-
Whatsapp: +86 13526572721
-
Email: info@zydiamondtools.com
-
Address: AUX Industrial Park, Zhengzhou City, Henan Province, China
-
Whatsapp: +86 13526572721
-
Email: info@zydiamondtools.com
-
Address: AUX Industrial Park, Zhengzhou City, Henan Province, China
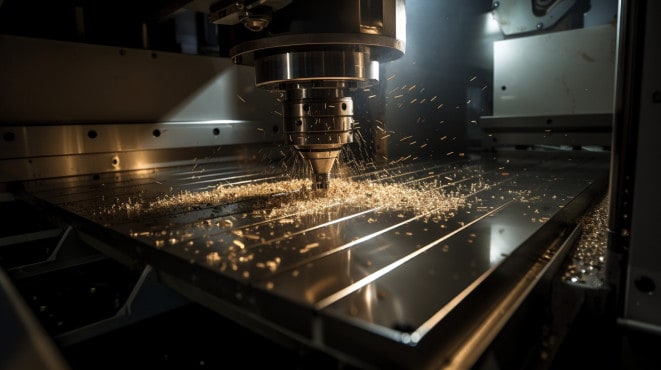
Trying to figure out whether a PCD or a Monocrystalline diamond end mill is the right choice for your specific milling job and performance goals?
Choosing between Polycrystalline Diamond (PCD) and Monocrystalline Diamond (MCD) end mills depends heavily on balancing material properties, required finish, operational demands, and economic factors. PCD offers robust performance and superior tool life for milling abrasive non-ferrous materials and composites, making it ideal for high-volume production. MCD provides unmatched sharpness for achieving mirror finishes in ultra-precision applications on specific soft materials but is limited by its brittleness, cost, and stringent machine requirements, making it generally unsuitable for general milling.
Table of Contents
ToggleHow Do PCD and MCD Fundamentally Shape End Mill Design and Capabilities?
How exactly do the basic differences between Polycrystalline Diamond (PCD) and Monocrystalline Diamond (MCD) materials influence the way diamond end mills are designed and what they can actually do?
The fundamental structures of Polycrystalline Diamond (PCD) and Monocrystalline Diamond (MCD) directly dictate key end mill design features and inherent capabilities. Specifically, PCD’s composite nature enables tougher, more complex geometries suitable for robust tools designed for wear resistance. In contrast, MCD’s single-crystal structure allows for unparalleled edge sharpness crucial for ultra-fine finishes but inherently limits geometric complexity and demands specific construction methods to protect its brittle nature.
Let’s delve into how these core material traits translate into the physical design and potential of PCD and MCD end mills.
Impact of Material Structure on Flute Edge Geometry (Achievable Sharpness vs. Edge Strength)
The very building blocks of PCD and MCD determine how sharp and how strong the cutting edge of an end mill flute can be. Think about the edge doing the cutting – its shape is crucial.
PCD Edge Characteristics
Polycrystalline Diamond (PCD)1 is like a microscopic mosaic, made of many tiny synthetic diamond crystals (grains) bonded together, usually with a metal like cobalt. Because of this structure:
- Edge Sharpness: The sharpest possible edge on a PCD end mill is limited by the size of these individual diamond grains. Imagine trying to make a perfectly smooth edge from tiny, hard pebbles – you can get it sharp, but not perfectly smooth down to the atomic level. While extremely sharp compared to traditional carbide tools, it won’t reach the ultimate sharpness of MCD. Finer PCD grains (sometimes down to sub-micron levels) generally allow for sharper edges than coarser grains, although the exact sharpness achievable can vary between PCD grades and manufacturers.
- Edge Strength: This is where PCD excels. The random orientation of the diamond grains and the presence of the binder material make the edge significantly tougher and more resistant to chipping. If a tiny crack starts, it hits grain boundaries that stop it or force it to change direction, preventing catastrophic failure. This allows PCD end mill edges to be honed or chamfered (given a small angle or radius) for added strength, especially important for handling the impacts common in milling.
MCD Edge Characteristics
Monocrystalline Diamond (MCD)2, being a single, flawless diamond crystal, behaves differently:
- Edge Sharpness: MCD allows for the creation of an atomically sharp cutting edge. Because it’s one continuous crystal structure, it can be polished (lapped) along specific natural planes to achieve an edge radius measured in mere nanometers. This results in an incredibly keen, almost perfectly continuous cutting line.
- Edge Strength: This incredible sharpness comes at the cost of brittleness. Like a thin sheet of glass, an MCD edge is very susceptible to chipping or fracturing if it encounters impact, vibration, or a hard spot in the material. There are no grain boundaries to stop cracks. Edge preparations like honing are generally not feasible as they would compromise the sharpness needed for MCD’s main purpose. Trying to break a concrete block (PCD) versus a sheet of glass (MCD) illustrates the toughness difference. Both are hard, but the concrete takes much more abuse, while the glass can shatter from a sharp impact.
Essentially, PCD offers a strong, durable edge suitable for demanding cuts, while MCD provides an incredibly sharp but delicate edge perfect for creating ultra-smooth finishes. Important Note: Specific hardness (e.g., Knoop hardness values) and fracture toughness values can vary between different grades of PCD (based on grain size and binder content) and specific orientations of MCD. Always consult the tool supplier’s specifications for the precise properties of the tool you are considering.
End Mill Construction Methods: Brazed PCD Tips vs. Shaped Monocrystal Edges
How the diamond cutting edge is actually attached to the end mill body differs significantly between PCD and MCD, impacting the tool’s overall design.
