Stands up extremely well against abrasive materials like composites, high-silicon aluminum, and graphite.
- High-Speed Capability: Allows for much faster cutting speeds, particularly in non-ferrous metals, increasing productivity.
- Excellent Surface Finish: Often produces smoother, more consistent finishes due to prolonged edge sharpness.
- Lower Cost Per Part (Potentially): In high-volume production or when machining difficult abrasive materials, the long life can lead to lower overall costs despite the high initial price.
Key Disadvantages and Limitations of PCD Tools
- High Initial Cost: Significantly more expensive to purchase upfront compared to carbide tools.
- Lower Toughness (More Brittle): More susceptible to chipping or breaking from impacts, vibrations, or interrupted cuts. Requires stable machining conditions.
- Not Suitable for Ferrous Metals: Generally cannot be used effectively on steel or cast iron due to adverse chemical reactions at high temperatures.
- Specialized Regrinding: Resharpening requires special equipment and expertise, making it more complex and costly than carbide regrinding (though needed less often).
Key Advantages of Using Carbide Tools
- Lower Initial Cost: Much more affordable to purchase initially, making them accessible for various budgets and applications.
- Good Toughness: Better able to withstand impacts, vibrations, and interrupted cuts without chipping compared to PCD.
- Versatility: Suitable for a very wide range of materials, including steels, cast irons, titanium, and many non-ferrous metals. A reliable general-purpose choice.
- Easier Maintenance: Regrinding or resharpening is a standard, relatively inexpensive process using common equipment.
- Wide Availability: Available in numerous grades, geometries, and coatings for diverse applications.
Key Disadvantages and Limitations of Carbide Tools
- Shorter Tool Life (vs. PCD in specific materials): Wears out much faster than PCD when machining highly abrasive materials or non-ferrous metals at high speeds.
- Lower Speed Limits: Cannot typically achieve the same high cutting speeds as PCD, potentially limiting productivity in some applications.
- Faster Wear Rate: The cutting edge dulls more quickly than PCD, which can affect surface finish consistency over long production runs.
- Higher Cost Per Part (Potentially): In high-volume abrasive applications, the frequent tool changes can lead to higher overall costs compared to using longer-lasting PCD.
Conclusion: Making the Right Choice
Ultimately, there’s no single “best” tool between PCD and Carbide – the right choice hinges entirely on your specific needs. By understanding the fundamental differences in their material properties, ideal applications, achievable performance, tool life expectations, and overall cost-effectiveness, you can make an informed decision.
Consider the material you’re cutting, your production volume, and whether your priority is minimizing upfront cost, maximizing speed and tool life, or achieving the best possible surface finish. Weighing the pros and cons discussed here against your unique requirements will guide you to selecting the most suitable and economical cutting tool for your job.
References
- Polycrystalline Diamond1 – ZYDiamondTools blog post providing a comprehensive overview of PCD tools.
- Vickers2 – Gordon England page detailing the Vickers hardness test procedure.
- Thermal Conductivity3 – Britannica article explaining the concept of thermal conductivity.
- regrinding or resharpening4 – ZYDiamondTools guide covering techniques and best practices for sharpening PCD and PCBN tools.
ZY Superhard Tools Co., Ltd.
Do you have any needs for PCD tools or diamond grinding wheels? We can customize products to meet your specific requirements. If you have any ideas or requests, feel free to reach out—we’ll respond within 24 hours!
Do you have any needs for PCD & CBN tools or diamond grinding wheels? We can customize products to meet your specific requirements. If you have any ideas or requests, feel free to reach out—we’ll respond within 24 hours!
Do you have any needs for PCD & CBN tools or diamond grinding wheels? We can customize products to meet your specific requirements. If you have any ideas or requests, feel free to reach out—we’ll respond within 24 hours!
Post Categories
Product Categories
About Company
Related Posts
Which Turning Insert Shape Should You Choose?
Master turning insert selection. Our guide covers choosing the right shape for your job, decoding ISO codes, and selecting the
How Do You Solve Vibration, Chip Control, and Surface Finish Issues in PCD Grooving?
Solve common PCD grooving problems. This guide details how to fix vibration, improve chip evacuation, and achieve a flawless sidewall
Why Is Your Tooling Wearing Out Prematurely? A Machinist’s Guide to Key Causes & Proven Solutions
Facing premature tool wear? Learn the key causes like heat, vibration, & wrong parameters. Discover proven solutions from setup to
How Do You Select the Optimal PCD Tools for Scroll Compressor Machining?
Learn how to select the right PCD tools for scroll compressor machining. This guide covers the benefits over carbide, key
Subscribe
Simply enter your email below and click “Subscribe” to stay connected with everything new and exciting.