- PCD End Mills: The most common method involves taking precisely cut segments or tips of PCD (often already bonded to a small carbide backing) and brazing them into slots machined into a solid carbide end mill body (shank). Brazing uses a filler metal melted at high temperature to join the PCD tip to the carbide shank. This process requires careful control to ensure a strong bond without damaging the PCD or the carbide, considering factors like different thermal expansion rates. You can often visually identify the distinct, darker PCD segments attached to the flutes of the carbide body.
- MCD End Mills: Creating an MCD end mill edge often involves taking a larger piece of high-quality synthetic or natural single-crystal diamond and carefully shaping it to form the cutting edge(s). This shaped diamond is then typically brazed or sometimes mechanically clamped onto a precision-made shank (often carbide or steel). A critical factor in MCD tool construction is orienting the diamond crystal correctly relative to the expected cutting forces to maximize wear resistance along its strongest planes. Because of MCD’s value and brittleness, construction is meticulous and often tailored for specific ultra-precision applications.
So, PCD construction typically involves adding pre-made composite tips to a standard body, while MCD construction focuses on shaping and carefully mounting a single, pure crystal element.
Feasible Geometries: Flute Count, Helix Angles, and Corner Radii/Chamfer Limitations
The material’s toughness or brittleness directly limits the shapes and features possible in an end mill design.
- PCD End Mill Geometries: Thanks to its relative toughness, PCD allows for a wide range of conventional end mill geometries, similar to carbide tools but adapted for diamond properties:
- Flute Count: Multiple flutes (commonly 2, 3, 4, or even more for finishing) are standard, enabling higher feed rates and productivity.
- Helix Angles: Standard helix angles (e.g., 30°, 45°) are used to provide smooth cutting action and aid chip evacuation.
- Corner Geometries: Sharp corners, corner radii, and corner chamfers are all readily achievable to suit different milling tasks (e.g., shoulder milling vs. preventing part burrs). Ball nose and toroidal (corner radius) cutters are also common.
- Limitations: While versatile, creating extremely fine or intricate features directly in the PCD edge itself can still be challenging compared to grinding carbide.
- MCD End Mill Geometries: The extreme brittleness of MCD severely restricts design possibilities, especially for tools intended for general milling:
- Flute Count: Often limited to a single cutting edge (similar to a fly cutter) or perhaps two very robustly designed flutes for highly specialized finishing passes. Multi-flute designs common in milling are generally impractical due to the high risk of chipping on impact.
- Helix Angles: High helix angles increase cutting forces in ways that can be detrimental to the brittle MCD edge, so low or zero helix angles are more common where MCD is used in a milling-like context.
- Corner Geometries: Sharp corners are extremely vulnerable points. Large corner radii or chamfers might be used where possible, but intricate tip geometries are generally avoided. Ball nose MCD tools exist but are highly specialized and delicate.
Therefore, PCD offers much greater flexibility in designing end mills for various standard milling tasks, whereas MCD’s geometric limitations typically confine it to simpler forms for specific finishing operations.
The Role of the Carbide Shank and Brazing Integrity
Even the best diamond edge is ineffective if not supported correctly. The rest of the end mill plays a vital role.
- Carbide Shank: The body of most diamond end mills is made from solid cemented carbide. Why carbide? Because it offers excellent rigidity (high stiffness, measured by Young’s Modulus3). This stiffness is crucial for minimizing vibration and tool deflection during cutting. Excessive vibration can quickly damage a diamond edge, especially a brittle MCD edge. A rigid shank ensures the cutting edge is presented stably to the workpiece. The diameter and length (overhang) of the shank significantly influence this rigidity.
- Brazing Integrity: For PCD end mills (and many MCD tools), the braze joint is the critical connection between the diamond cutting element and the carbide shank. This joint must be strong enough to withstand the cutting forces, impacts, and thermal stresses experienced during high-speed milling without failing. A weak or flawed braze joint can lead to the PCD tip detaching prematurely, causing immediate tool failure. High-quality manufacturing processes ensure a void-free, high-strength braze for reliable performance.
Think of the end mill as a system: the diamond provides the cutting ability, the braze provides the secure connection, and the carbide shank provides the stable platform. All parts must function correctly for the tool to perform effectively and safely.
What Are the Performance Differences in Common End Milling Operations?
When you put PCD and MCD end mills to work in actual milling jobs, how do they really stack up against each other in terms of performance?
In common end milling operations, Polycrystalline Diamond (PCD) and Monocrystalline Diamond (MCD) exhibit significant performance differences. Specifically, PCD end mills excel in chip control, tool life, and handling interrupted cuts, particularly in abrasive materials, delivering good to excellent finishes reliably. Conversely, MCD’s extreme sharpness allows for superior mirror finishes in specific continuous finishing cuts but suffers from poor chip handling in heavier operations and extreme sensitivity to vibrations and impacts, making it generally unsuitable for roughing or standard milling tasks.
Let’s explore how these differences play out when milling slots, pockets, profiles, and faces.
Chip Control and Evacuation in Slotting and Pocketing with PCD End Mills
When cutting deep slots or clearing out pockets, getting the cut material (the chips) out of the way efficiently is critical. How do PCD end mills handle this?
PCD end mills generally perform well in these operations, especially in their preferred non-ferrous materials like aluminum alloys. Here’s why:
- Good Chip Formation: Diamond’s low friction helps create smoother, more manageable chips compared to other tool materials in non-ferrous metals.
- Flute Design: Quality PCD end mills often feature polished flutes. This smooth surface reduces friction further, allowing chips to slide out more easily, preventing them from getting packed in the flute, which can cause tool breakage or poor surface finish.
- Toughness Advantage: PCD’s toughness allows for reasonable chip loads (the thickness of material each flute cuts). This means you can remove material efficiently without excessive risk of the edge chipping.
- Importance: Effective chip evacuation is vital in slotting and pocketing. If chips pack the flutes, they can be recut, generating excess heat, potentially damaging the tool or workpiece, and leading to poor surface finish or dimensional inaccuracy. Using appropriate coolant or compressed air blast is still crucial to aid this process, especially in deep cavities.
In contrast, MCD end mills are rarely suitable for significant slotting or pocketing. Their inherent brittleness makes them prone to fracture with the cutting forces involved in heavier material removal. Furthermore, their typical geometry (often single or few flutes) isn’t designed for efficient chip evacuation from confined spaces. While they might handle a very light finishing pass in a pocket floor in specific scenarios, PCD is overwhelmingly the choice for these common operations due to its robustness and chip handling capabilities.
Achieving Wall and Floor Surface Finish in Profiling and Face Milling
Surface finish is often a key requirement. How smooth can PCD and MCD end mills make the walls and floors of milled parts?
This is where the fundamental differences become visually apparent:
- PCD Surface Finish: PCD end mills typically produce very good to excellent surface finishes on non-ferrous metals and composites. Achieving surface roughness (Ra) values below 0.4 micrometers (µm) is common, and with fine-grain PCD grades and optimized conditions, finishes below 0.2 µm are possible. This is often significantly smoother than finishes from carbide tools in the same material. The resulting surface is usually smooth and functional, suitable for demanding automotive or aerospace components. However, due to the micro-structure of grains and binder, it won’t typically achieve a true mirror polish. Keep in mind that the final Ra value depends heavily on the specific PCD grade (grain size), cutting parameters, coolant application, and the rigidity and condition of the machine tool; it’s wise to consult tool supplier data for expected ranges in your specific application.
- MCD Surface Finish: When the goal is a true mirror finish, MCD is often the only way to achieve it directly through milling (or more commonly, fly-cutting, which uses a similar single-point diamond tool). On suitable soft, non-abrasive materials (like high-purity aluminum, copper, acrylic), MCD’s atomically sharp edge shears the material cleanly, capable of producing Ra values below 0.025 µm (25 nanometers), sometimes even lower. This level of finish is essential for optical components like mirrors and molds, or high-end decorative parts. Achieving this requires ultra-precision machine tools with excellent vibration control and meticulously optimized cutting parameters.
Think of it like this: PCD gives you a surface like finely sanded wood – very smooth and functional. MCD, under the right conditions, gives you a surface like polished glass – highly reflective and near-perfect.
Tool Life and Failure Modes During Interrupted Cuts (Roughing vs. Finishing)
Milling often involves interrupted cuts – the cutting edge constantly enters and exits the material, like when milling across slots, holes, or starting/ending a pass. How do PCD and MCD hold up?
- PCD Tool Life & Failure: PCD truly shines here due to its toughness.
- Tool Life: It offers exceptionally long tool life when milling its preferred abrasive materials, often lasting tens or even hundreds of times longer than carbide. Always refer to supplier recommendations and consider running tests for your specific scenario.
- Interrupted Cuts: It handles the repeated impacts of entering and exiting the workpiece relatively well. The wear pattern is typically gradual abrasion or rounding of the cutting edge.
- Failure Mode: While excessive force or severe instability can cause chipping, the failure is usually less sudden or catastrophic than with MCD. Predictable wear allows for planned tool changes. PCD is well-suited for both roughing (removing large amounts of material) and finishing passes in suitable materials.
- MCD Tool Life & Failure: MCD performs poorly in interrupted cuts.
- Tool Life: Its tool life is critically dependent on continuous, stable cutting in soft, non-abrasive materials. Any interruption dramatically shortens its life.
- Interrupted Cuts: The impact stress as the ultra-brittle edge enters or exits the material very often leads to immediate micro-chipping or catastrophic fracture.
- Failure Mode: Failure is typically sudden edge breakage, instantly ruining the tool and potentially damaging the workpiece. This makes MCD generally unsuitable for roughing or any standard milling operation involving significant interruptions.
Consider face milling an aluminum casting with several holes. A PCD end mill can typically pass over the holes repeatedly with minimal issues. An MCD tool used in the same way would likely fracture its edge the first time it encountered the edge of a hole.
Managing Vibration and Deflection: PCD Robustness vs. MCD Sensitivity
No machine is perfectly rigid, and cutting forces cause tools to vibrate and deflect slightly. How tolerant are PCD and MCD end mills?
- PCD Robustness: PCD end mills are more forgiving of typical machining vibrations and minor instabilities. Their inherent toughness helps the cutting edge withstand these dynamic forces without immediate failure. While optimal performance and tool life always benefit from a rigid setup (good machine tool, secure workholding, minimal tool overhang), PCD doesn’t necessarily demand the absolute perfection required for MCD. It offers a wider, more practical operating window for general milling tasks.
- MCD Sensitivity: MCD end mills are extremely sensitive to any vibration or deflection.
- Vibration: Even slight chatter, which might be barely noticeable with other tools, can cause the delicate MCD edge to chip instantly. This necessitates the use of ultra-precision, highly damped machine tools and very careful setup.
- Deflection: Tool deflection must be minimized by using short, stout tools and very light cutting forces (shallow depths of cut, low feed rates). Any significant deflection can alter the precise cutting geometry and potentially overload the fragile edge.
This difference in sensitivity has major practical implications. Using PCD is feasible on a wider range of good-quality machine tools, offering greater process security. Successfully using MCD for milling-like operations demands significant investment in specialized equipment and process control to maintain the necessary stability.
Which Milling Applications Specifically Demand PCD vs. Monocrystalline Diamond End Mills?
So, when it comes to specific milling jobs, which applications absolutely call for PCD end mills, and where does MCD fit into the picture?
Specific milling applications strongly dictate the choice between PCD and Monocrystalline Diamond end mills based primarily on the material being machined and the required finish quality. Essentially, PCD end mills are demanded for high-volume, high-speed milling of abrasive non-ferrous materials (like high-silicon aluminum) and composites due to their essential wear resistance. Conversely, MCD finds its specialized niche mainly in ultra-precision finishing operations, often utilizing fly-cutting rather than conventional milling, to achieve mirror finishes on specific soft, non-abrasive materials where ultimate edge sharpness is the priority.
Let’s look closer at the specific types of jobs where each type of diamond end mill becomes the necessary choice.
High-Volume Milling of Abrasive Non-Ferrous Metals & Composites (The PCD End Mill Domain)
Certain materials are notoriously tough on cutting tools because they contain hard, abrasive particles or fibers that act like sandpaper. When you need to mill these materials efficiently, especially in large quantities, PCD end mills often become indispensable.
- Key Materials:
- High-Silicon Aluminum Alloys: Alloys containing more than roughly 12% silicon (like automotive-grade A380 or A390) contain very hard silicon crystals that rapidly wear down other tools.
- Metal Matrix Composites (MMCs)4: Materials like aluminum reinforced with Silicon Carbide (Al/SiC) particles, commonly used for high-performance brake rotors or aerospace parts, are extremely abrasive.
- Carbon Fiber Reinforced Polymers (CFRP) & Glass Fiber Reinforced Polymers (GFRP): Widely used in aerospace, automotive, and sporting goods, the strong carbon or glass fibers are highly abrasive to cutting edges.
- Wood Composites (MDF/HDF) & Filled Plastics: These also contain abrasive elements (resins, fillers) that cause rapid tool wear.
- Typical Operations: High-speed milling (HSM), face milling, shoulder milling, pocketing, contouring, and drilling/reaming (using PCD rotary tools) in the materials above.
- Industries: This is the heartland of PCD applications – primarily automotive (machining engine blocks, cylinder heads, pistons, transmission cases) and aerospace (machining aluminum or composite structural components, engine casings). It’s also heavily used in woodworking for routing engineered wood products.
- Why PCD is Demanded: In these applications, standard carbide end mills wear out incredibly quickly. This leads to frequent tool changes, machine downtime, inconsistent part quality, and high overall tooling costs. PCD end mills, due to their extreme hardness and wear resistance, can last 50 to 100 times longer (or even more) than carbide in materials like A390 aluminum or CFRP. This dramatic increase in tool life is crucial for enabling automated, high-volume production runs, maintaining tight tolerances consistently, and achieving a lower cost per part despite the higher initial tool price. PCD isn’t just better here; it’s often the only economically viable solution.
Ultra-Precision Finishing via Fly-Cutting or Specialized Milling (The MCD Limited Milling Niche)
Monocrystalline Diamond (MCD) occupies a very different, highly specialized application space, usually focused on achieving the absolute best surface finish possible.
- Key Operations: While standard “end milling” with MCD is rare, its properties are essential for:
- Diamond Fly-Cutting: A process where a single-point MCD tool is mounted on a rotating head and swept across a surface to create extreme flatness and a mirror finish. This is technically a milling-like operation.
- Specialized Finishing Passes: Potentially, very light, continuous finishing passes using uniquely designed MCD tools on ultra-precision machines for specific features. (Note: Single-Point Diamond Turning (SPDT) on a lathe is the more common application for MCD’s finishing capabilities).
- Key Materials: Suitable materials are soft, pure, and non-abrasive, allowing the sharp MCD edge to shear cleanly:
- High-Purity Metals: Aluminum (esp. 6061-T6), Oxygen-Free High Conductivity (OFHC) copper, Brass, Gold, Silver.
- Plastics: Acrylic (PMMA), Polycarbonate (PC) for optical clarity.
- Other: Germanium, Electroless Nickel plating.
- Industries: Primarily optics (manufacturing mirrors, lenses, molds for optical components), electronics (computer memory disks, high-frequency parts), medical device manufacturing, and producing luxury goods with flawless finishes.
- Why MCD is Demanded: These applications require surface roughness at the nanometer level (e.g., Ra < 25nm) or form accuracy within sub-micron tolerances. MCD’s ability to be sharpened to a near-atomic radius allows it to achieve these results directly through cutting, often eliminating the need for time-consuming and potentially accuracy-reducing post-polishing steps. It enables the creation of surfaces with specific optical properties or extreme smoothness requirements unattainable by other machining methods.
Micro-Milling Challenges: Balancing Edge Integrity with Feature Size Requirements
What happens when you need to machine extremely small features, perhaps only tens or hundreds of microns wide, using tiny end mills?
Micro-milling presents a unique challenge for both PCD and MCD:
- The Need: Creating micro-channels, small pockets, tiny molds, or miniature mechanical features requires end mills with diameters often less than 1 millimeter, sometimes down to 0.1mm or smaller. These tools need proportionately fine cutting edges.
- PCD Micro-End Mills: Toolmakers can produce micro-end mills tipped with PCD. These offer good wear resistance, which is helpful when machining potentially abrasive micro-features or for achieving longer life in micro-production runs. However, the inherent grain structure of PCD still limits how sharp and perfectly defined the cutting edge can be relative to the tiny feature sizes. Achieving a perfectly sharp corner on a 50-micron wide rib with a tool made of 2-micron grains presents a geometric challenge. Edge chipping, while less likely than with MCD, remains a concern due to the delicate tool size.
- MCD Micro-End Mills: Theoretically, MCD could provide an incredibly sharp, well-defined edge even at the micro-scale. However, the extreme brittleness of MCD becomes magnified in such tiny, fragile tools. The cutting forces, even if small overall, can easily exceed the strength of the minuscule edge or tip, leading to immediate fracture. Manufacturing and handling such tools are also extremely difficult.
- The Balancing Act: Choosing between PCD and MCD for micro-milling is complex. PCD offers better robustness but limited edge definition. MCD offers potential for ultimate sharpness but extreme fragility. Consequently, for many micro-milling tasks, especially in less challenging materials, specialized fine-grain carbide micro-end mills often provide the best balance of achievable edge sharpness, geometric accuracy, and practical tool strength. Diamond micro-tools are typically reserved for very specific material/application combinations where their unique properties are absolutely necessary and the process can be exceptionally well-controlled.
Clarifying the Rarity: Why Standard MCD End Mills are Impractical for Most Tasks
Given MCD’s amazing sharpness, why aren’t standard multi-flute MCD end mills commonly found in machine shops? The reasons stem directly from its fundamental properties conflicting with the demands of typical milling:
- Extreme Brittleness: Standard milling involves interrupted cuts, varying chip loads, and potential minor impacts or vibrations. MCD edges simply lack the toughness to withstand these conditions and are highly prone to chipping or catastrophic fracture.
- Geometric Limitations: It’s extremely difficult, if not impossible, to manufacture robust multi-flute end mills with complex geometries (like helical flutes) using brittle single-crystal diamond. Simpler, stronger geometries are necessary, limiting versatility.
- Machine & Setup Sensitivity: MCD demands ultra-high precision, vibration-free machine tools and meticulous setup – conditions not typical outside specialized labs or production facilities. General-purpose machining centers often lack the required stability.
- High Cost & Risk: MCD tools are significantly more expensive than PCD or carbide. Combining this high cost with the high risk of premature failure due to chipping makes them economically unviable for most standard milling jobs.
- Material Restrictions: MCD only works well on a narrow range of soft, non-abrasive materials, severely limiting its applicability compared to PCD or carbide.
In essence, the very nature of conventional end milling—with its dynamic forces and interruptions—is fundamentally incompatible with the delicate nature of Monocrystalline Diamond. PCD, with its engineered toughness combined with high hardness, provides the practical diamond solution needed to meet the wear resistance and productivity demands of the vast majority of milling applications where diamond tooling is beneficial.
How Do Cost, Setup, and Tool Life Influence Diamond End Mill Selection?
Beyond just performance in the cut, what practical things like cost, machine setup, tool lifespan, and day-to-day handling should you consider when choosing between PCD and MCD end mills?
Practical factors including the initial purchase price, the overall machining economics (cost per part), specific machine tool capabilities, and routine handling or maintenance procedures heavily influence the selection between PCD and MCD end mills. Although PCD tools have a higher initial cost compared to carbide, they frequently prove more economical in high-wear milling scenarios because of their significantly longer tool life. Conversely, MCD tools demand a substantially higher investment not only for the tool itself but also for the required ultra-precision machinery and meticulous handling protocols, making them justifiable primarily when their unique finishing capabilities are absolutely essential.
Let’s unpack these crucial practical considerations that go beyond just the cutting edge.
Initial Investment: Standard vs. Custom Diamond End Mill Geometries
The upfront cost of diamond end mills is a significant factor. How do PCD and MCD compare, and how does customization affect the price?
Generally, there’s a clear cost hierarchy:
Standard Carbide < Standard PCD < Custom PCD < Standard MCD < Custom MCD
Here’s a breakdown:
- PCD End Mill Costs: PCD tools are notably more expensive than comparable solid carbide end mills. This reflects the cost of the synthetic diamond material and the complex high-pressure, high-temperature (HPHT) sintering process used to create the PCD layer, plus the precision grinding and brazing onto the carbide shank.
- Standard vs. Custom PCD: Standard, off-the-shelf PCD end mills with common diameters, flute counts, and corner radii are produced in higher volumes and are thus less costly than custom tools. Custom PCD tools, which might involve specific geometries, non-standard PCD grades (like varying grain sizes or binder types), or complex edge preparations, require special manufacturing runs and engineering, increasing their price.
- MCD End Mill Costs: MCD tools typically represent another significant jump in cost compared to PCD. This is due to several factors: the higher cost of producing large, high-quality single diamond crystals (whether natural or synthetic), the extremely precise labor involved in orienting, cutting, and lapping the crystal to form a nanometer-sharp edge, and often more complex or specialized mounting techniques.
- Standard vs. Custom MCD: While “standard” MCD tools are less common than standard PCD, basic geometries for specific applications (like fly-cutting or turning tools) exist. Custom MCD tools, designed for unique optical surfaces or highly specialized tasks, can be exceptionally expensive due to the bespoke design and manufacturing processes.
When selecting, you must weigh this initial investment against the tool’s expected benefits – primarily extended tool life and productivity for PCD, or unique surface finish capabilities for MCD.
Calculating Total Machining Cost in High-Wear Milling (PCD End Mill Economics)
While PCD end mills cost more initially, they can actually save money in the long run, especially when milling abrasive materials. How does this work?
Focusing solely on the purchase price is misleading. The true measure is the total machining cost per part5. This includes several factors:
- Initial Tool Price: What you pay upfront.
- Tool Life: How many parts can one end mill produce before needing replacement or resharpening?
- Machine Hourly Rate: The cost of operating the CNC machine (including labor, power, overhead).
- Tool Change Time: How long does it take to swap out a worn tool? This is non-productive machine time.
- Scrap/Rework Costs: Does inconsistent tool wear lead to out-of-spec parts?
The PCD Advantage: In applications like milling high-silicon aluminum or composites, PCD’s dramatic tool life advantage is key.
- Example (Illustrative): Imagine milling an abrasive aluminum part:
- Carbide End Mill: Costs $50, lasts for 200 parts. Requires 10 tool changes for 2000 parts.
- PCD End Mill: Costs $450, lasts for 10,000 parts. Requires only 1 tool for 2000 parts (with life remaining).
- Calculation Insight: Even though the PCD tool costs 9 times more upfront, it might eliminate 9 tool changes needed for the carbide tool over 2000 parts. If each tool change takes 10 minutes and the machine rate is $100/hour, those 9 changes represent 1.5 hours of lost production time, costing $150 in machine time alone, plus the cost of the additional carbide tools. The PCD tool completes the job with far less downtime and operator intervention.
Therefore, particularly in high-volume or demanding applications, the extended lifespan and reliability of PCD end mills significantly reduce downtime and spread the initial cost over vastly more parts, leading to a lower total cost per part compared to rapidly wearing carbide tools.
Machine Tool Requirements: Rigidity, Spindle Speed, and Precision Needs
Can any CNC machine run diamond end mills effectively? Not necessarily. The machine itself plays a crucial role.
- Requirements for PCD End Mills:
- Rigidity: PCD performs best on rigid, stable machine tools. Good machine construction and well-maintained components minimize vibration, which helps prolong tool life and improve surface finish.
- Spindle Speed: PCD often excels at higher cutting speeds (higher RPM) compared to carbide in non-ferrous materials. Therefore, machines with high-speed spindle capabilities are often preferred to maximize productivity.
- Coolant Delivery: Effective coolant or air/oil mist delivery is important for chip evacuation and thermal control, especially at high speeds.
- Overall: Many modern, well-maintained CNC machining centers are suitable for running PCD end mills effectively, provided they are rigid and have adequate spindle speed.
- Requirements for MCD End Mills: The bar is set much higher for MCD.
- Ultra-Precision & Rigidity: MCD demands machines with exceptional stiffness and vibration damping characteristics (often featuring granite bases, hydrostatic or aerostatic bearings). Standard machining centers generally lack the required stability.
- Accuracy & Control: High-accuracy spindles, precise axis movements (sub-micron resolution), and sophisticated thermal stability control are essential to prevent minute vibrations or movements that could chip the delicate edge.
- Environment: Often requires a temperature-controlled, clean environment to maintain stability and prevent contamination.
- Overall: Successfully using MCD tools typically requires investing in specialized ultra-precision machine tools, which are significantly more expensive and complex than standard CNCs.
The takeaway is clear: your available machinery may limit your effective use of diamond tooling, particularly MCD.
Handling, Setup, and Resharpening Considerations for Each Type
Diamond tools require specific care throughout their lifecycle.
- Handling:
- PCD: While tougher than MCD, PCD tips are still relatively brittle compared to carbide. Avoid dropping the tools or letting the cutting edges knock against hard surfaces (like vices or fixtures). Use protective caps or containers during storage and transport.
- MCD: Treat with extreme care. These tools are highly susceptible to damage from even minor impacts. Use specialized handling procedures, avoid touching the edge, and always store them securely in protective packaging. Operator training on proper handling is crucial.
- Setup:
- PCD: Setup is similar to carbide, focusing on proper tool holding (high-quality holders like hydraulic or shrink-fit are recommended), minimizing tool runout (wobble), and ensuring secure workpiece clamping.
- MCD: Requires meticulous setup. Achieving near-zero runout is critical. Tool setting often uses non-contact methods (optical or laser systems) to avoid damaging the fragile edge. Precise alignment of the tool’s cutting edge to the workpiece might be needed for specific optical applications.
- Resharpening/Relapping: Can worn diamond tools be given a second life?
- PCD: Yes, PCD end mills can often be resharpened by specialized grinding services. This typically involves regrinding the flank or face of the PCD segments. The feasibility and number of possible resharpenings depend on the extent of wear and the tool’s original design. It’s important to compare the cost and expected performance of a resharpened tool versus a new one. Quality can vary, so choose reputable resharpening providers, and note that resharpening capabilities might differ based on the original manufacturer’s design.
- MCD: If the wear is minor and primarily on the flank face, MCD tools can sometimes be relapped (a specialized polishing process) to restore sharpness. However, if the tool is significantly chipped or fractured, repair is often impossible or uneconomical. Relapping requires highly specialized expertise and equipment. It’s best to consult the original tool manufacturer regarding potential relapping services and viability for your specific tool.
Considering these factors – initial cost versus total cost, machine compatibility, and the required care in handling and maintenance – provides a practical framework for selecting the most appropriate and cost-effective diamond end mill solution.
Making the Definitive Choice: A Practical Guide for Selecting Your Diamond End Mill
Okay, after considering all the details, how do you actually pull it all together and make the final, practical choice between a PCD and an MCD end mill for your specific job?
Making the definitive choice between PCD and MCD end mills involves a systematic approach focused on your specific needs. Primarily, you must match the tool type to the workpiece material’s abrasiveness and required finish. Then, align the tool’s characteristics (toughness vs. sharpness) with the demands of your specific milling operation. Asking key diagnostic questions and, for PCD, selecting the appropriate grain size will guide you to the most effective and economical solution.
Let’s walk through the steps to make that final selection confidently.
Matching Material Abrasiveness and Hardness to the Right Diamond Type
The material you intend to mill is arguably the single most important factor driving the initial decision.
- Rule 1: Highly Abrasive Materials: If your workpiece is a known abrasive non-ferrous material (like high-silicon aluminum alloys [e.g., >12% Si], Metal Matrix Composites [MMCs], Carbon or Glass Fiber Reinforced Polymers [CFRP/GFRP], or even ‘green’ ceramics), PCD is almost certainly the necessary choice. Its superior wear resistance is essential to achieve acceptable tool life and productivity. Using anything else will likely result in extremely rapid wear.
- Rule 2: Soft, Non-Abrasive Materials + Ultimate Finish: If your material is soft, high-purity, and non-abrasive (like OFHC copper, pure aluminum, gold, PMMA/acrylic) AND you absolutely require a mirror surface finish (typically Ra < 0.025 µm or 25nm) or ultra-high precision form accuracy, then MCD becomes the primary candidate. However, this is only if the milling operation and machine tool are suitable for its delicate nature (see next steps).
- Rule 3: General Non-Ferrous Materials: For standard non-ferrous metals (like common aluminum alloys such as 6061) or softer non-ferrous materials where an excellent, but not mirror, finish is sufficient, PCD is usually the most practical and cost-effective choice. It provides very good tool life, good surface finish, and overall process reliability.
- Rule 4: Ferrous Metals: If you are milling steels or cast irons, remember that neither PCD nor MCD is suitable due to adverse chemical reactions at machining temperatures. You will need to use carbide, ceramic, or CBN tools.
Aligning Specific Milling Operations with Optimal End Mill Characteristics
Next, consider the nature of the milling task itself and how it matches the core strengths of PCD and MCD.
- Interrupted Cuts / Robust Operations: If your milling operation involves significant interrupted cuts (like standard end milling passes, entering/exiting corners, milling across holes or slots), roughing (heavy material removal), or generally demands tool toughness, then PCD is the clear choice. Its ability to withstand impacts and resist chipping is crucial for reliability in these common scenarios. MCD is generally unsuitable for these tasks.
- Continuous Finishing / Mirror Surface Need: If the operation is a continuous finishing pass (like light face milling or fly-cutting) on a suitable soft material, AND the absolute priority is achieving the smoothest possible mirror finish, then MCD’s extreme sharpness makes it the tool for the job, if material and machine permit.
- General-Purpose Milling: For most typical milling jobs involving a mix of roughing and finishing, standard tolerances, and good-but-not-perfect finishes in appropriate non-ferrous materials, PCD offers the best all-around balance of performance, tool life, versatility, and process security.
Decision Framework: Key Questions for Choosing PCD vs. MCD for Milling
To structure your decision, ask yourself these key questions:
- Material Check: What is the exact material specification? (Is it ferrous? Abrasive non-ferrous? Soft non-ferrous?) -> Guides initial PCD/MCD/Neither path.
- Finish/Tolerance Check: What is the non-negotiable surface finish (Ra value) and dimensional tolerance required for the part function? (Standard? Excellent? Optical/Mirror quality?) -> Highlights need for MCD only if extreme requirements exist.
- Operation Check: What type of milling will be performed? (Roughing? Finishing? High chip load? Interrupted cuts? Continuous finishing?) -> Favors PCD for robustness; MCD only for stable, light finishing.
- Machine Check: What are the capabilities and condition of the machine tool? (Standard rigid CNC? Ultra-precision machine? Known vibration issues?) -> Eliminates MCD if machine isn’t sufficiently stable/precise.
- Economic Check: What is the production volume and primary economic driver? (High volume where tool life dominates cost? High-value part where achieving a unique finish justifies higher tool/process cost?) -> Balances initial cost vs. total cost per part.
This simple table summarizes the leanings based on key factors:
Key Factor Consideration | If Condition Points Towards… | Lean Towards… | Notes |
---|---|---|---|
Material Abrasiveness | High (Si >12%, MMC, CFRP/GFRP) | PCD | Essential for tool life |
Material Softness + Finish Need | Soft/Pure + Mirror Finish (Ra < 25nm) | MCD | If operation/machine suitable |
Milling Operation Type | Interrupted / Roughing / General | PCD | Requires toughness |
Milling Operation Type | Continuous Finishing (Ultra-Precision) | MCD | If material/machine suitable |
Machine Tool Capability | Standard Good CNC | PCD | More forgiving |
Machine Tool Capability | Ultra-Precision Machine Required | MCD | Mandatory for MCD success |
Primary Economic Driver | Tool Life / Cost Per Part (Volume) | PCD | Usually lower total cost in wear apps. |
Primary Economic Driver | Unique Finish / Enabling Technology | MCD | Justified by capability, not just tool life |
Selecting the Right PCD Grade (Grain Size) for Your End Mill Application
If your analysis points towards using a PCD end mill, there’s one more important selection to make: choosing the appropriate PCD grade, often distinguished by the average diamond grain size. PCD isn’t just one material; different grades offer different balances of properties.
- Understanding Grain Size: PCD tool suppliers offer various grades, often classified by the average size of the diamond crystals used (e.g., sub-micron grades around 1-2 µm, medium grades around 10 µm, coarse grades around 25 µm or more). Crucially, specific grade designations and their corresponding properties can vary significantly between manufacturers. Always refer to the supplier’s technical data for the grades you are considering.
- The Grain Size Trade-off:
- Finer Grains (e.g., < 5 µm): Tend to provide higher hardness and allow for a slightly sharper, more defined cutting edge. This often results in better surface finishes. They are frequently preferred for finishing operations or machining materials where achieving the best possible finish with PCD is the goal. However, in some very abrasive applications, they might wear slightly faster than coarser grades.
- Medium Grains (e.g., ~10 µm): Often represent a versatile balance between good wear resistance, reliable toughness, and very good surface finish capability. This makes them a popular choice for general-purpose milling in materials like standard aluminum alloys found in automotive manufacturing.
- Coarser Grains (e.g., > 20 µm): Generally offer the highest toughness and resistance to abrasion. This makes them well-suited for demanding applications like roughing, heavy interrupted cuts, or machining highly abrasive materials like MMCs, GFR polymers, or very coarse-grained composites. The achievable surface finish might be slightly rougher than with finer grain grades.
- Making the Grade Selection:
- If your primary goal is the best possible surface finish with PCD -> Explore finer grain grades.
- If your primary challenge is extreme abrasion or heavy interruptions -> Investigate coarser grain grades for maximum toughness and wear resistance.
- For general-purpose milling in common aluminum alloys -> Medium grain grades are often an excellent starting point.
Recommendation: The best approach is often to consult directly with your cutting tool supplier. Provide them with detailed information about your specific workpiece material (including alloy designation or composite type), the exact milling operation, your machine tool, and your key performance objectives (finish vs. tool life). They can leverage their expertise to recommend the most suitable PCD grade and end mill geometry for optimal results in your application.
Conclusion
Choosing between Polycrystalline Diamond (PCD) and Monocrystalline Diamond (MCD) end mills isn’t about which one is universally “better,” but about which one is precisely “right” for your specific milling challenge. PCD stands out as the robust, reliable workhorse, offering exceptional tool life and productivity when tackling abrasive non-ferrous metals and composites, making it the go-to choice for most demanding, high-volume milling applications. Its toughness allows for versatile geometries and resilience in interrupted cuts.
MCD, in contrast, is the ultra-precision specialist. Its unparalleled edge sharpness enables the creation of mirror finishes and sub-micron tolerances directly from machining, but only on specific soft, non-abrasive materials and under highly controlled, continuous cutting conditions, often in specialized operations like fly-cutting rather than standard milling. Its inherent brittleness, high cost, and stringent machine requirements confine it to a niche where its unique capabilities are indispensable.
Ultimately, the optimal choice hinges on a careful evaluation of your workpiece material, the non-negotiable surface finish and tolerance requirements, the nature of the milling operation, your available machine tool capabilities, and the overall cost-effectiveness calculation. By systematically analyzing these factors and, when selecting PCD, considering the appropriate grain size, you can confidently choose the diamond end mill technology that will deliver the best performance, quality, and economic value for your manufacturing needs. Consulting with experienced tooling suppliers remains a valuable step in finalizing your selection and optimizing your process.
References
- Polycrystalline Diamond (PCD)1 – ZYDiamondTools blog post providing a comprehensive overview of PCD tools.
- Monocrystalline Diamond (MCD)2 – ZYDiamondTools blog post explaining MCD tools and their use for precision finishes.
- Young’s Modulus3 – Encyclopedia Britannica article defining Young’s modulus of elasticity.
- Metal Matrix Composites (MMCs)4 – ScienceDirect topic page providing an overview of metal matrix composites.
- total machining cost per part5 – ZYDiamondTools blog post explaining Total Cost of Ownership (TCO) for tooling.
ZY Superhard Tools Co., Ltd.
Do you have any needs for PCD tools or diamond grinding wheels? We can customize products to meet your specific requirements. If you have any ideas or requests, feel free to reach out—we’ll respond within 24 hours!
Do you have any needs for PCD & CBN tools or diamond grinding wheels? We can customize products to meet your specific requirements. If you have any ideas or requests, feel free to reach out—we’ll respond within 24 hours!
Do you have any needs for PCD & CBN tools or diamond grinding wheels? We can customize products to meet your specific requirements. If you have any ideas or requests, feel free to reach out—we’ll respond within 24 hours!
Post Categories
Product Categories
About Company
Related Posts
Why Is Your Tooling Wearing Out Prematurely? A Machinist’s Guide to Key Causes & Proven Solutions
Facing premature tool wear? Learn the key causes like heat, vibration, & wrong parameters. Discover proven solutions from setup to
How Do You Select the Optimal PCD Tools for Scroll Compressor Machining?
Learn how to select the right PCD tools for scroll compressor machining. This guide covers the benefits over carbide, key
How Do You Choose the Right Cutting Tool for Your Mold Steel Machining?
Learn how to choose the right cutting tools for mold steel machining. This guide covers steel hardness, tool materials, coatings,
Machining Nickel-Based Superalloys: Tooling Selection and Case Studies
Learn to master machining nickel-based superalloys. This guide covers tooling selection (CBN, ceramics), parameter optimization, and real-world case studies. Read
Subscribe
Simply enter your email below and click “Subscribe” to stay connected with everything new and exciting.